What to look for when choosing an A&P to work on your aircraft.
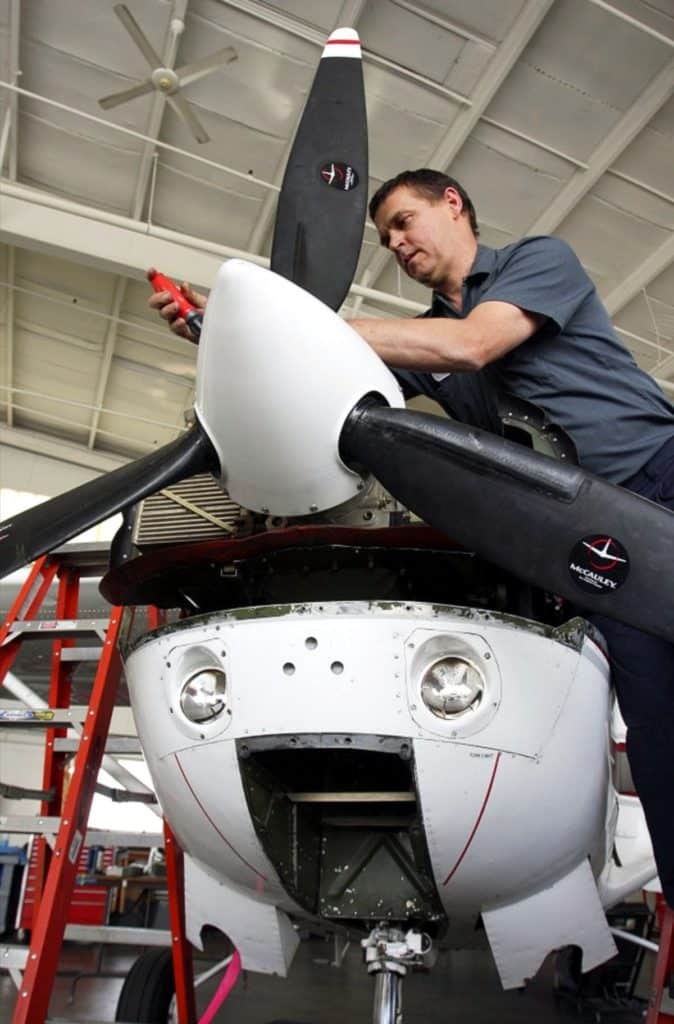
Over the past 45 years, I’ve had the opportunity—and often the privilege—of working with hundreds of aircraft mechanics. At first it was as a naïve aircraft owner having them perform inspections and repairs on my airplane. Later it was as a student and apprentice swinging wrenches under their supervision as I struggled to learn their craft. More recently, having become an A&P/IA myself, it has been mostly as a colleague consulting about thorny mechanical problems with hundreds of my clients’ airplanes (and occasionally my own).
I’m greatly indebted to these mechanics—some more than others—for they taught me everything I know about aircraft maintenance, and also a good deal about human nature.
I never cease to be struck by the remarkable variety of talented people involved in aviation in general, and in aircraft maintenance in particular. Some of the finest aircraft mechanics I’ve ever known come across loquacious and cock-sure, while others are taciturn and exude quiet confidence. Some seem to have heads bursting with knowledge and expertise, while the wisdom of others seems to be focused in their steady, calloused hands. Some approach aircraft problems thoughtfully and analytically, while others seem to rely almost entirely on experience and instinct. Some accomplish their work with great skill and lightning speed, while others are slow and meticulous. About the only attribute they all seem to have in common is uniqueness; no two are the same.
A dozen things to look for
I’ve thought quite a bit about the most important characteristics an aircraft mechanic should have, and identified a dozen specific attributes that I look for when choosing an A&P. To my way of thinking, the ideal mechanic is…
- Communicative. A mechanic’s willingness and ability to communicate with customers is right at the top of my list of important attributes. Any time I put my aircraft in the shop, I want to feel confident that I’ll be kept “in the loop” and that I’ll have ample opportunity to participate in all significant maintenance decisions. What I don’t want is surprises. I need a mechanic who’ll communicate throughout the maintenance process, keeping me apprised of what’s going on with the aircraft, and ask me what I want to do whenever any decisions need to be made.
- Owner-friendly. Some mechanics are simply not comfortable working with maintenance-involved owners. Their attitude is “you hired me to maintain your aircraft, so leave me alone and let me do my job.” I can’t tolerate an attitude like that. I want a mechanic who welcomes my visits to the shop, who is happy to let me watch and ask questions, and who is open to owner-assisted annuals and owner-performed preventive maintenance. I think A&Ps need to be mindful that the FAA holds the OWNER primarily responsible for maintaining the aircraft in airworthy condition. Of course, I also think owners need to be mindful that the mechanic’s A&P certificate is on the line whenever he signs a logbook entry approving the aircraft for return to service. That’s why aircraft maintenance ought to be a team sport. Under the FARs, the owner is responsible for deciding what maintenance is to be done and when to do it, and the mechanic is responsible for performing the work properly and documenting it accurately.
- Thoughtful. By “thoughtful” I don’t mean “considerate” (as in a mechanic who sends Christmas cards to his customers), but rather “full of thought” (as in a mechanic who takes the time to think carefully and critically about a squawk before trying to fix it). One of my biggest gripes is with A&Ps who try to “shotgun” aircraft problems by replacing parts (usually expensive ones) instead of troubleshooting them methodically to determine where the fault lies. The best mechanics with whom I’ve had the privilege of working have always been those who are at least as strong at headwork as they are at handwork.
- Reasonable. As an owner, I want my mechanic to listen to my requests, to make a good-faith effort to accommodate them if he considers them to be reasonable, and to discuss them with me in a reasonable fashion if he thinks they’re not. I’ve had the distinct displeasure of having to deal with otherwise excellent mechanics whose only flaw was that they took a dogmatic, “my way or the highway” approach when dealing with owners. Sadly, this isn’t uncommon. I’ve lost count of how many times I’ve received calls and emails from frustrated aircraft owners who tell me, “my mechanic says he won’t sign off my annual unless I agree to do xxxxx.” I consider such strong-arm tactics by any mechanic to be the kiss of death, however well-intentioned. My company manages more than 500 annual inspections per year, and once or twice a year we find it necessary to instruct an unreasonable IA to sign off the annual with discrepancies (rather than comply with his unacceptable demands) and then find another mechanic who has his head screwed on straight to approve the aircraft for return to service. It doesn’t happen often—perhaps 0.5% of the time—but any IA who pulls such a stunt gets red-flagged so he won’t ever be hired again to do annuals on my clients’ airplanes.
- Experienced. It goes almost without saying that I want my mechanic to be a seasoned veteran. When a repair is necessary, I want a mechanic who’s “been there, done that.” I just as soon not have someone go through a learning curve on my aircraft and on my nickel.
- Knowledgeable in type. When it comes to troubleshooting a thorny problem or performing a really thorough annual inspection, there’s no substitute for a mechanic who has extensive knowledge and experience with the particular aircraft make and model involved. In this regard, “time in type” can be much more important than “total time.” In the heyday of piston GA prior to 1980, the major aircraft manufacturers provided a network of specialized service centers staffed with mechanics who worked on nothing but a handful of models and knew them cold. Nowadays, such specialized service facilities are few and far between, but it’s worth the search.
- Up-to-date. I’ve stressed the importance of general experience and experience in type. Be aware, however, that there’s a possible downside to using a graybeard mechanic who’s been swinging wrenches on airplanes since Orville and Wilbur’s coin-toss. I’m talking about the possibility that your seasoned veteran mechanic hasn’t kept his knowledge up-to-date. A fundamental flaw in our current system is that there’s no recurrent training requirement whatsoever for A&P mechanics (and I certainly think there should be). So don’t be surprised if your old-timer still believes that a big-bore Continental jug must be pulled if it measures 59/80, or that a new cylinder requires non-AD oil for break in, or that LOP operation burned exhaust valves, or who doesn’t own and use a borescope. Do take advantage of your graybeard’s decades of experience, but be sure to keep your Old Wives Tale detector turned onand make sure you keep your own knowledge up-to-date.
- Cost-conscious. I know quite a few aircraft owners for whom money is no object when it comes to their airplanes. Unfortunately, I’ve never had the luxury of being one of them. The high cost of flying is a big deal to me, so mechanics who go out of their way to help me save money on maintenance, especially on replacement parts, tend to quickly earn my undying loyalty. Those who insist that all parts must be new from the original manufacturer, and who don’t offer me the alternative of choosing of lower-cost aftermarket, overhauled, continued-time, or salvage yard parts where appropriate get crossed off my good-guy list. (Mechanics who are aircraft owners themselves are sometimes more sensitive in this area.)
- Skillful. Certain maintenance operations require special skills. Examples include welding, painting, sheet metal repairs, upholstery work, deice boot installation, and autopilot repairs. If my aircraft needs this sort of work, it’s very important to determine whether or not my regular mechanic has the requisite skill, or whether I would do better taking the aircraft to a specialist who does this kind of thing every day.
- Fast and efficient. During my years of doing owner-assisted annuals, I spent a fair amount of time hanging around maintenance shops and observing other aircraft being worked on by the A&Ps. I was often struck by the differing paces of the various mechanics I watched. Some mechanics could consistently get routine tasks done much more quickly than others. Sometimes the quickest mechanic could get a job done in half the time that the slowest mechanic took. (Of course, the slowest mechanic was still twice as fast as me.) Interestingly, I observed that the fast guys didn’t seem to be cutting corners or doing sloppy work; they simply operated at a more intense and efficient pace, and were less apt to get distracted. If I’m paying for routine maintenance by the hour, I’ll take Fast Eddy, thank you.
- Meticulous and exacting. On the other hand, there are some tasks where I’d prefer to have a mechanic who is a real a fussbudget, more interested in doing the job flawlessly than getting it done quickly. Examples might be avionics or instrument installation, changing a cylinder, or major disassembly of a retractable landing gear—all tasks where there’s obviously no room for error. I also really appreciate it when a mechanic takes the time to write up a half-page of detailed notes in my maintenance logbook at the end of an annual inspection, rather than dashing off a quick one-line-plus-rubber-stamp entry of the sort I so often see in other owners’ logbooks. Another observation: The Fast Eddy types aren’t usually well-suited to supervising owner-assisted maintenance, since they tend to be frustrated by the snail-like pace at which amateur mechanics work and the innumerable elementary questions they ask.
- Accessible. Finally, finding the world’s greatest aircraft mechanic doesn’t help if he’s not available when you need him. The best ones are typically booked up for months in advance. If your aircraft is AOG and you have an important business trip the day after tomorrow, can your terrific mechanic work you into his schedule? In a similar vein, many aircraft owners depend on a mechanic or shop located at a different airport than the one where the aircraft is based. Such an arrangement often results in squawks being deferred rather than fixed promptly, and can be a huge problem if the plane develops a problem that makes it unflyable. If your primary-care mechanic is located away from home base or otherwise inaccessible, you really need to have a “Plan B” for use when you need an unscheduled repair right here and right now.
Quest for the ideal mechanic
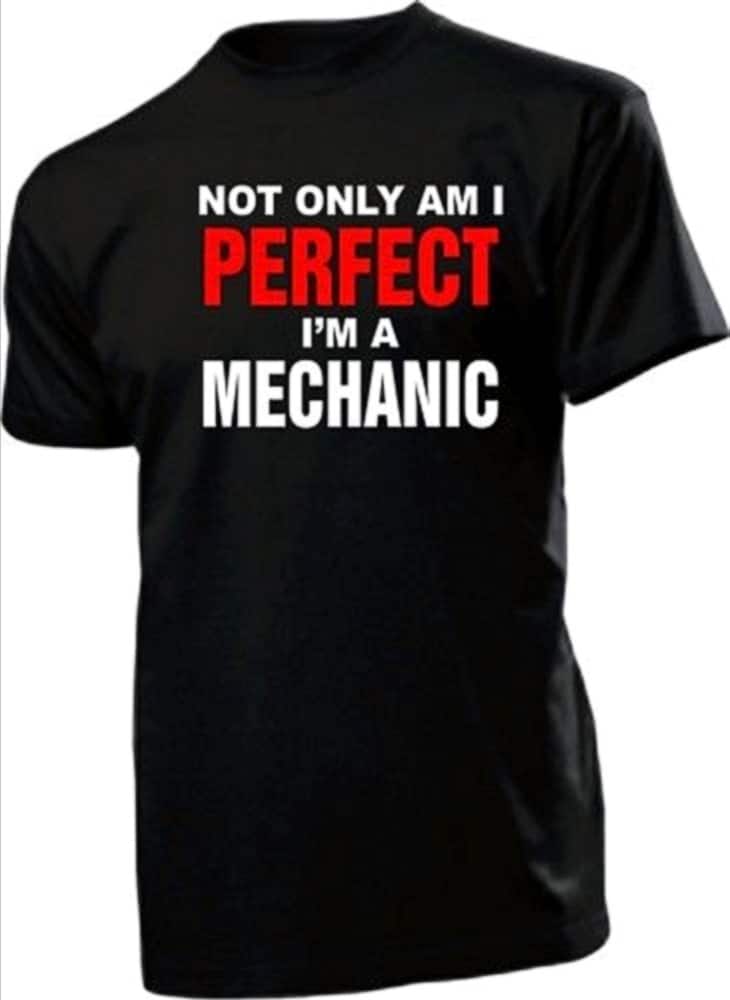
In a perfect world, your mechanic would score an A+ on all 12 of these attributes. In the real world you’ll never find one who does. (At least I haven’t found one in 45 years of looking.) So what’s an owner to do?
First, you need to develop an accurate assessment of your mechanic’s strengths and weaknesses. Then, you need to come up with a strategy for taking advantage of his strengths and overcoming his weaknesses.
What’s the best way to assess a mechanic’s strengths and weaknesses? One of the best ways is simply to ask him for an honest self-assessment. Most mechanics are acutely aware of their own aptitudes and shortcomings, and most will be straight with you if you simply ask.
If you asked me for my own self-assessment as a mechanic, for instance, I’d tell you that I’m strong on headwork and weak on handwork. Not to brag (ahem), but I consider myself one of the best natural-born troubleshooters I’ve ever encountered. I’m also extremely careful and meticulous and very seldom make an error of omission (like forgetting to tighten something). On the other hand, I was born with ten thumbs and my manual skills are sorely lacking. I don’t think I’ve ever painted anything that didn’t end up with runs and sags, or ever riveted anything that didn’t require at least one rivet to be drilled out and redriven. During my A&P practical test, the examiner took one look at my welding samples and made me promise I’d never try to weld anything on an actual airplane. I’m also without doubt the slowest wrench in all of aviation; if I worked on airplanes for a living, I couldn’t charge more than ten bucks an hour.
So buy your A&P a tall cold one and ask him to tell you a little about his background, and what he thinks his strongest and weakest areas are. Ask him his philosophy about communicating with customers, how he feels about owner-assisted annuals, and what he thinks about the stratospheric cost of replacement parts. I bet you’ll learn a lot about what makes him tick.
It’s also an excellent idea to talk to some of the mechanic’s customers and find out what their experiences have been—good , bad and/or ugly. A little time spent interviewing a mechanic and a few of his customers will almost always yield the information you need to size him up. Once you have figured out the shortcomings of your mechanic, it’s often not too difficult to work around them.
Case in point
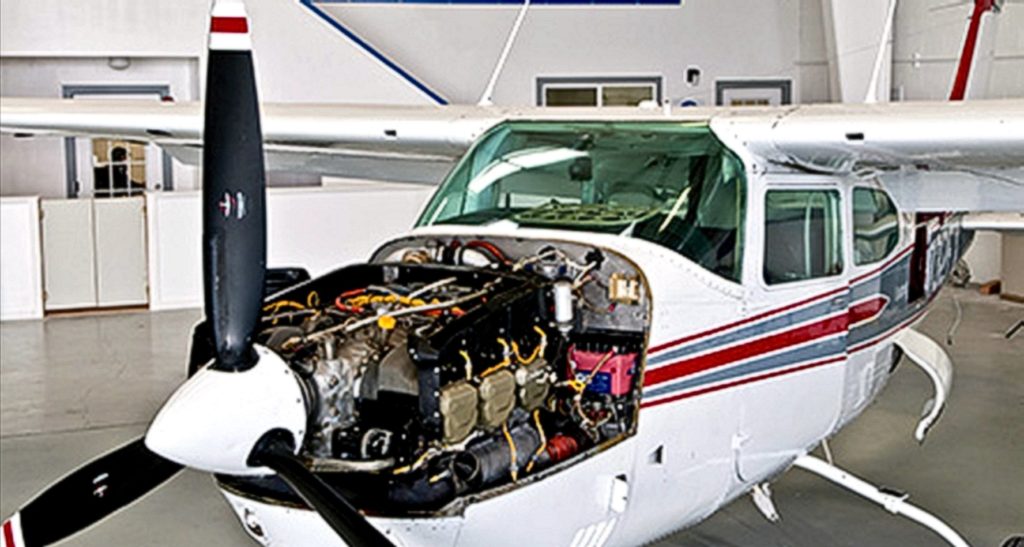
I recall being contacted by a Cessna 210 owner who found himself in the position of having to switch mechanics on short notice. It seems that the shop he’d been using closed down and his longtime mechanic went to work for corporate flight department:
I really liked my old mechanic. He always did something that I did not realize was unique: He performed the annual inspection, wrote up a squawk sheet, and then asked me to come by the shop. He then went over every squawk with me, showing me each problem on the airplane and giving me an estimate to fix it. For some squawks, he’d tell me “there’s no choice, this has to be fixed.” For others, he’d say it was my choice, but would explain the possible repercussions if the problem wasn’t fixed. Sometimes he’d offer recommendations: “You can probably let this one go until next year.” I always walked out of that session having a good idea of the overall cost before any work was done, and feeling that I was in the loop. I really, really liked that approach!
When the Cessna 210 came due for its next annual, this owner took the airplane to a new shop that had just opened on the field. His decision to use this shop was in large part due to the fact that the new shop’s owner had recently retired as an aircraft mechanic for the state highway patrol, where he’d maintained the agency’s fleet of Cessna 210s for the past 20 years:
Excellent, I thought. With 20 years of experience maintaining Cessna 210s, how could I go wrong?
To make a long story short, at the end of the annual I received a shocker of a bill! My new mechanic didn’t go over the squawk sheet with me before doing the work. About half the things on the bill were things I knew were coming, but the other half came as a complete shock. Many of the items were discretionary things that I might have elected to defer had I been given the choice.
In hindsight, I realized that my new mechanic had spent the past 20 years maintaining Cessna 210s but never talking to customers! The highway patrol airplanes he worked on did not have “owners” in the normal sense of the word. These were government-owned airplanes, so all squawks were fixed automatically and cost was something that never entered the equation.
In short, the new mechanic scored A+ on “experienced” and “knowledgeable in type,” but C- on “communicative” and “cost-conscious.”
Does this mean that the owner shouldn’t use this mechanic again? Of course it doesn’t. What it does mean is that the owner needs to sit down with the mechanic and explain the rules of the road:
Mr. Mechanic, when I bring you my Cessna 210 for annual, I would like you to call me when you’ve completed the inspection but before you perform any repairs or order any parts so that we can go over the squawk sheet together and decide which items to fix and which to defer. To help me make informed decisions, I would appreciate it if you’d prepare a cost estimate to fix each squawk, and identify which ones you consider to be critical safety-of-flight items that should not be deferred.
You bought a plane to fly it, not stress over maintenance.
At Savvy Aviation, we believe you shouldn’t have to navigate the complexities of aircraft maintenance alone. And you definitely shouldn’t be surprised when your shop’s invoice arrives.
Savvy Aviation isn’t a maintenance shop – we empower you with the knowledge and expert consultation you need to be in control of your own maintenance events – so your shop takes directives (not gives them). Whatever your maintenance needs, Savvy has a perfect plan for you: