Each time you change mixture, RPM or MP, it affects combustion timing. Understanding how is your best defense against harming your engine by doing something dumb.
My last few columns focused on the physics of the combustion event in Otto-cycle engines. I’m sure this was fascinating to the two or three of you who are interested in combustion theory, but of what possible relevance is it to a pilot whose main concerns are measured in knots and dollars rather than milliseconds and PSI?
Actually, it’s extremely relevant. That’s because you modify the speed, intensity and timing of the combustion process every time you move the throttle, mixture and prop controls. If you don’t have a clear mental picture of how changing MP, RPM and mixture affects the combustion event, you’ll never truly understand optimum power settings or leaning, and you’ll simply have to operate your engine by rote – which is exactly what most pilots do.
Little was known about this stuff back when Beech wrote the POH for your airplane. Much of what we now know comes from recent research done by my old friend George Braly at GAMI’s Carl Goulet Memorial Engine Test Facility in Ada, Oklahoma, arguably the most sophisticated digitally instrumented piston aircraft engine test cell in the world. Not satisfied with simply looking at engine temperatures and pressures and fuel flows, George has placed solid state pressure transducers into the combustion chambers, enabling him to analyze what’s actually going on inside the cylinders on a microsecond-by-microsecond basis.
With that preamble, let’s take a look at some of the data from the GAMI engine test facility, and see exactly what happens when we fiddle with those engine controls..
Effect of Leaning
Figure 1 shows what happens to a big-bore TCM engine at sea level, full throttle and redline RPM when we progressively pull back the mixture control from full-rich to ultra-lean without changing anything else.
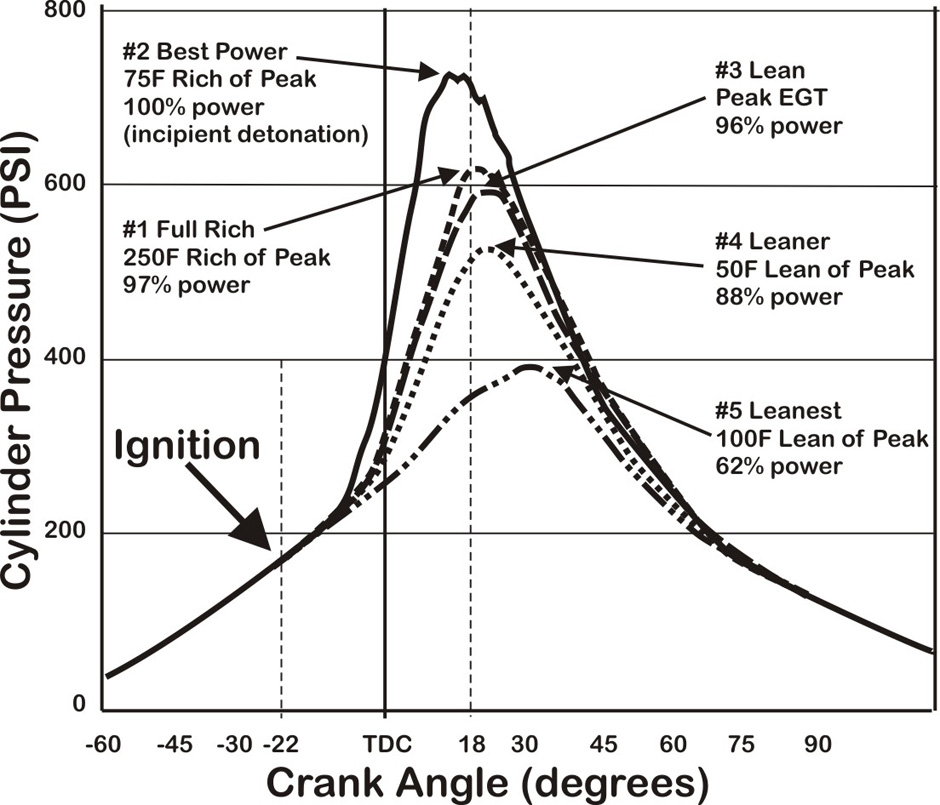
Figure 1-Effect of moving mixture control from full-rich to ultra-lean without changing MP or RPM.
As the mixture is leaned from full-rich to best-power mixture (approximately 75degF rich of peak EGT), combustion becomes more and more rapid, causing the peak pressure to occur earlier and earlier – closer and closer to TDC. The result is increased peak pressure, degraded pushrod-to-crankshaft geometry, and generally more stress on the engine (but not enough additional power to talk about). If you look closely at trace #2 in Figure 1, you’ll see the subtle beginnings of a detonation signature. (This is mild detonation – not enough to damage anything, but a warning that we’re approaching the danger zone.)
But look what happens if you continue to lean from best-power mixture to peak EGT. Combustion starts to slow down, the peak pressure occurs further after TDC, the excessive stresses are eliminated, and the power output and combustion timing are nearly identical to what we saw at full-rich mixture.
So why don’t we take off leaned to peak EGT instead of at full-rich? Well, we certainly could do that without fear of any short-term engine damage from detonation. In the long run, however, the high exhaust gas temperatures would probably shorten the life of our exhaust valves and valve guides. But one or two takeoffs leaned to peak EGT probably wouldn’t hurt.
Now look what happens if we continue to lean beyond peak EGT into the lean-of-peak (LOP) realm: The combustion rate continues to slow, the pressure peak occurs even later, the peak pressure and power output decline significantly, detonation margin increases … and of course, EGT decreases. A takeoff made with the mixture set at 50degF lean of peak EGT wouldn’t abuse the engine at all. The only problem is that you’d use more runway because the engine would be putting out only perhaps 90% of the power that it does at full-rich.
What this means is that an engine at full takeoff power will not be harmed a bit by leaning from full-rich to 50degF lean of peak provided you pull back the mixture control briskly and don’t dawdle too long between best-power mixture (where engine stress and detonation risk are highest) and peak EGT (where exhaust temperature is highest). I’m not suggesting that you actually do this, only that you understand what would happen if you did.
Effect of Reducing MP
Figure 2 shows the effect of throttling back from 30 inches of MP to 25 inches after take-off. As you might expect, this reduces peak combustion pressure – but it also results in a couple of not–so-obvious changes. The timing of the pressure peak is dramatically retarded from a stressful and detonation-prone 14deg after TDC to low-stress but inefficient 22deg after TDC. (To bring the peak back into the optimum 15deg to 20deg ATDC range, we’d probably want to pull the prop control back to 2500 RPM – see below.)
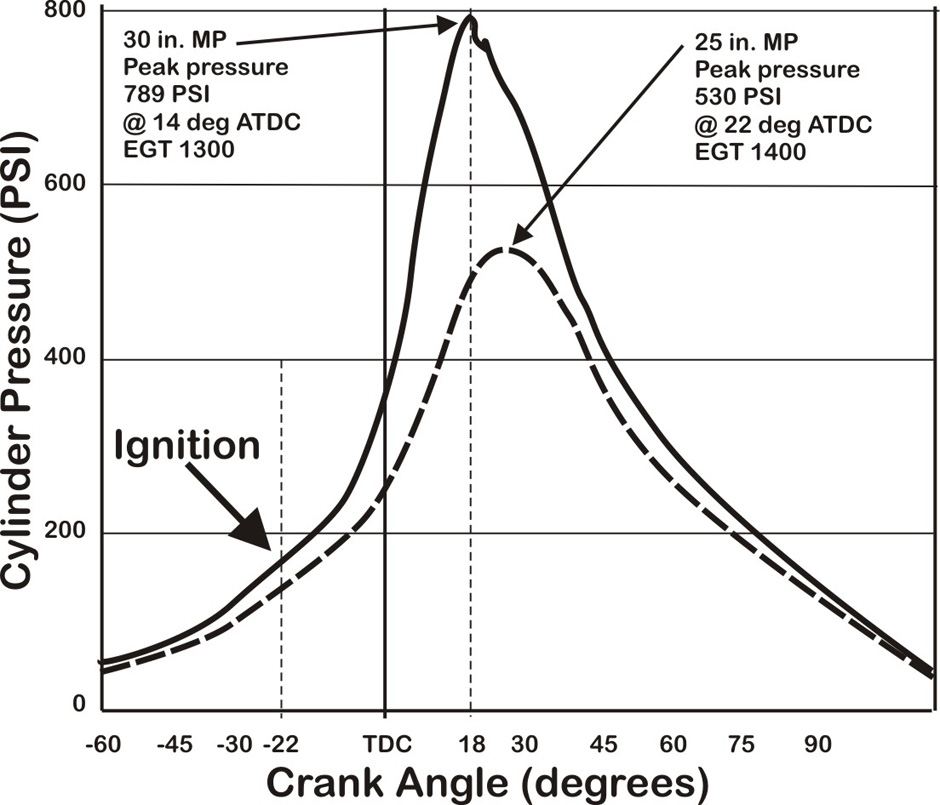
Figure 2-Throttling back from 30″ to 25″ reduces peak combustion pressure, retards the peak pressure point, and improves detonation margins dramatically. Note light detonation at the higher MP.
Also, despite the fact that power output is decreased, EGT actually increases from 1300degF to 1400degF. There are two reasons for this. First, the act of throttling back also reduces fuel flow, and takes the fuel control unit out of its full-throttle enrichment mode. Second, retarding of the combustion event means that less heat energy is converted to mechanical energy by the time the exhaust valve opens, so more is wasted through the exhaust.
Effect of Reducing RPM
Finally, Figure 3 shows the effect of reducing propeller RPM from 2700 to 2500 after takeoff, with no throttle reduction or mixture change. Note that the result of such an RPM reduction is a higher pressure peak that occurs earlier – closer to TDC. Thus, although pulling back the prop reduces engine power output, it increases the stress on the engine and reduces detonation margin (although in this case, no detonation signature is apparent in the pressure trace).
