Recently, one of our clients upgraded his JPI 700 to a Garmin G3X. Our tech specialist Kurt changed the account configuration so the new data will use the correct parser. In his note to the client, Kurt said “you’ll now have a dizzying array of data available to you.” I remembered my own upgrade from an Insight GEM 602 to a JPI 830. The old GEM didn’t display numbers – just a series of bars for each 25º – and they were almost always higher than I wanted to see. I always wondered if that extra bar meant that my number 3 CHT was 401° or 424°.
One of my favorite things to do on a rainy day at Oshkosh is to stroll the avionics booths and compare how the various monitor manufacturers display their data. Bars, needles, numbers – lots of options to choose from. And if a rainy day at home finds you curled up with a favorite old airplane movie like Spirit of St. Louis or Air Force or 12 O’clock High or The High and the Mighty, it’s remarkable how little engine data they had to process. So it’s good to have real time access to a dizzying amount of data, but it’s up to us as pilots to absorb what we need and filter out the rest.
Let’s start this month with data from a Cirrus SR 22 powered by a Continental IO—550 and data from an Avidyne using a 6-second sample rate. EGTs are on top, with CHTs and FF below. This is the full 21-minute flight.
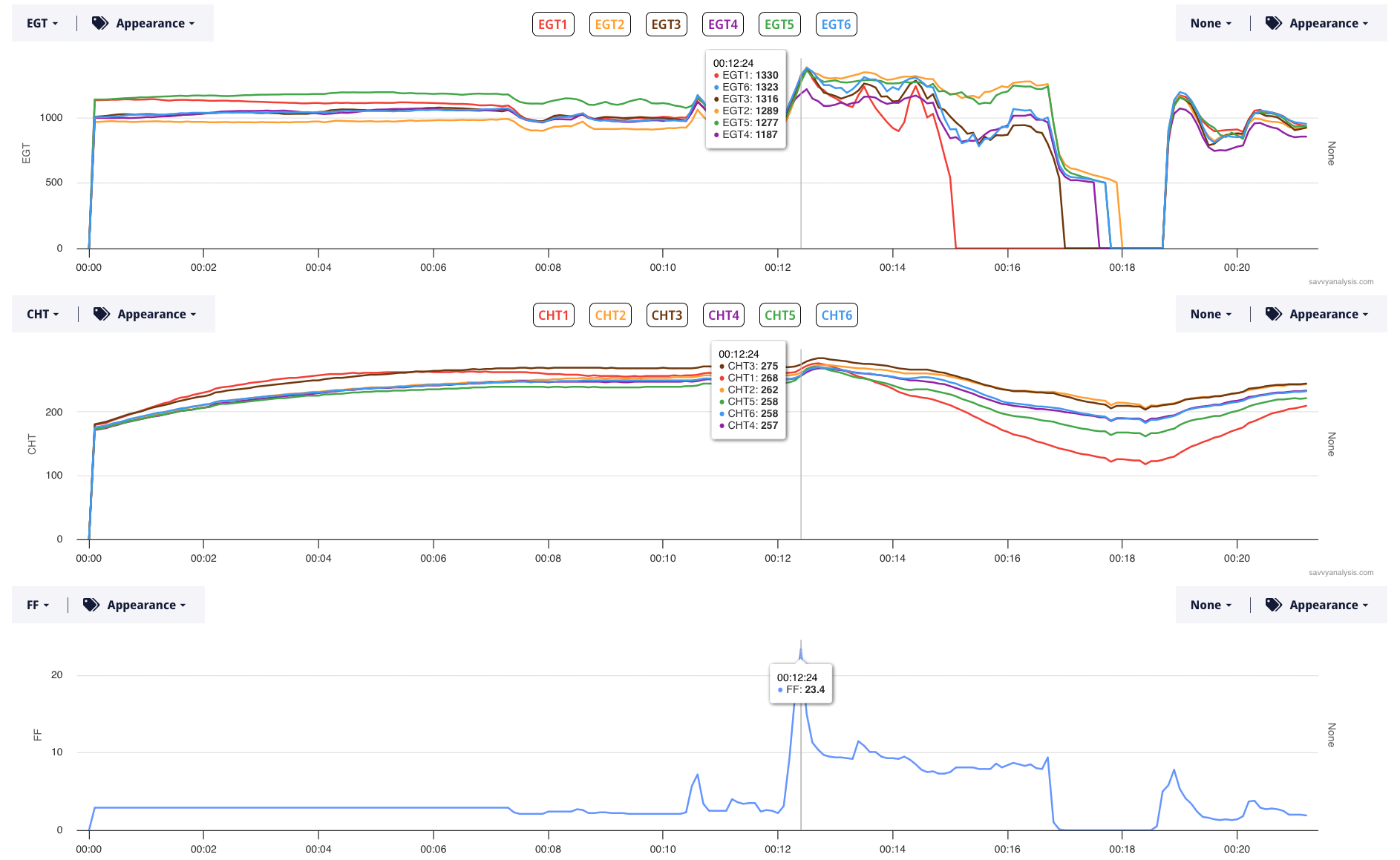
The pilot reported that the engine lost almost all power just after takeoff climbing through 900 AGL. The pilot was able to return to the airport property and landed in the grass. After the shock subsided, the pilot was able to restart the engine and taxi back to his hangar. We can see that in the status starting at the 19 minute mark. Let’s zoom in to the takeoff and landing.
