Teaching owners (and mechanics) how to do borescope inspections right
In my last column (“Ending the War on Jugs,” AOPA Pilot March 2024 issue), I talked at length about why we should use the borescope—not the compression tester—as the gold standard for assessing cylinder condition. Borescopes are now inexpensive (under $300) and capable of breathtaking image quality. These new borescopes let us diagnose cylinder issues accurately and often early enough that the problem can be remediated using modern minimally invasive techniques—lapping leaking valves in place, and freeing stuck rings with a simple solvent flush—thereby eliminating the need to incur the cost and risk of cylinder removal.
But there’s a problem: Very, very few A&Ps know how to do a proper borescope inspection of cylinders. There’s little or no training on this subject in A&P school, and no relevant questions on the A&P knowledge tests. There’s nothing in any maintenance manual or service bulletin from aircraft or engine manufacturers that provides any guidance on this subject.
Interestingly, Continental has “required” that a borescope inspection be done any time a compression test is performed, but they offer not a syllable of guidance on how to do one! What’s wrong with this picture? (Lycoming says almost nothing about borescope inspection of cylinders.)
My company’s team of 40+ A&Ps look at countless thousands of borescope images on behalf of our 6,000 clients, most of them taken by mechanics at the hundreds of maintenance shops we work with. A lot of the images we receive are diagnostically useless because that the mechanic who shot them didn’t really understand what to look for. Almost all of the image sets we receive are woefully inadequate—for example, mechanics seldom capture images of the valves when they are wide open so that the all-important sealing surface of the valve and the valve seat that it mates with can be visualized.
Savvy’s Borescope Initiative
Something had to be done. After much discussion with my company’s leadership team, we decided to tackle this problem head on. We invested hundreds of hours developing a standardized borescope inspection protocol, a 35-minute training video, a companion checklist, and a detailed users guide.
Hundreds more hours were spent in software engineering to extend Savvy’s web-based platform with the addition of a sophisticated borescope image repository that allows borescope image sets to be uploaded, tagged for identification, stored, analyzed, annotated, archived and compared, including a report generator that produces elegant reports in PDF format suitable for printing and incorporating into the aircraft maintenance records.
We launched this initiative on January 1, 2024. You can find it all online by going to the https://savvyaviation.com website and navigating to Resources > Other Resources > Borescope Initiative. To encourage the widest possible adoption of these standardized methods, techniques and practices for cylinder borescope inspection, we decided to make all of this available at no cost to any mechanic, shop, or maintenance-involved owner who wishes to use it.
Inspection Protocol
Our first challenge was to create a standardized cylinder borescope inspection protocol so that borescope images would be obtained in a consistent fashion from one inspection to the next regardless of which mechanic (or owner) was manipulating the scope, and would capture everything needed to assess cylinder condition. For this, I turned to Savvy’s borescope inspection guru Dave Pasquale A&P/IA. Dave is director of maintenance at Pasquale Aviation in Pottstown, Pennsylvania as well as being a veteran member of Savvy’s technical team. Dave has done pioneering work in piston aircraft engine borescopy, and is certainly one of the foremost experts on this subject in the industry.
Over many years of doing these inspections, Dave developed a protocol of 11 specific views for each cylinder to be captured in a specific order:
- Piston crown (at bottom of stroke)
- Exhaust valve head (valve closed)
- Intake valve head (valve closed)
- Exhaust valve seat and face (valve wide open)
- Exhaust valve stem (valve wide open)
- Intake valve seat and face (valve wide open)
- Intake valve stem (valve wide open)
- Cylinder wall at 12 o’clock
- Cylinder wall at 3 o’clock
- Cylinder wall at 6 o’clock
- Cylinder wall at 9 o’clock
Now, 11 views of each cylinder may seem like a lot—and it is—but it’s really what’s needed to cover all the bases. After a little practice it takes the technician less than five minutes per cylinder to obtain these views. An inspection of a six-cylinder engine (66 images) should take about a half-hour to do (if the upper cowling is off and the top spark plugs are out).
