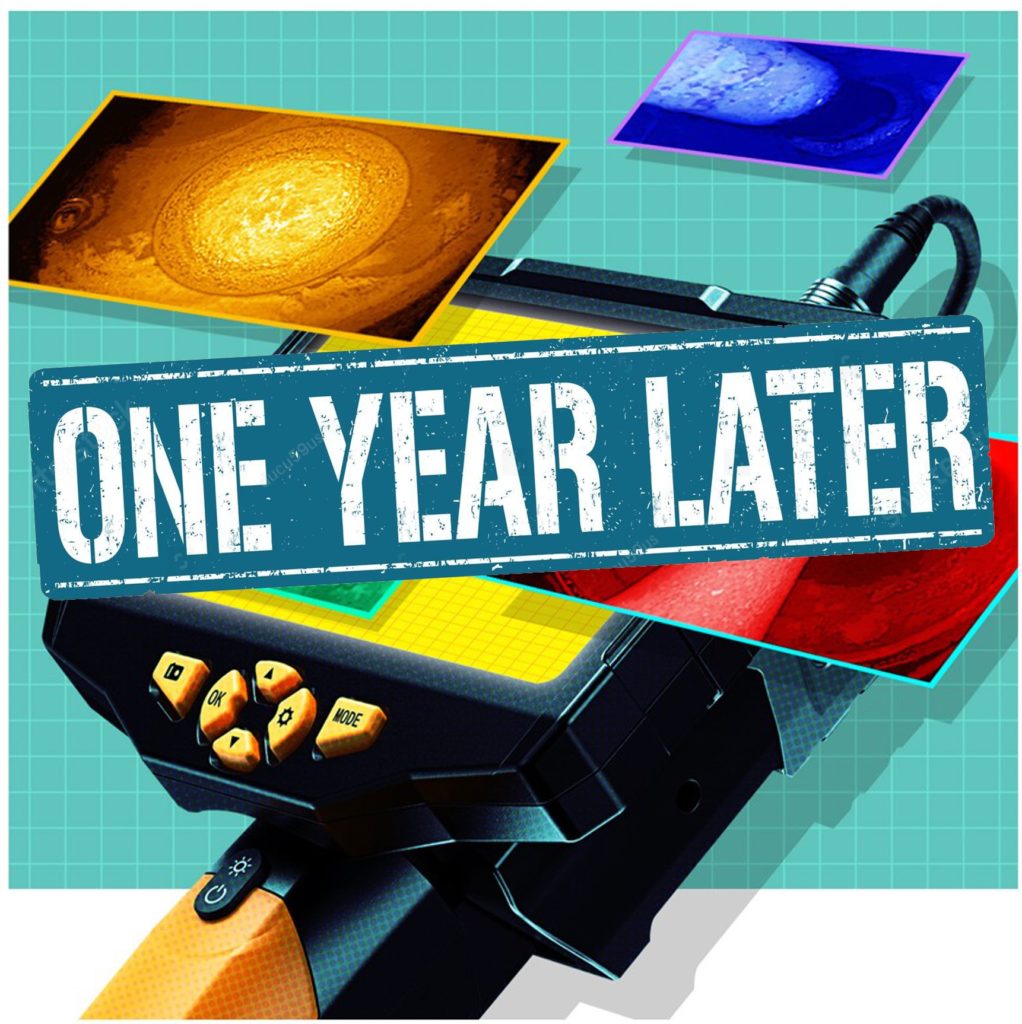
For 20 years I’ve been preaching about the benefits of using borescope inspections as the gold standard for assessing cylinder condition. Yet we still see far too much dependence on the traditional (and unreliable) differential compression test. Mechanics are removing far too many perfectly good cylinders solely based on weak compression test scores. So about two years ago, my company Savvy Aviation decided to do something about this. After six months of intensive development effort, on January 1, 2024, we launched our borescope initiative. (I wrote about this in the April 2024 issue of AOPA Pilot.)
Because none of the engine or aircraft manufacturers offered guidance about how to perform a borescope inspection of a cylinder, we decided to create one. Our borescope guru Dave Pasquale developed a standard inspection protocol, comprising 11 specific images for each cylinder—three images of each valve, four images of the cylinder barrel, and one of the piston crown. We created an inspection checklist with descriptions and thumbnails for each of these 11 images, and we created a half-hour YouTube video demonstrating how to capture each of these images.
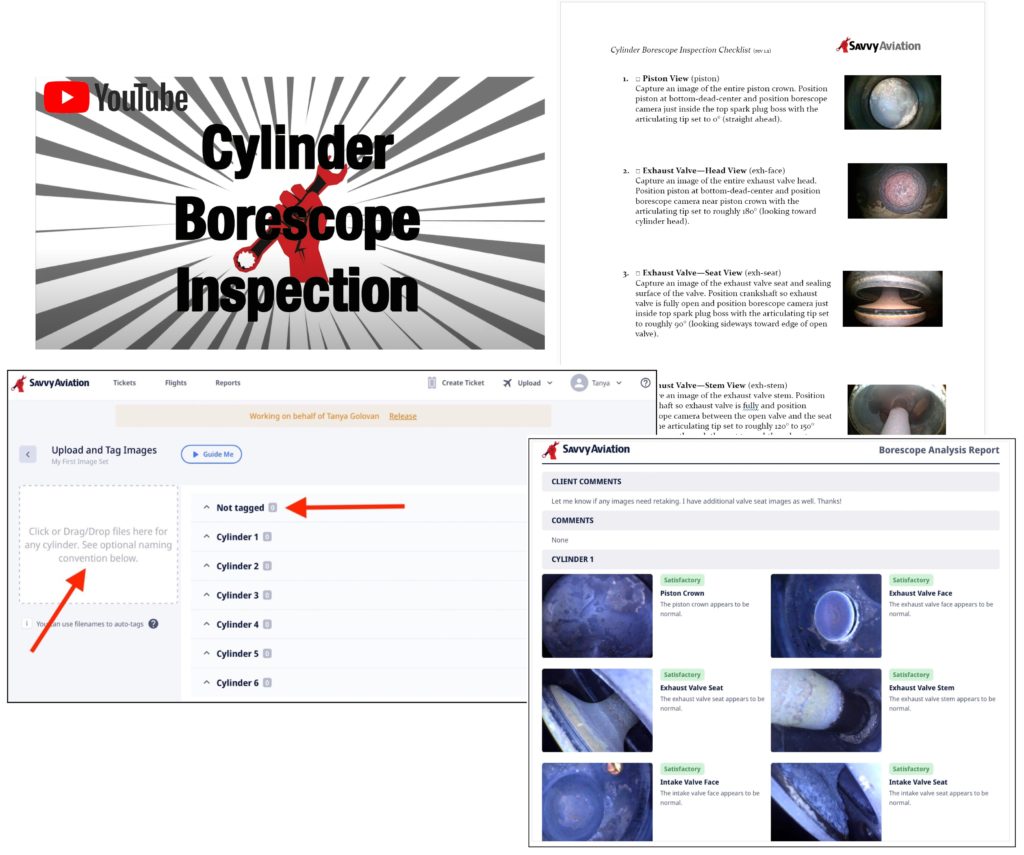
We also extended our online platform to include a borescope image repository. This allows mechanics and maintenance-involved aircraft owners to upload their borescope images to the cloud, to archive and organize their images into image sets with each image tagged with cylinder number and view information, to analyze and annotate each image, and to generate attractive borescope inspection report suitable for inclusion in the aircraft maintenance records. We made this borescope image repository available at no cost to anyone who wanted to use it. All that’s required is to create a free account on the Savvy platform.
The checklist, video, borescope image repository users manual, and instructions for creating a free account can all be found in the “Resources” section of the SavvyAviation.com website.
100,000+ Images Later
Now, just over one year later, more than 100,000 borescope images have been uploaded to the image repository. About 2,000 new images are being uploaded every week. I find this gratifying. It suggests that our initiative has been successful in encouraging cylinder borescope inspections.
Savvy’s team of analysts were asked to review and interpret about 70,000 of these images. For each of these images, the analyst labeled the image as being normal or abnormal. Each abnormal image was further labeled with the type and extent of abnormality observed by the analyst. The results were pretty interesting.
The analysts evaluated about 7,500 exhaust valves. Roughly 8.5% of them were classified as showing signs of distress (“burning”). That strikes me as a surprisingly high percentage. I’d be surprised if 8.5% of the exhaust valves in the piston fleet are distressed. I’m guessing there’s some selection bias—users might be more likely to upload borescope images of cylinders that they’re concerned about. But if even only 5% of the exhaust valves in the fleet were distressed, that would be troubling.
But it gets worse: The borescope images uploaded to the repository are uploaded in “image sets” that comprise all the images uploaded for a particular borescope inspection of an engine. If the inspection is performed according to Savvy’s 11-image-per-cylinder protocol, then an image set will contain 44 or 66 images depending on whether the engine has four or six cylinders. Not all uploaded image sets are that comprehensive—the average size of uploaded image sets was 36 images. But here’s the thing: Of the 1,550 image sets examined by Savvy analysts, 27% of them contained at least one distressed (“burned”) exhaust valve. Even allowing for some selection bias, I think it would be reasonable to assume that at least 20% of the engines in the piston fleet have at least one distressed exhaust valve. It could be 25%.
If there’s a silver lining in this data, it’s this: Of the exhaust valves identified by our analysts as being distressed, only 15% were classified as “late stage” burned valves, while the other 85% were classified as “early stage.” This means that 85% of the burned valves would have been excellent candidates for lapping in place, while only 15% were burned badly enough that cylinder removal and repair, overhaul or replacement is indicated.
The potential impact on maintenance cost is profound. Lapping an exhaust valve in place involves about $200 of labor, while cylinder removal typically costs between $2,000 and $4,500 depending on whether the cylinder is repaired, overhauled or replaced. Also, cylinder removal is vastly more invasive and risky than valve lapping in place.
How many of you have had cylinders removed because of low compression? (Don’t all raise your hands at once!) We’re learning that the overwhelming majority of these cylinder removals were not necessary.
Try Lapping First
Even if the borescope inspection reveals an exhaust valve in late-stage distress, if there’s no evidence of cracks on the valve it’s often worthwhile to give lapping-in-place a try before resorting to cylinder removal. For example, take a look at this #4 exhaust valve from a Beech Bonanza with a Continental IO-520-BB engine about 500 hours since major overhaul:
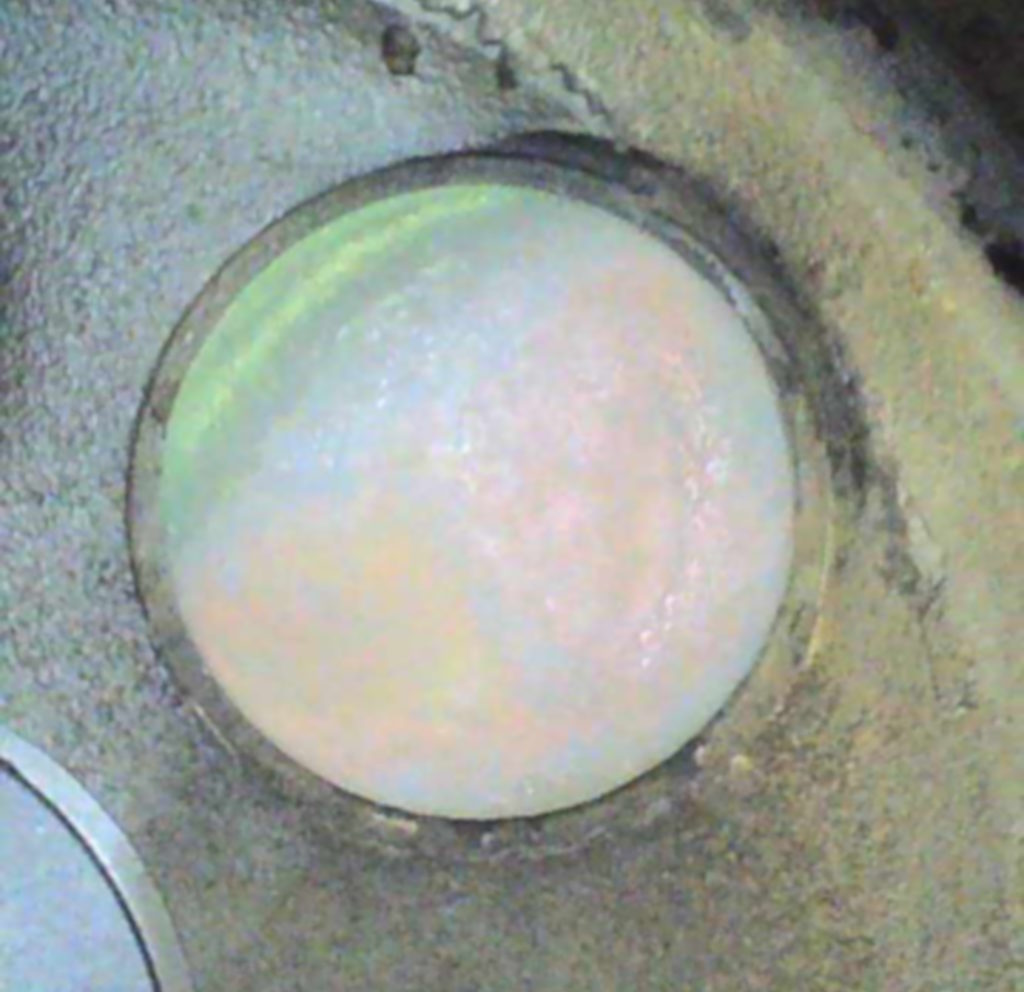
I think anyone would classify this valve as profoundly burned, based on its obvious green-colored hot spot. Almost every A&P who sees a valve in this condition would recommend cylinder removal and re-valving. If this condition was detected during an annual inspection, most IAs would require re-valving before they’d be willing to sign off the aircraft as airworthy.
I received this borescope image from my North Texas friend Ashley Blythe—a commercial pilot and A&P mechanic—who’s a true believer in minimally-invasive reliability-centered maintenance. And the IO-520-BB in question is in a Bonanza that Ashley flies regularly. So, even though Ashley figured this late-stage burned exhaust valve was probably beyond redemption, he decided to try lapping it in place to see what would happen.
The first thing that happened is that the #4 cylinder’s compression increased dramatically (from the 50s to the 70s). The aircraft was than flown for several hours, after which the top #4 spark plug was removed and the burned valve re-inspected. Here’s what it looked like:
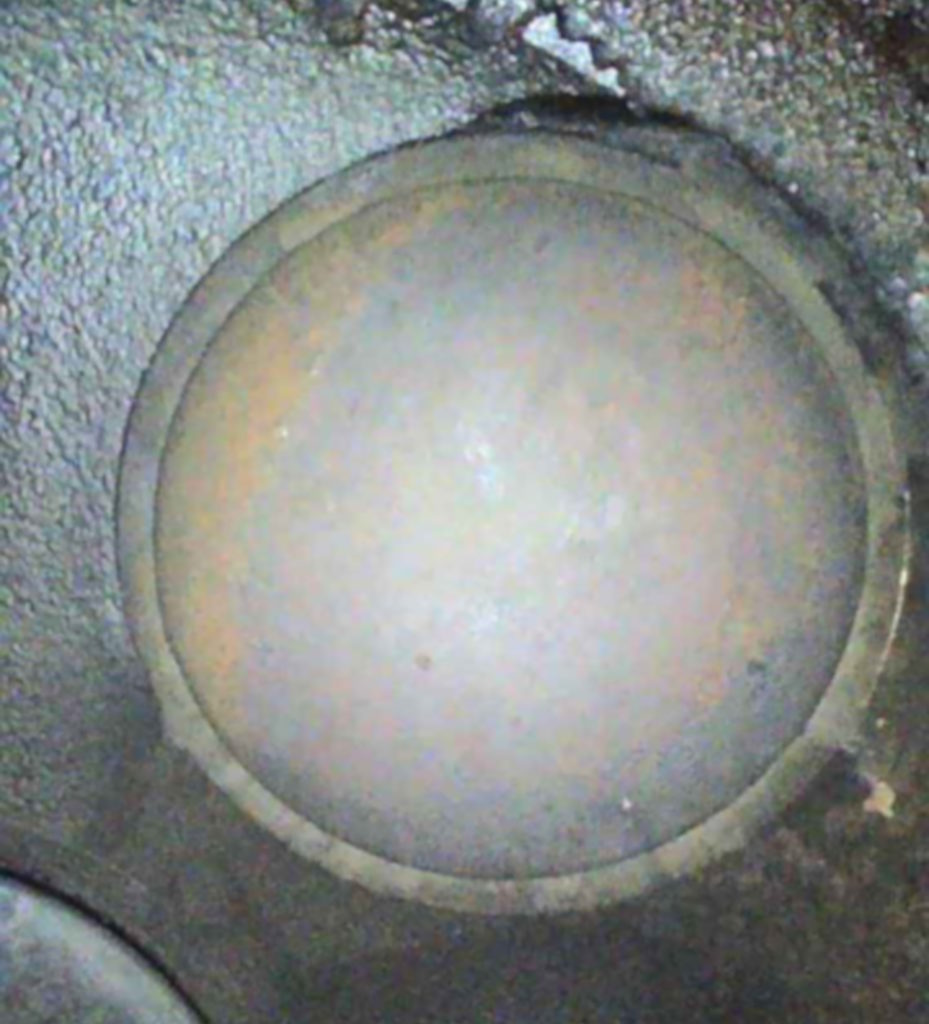
While this isn’t quite the perfect bullseye heat signature that we like to see, it’s certainly much improved and probably on its way to making a full recovery. I asked Ashley whether he’d replaced the #4 rotocoil before reassembling the valve train, and he told me that he had not. (We always recommend prophylactically replacing the rotocoil or rotator cap whenever lapping a valve—they’re cheap.) I suggested that Ashley reinspect the #4 cylinder in another 15-20 hours. If the valve doesn’t appear totally healed, then I suggested lapping the valve again—a bit more aggressively this time—and replacing the rotocoil. Only if the valve condition appeared deteriorated at the re-inspection would I bite the bullet and pull the jug.
Key Take-Aways
Based on the 100,000 borescope images collected during the first year of Savvy’s borescope initiative, we’ve arrived at some surprising conclusions. The bad news is that at least 20% and perhaps 25% of engines in the piston fleet have at least one burned exhaust valve. The good news is that about 85% of those burned valves are in early-stage distress and can be healed by lapping in place at a cost of around $200. Only about 15% of the burned valves are in late-stage distress where cylinder removal may be indicated (costing $2,000 to $4,500). Even for late-stage valves, lapping may be worth a try provided no cracks are visible in the borescope image.
These statistics emphasize the importance of doing cylinder borescope inspections on a regular basis. The borescope can identify valve distress at an early stage where lapping in place is almost certain to be effective. The traditional practice of relying solely on the compression test—or using a borescope only if compression is low—can result in detecting valve distress only at late-stage where costly cylinder removal might be necessary. It’s important to perform a comprehensive borescope inspection of every cylinder at every annual inspection. More frequent borescope inspections—say, every 50 hours—would be even better.
We will be doing more analysis—for example, to determine if there are significant statistical differences between Continentals and Lycomings—and we’ll report back if we find anything interesting.