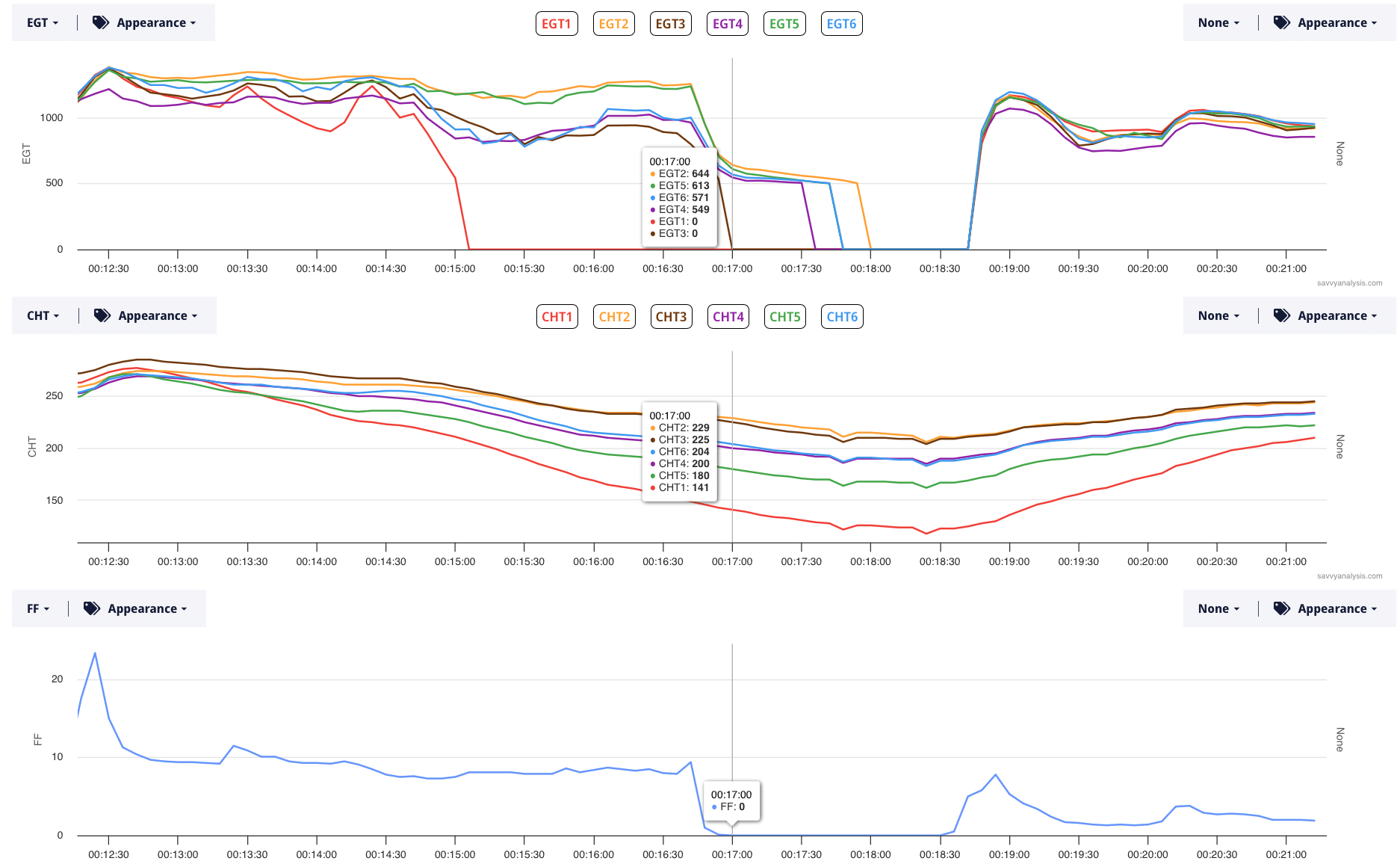
At first glance, we noted the takeoff roll is at 12 mins. EGT 4 never quite joins the others there, then EGT 1 is first to show signs of trouble. Drop, rise, drop, rise then the big drop. We wondered if cyl 1 had swallowed a valve. But that didn’t explain why FF was initially ok, then dropped to the 10 gph range. We also considered a bent fuel hose, a clogged gascolator, and bad fuel. In our back and forth, the client mentioned that the boost pump went on during the runup and never went off, and that the fuel pump had just been repaired. That called into question whether there was a post-repair fuel system setup (once known as a SID-97). In the course of our discussions, the client obtained and installed an overhauled fuel pump and there were no further problems.
Our best explanation for why cylinder 1 was the first to quit is that the initial turn after takeoff was a left turn, so the 1-3-5 side of the engine was “uphill” from the fuel pump.
Next is a Beech A 36 powered by a Continental IO – 550 (TN) and data from a JPI 900 with a 1 second sample rate. EGTs and TIT (this is a turbo-normalized 550) on top, with CHTs and FF below.
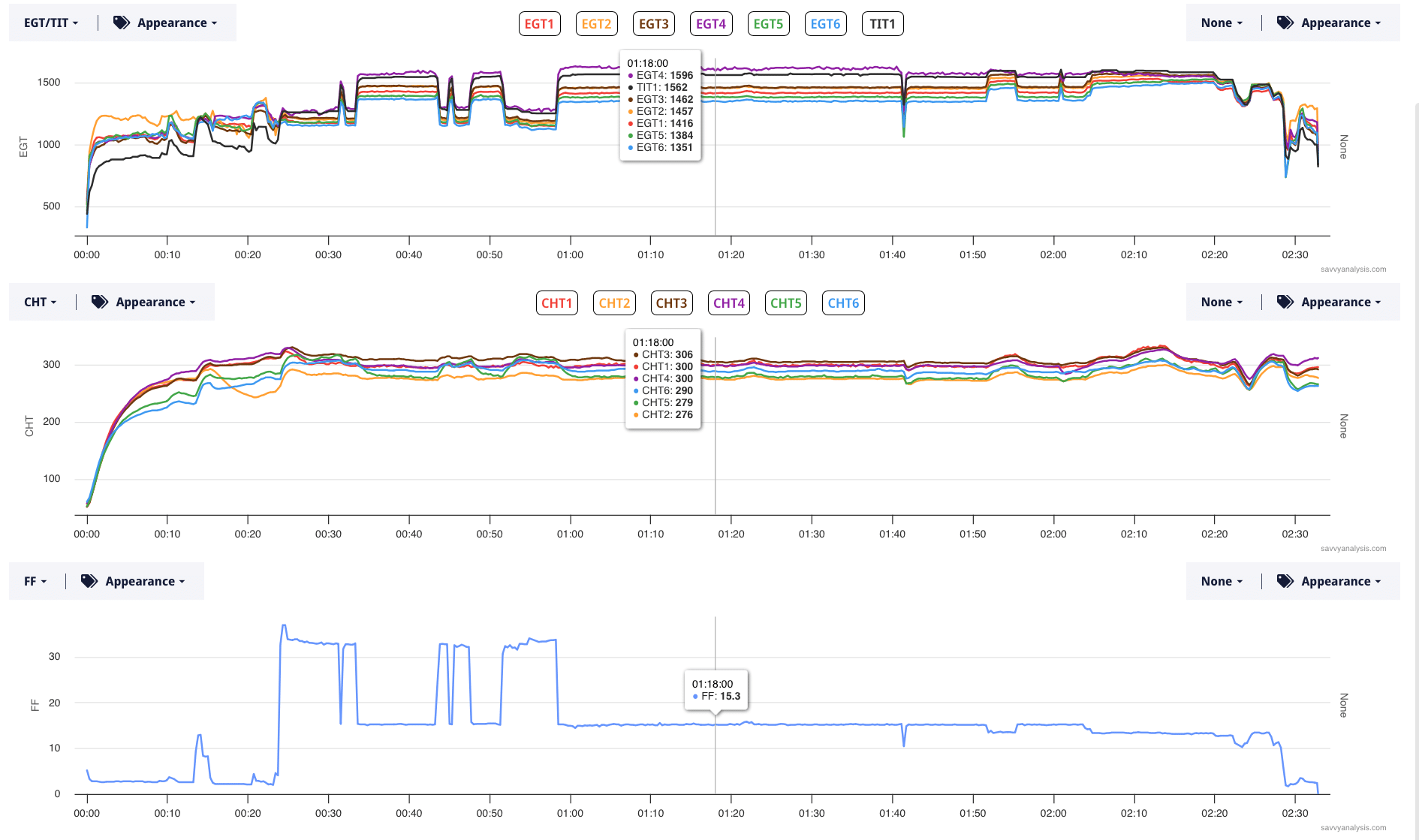
EGTs are stable, except EGT 4 is high in flight. It was ok just after engine start and through the mag check. It rises just after that. EGT 4 rises about 120º, which is the top of the range we’d expect to see if one of the plugs stopped firing. We recommended an in-flight LOP mag check. Here’s the data for that.
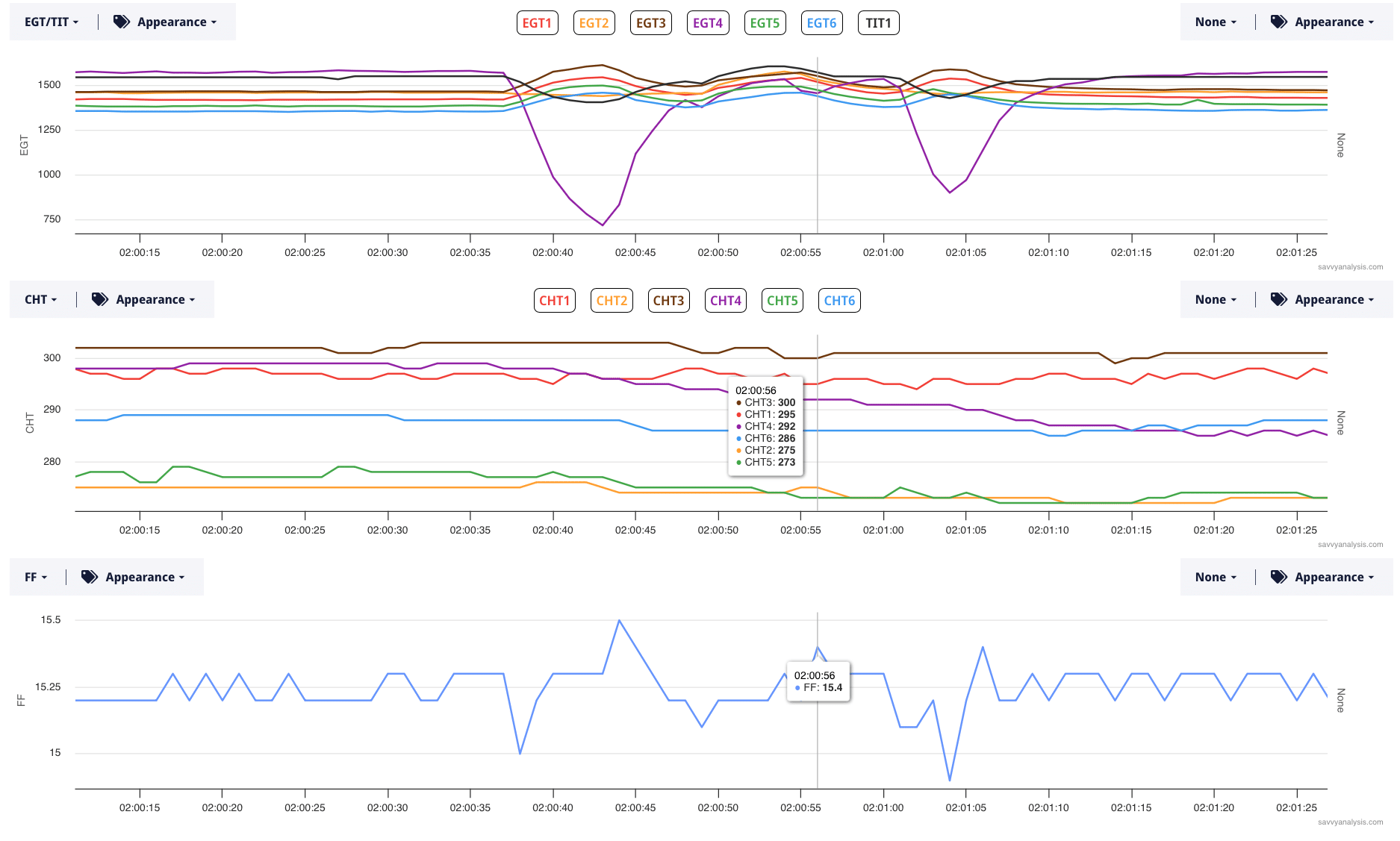
Data clearly identified the top plug of cyl 4.
And when that plug was inspected, this is what they found.
Now the question is what happened to that iridium electrode? Did it burn away or did it separate and work its way through the engine – maybe damaging a turbine blade along the way?
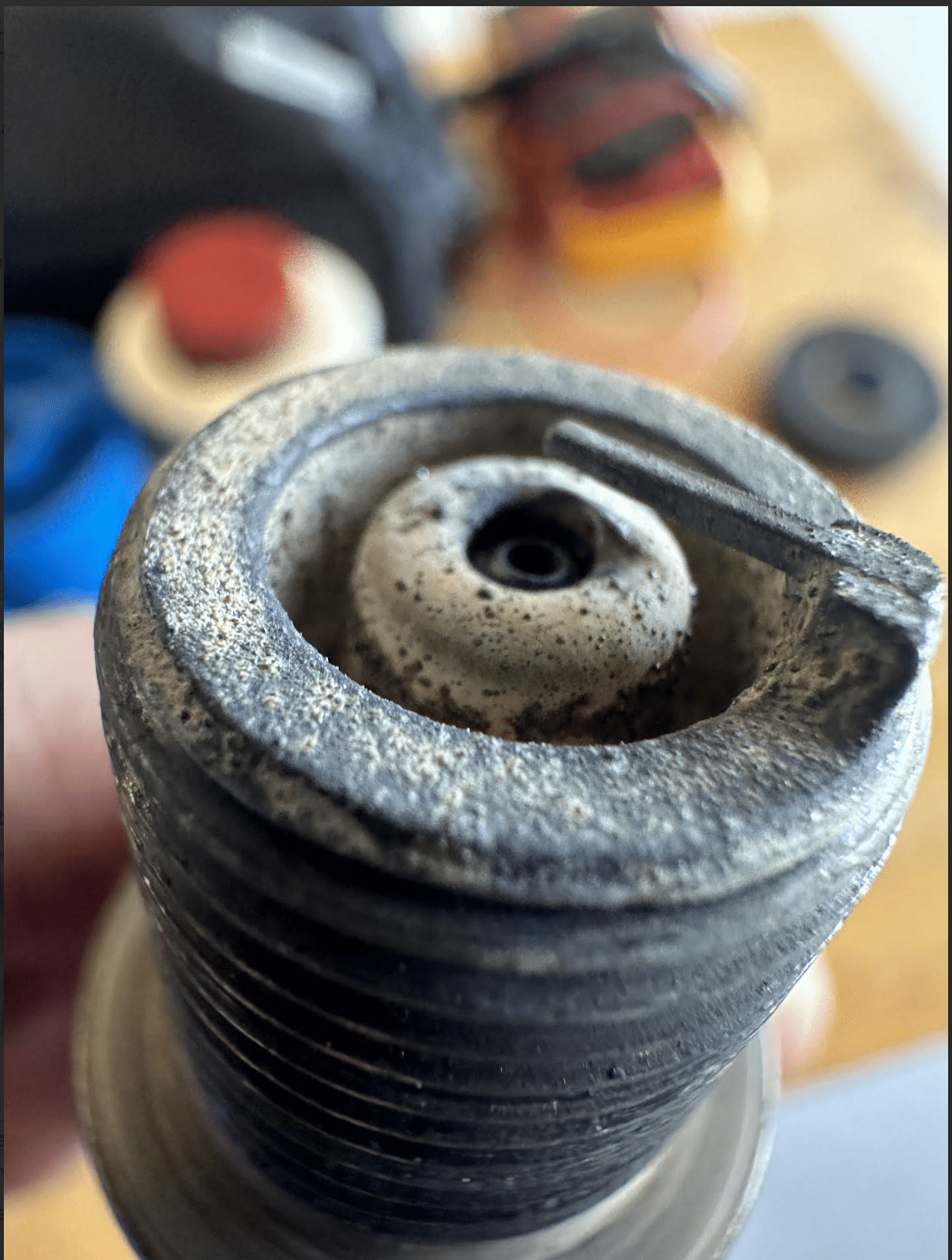
Next is a Piper Chieftain powered by Lycoming LTIO-540 engines, with data from a JPI 760 twin with a 2-second sample rate. Here’s a typical short flight with EGTs and CHTs for both engines.
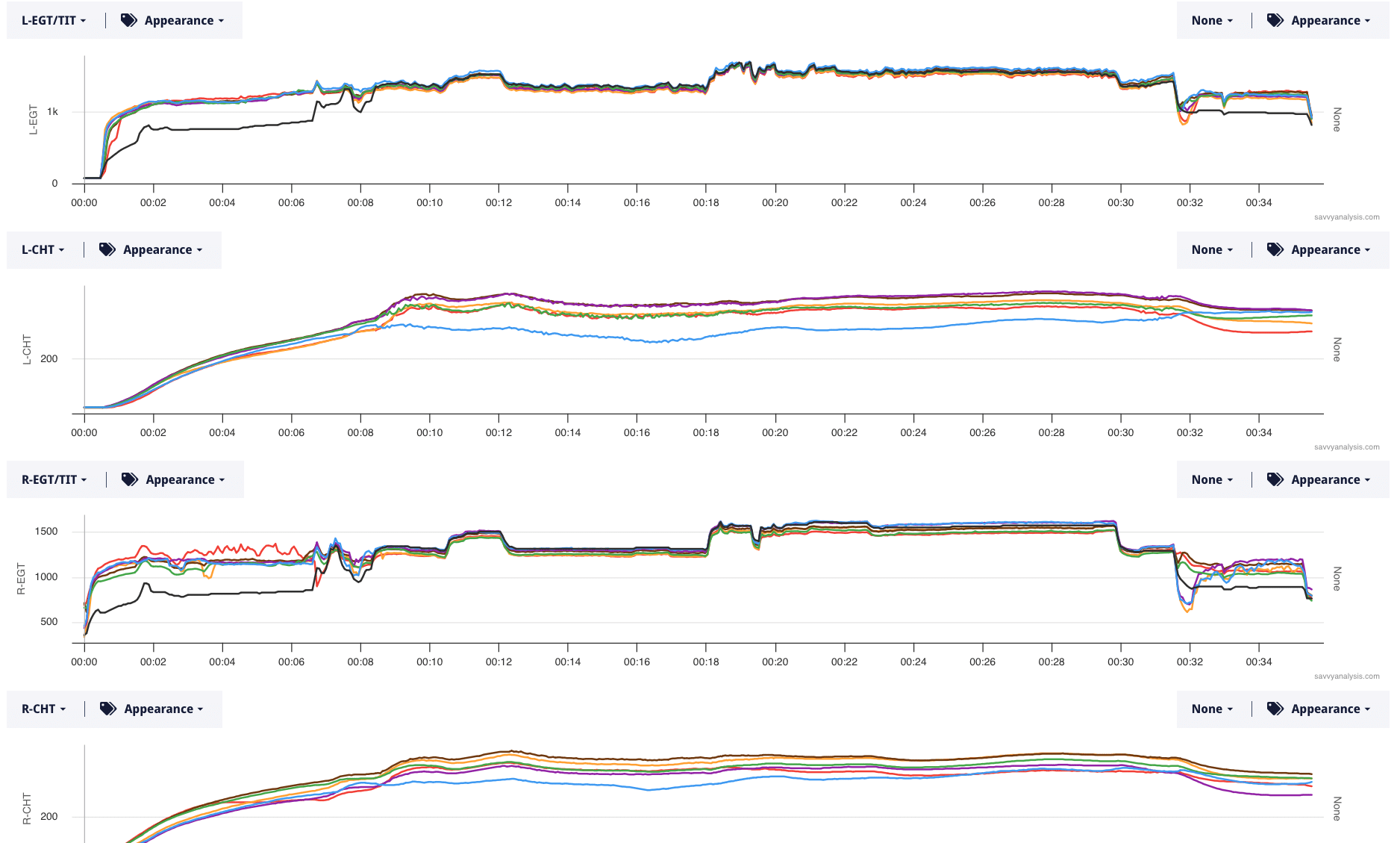
Our client reported surging from the left engine, along with trouble achieving LOP in cruise without sending the TIT up to the redline. Here’s the L engine during cruise with FF in bold.

Our client had already done some troubleshooting. They noticed that FF was a little low in the climb, so they bench-tested the fuel control unit and bumped up mid-range FF a bit. That’s when the engine started surging. They thought it was an upper deck issue and replaced all the hoses, but the surging continued. They reported that mag checks were all good.
However, the data shows that the EGTs are jumpy even as fuel flow is relatively stable. That suggests weak spark, and because it’s happening on all cylinders, it suggests a mag problem. We asked for a LOP mag check. They skipped that step and pulled the mag and found that timing had drifted 4° because of worn points. They also found a problem with the coil. It would test OK when it was cold, but as soon as the coil got warm, the resistance jumped off the charts.
We’ll finish this month with a Cessna 414 powered by Continental TSIO-520 engines and data from a JPI 960 twin with a 1q second sample rate. This is a typical 3 hour flight with EGTs and CHTs for each engine.
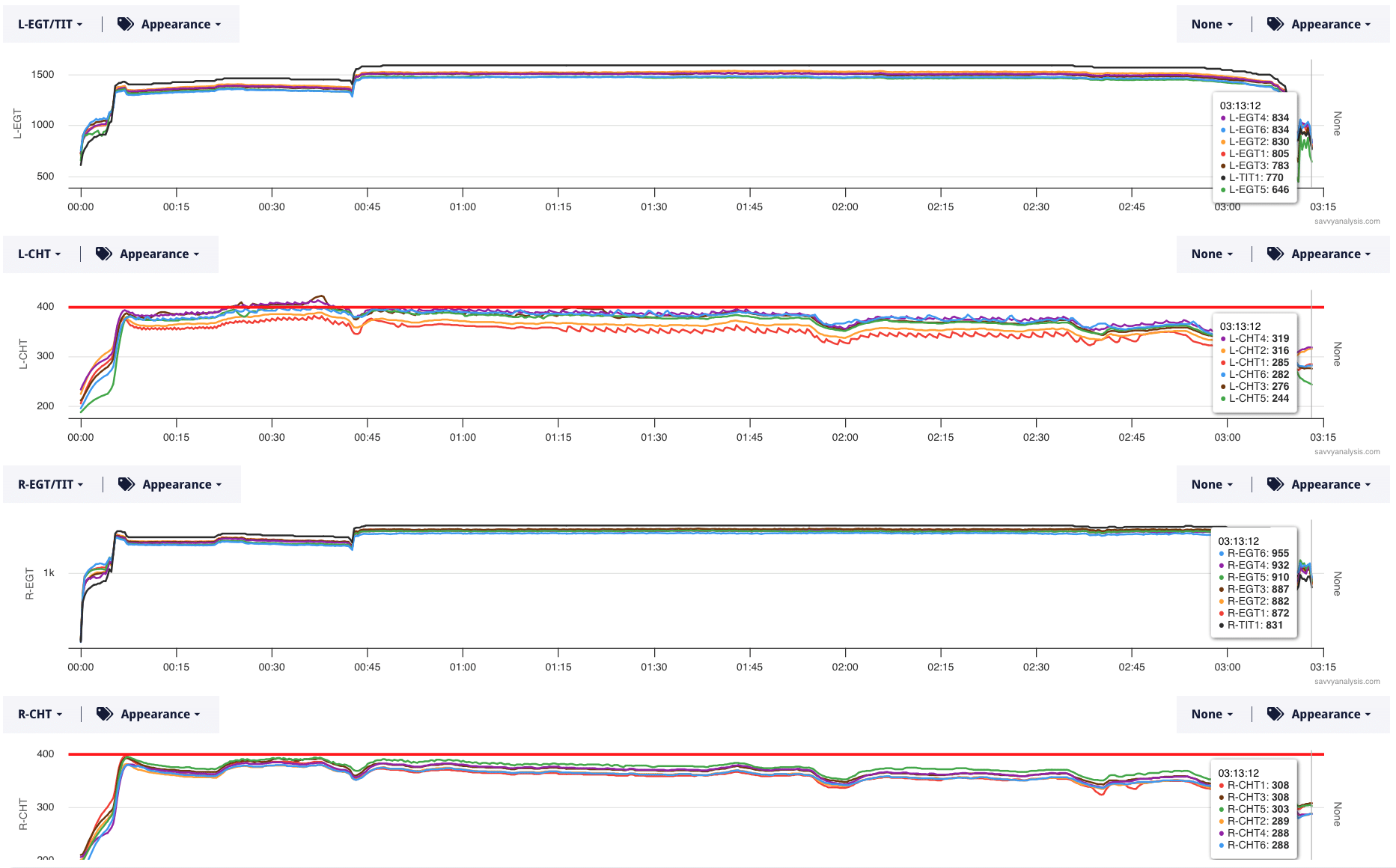
EGTs are remarkably stable on both engines. R engine CHTs are in a good range with a low spread. L engine CHTs are a little higher – tickling the CHT alert line – and are showing a lot of wavy patterns.
Quick sidebar: veteran puzzler readers and most Savvy clients don’t need this reminder, but because we’re always bringing new clients on board let’s do a quick refresher. FEVA has been around long enough that pilots get nervous when they see a wavy or oscillating pattern in their data. We often get data like this, asking whether it’s an indication of a burned valve. When we see an oscillation in EGT, we want to investigate the condition of the exhaust valve. When we see an oscillation in CHT, it’s most likely caused by a cooling baffle that’s loose enough to move against the incoming wind. That’s what we see here.
Here are L engine CHTs with 1-3-5 on top and 2-4-6 below.
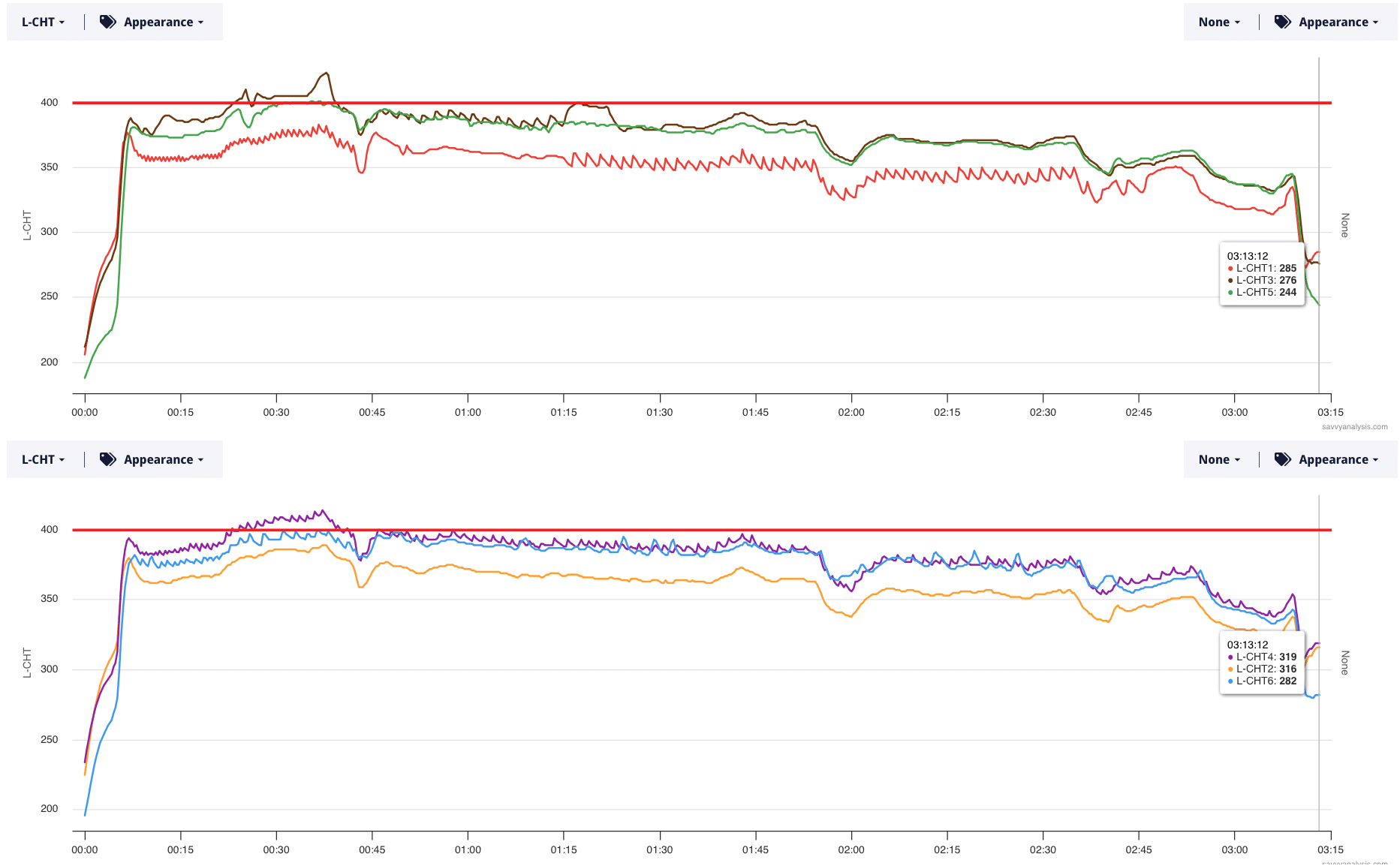
There are sawtooth patterns in the red CHT 1 trace, the brown CHT 3 trace, and the purple CHT 4 trace. At the 1 hr 15 min mark, the pattern moves from cht 3 to chat 1. We think all of this is due to cooling baffles that are loose enough to move with the incoming air. The red trace “teeth” are close together in climb when the airspeed is lower, then they space out after the plane noses over for cruise.
Check on both sides of cylinder 4. Because of the cylinder 1/cylinder 3 connection, it makes sense to check the inter-cylinder baffle between 1 and 3.