To keep all these images well-organized, we came up with a standardized file naming convention to ensure that each image file was easily identifiable as to which view of which cylinder it is. For example, the image of the piston crown of the #5 cylinder would be named “5-piston.jpg” and the imge of the #2 cylinder wall in the 12 o’clock position would be named “2-wall-12.jpg” and so forth.
Training video and checklist
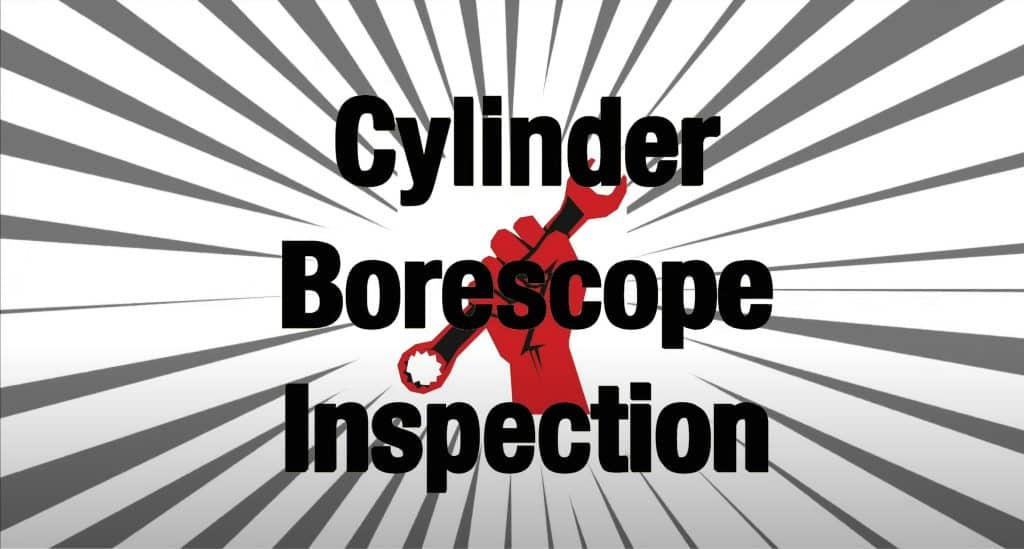
To help technicians master the technique of performing this sort of comprehensive cylinder inspection, we created a 35-minute training video aimed primarily at A&P mechanics (but also of interest to maintenance-involved aircraft owners). The lion’s share of this video shows Dave Pasquale performing the 11-image inspection of a cylinder, demonstrating how he positions the crankshaft and manipulates the scope to obtain each view, and showing what each of the captured images should look like.
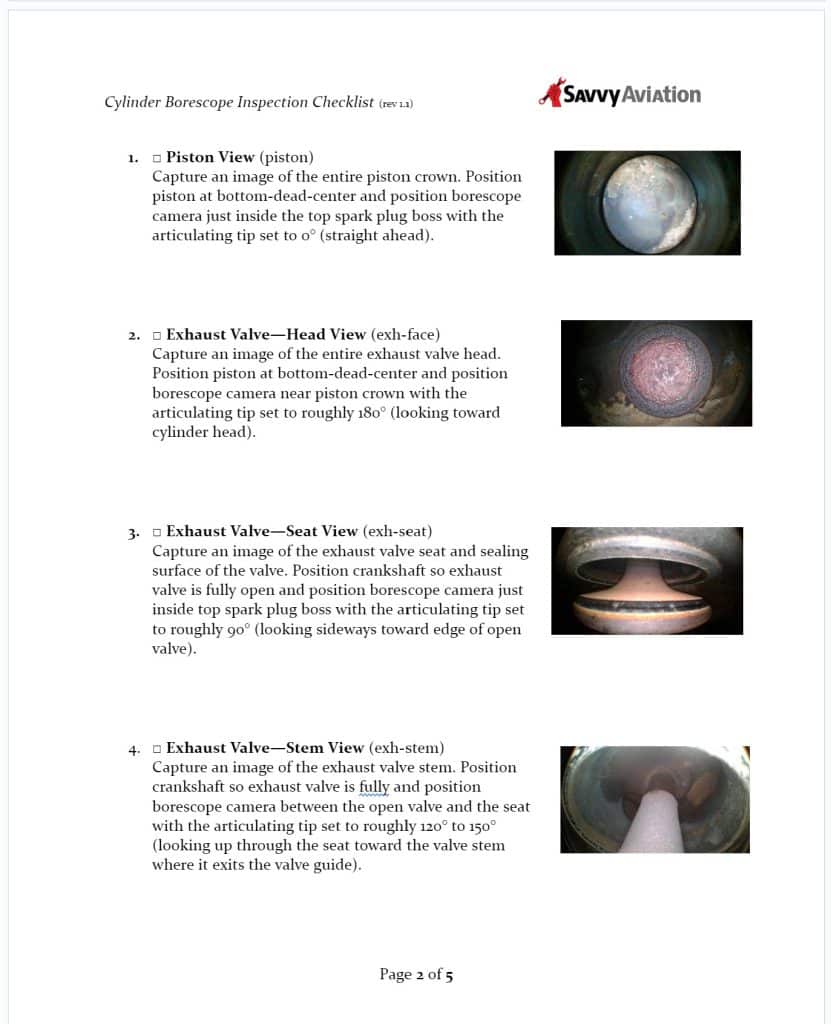
Because mechanics always like to have written guidance, we also developed a five-page checklist that describes each of the images in the protocol, explains how to capture each one, and includes photos of what each image should look like. The checklist also includes details of the recommended file-naming convention for these images.
Image Repository and Report Generator
So, you or your mechanic have shot a whole bunch of borescope images of the cylinders of your engine, hopefully conforming to the 11-image-per-cylinder protocol. Now, what are you going to do with them? To address this, Savvy’s web-based platform has been extended to provide a cloud-based borescope image repository that is available at no cost for anyone who wants to use it. You’ll need to create a free Savvy account, and then you’re good to go.
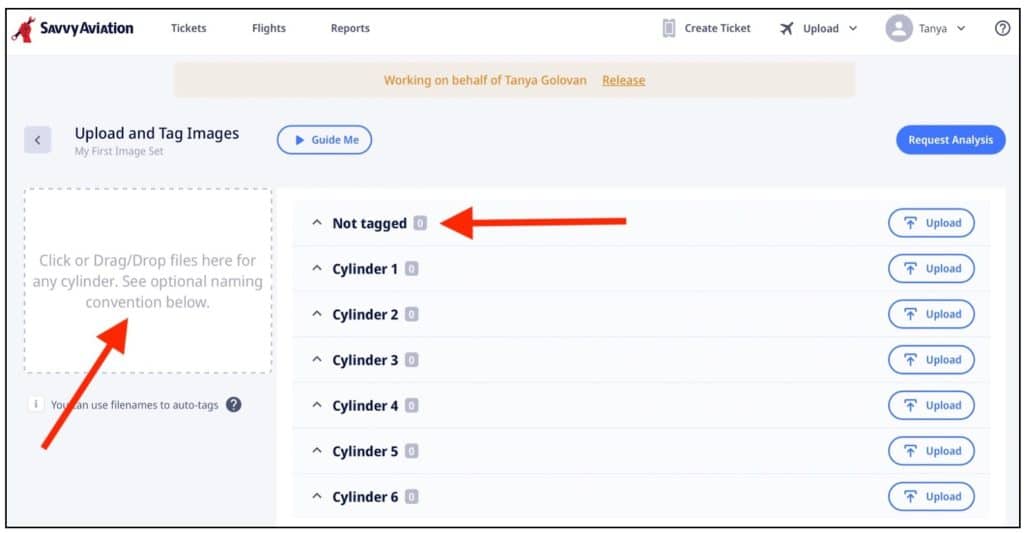
The borescope image repository provides a place for all your borescope images to be uploaded, tagged for identification, stored, organized, analyzed, annotated, archived and compared. If your image files are named in accordance with the recommended file-naming convention, then you can drag-and-drop them onto the upload screen in one fell swoop and the software will automatically tag them by cylinder number and view. Any image files with non-conforming names can be tagged manually. All the images associated with a particular inspection are organized as a named “image set” and the repository allows you to upload and archive an unlimited number of such image sets.
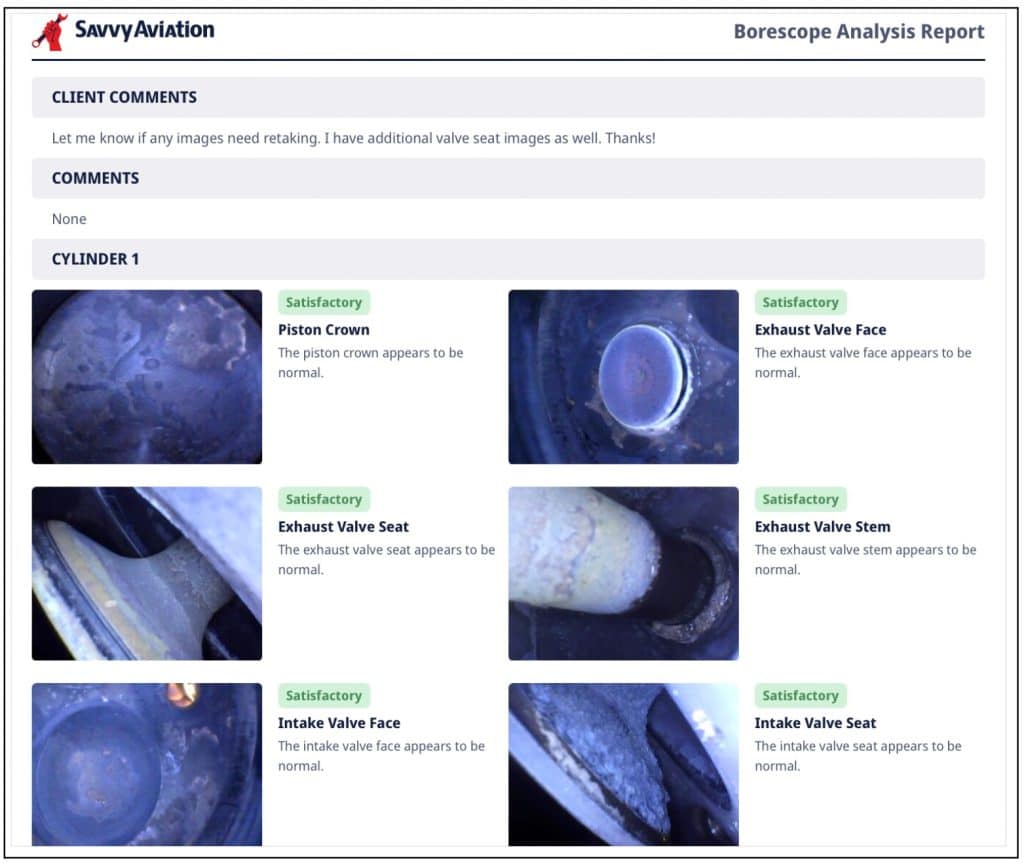
The platform also includes a report generator that produces elegant reports in PDF format suitable for printing and incorporating into the aircraft maintenance records. This can be used in two different ways. If you have a free Savvy account, then you or your mechanic can analyze and annotate the images in your image set before generating the inspection report. Alternatively, if your aircraft is enrolled in SavvyAnalysis, SavvyQA or SavvyMx, you can click on a “request analysis” button and have one of Savvy’s professional analyts analyze and annotate your images and generate the report for you.
What’s Next?
We hope that this borescope initiative will gain wide industry acceptance by shops and mechanics (and maintenance-involved owners) who perform inspections of piston aircraft engines. Widespread acceptance of borescopy as the preferred method for assessing cylinder condition has long been hampered by lack of guidance, training and standards. Assessment of cylinder condition using solely the old, unreliable, invalid differential compression test has been responsible for tens of thousands of cylinders being needlessly removed. Our goal for this initiative is to change that.
But there’s more to come. By the time you read this, I expect that we’ll have more than 1,000 image sets uploaded into the repository. Once that number reaches 10,000 or so, we should have accumulated enough images to start training a neural network to identify abnormal images and ultimately generate detailed diagnoses through AI software (much in the fashion that facial recognition software now does for faces). That would truly bring cylinder borescope inspections firmly into the 21st century! Stay tuned…