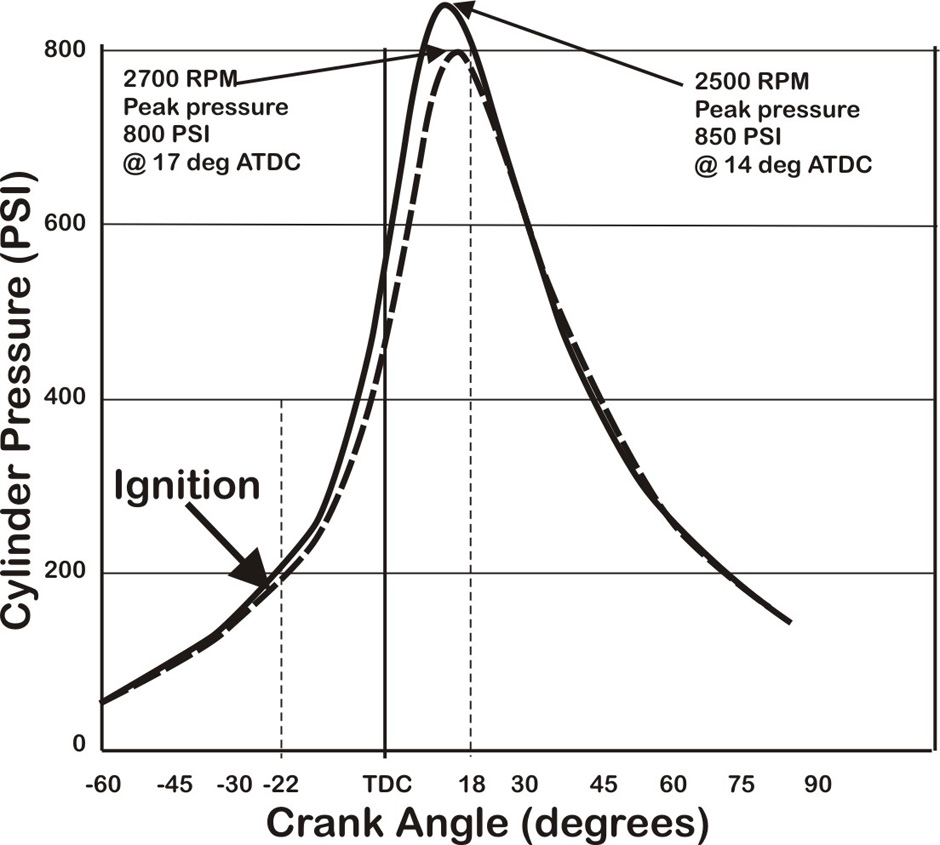
Figure 3-Reducing RPM from 2700 to 2500 advances the peak pressure point and reduces detonation margin. Although power output is reduced, engine stress increases.
This explains the old rule about always reducing MP before reducing RPM. Note that reducing MP causes the pressure peak to decrease and occur later, while reducing RPM causes the pressure peak to increase and occur earlier. Thus, doing both together tends to cancel out the timing change, and to keep peak pressure and its timing relatively constant.
If you haven’t nodded off by now, you might well ask why reducing RPM causes the pressure peak to occur earlier. Shouldn’t the fuel/air mixture burn at the same rate, regardless of the position of the prop control? In the words of the old joke, “how does it know?”
Indeed, the elapsed time from ignition to peak pressure does not change significantly as you pull back on the prop control. What does change is the number of degrees of crankshaft rotation that occurs during this time interval. Since the crankshaft is turning slower, it doesn’t rotate as many degrees by the time the pressure peak occurs, so the peak occurs at fewer degrees after TDC.
Putting It All Together
Later this decade, many of us will probably be flying behind engines equipped with fancy FADECs that automatically vary the ignition timing to keep that all-important pressure peak in the “sweet spot” of 15deg to 20deg after TDC. But for now, the responsibility for doing so remains with the pilot. So let’s quickly review what we’ve learned
Leaning from full rich to best-power mixture (approximately 75degF rich of peak EGT) causes combustion to occur more rapidly and the pressure peak to advance. Continuing to lean toward peak EGT and into the LOP realm causes combustion to slow down again, retarding the pressure peak. Leaning from full rich to peak EGT causes very little change in engine power output, but continuing to lean beyond peak EGT results in a power reduction that is more or less linear with fuel flow.
Reducing MP and RPM also affects the intensity and timing of the pressure peak, but in opposite directions. Reducing MP (throttling back) results in a lower pressure peak that occurs later (in terms of crankshaft rotation), while reducing RPM results in a higher pressure peak that occurs earlier. Reducing both MP and RPM (preferably in that order) results in opposing changes to the intensity and timing of the pressure peak that tend to cancel one another out.
Detonation occurs only when the pressure peak is high and early. Therefore, the greatest risk of detonation occurs at or near best-power mixture (50degF to 100degF rich of peak EGT). Interestingly, this is exactly where most POHs recommend that we operate, but it’s bad advice. (They didn’t know any better back when they wrote it.) Detonation margin can be further impaired by high MP and low RPM.
The timing and intensity of peak combustion pressure are among the most important parameters in piston engine operation. Unfortunately, you don’t have a panel instrument to show you that information. In the absence of such instrumentation, a solid understanding of how these parameters are affected by changes to mixture, RPM and MP is your best defense against damaging your engine by doing something dumb.