Exhaust valves are the most heat-stressed components in your piston aircraft engine, and the most likely to fail prior to TBO. Here’s what you need to know about them.
I experienced my first in-flight exhaust valve failure about twenty years ago. The engine started running very rough (as you might expect of a six-cylinder engine that was only running on five cylinders). After I landed, I noticed that the manifold pressure at idle was several inches higher than normal, confirming that something was definitely wrong with the engine.
I put the airplane in the hangar, removed the top cowling and the top spark plugs, and performed a differential compression test. Five of the cylinders measured just fine, but one measured 0/80 with a hurricane of air blowing out the exhaust pipe. It was pretty obvious that this jug was going to have to come off.
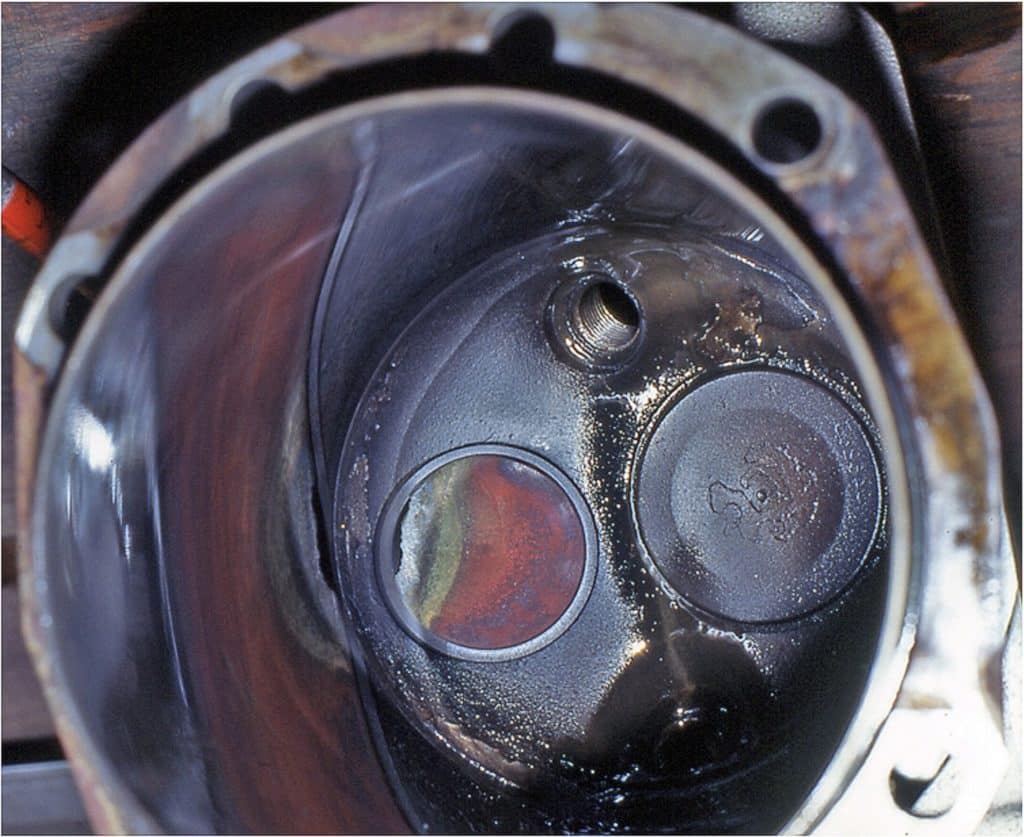
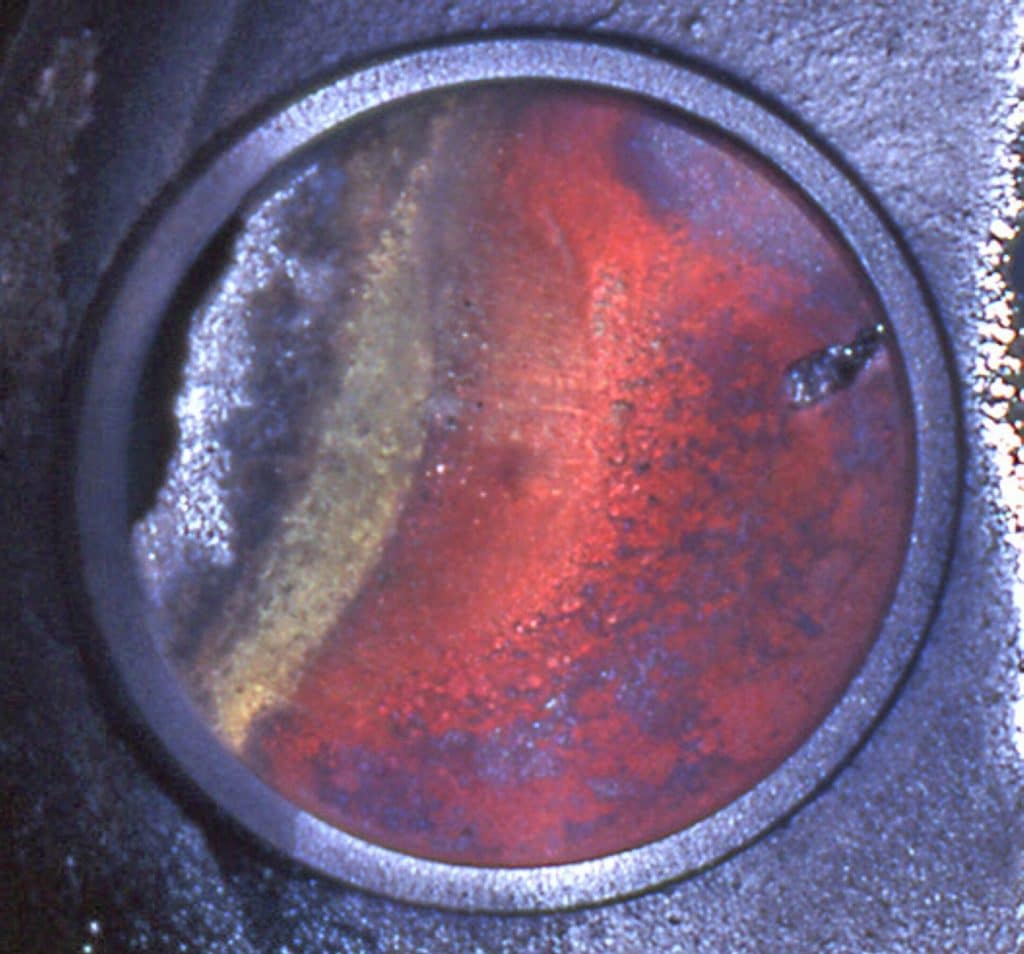
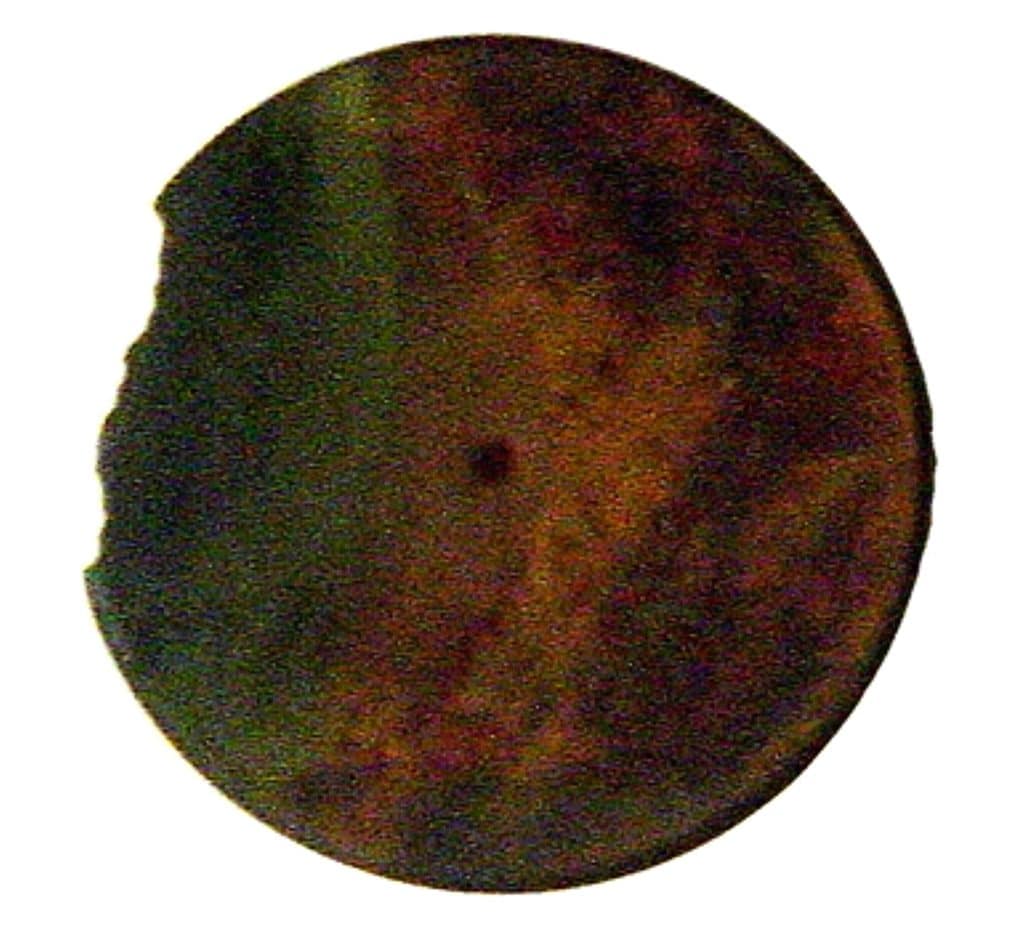
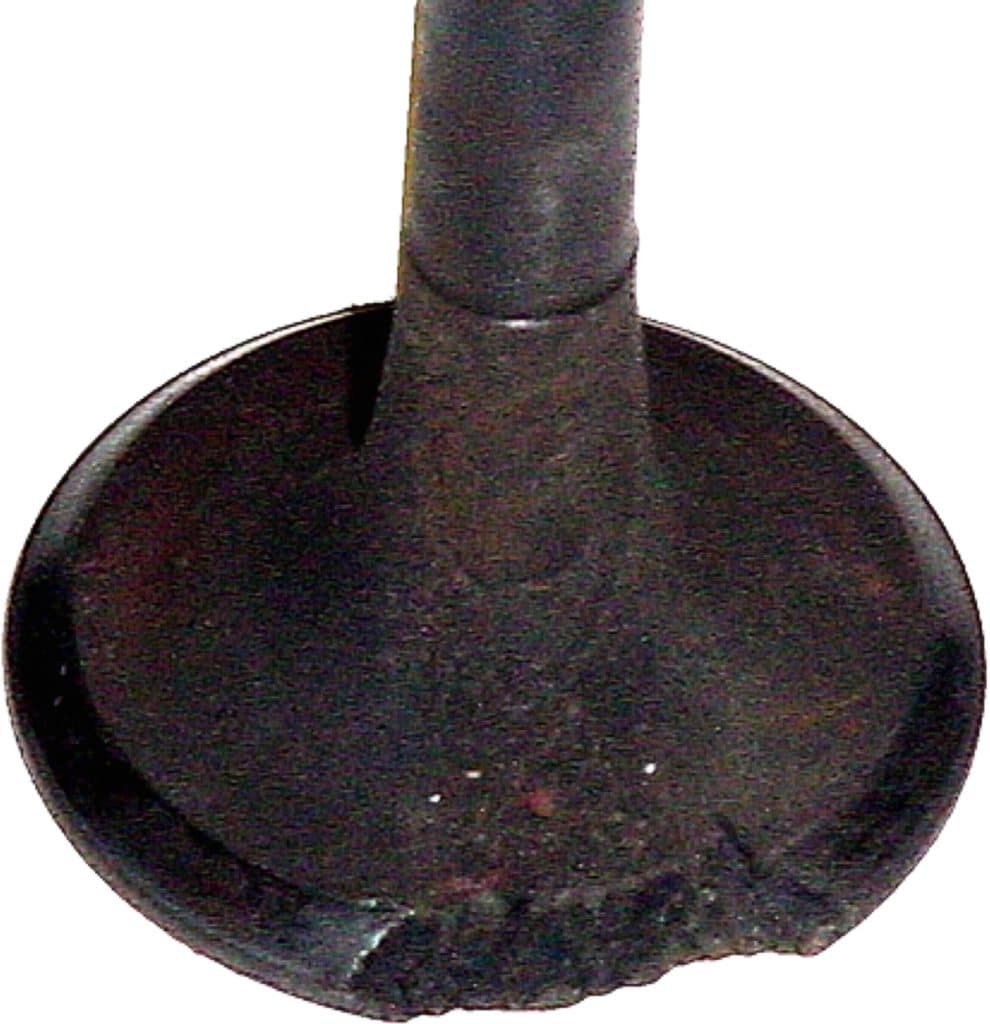
Once I wrestled the cylinder off the engine and looked at the exhaust valve, it was pretty obvious that something was missing (see Fig. 1). A fragment of the exhaust valve face had broken off and departed the premises for parts unknown. Luckily, it opted to depart through the wastegate and to spare the turbocharger turbine wheel from destruction.
I sent the jug out for repair. It came back with a new exhaust valve and guide, and with some dressing to the valve seat. I installed the cylinder back on the engine, where it is happily operating to this day, nearly 20 years and 3,000 hours later.
Hot, Hot, Hot!
Exhaust valves are the most heat-stressed components in your engine. They live their lives exposed to hideously high temperatures, while oscillating back and forth through a valve guide largely without benefit of lubrication (since they’re too hot for engine oil to tolerate without coking). Frankly, it’s astonishing that they last as long as they do.
During the peak pressure and temperature portion of each combustion event, gas temperatures in the combustion chamber approach 4,000°F, far hotter than the exhaust valve could withstand. Fortunately, the valve is closed during this time, so the heat energy absorbed by the valve face is quickly transferred through the valve seat to the cylinder head, where it is absorbed by the head’s large thermal mass and dissipated its cooling fins (see Fig. 2). This “heat sink” arrangement is absolutely essential to the survival of the valve. Without it, the valve face would overheat and self-destruct quite rapidly.
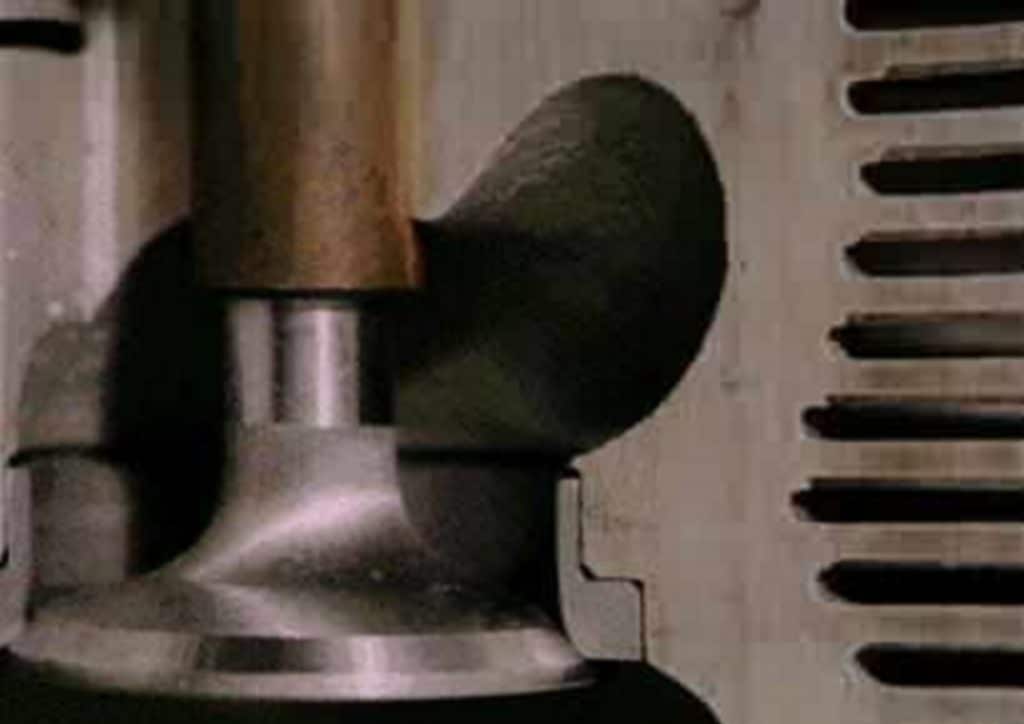
As the combustion event subsides, the exhaust valve opens. By this time, the gas temperature in the combustion chamber has transferred much of its heat energy to the piston (converting it to mechanical energy), so the exhaust gas that flows past the valve and out the exhaust port starts out at less than 2,000°F and cools very rapidly as the combustion chamber pressure drops. This is a good thing, because when the exhaust valve is open it loses its primary heat sink (the valve seat), and the only way the valve can dissipate heat is through the valve stem to the valve guide. This secondary heat path is a bit more effective in Lycoming engines (with their sodium-filled valve stems) than it is in TCM engines (with their solid valve stems).
At the end of the exhaust stroke, the exhaust valve closes, once more making firm contact with the valve seat and establishing the primary heat sink arrangement in preparation for the thermal assault of the next combustion event.
How Exhaust Valves Fail
Exhaust valve problems often cause aircraft owners to suffer from pangs of guilt. “Why did the valve burn? What did I do wrong?” Mechanics often contribute to such guilty feelings by telling owners that their exhaust valve burned because the engine was leaned too aggressively. This is almost always wrong.
The overwhelming majority of exhaust valve problems are caused by excessive valve guide wear. Some guide wear is normal and inevitable, given that the guide is softer than the chrome-plated valve stem that passes through it, and that the two are in constant relative motion without benefit of lubrication. But if the guide wears excessively, it cannot hold the valve face perfectly centered in the valve seat. That’s when problems begin.
If the valve face and seat are not perfectly concentric, then one spot on the valve face will not seal properly against the seat when the valve is closed during the combustion event. This causes two bad things to happen. First, the heat path from the valve face through the seat and head is disrupted, interfering with the ability of that spot on the valve face to shed heat. Second, tiny amounts of extremely hot combustion gas leak past the spot that isn’t sealing properly. The result is a “hot spot” on the valve face.
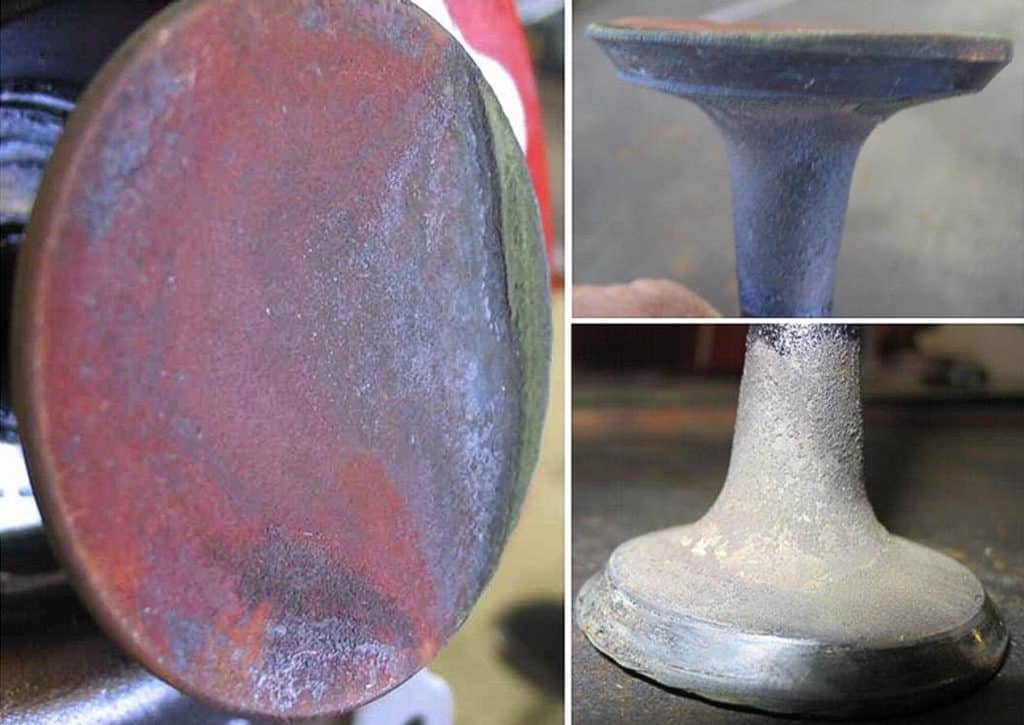
Once the exhaust valve develops a hot spot, things can deteriorate rather quickly. Metal starts eroding from the hot spot, causing its seal against the valve seat to get worse, interfering with the heat path even more, and allowing increasing amounts of leakage during the hottest part of the combustion event. When the hot spot gets hot enough, the valve face will start to warp, further degrading the seal and increasing the leakage. Deterioration progresses at an ever-increasing pace until the hot spot gets so hot that the valve ultimately sheds a chunk of metal, at which point compression goes to zero and the cylinder shuts down. (Colloquially, we say the engine “swallowed a valve.”)
Bottom line: Once the hot spot develops, the valve is doomed—it’s not a question of whether it will fail, only when.
Why They Fail Prematurely
Any exhaust valve will fail if it remains in service long enough. In a perfect world, the valve, guide and seat will survive to TBO or beyond. In the real world, that isn’t always the case.
There are a number of factors that can contribute to premature exhaust valve failure. If the guide is not properly machined (reamed) during cylinder manufacture, overhaul or repair to hold the valve perfectly concentric with the seat, then a hot spot can develop relatively quickly. For example, there is considerable evidence that TCM had some valve concentricity issues on cylinders they manufactured during the late 1990s and early 2000s, resulting in an epidemic of burned exhaust valves at 500 to 700 hours. TCM changed its manufacturing procedures and these problems seem to have gone away.
Another factor involves how the valve seat is ground, and how wide the contact area is between the valve and the seat. If the contact area is too wide, then may not be enough pressure between the valve and seat to cut through carbon deposits that form on the valve seat (particularly when the engine is operated at low power and/or rich mixture). If the contact area is too narrow, then the heat transfer path from the valve to the seat is compromised and the valve runs too hot (particularly at high power settings and lean mixtures). Grinding the seat to obtain the optimal contact area can be more of an art than a science.
If the engine is operated with a rich mixture (particularly during taxi and other ground operations), lead, carbon, and other unburned combustion byproducts can build up on the portion of the exhaust valve stem that projects into the exhaust port when the exhaust valve is open. When the valve closes, this deposit build-up is dragged into the lower portion of the valve guide, and often causes accelerated guide wear (“bellmouthing”), particularly in TCM engines that use relatively soft valve guides. As we’ve seen, accelerated valve guide wear generally leads to valve hot spots (“burned valves”) and ultimately to valve failure (“swallowed valves”).
In most Lycoming and some TCM engines that use relatively hard valve guides, the deposit build-up on the valve stem makes it difficult for the valve to close fully. This can also cause leakage past the valve, resulting in hot-spotting and ultimately valve failure. If the situation gets bad enough, the result in a stuck valve that won’t close. (The same problem can be caused by valve guide corrosion in engines that sit unflown for long stretches of time.) The first symptoms of this condition is usually “morning sickness” where the engine runs very rough when first started but smoothes out as the CHTs come up to operating temperature. If the problem isn’t addressed promptly, it can lead to an in-flight stuck valve that can have quite serious consequences: bent pushrod, damaged cam, even snapping the head right off the valve if the piston strikes the head of the stuck-open valve. Stuck valves are quite common in Lycomings and TCM O-200/O-300 engines; they are quite rare in big-bore TCM engines.
So contrary to popular belief, to the limited extent that pilot leaning procedure contributes to burned, stuck, and swallowed exhaust valves, such issues are far more likely to be caused by excessively rich mixtures (particularly during ground operations) than by lean mixtures. I operate my engines brutally lean during ground ops, and lean-of-peak EGT (LOP) during all phases of flight other than takeoff and initial climb. This assures the cleanest and coolest operation, which is the optimum prescription for long valve life.
During the late 1980s and early 1990s, TCM switched to a new, ultra-hard “nitralloy” exhaust valve guide in an attempt to reduce guide wear. Unfortunately, some of these guides weren’t properly chamfered and developed a sharp edge that chiseled the chrome plating from the valve stems and allowed the valves to wobble, burn, and ultimately fail. That was the reason for my exhaust valve failure nearly 20 years ago. As is true more often than not, my valve failure was not caused by pilot error but by manufacturing error.
Next month, in Part 2 of this article, we’ll examine how we can monitor exhaust valve condition—using borescope inspections, engine monitor data, and oil analysis—detect incipient valve problems, and deal with them before in-flight failure occurs. See you next month.
You bought a plane to fly it, not stress over maintenance.
At Savvy Aviation, we believe you shouldn’t have to navigate the complexities of aircraft maintenance alone. And you definitely shouldn’t be surprised when your shop’s invoice arrives.
Savvy Aviation isn’t a maintenance shop – we empower you with the knowledge and expert consultation you need to be in control of your own maintenance events – so your shop takes directives (not gives them). Whatever your maintenance needs, Savvy has a perfect plan for you: