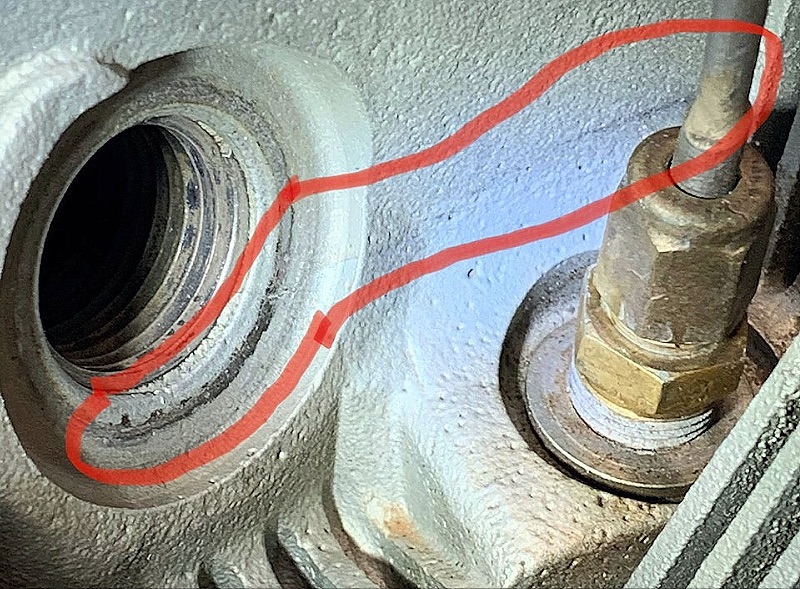
Ken was having issues with the fuel boost pump on his Cessna 180, so he put his airplane in the shop to have his mechanic investigate it. A few days later, the shop called with some unpleasant news unrelated to the fuel pump.
The A&P advised Ken that two of the six cylinders on his Continental IO-470 appeared to have cracked cylinder heads, with cracks running between the fuel nozzle and the top spark plug. The mechanic said that such head cracks were not repairable, and so both cylinders would need to be replaced. Estimated cost of parts and labor was $6,000.
Yikes!
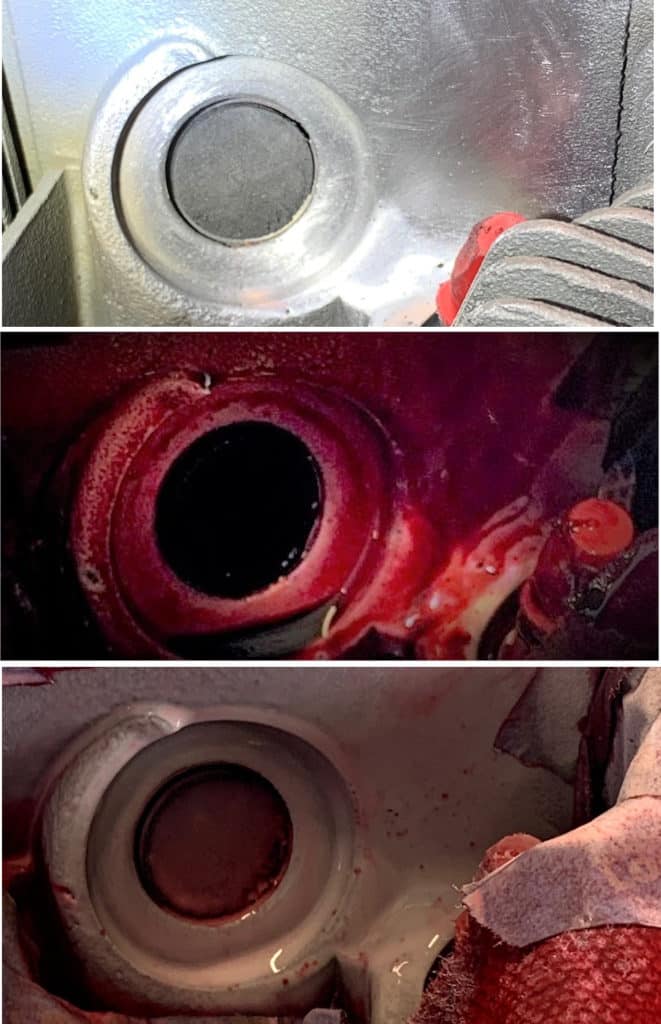
Ken was a SavvyQA maintenance consulting subscriber, so he contacted Savvy for advice. Savvy’s account manager Tony Barrell explained that the location described was indeed a common location for cracks to develop in Continental cylinder heads. On the other hand, Tony told Ken that in Savvy’s experience more than half of the reported cracks in this area turn out not to be cracks at all, but rather superficial cosmetic flaws in the head casting. In fact, unless the crack is clearly blue-stained and leaking fuel, it rarely turns out to be an actual crack. Therefore, Tony suggested that Ken ask the shop to sand the suspected crack area smooth and then perform a dye penetrant inspection (DPI) of the area.
DPI is a quick, low-cost inspection method used to locate surface defects on non-ferrous metals. The DPI kit contains three aerosol cans—cleaner, penetrant, and developer—and the inspection procedure is simple:
- Spray the surface with aerosol cleaner, and then wipe dry.
- Spray the surface with aerosol penetrant (typically deep red in color) and allow it to soak into any surface flaws for 10 to 30 minutes.
- Wipe the surface with a clean cloth moistened with aerosol cleaner to remove all residual red-dyed penetrant from the surface.
- Spray the surface with aerosol developer powder and allow to dry to an even white powdery layer. Inspect the developer-covered surface.
Any cracks will show up clearly as a red line on the white surface as red-dyed penetrant embedded in the cracks is wicked up out of the crack and absorbed by the white powdery developer.
Ken went to the shop and watched while his mechanic performed the DPI procedure. The test showed clearly that there was no crack in either cylinder head. Ken’s mechanic was satisfied, the two cylinders remained in service, and Ken found a better use for his $6,000.
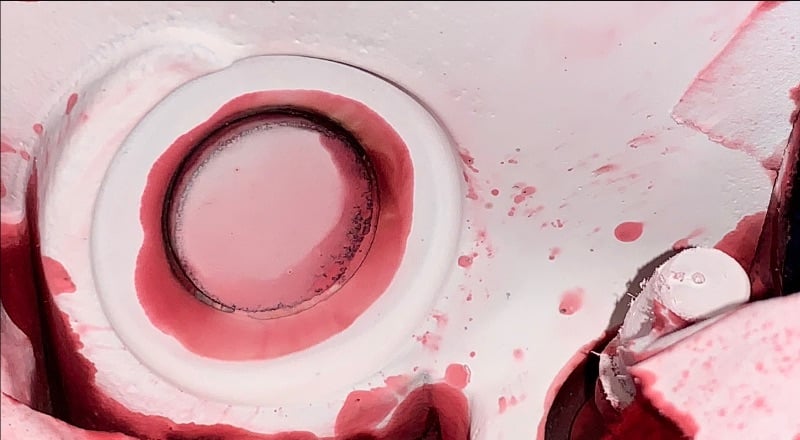
Ken’s decision to get a second opinion from Savvy was a smart move that saved him more than $6,000 in unnecessary maintenance expense, plus a week or two of downtime and the risky business of cylinder replacement in the field. Ken’s SavvyQA subscription entitles him to unlimited consultations throughout the year. This one second opinion saved him enough to pay for the service for the next 16 years.
This isn’t unusual. We almost always save our clients more in reduced maintenance costs than the annual subscription cost. Often a LOT more.
Wouldn’t you benefit by having Savvy watching your six?
You bought a plane to fly it, not stress over maintenance.
At Savvy Aviation, we believe you shouldn’t have to navigate the complexities of aircraft maintenance alone. And you definitely shouldn’t be surprised when your shop’s invoice arrives.
Savvy Aviation isn’t a maintenance shop – we empower you with the knowledge and expert consultation you need to be in control of your own maintenance events – so your shop takes directives (not gives them). Whatever your maintenance needs, Savvy has a perfect plan for you: