Sensitive and fragile compared to their automotive brethren, aircraft batteries need TLC if you don’t want to be left stranded.
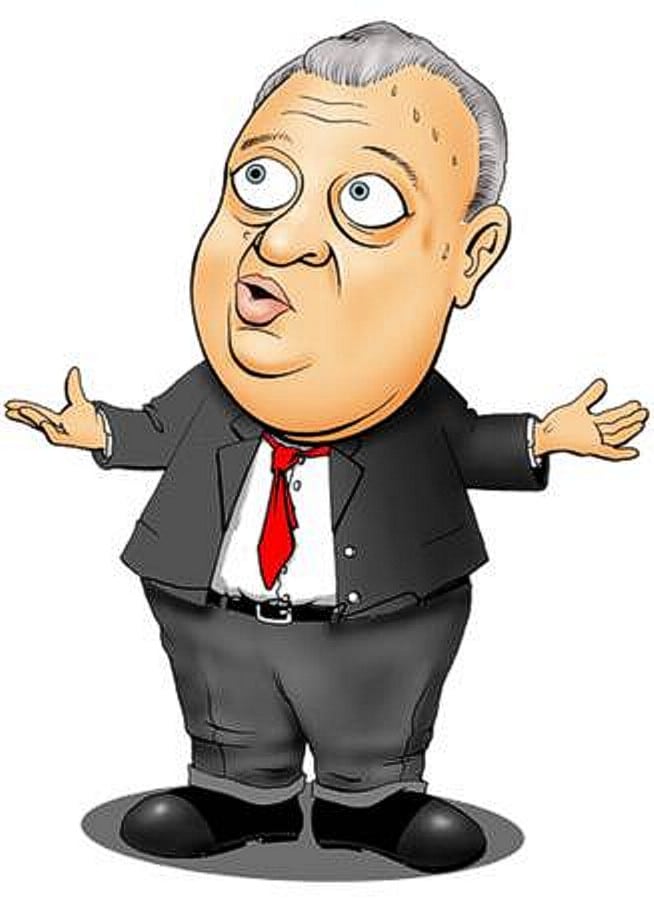
Aircraft batteries are the Rodney Dangerfields of general aviation. They get no respect.
We let them sit unflown for weeks at a time, sometimes months. We deep-discharge them by forgetting to turn off the master switch. Then we jump-start the airplane with a ground power unit and go fly as our alternator fries them with excessive charging current. We fail to check our bus voltage regularly, resulting in long periods of undercharge or overcharge. If we’re lucky, the electrolyte level gets checked once a year at annual inspection time.
Then we cuss them out when the airplane won’t start on a cold Sunday winter morning in Sheepdip, Nebraska, and there’s no mechanic or battery cart on the field.
Not Die-Hards
We probably learned these bad habits from our experience with automobiles. Car batteries are big, heavy, robust brutes that can tolerate this sort of abuse. Aircraft batteries aren’t and can’t. They’re fragile and sensitive. They’re not Die-Hards.
Aircraft batteries are built to be lightweight and compact. They have a small fraction of the capacity of our automotive batteries—typically 10-35 ampere-hours for an airplane battery compared to 100-200 ampere-hours for a car battery. Their lead plates are thin, fragile and closely spaced. They can’t handle much physical or electrical abuse.
Construction and Chemistry
Almost all primary (starting) batteries in piston GA are lead-acid batteries, basically the same kind we use in our cars. Transport jets use mostly nickel-cadmium (NiCd) batteries, while turbine GA uses a mixture of NiCd and lead-acid.
There are two kinds of lead-acid batteries used in piston GA. One is the traditional “flooded-cell” battery that uses lead plates in a liquid sulfuric acid electrolyte bath. The other kind is the sealed battery known technically as “valve-regulated lead-acid absorbed glass mat” or VRLA/AGM. These two kinds of batteries each have their pros and cons, and we’ll be getting into that a bit later.
The chemistry of flooded-cell and sealed lead-acid batteries is identical. Each is constructed with multiple 2-volt cells connected in series—6 cells for a 12-volt battery, 12 cells for a 24-volt battery. Each 2-volt cell contains an array of alternating plates known as “cathode” plates and “anode” plates. The cathode plates are connected to the cell’s positive terminal, and the anode plates are connected to the cell’s negative terminal.
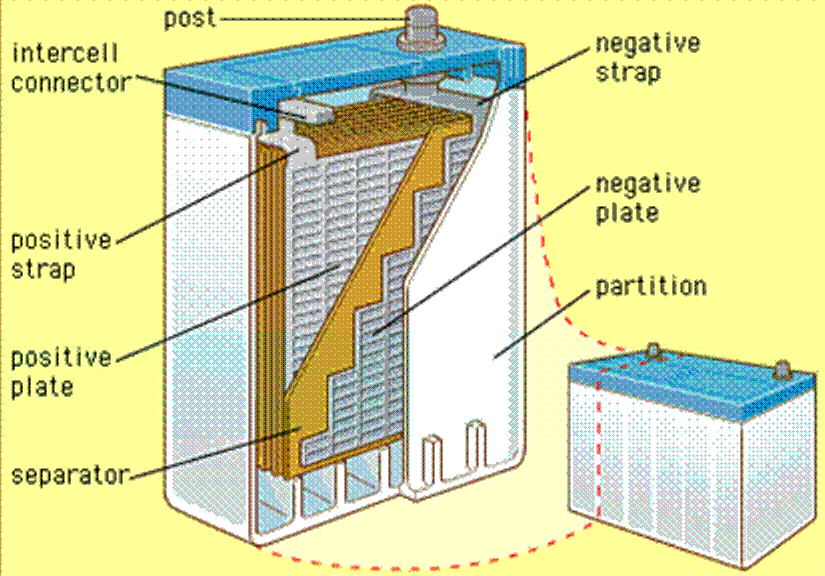
The plates are not flat; they’re intricately formed in a grid-like pattern to maximize their surface area. In fact, they’re sometimes referred to as “grids.”
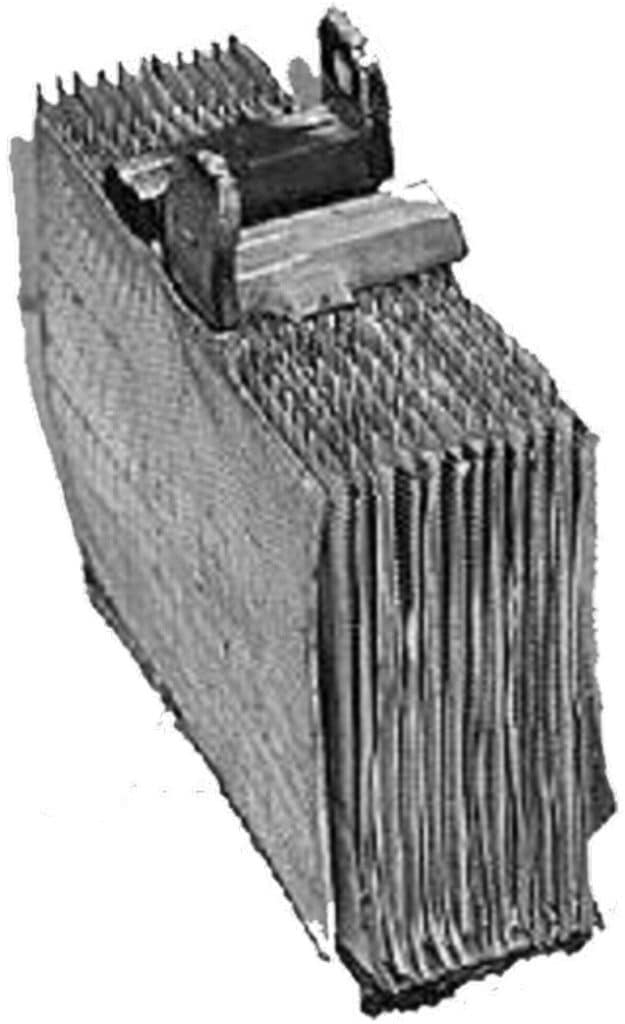
When the cell is in a fully-charged state, the cathode plates are elemental lead (Pb) and the anode plates are lead oxide (PbO2). Both are immersed into an electrolyte consisting of dilute (about 33.5%) sulfuric acid (H2SO4). As the battery discharges, the sulfur and oxygen from the sulfuric acid electrolyte migrates to the plates, and both cathode and anode plates transform into lead sulfate (PbSO4), and the electrolyte becomes increasingly dilute (i.e., mostly water).
As the battery is recharged, the sulfur and oxygen migrate from the plates back into the electrolyte, returning the cathode plates to Pb, the anode plates to PbO2, and the electrolyte to 33.5% H2SO4.
Outgassing
As the cell charges, hydrogen and oxygen gas is liberated and gas bubbles form in the electrolyte. In conventional flooded-cell batteries, those gasses are permitted to escape freely through the vented caps installed on each of the cells. The battery is positively ventilated when the aircraft is in flight to carry off these hydrogen and oxygen gasses so that they don’t form an explosive mixture. When the battery is charged on the ground, it should be done with the battery removed from the aircraft and well-ventilated to prevent the risk of explosion.
In a sealed battery, the liberated gasses are held inside each cell and not allowed to escape. Ultimately they recombine with the electrolyte (which is why these batteries are sometimes called “recombinant gas” or RG batteries). If a cell is overcharged and the gas pressure builds up to a dangerous value, pressure relief valve will open to relieve the excessive gas pressure (hence “valve-regulated lead-acid” or VRLA), but this permanently impairs the capacity of the cell. This doesn’t happen under normal controlled charging conditions.
In sealed batteries, the sulfuric acid electrolyte is immobilized in one of two ways. A gelling agent can be added to the electrolyte to create a “gel cell” battery. Or the electrolyte can be fully absorbed into a glass-fiber mat to create an AGM battery. Gel-cell batteries are frequently used in motorcycle and golf cart applications, and sometimes as backup aircraft batteries. Sealed aircraft starting batteries are always of the AGM variety.
AGM Pros and Cons
The sealed AGM battery—originally developed by Concorde Battery Corporation in the mid-1980s—has a number of significant advantages over the traditional flooded-cell variety.
Because its plates are tightly sandwiched between layers of acid-saturated glass mat, the plates can be made thinner because they don’t need to be self-supporting. This permits AGM batteries to squeeze more plates into a given volume, resulting in a higher energy density that can be as much as 1.5 times that of a comparably sized flooded-cell battery. The AGM construction also results in lower internal resistance, permitting the battery to accept faster charge and discharge rates without being damaged.
In addition, the AGM batteries have a significantly lower self-discharge rate (more about this later), are more resistant to freezing at extremely cold temperatures, and are more tolerant of vibration and physical shock. And of course, they’re “maintenance-free” in the sense that they do not require (or permit) regular adjustment of the electrolyte level the way flooded-cell batteries do.
So what’s not to like about sealed AGM batteries?
Actually, they do have a few disadvantages compared to the traditional flooded-cell battery.
Probably the biggest disadvantage is that AGM batteries are intolerant of deep discharging below about 50% of their fully-charged capacity. By comparison, a flooded-cell battery can be discharged by 80% of capacity without injury. So if your aircraft uses an AGM battery, you really don’t want to leave the master switch on. You also don’t want to run your avionics for any significant time on battery power (say while updating software or databases) without plugging a GPU into the aircraft. We’ve seen quite a few cases where AGM batteries died a sudden and untimely death right after a lengthy maintenance event (typically an annual inspection) where the shop did gear swings or avionics work running off the ship’s battery without external power. That’s a definite no-no with AGM batteries.
Also, the AGM batteries are less tolerant of overcharging than flooded-cell batteries. They will accept faster charge rates, but if you charge them too fast or too long and a pressure-relief valve opens to relieve excess pressure from outgassing, the cell capacity is permanently impaired because there’s no way to add water to the electrolyte as there is with a conventional flooded-cell battery.
Finally, the AGM batteries are more expensive. As I’m writing this, a flooded-cell Gill G-243 battery with acid lists for $624.72 and can be purchased at Aircraft Spruce for $312.95. The comparable Concorde RG-24-15 AGM battery lists for $872.95 and sells at Spruce for $399.95.
Please note the HUGE markup on aircraft batteries! If you have your shop replace your battery, be warned that they’re quite likely to charge you list price (this is standard industry practice). If you replace the battery yourself (which you are permitted to do under the FARs as preventive maintenance), you may save many hundreds of dollars.
What to Buy
There are two companies that make starting batteries for piston GA aircraft: Teledyne Battery Products (who sell them under the “Gill” tradename) and Concorde Battery Corporation. As I’m writing this, both firms sell both kinds of batteries: flooded-cell and sealed AGM.
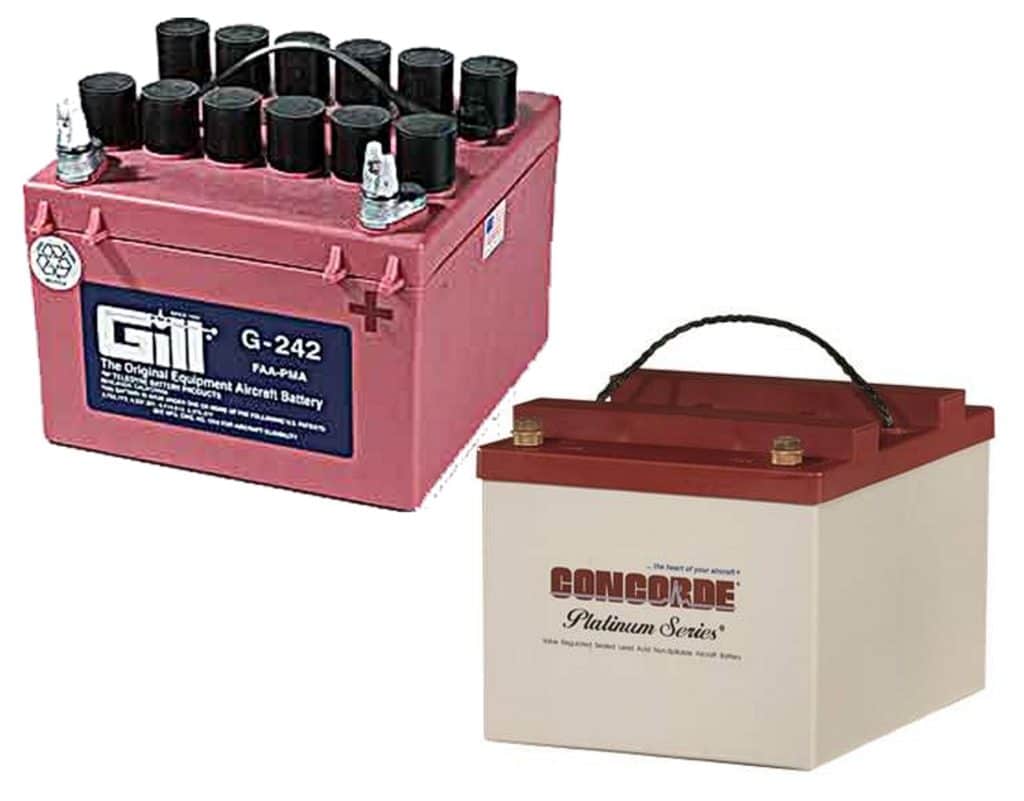
However, Gill’s sealed batteries do not have a good track record in my experience, so I would suggest steering clear of them. And although Concorde does sell flooded-cell batteries, they have announced that they will soon be discontinuing them and offering only the sealed AGM type that Concorde first pioneered 25 years ago.
Therefore, there are really only two viable choices: Gill flooded-cell batteries and Concorde sealed AGM batteries. I have always used the Gill batteries in my own airplane, and my firm generally recommends them to our managed maintenance clients, because they are relatively inexpensive, very reliable, and seem to give more warning before they fail. If you choose a flooded-cell battery, it is extremely important to check the electrolyte level regularly and add distilled water as necessary to avoid allowing the top of the plates to become uncovered.
Many owners prefer the “maintenance-free” sealed Concorde AGM batteries, particularly for aircraft based in hot climates where the lower self-discharge rate of the AGM battery offers a decisive advantage. The AGM batteries are great if you are careful not to let them discharge too far. Use of a GPU during maintenance is a must with these batteries, and use of a trickle charger during periods of disuse is highly recommended.
The care and feeding of aircraft batteries
Charging
Charging a lead-acid battery involves three phases: (1) a constant-current phase during which charging voltage gradually increases; (2) a constant-voltage phase during which charging current gradually tapers off to very low levels as the battery approaches its fully-charged state; and (3) a float (or trickle) charge phase that maintains the battery in its fully-charged condition and offsets the battery’s natural tendency to self-discharge.
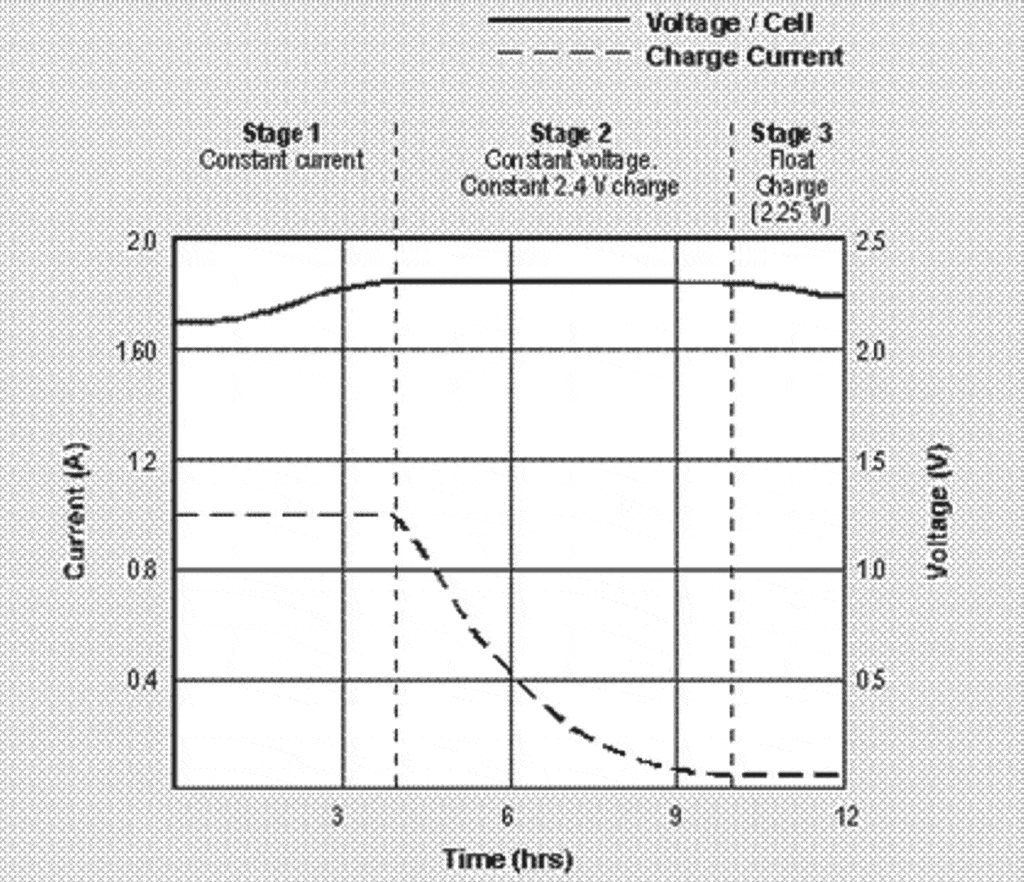
Although this is a fairly complicated procedure, we now have very reasonably priced microprocessor-controlled battery charges that can perform this automatically. Keep in mind, however, that your aircraft’s charging system is strictly a constant-voltage charger, which is why it’s a very bad idea to fly with a deeply discharged battery (e.g., after maintenance or a GPU start). The aircraft’s charging system will charge a deeply discharged battery at an excessive rate (because it is a “dumb” charger without current limiting), and is very likely to damage the battery in the process, sometimes catastrophically.
It’s also important to understand that batteries are exquisitely sensitive to charging voltage. A 12-volt battery requires about 14 volts to attain and maintain a full charge. A 24-volt battery requires about 28 volts. The exact optimal charging voltage depends on battery temperature (see Figure 6). For example, the battery in my Cessna 310 (which runs cool because it’s mounted in the wing) requires a lower bus voltage than the battery in a Cessna 210 (which runs warm because it’s mounted on the firewall inside the engine compartment).
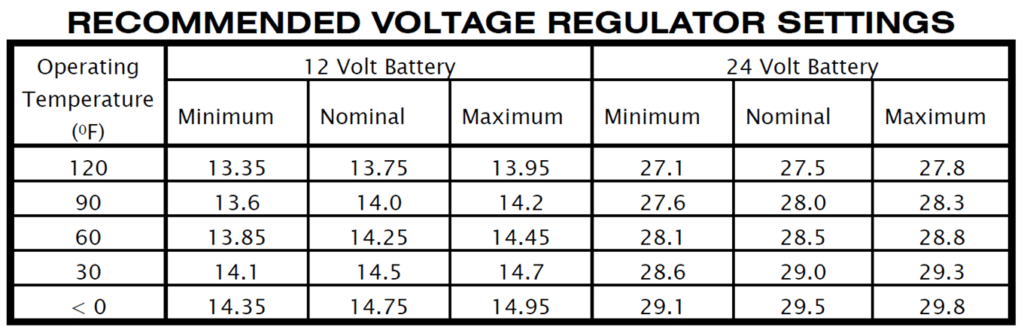
If the aircraft’s voltage regulator is misadjusted by even a few tenths of a volt from the optimum setting, that’s a bad thing. If the bus voltage is too low, then the battery will not charge to its rated capacity, which would be unpleasant in the event of an in-flight charging system failure that forces you to operate solely on battery power. If the bus voltage is too high, the battery will overcharge, overheat, outgas, and possibly lose electrolyte and/or warp or damage its plates; the result is reduced battery lifespan, and occasionally catastrophic failure.
Self-discharge
Lead-acid batteries gradually lose their charge during periods of disuse. If the OAT is warm, the self-discharge may not be so gradual. The self-discharge rate doubles with every 18°F (10°C) increase in temperature.
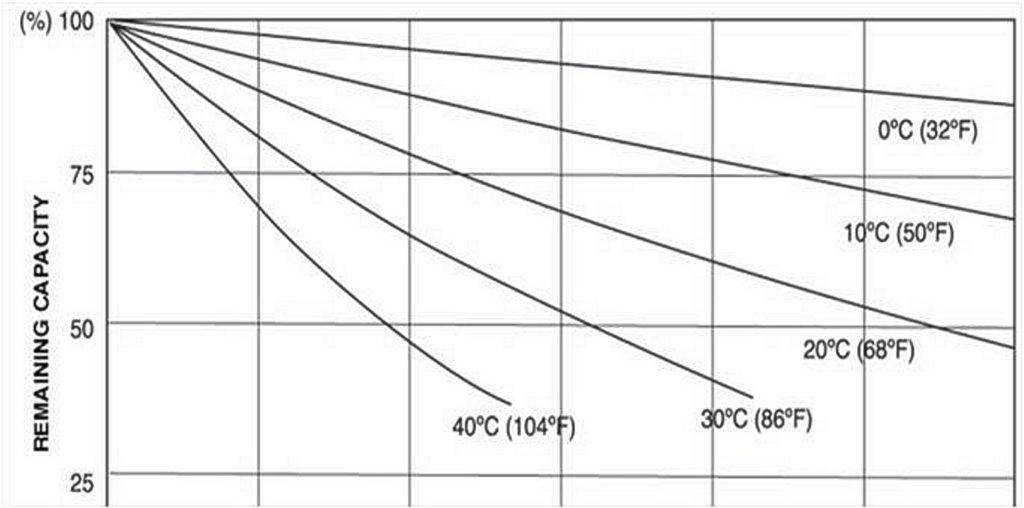
A flooded-cell battery will typically lose 25% of its charge:
- Every 30 days at 77°F
- Every 15 days at 95°F
- Every 7 days at 113°F
An AGM battery will self-discharge more slowly, roughly one-third the rate of a flooded-cell battery. This can be a big advantage for aircraft that are based in hot climates, such as the desert southwest. If you’re based in a hot climate and don’t fly every few days, it probably makes a lot of sense to keep your aircraft battery on a trickle charger between flights.
Sulfation
In last month’s article, we saw that lead sulfate (PbSO4) is deposited on the plates of a lead-acid battery as it discharges. The lead sulfate forms in a powdery “amorphous” state that easily recombines with the electrolyte when the battery is recharged. However, if the battery is allowed to remain discharged for any significant period of time, the lead sulfate will gradually transform into a crystalline state that no longer dissolves. This process is known as “sulfation” and causes battery capacity to decline over time.
Sulfation occurs when the battery is discharged and allowed to remain in that state. It also occurs quite rapidly if the electrolyte level is allowed to decline to the point that the top of the plates are exposed. Thus, the better job you do of keeping the battery fully charged at all times and the electrolyte at the proper level (for flooded-cell batteries), the longer the battery will last. Let it discharge or let the top of the plates get exposed and the lifespan of the battery will be severely compromised.
A process known as “pulse conditioning” may help prevent or reverse sulfation. The process involves charging the battery with voltage pulses intended to break up the crystalline lead sulfate. The effectiveness of pulse conditioning is somewhat controversial. The companies that make pulse-conditioning chargers claim it’s the greatest thing since sliced bread, while the battery manufacturers tend to remain skeptical. I cannot vouch personally for the effectiveness of pulse conditioning, although I’m pretty sure it couldn’t hurt.
Capacity Testing
Both Teledyne-Gill and Concorde have issued Instructions for Continued Airworthiness (ICA) calling for regular capacity testing of their batteries. A capacity test consists of fully charging the battery, then applying a specific load and measuring how long it takes for the battery to discharge. Gill calls for doing an initial capacity test after one year and then every six months thereafter. Concorde calls for doing an initial test after two years and then every year thereafter. In the real world, these capacity tests are sometimes done at annual inspection (and sometimes not), but it’s almost unheard of for them to be done more often. Gill calls for the battery to be replaced when its capacity declines to less than 80% of specifications; Concorde’s replacement threshold is 85%.
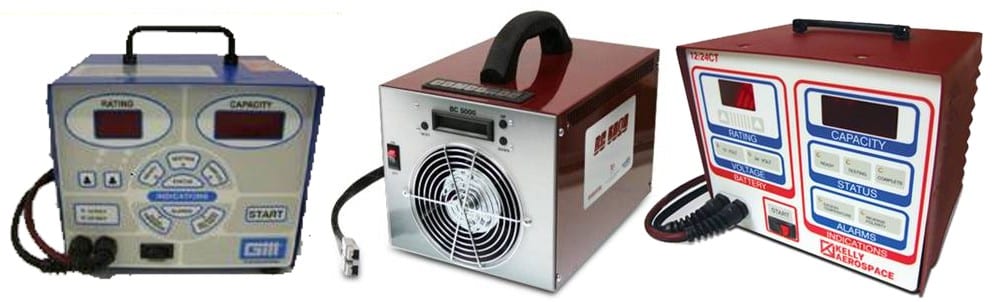
The best way to perform a capacity test is by using an aircraft capacity tester (see Figure 8). Unfortunately, they aren’t particularly cheap—$900 to $1,300 depending on model. Consequently, many maintenance shops don’t own one and so many aircraft batteries never get capacity checked.
It is possible to do a rough “do-it-yourself” capacity check without using a capacity tester. This is done by charging the battery fully, then turning on enough electrical equipment to drain the battery at a rate in amps equal to the battery’s rated one-hour discharge rate in ampere-hours. (E.g., a discharge rate of 12 amps for a battery rated at 12 ampere-hours.) Measure how much time it takes to fully discharge the battery to 10 or 20 volts (for a 12 or 24 volt battery, respectively). A new battery should take 60 minutes to discharge. An older battery will take less. If the battery fully discharges in 48 minutes, then the battery capacity has declined to 80% and it’s time to replace it.
Be sure to charge the battery immediately following any capacity check. Leaving them discharged is a sure way to hasten their demise.
Battery Chargers
Nowadays there are some very sophisticated yet inexpensive battery chargers available for aircraft use. In my opinion, every aircraft owner should own one.
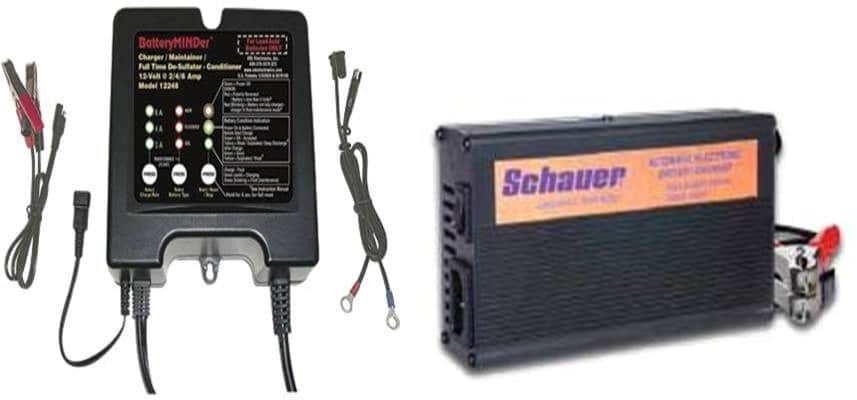
One of the very best is the BatteryMINDer from VDC Electronics. Model 12248-AA-S1 is an 8-amp charger for 12-volt aircraft batteries, and model 24041-AA-S2 is a 4-amp charger for 24-volt aircraft batteries. Both models provide automatic three-phase charging and pulse conditioning. They are fully automatic—set it and forget it—and will not harm the battery even if left on 24/7. (To the contrary, leaving the charger on 24/7 is the best thing you can do for maximum battery longevity during periods of disuse.) Both models are priced under $200.
If $200 is above your budget, Schauer makes two automatic chargers designed for aircraft batteries. The model JAC1212 is a 12-amp 12-volt charger, and the JAC0524 is a 5-amp 24-volt charger. Both offer fully automatic three-phase charging, but neither does pulse conditioning. Both are bargain-priced under $80.
You bought a plane to fly it, not stress over maintenance.
At Savvy Aviation, we believe you shouldn’t have to navigate the complexities of aircraft maintenance alone. And you definitely shouldn’t be surprised when your shop’s invoice arrives.
Savvy Aviation isn’t a maintenance shop – we empower you with the knowledge and expert consultation you need to be in control of your own maintenance events – so your shop takes directives (not gives them). Whatever your maintenance needs, Savvy has a perfect plan for you: