Even a seemingly trivial mistake by a well-intentioned mechanic can have dire consequences.
On April 19, 2005, a 1966 Beechcraft Debonair was cruising at 8,500’ on a VFR flight from Van Nuys to San Jose, Calif., when the pilot heard a loud noise and the Continental IO-550 engine started running rough. The pilot checked the oil pressure and oil temperature gauges and found both had normal readings in the green. He throttled back, advised Oakland Center that he was diverting to Paso Robles, and began descending.
Then there was another loud bang from the engine compartment, engine RPM dropped dramatically, and the cockpit started to fill with white smoke. The PIC—a 32-year-old 500-hour commercial pilot who had recently earned his CFI—throttled back to idle, made a mayday call to Oakland Center, and established an 80-knot glide. The smoke cleared from the cockpit and the pilot determined that he was within gliding distance of Paso Robles Airport.
Just as it seemed like the story might have a happy ending, the Debonair’s lefthand engine cowling door popped open and stayed open. That increased drag and caused the rate of descent to increase to nearly 1,000’/minute. The pilot now realized he wasn’t going to be able to make the airport.
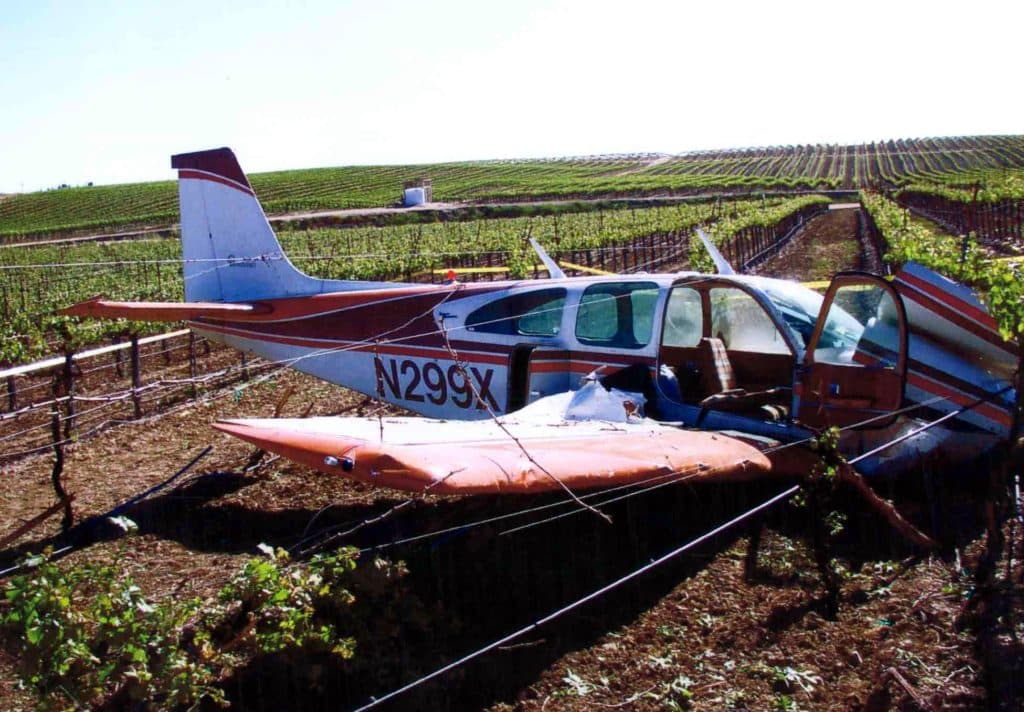
He set up for an off-airport landing in what he thought was a green field about two miles short of the airport. At the last minute he realized that it was a vineyard and his flight path was at a 45-degree angle to the rows. The pilot extended the landing gear in an attempt to mitigate the impact, but the left main gear snagged a grapevine row pole and wires. The aircraft veered left and stopped abruptly.
Both the pilot and his right-seat passenger were wearing lap belts, but the aircraft was not equipped with any upper-body restraints. (Shoulder belts were not offered by Beech when the airplane was built in 1966, and no regulation required that they be retrofitted.) Both pilot and passenger sustained serious injuries when their heads struck the instrument panel. The 44-year-old passenger was knocked unconscious, and his head trauma tragically resulted in permanent brain injury.
NTSB investigation
The NTSB conducted an investigation into the accident and issued its probable-cause report about a year later. The investigation included a detailed examination of the engine by the Safety Board investigator-in-charge and a technical representative of Teledyne Continental Motors.
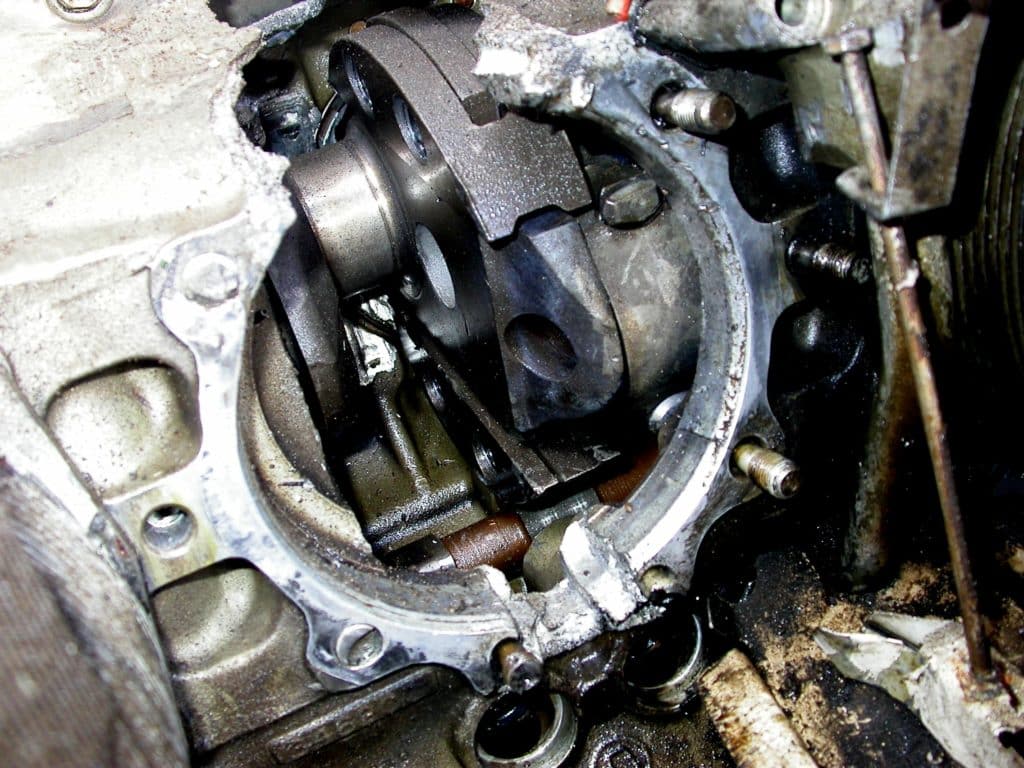
The post-accident engine examination revealed that the #4 cylinder and piston had departed the engine in-flight; they were never recovered. The two righthand cylinder hold-down studs appeared relatively undamaged, but their hold-down nuts had backed off. The four remaining hold-down studs were sheared, and both through-bolts were sheared as well. The #4 connecting rod punctured a 3” x 7” hole in the top of the crankcase. The #4 connecting rod, cap and rod bolts and nuts were recovered from inside the engine cowling, as were most of the sheared-off studs, through-bolts and nuts.
The engine logbook entry for the June 2004 annual inspection conducted 10 months prior to the accident indicated that cylinders 2, 4, 5 and 6 had been removed and replaced with four overhauled cylinders. The engine had subsequently undergone a 100-hour inspection and then a 50-hour oil change. No defects were noted.
The NTSB concluded the obvious:
“The National Transportation Safety Board determines the probable cause(s) of this accident to be the separation of the #4 engine cylinder due to improperly torqued cylinder hold-down nuts. A finding in this accident was the lack of a shoulder restraint system in the airplane, which contributed to the occupants’ injuries.”
Ah, but the story didn’t end there…not by a long shot. As so often happens these days, it ended up in court. The ensuing litigation revealed that there was a whole lot more to this accident than what the NTSB found. (That’s why I’m writing this article.)
The smoking gun
The brain-injured passenger sued. Defendants included the PIC, the corporation that owned the Debonair, the repair station that maintained it (and performed the cylinder replacement), and engine manufacturer Teledyne Continental Motors. The litigation went on for five years, and culminated in a jury trial in 2010 in California Superior Court.
The lead attorney for the plaintiff was himself a GA pilot and aircraft owner who had enough experience doing owner-assisted annuals on his Grumman American Tiger that he knew his way around a toolbox, a maintenance manual, and FAR Part 43. In reviewing the photographs taken during the NTSB’s examination of the engine, the attorney discovered something crucial that the NTSB missed: a number of dabs of light brown sealant on the cylinder deck area of the crankcase where cylinders 2, 4, 5 and 6 were attached. This was literally the “smoking gun” that explained precisely why the #4 cylinder departed the engine in-flight.
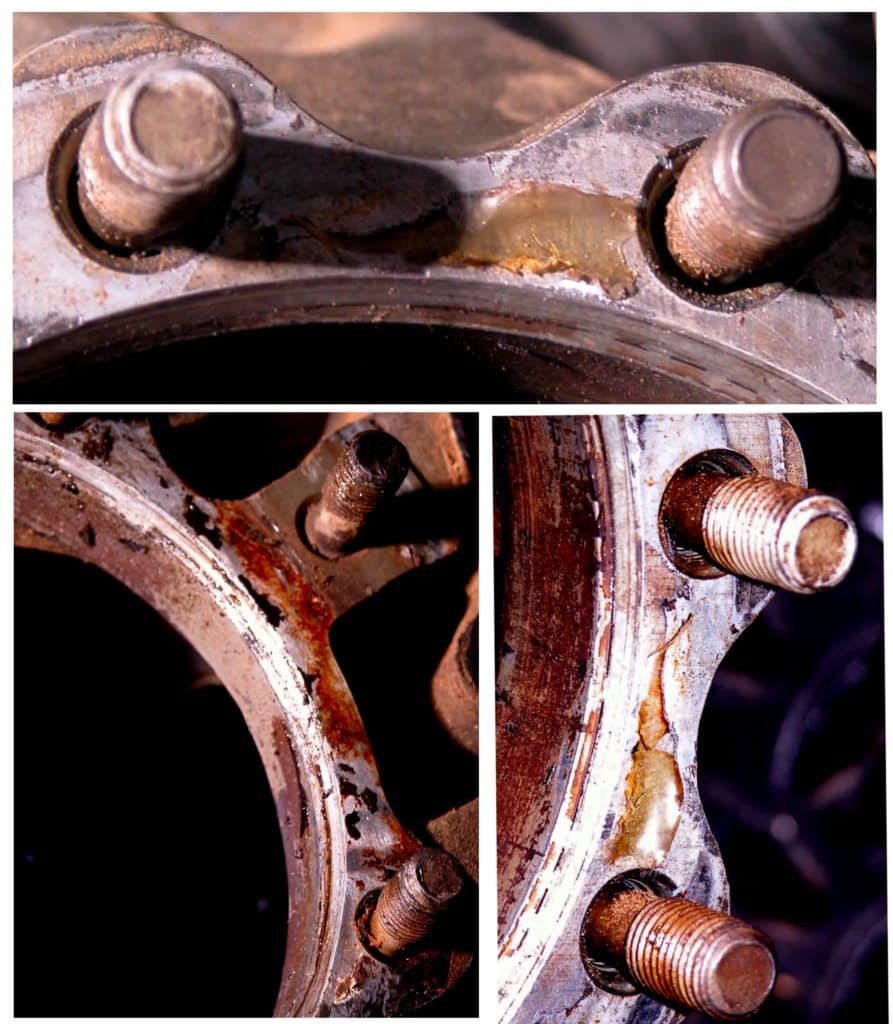
The mating surfaces of the crankcase’s cylinder deck and the cylinder’s mounting flange need to be perfectly clean when the cylinder is mounted and its hold-down nuts are torqued up. Any sort of contamination of those surfaces—even a thin coat of paint—is enough to cause the hold-down studs to lose their pre-load and ultimately to fail. The presence of even a tiny dab of flexible sealant on the mating surfaces could have disastrous consequences. Any competent A&P mechanic who works on piston aircraft engines knows this (or at least should know it).
So how the heck did the sealant get on the cylinder deck?
Discovery
In a videotaped deposition, the young mechanic who had installed the cylinders in June 2004 readily admitted that he had applied a sealant called “Gasket Maker” (TCM part number 646942) to the cylinder base O-rings when he installed the four cylinders. He had installed cylinders on TCM engines on a number of prior occasions and was quite familiar with the process. However, this was the first time he’d ever applied Gasket Maker to the cylinder base O-rings.
The young mechanic also acknowledged that he did not hold an FAA mechanic certificate at the time he did the cylinder work on the accident airplane, although he had earned his A&P subsequently. As an uncertificated apprentice mechanic, he had been working under the supervision of a senior A&P/IA who signed off his work. (The use of uncertified apprentice mechanics is quite common in FAA-certified repair stations, and is explicitly permitted by FAR Part 43.)
So why did the apprentice mechanic decide to use Gasket Maker on the cylinder base O-rings this time, a departure from the procedure he’d been taught and used on previous occasions? The answer to that question was interesting.
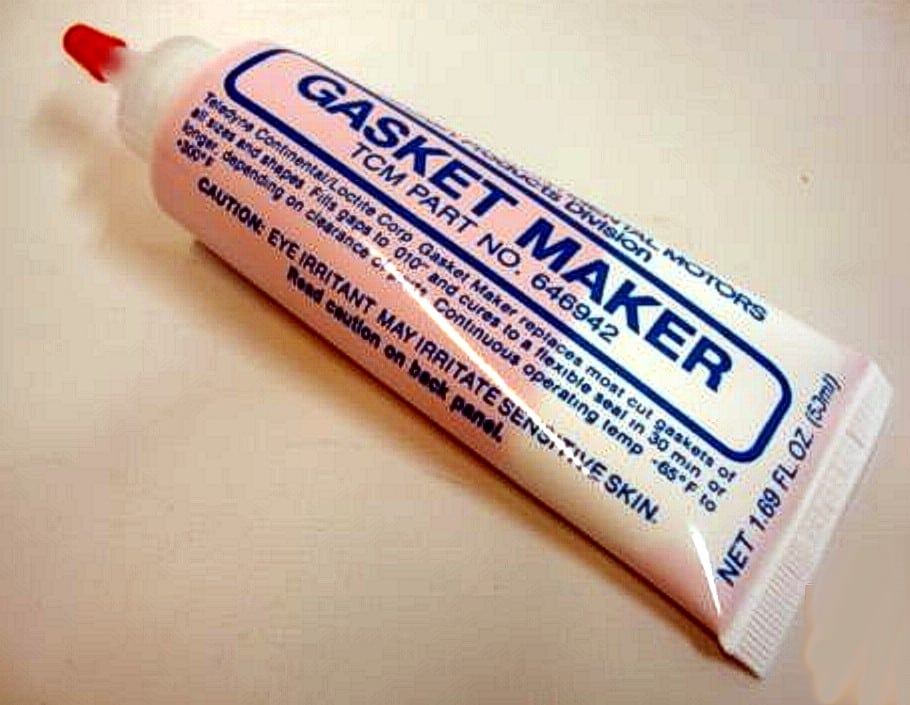
It turns out that shortly before the Debonair’s annual commenced, the repair station had hosted an American Bonanza Society service clinic. A TCM technical representative was in attendance at the service clinic, and was touting a new TCM product called Gasket Maker as the ultimate solution to preventing and correcting oil leaks in TCM engines. In his deposition, the apprentice mechanic stated that he asked the TCM tech rep where Gasket Maker could be used, and was told “anywhere you have a leak.” Immediately after the service clinic ended, the apprentice mechanic ordered a tube of TCM Gasket Maker for his toolbox and was on the lookout for opportunities to use it.
When it came time to install the four cylinders on the Debonair’s engine, the apprentice mechanic consulted with a senior A&P to determine whether using Gasket Maker on the cylinder base O-rings would be appropriate. The A&P had no familiarity with the TCM Gasket Maker product, so he consulted the section of the TCM IO-550 maintenance manual that listed approved lubricants, sealants and adhesives. In that section, he found a reference to Gasket Maker that listed a number of specific applications, followed by a catch-all item indicating that Gasket Maker was appropriate for use on “all uncoated oil seals.”
The A&P then looked up the cylinder base O-ring in the IO-550 illustrated parts catalog, and found that it was listed there as a “seal.” After some discussion, the apprentice mechanic and the senior A&P agreed that a cylinder base O-ring was indeed an “uncoated oil seal” and therefore the use of Gasket Maker was appropriate.
So the apprentice mechanic applied Gasket Maker to the cylinder base O-rings before installing the four cylinders on the Debonair’s engine. When he torqued down the cylinder hold-down nuts, the sealant on the O-rings was extruded onto the mating surfaces of the cylinder base flange and the crankcase cylinder deck. About 150 hours later, the #4 cylinder departed the engine and the Debonair fell out of the sky.
Trial and verdict
When the case finally came to trial in 2010, the plaintiff’s attorney knew that he had to convince the jury that TCM was at least partially to blame for the accident, because none of the other defendants had any significant assets or insurance. Although the apprentice mechanic clearly screwed up by using sealant on the cylinder base O-rings, the attorney made sure that the jury understood that the mechanics were trying to do the right thing after consulting the appropriate TCM manuals. The manuals weren’t particularly helpful, stating that Gasket Maker could be used on “all uncoated oil seals.”
The jury might have let TCM off the hook altogether but for one thing: TCM’s expert conceded under cross examination that TCM knew of other incidents where their engines came apart because mechanics had applied Gasket Maker to cylinder base O-rings, yet had not revised its manuals to make it clear that this was not an acceptable use for the product.
In the end, the jury awarded $15 million in damages to the brain-injured plaintiff. They assessed comparative fault to the various defendants as follows: 55% for the repair station that worked on the engine for its inappropriate use of sealant, 35% for TCM because it failed to warn against doing so, and 10% for the PIC because his forced landing in the vineyard left a lot to be desired. However, under California law (as in many other states), each defendant is liable for 100% of the economic damages (e.g., medical expenses, loss of future income), but only for its proportionate share of non-economic damages (e.g., pain and suffering). Since the other defendants had little ability to pay, TCM wound up being on the hook for the lion’s share of the $15 million award.
Takeaways
Aircraft owners need to understand that invasive piston engine maintenance—particularly cylinder removal—is fraught with peril. There are countless little details that have to be done exactly right. Even a seemingly insignificant error or omission can have catastrophic consequences.
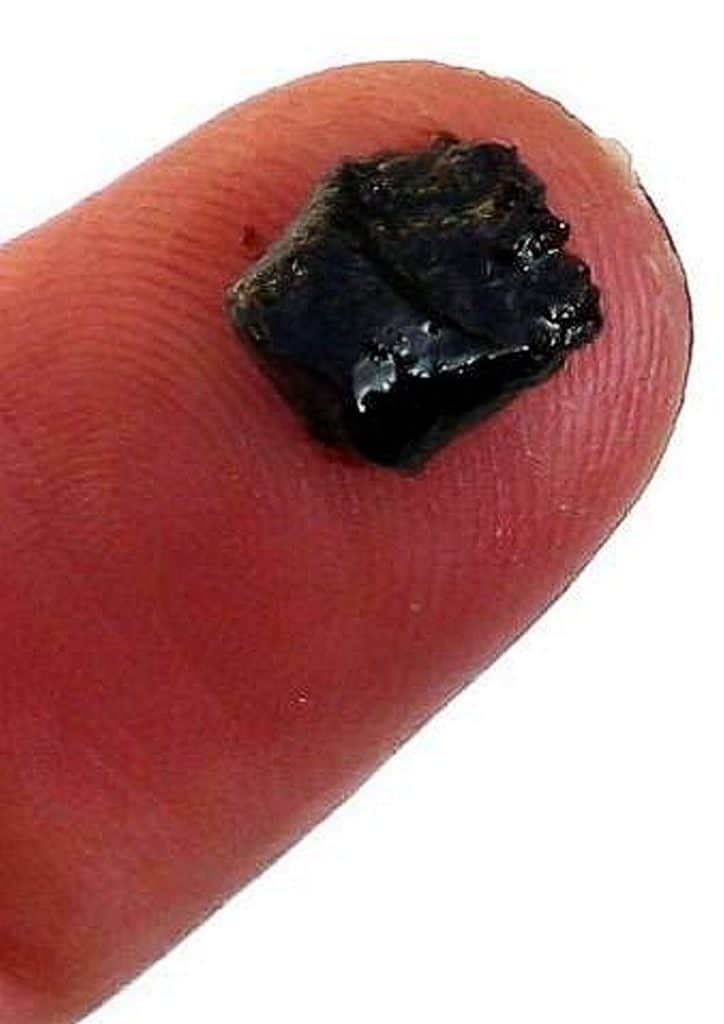
Owners also need to understand just how commonplace it is for critical work like this to be performed by young, inexperienced, and often uncertificated mechanics (affectionately known as “nuggets”), even at large FAA-certified repair stations. It takes 30 months of full-time aircraft maintenance experience to earn an A&P certificate. How do you suppose most mechanics obtain that experience so they can qualify to take their A&P exam? By swinging wrenches on airplanes—quite possibly on your airplane. In this case, the apprentice mechanic was actually a bright, thoughtful, conscientious fellow who was really trying to do the right thing. But a little dab of Gasket Maker no larger than a pea brought down the Debonair and seriously injured its two occupants.
Finally, owners need to understand the extent to which the threat of litigation casts a chilling shadow over every person and company involved in building, maintaining and operating aircraft. If you wonder why aircraft, engines and parts are so expensive, consider the cost of product liability that everyone involved in the industry has to bear.
Epilogue
As a result of this lawsuit, Continental has added the following warning to its technical publications:
WARNING
Apply Gasket Maker only as directed. The improper use of sealants may cause engine malfunction or failure. Do not apply any form of sealant to the crankcase cylinder deck, chamfer, cylinder mounting flange, cylinder base O-ring, or cylinder fastener threads. The use of RTV, silicone, Gasket Maker or any other sealant on the areas listed above during engine assembly will cause a loss of cylinder deck stud or through-bolt torque. Subsequent loss of cylinder attachment load, loss of main bearing crush and/or fretting of the crankcase parting surfaces will occur. The result will be cylinder separation, main bearing movement, oil starvation and catastrophic engine failure. USE ONLY CLEAN 50 WEIGHT AVIATION ENGINE OIL ON SURFACES LISTED.
You bought a plane to fly it, not stress over maintenance.
At Savvy Aviation, we believe you shouldn’t have to navigate the complexities of aircraft maintenance alone. And you definitely shouldn’t be surprised when your shop’s invoice arrives.
Savvy Aviation isn’t a maintenance shop – we empower you with the knowledge and expert consultation you need to be in control of your own maintenance events – so your shop takes directives (not gives them). Whatever your maintenance needs, Savvy has a perfect plan for you: