We have the technology to prevent these failures by detecting them in the incipient phase.
Last month we discussed how exhaust valves fail and why they sometimes fail prematurely. This month, we’ll shift our focus to how we can monitor exhaust valve condition, detect incipient valve problems, and deal with them before in-flight failure occurs.
I started last month’s column with a description and photos of an in-flight exhaust valve failure that occurred in my airplane nearly 20 years ago. That failure occurred “back in the bad old days” before we had the sophisticated engine monitoring tools that we have today—specifically spectrographic oil analysis, borescope inspections, and digital engine monitors. Nowadays, there’s no excuse for such an in-flight failure because we have the technology to detect these problems early. Anyone who experiences an in-flight exhaust valve failure today just wasn’t paying attention.
Borescope Inspections
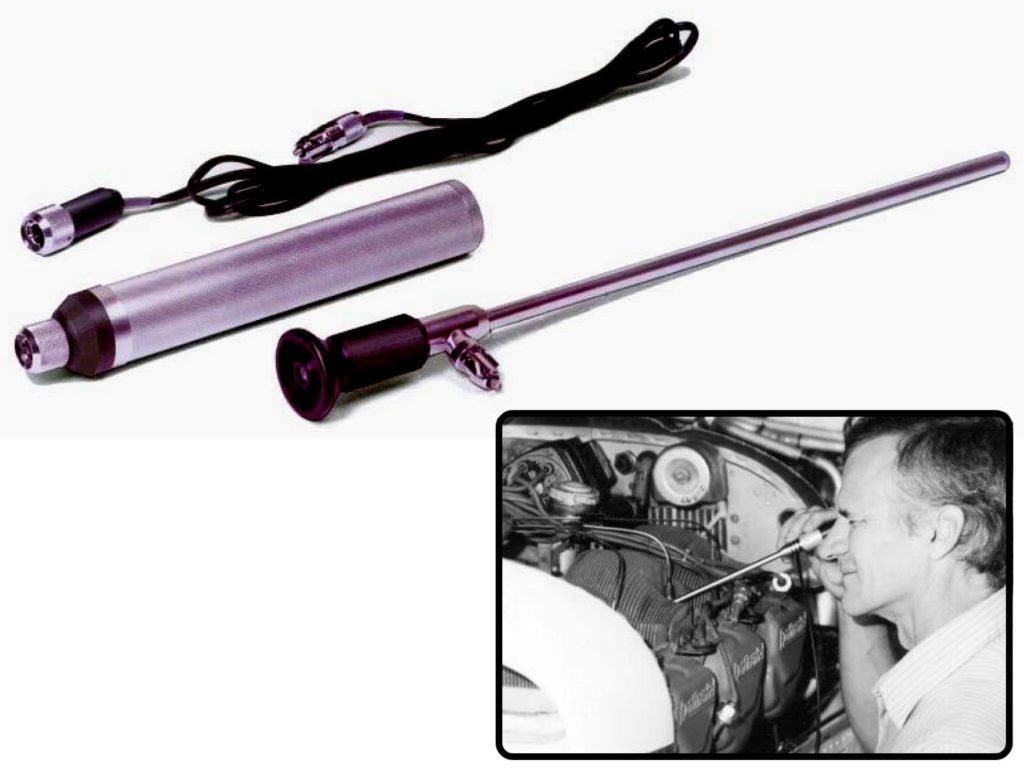
In my opinion, regular borescope inspections should be our first line of defense against exhaust valve failure. The borescope is an optical probe (see Fig. 4) or a subminiature digital camera (depending on which model is used) that can be inserted through a spark plug boss (usually the top one). It is used to perform a direct visual inspection of the combustion chamber, including the valves, cylinder head, cylinder barrel and piston crown. The borescope permits a quick, inexpensive, unambiguous determination of whether the exhaust valve is operating normally, or whether it is starting to burn or stick.
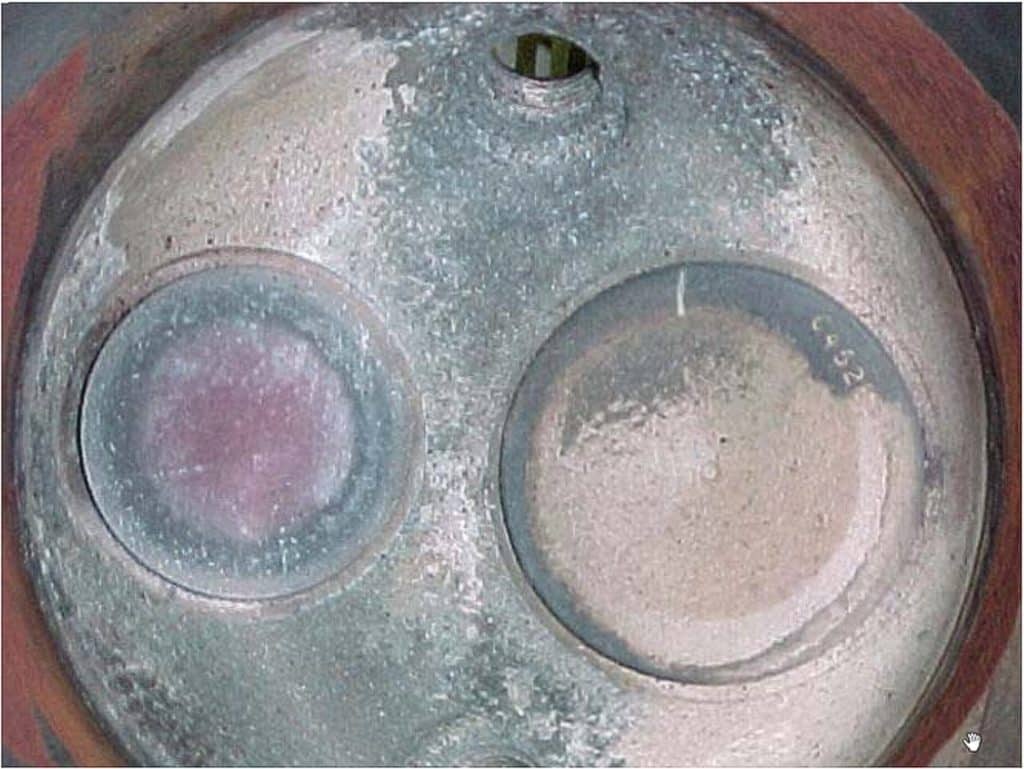
Figure 5 shows the appearance of normal valves in a TCM cylinder. The smaller valve on the left is the exhaust valve. Note the reddish pattern of exhaust deposits on the face of the valve. The deposits are quite minimal, indicating that this cylinder has been running a nice, lean, clean-burning mixture that produces relatively few deposits. More importantly, the deposit pattern is almost perfectly symmetrical—similar to a bullseye—showing that this valve is operating at the same temperature all the way around the circumference of its face, with no hot spots. That’s exactly the way a healthy exhaust valve should look.
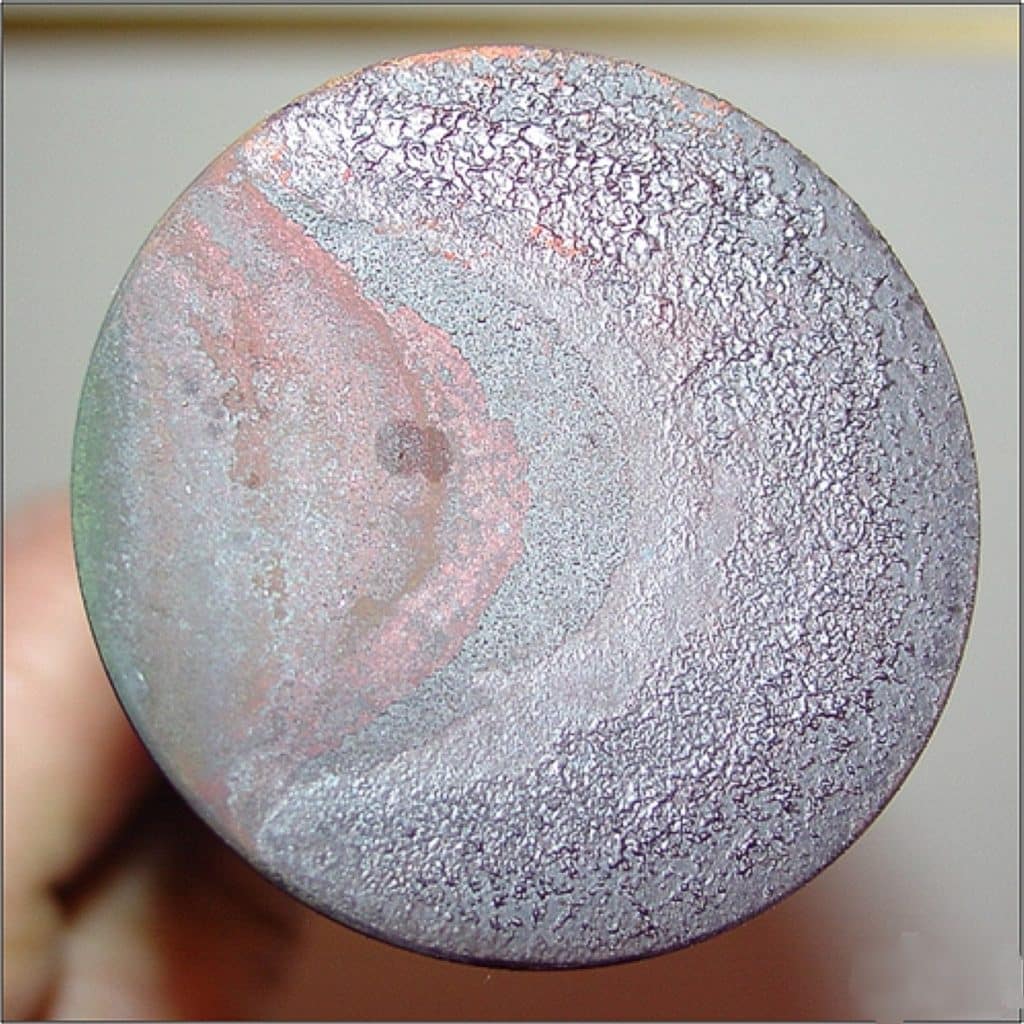
Compare that with the exhaust valve in Figure 6. Look at the highly asymmetrical pattern of exhaust deposits on the face of this valve. The cylinder has been running rather rich, causing thick deposits to form around most of the circumference of the valve face. But the valve has an extreme hot spot in the 8 to 10 o’clock position, so hot that is has burned off almost all the exhaust deposits in this area. This valve is in very serious shape, and wouldn’t have survived very many more hours without failing.
The borescope inspection is the gold standard for evaluating exhaust valve condition. Unlike the differential compression test (which has proven to be inconsistent and unreliable), the borescope provides a clear, unambiguous indication of whether or not the exhaust valve is healthy. If the valve has a symmetrical appearance under the borescope, it’s fine. If the appearance is asymmetrical (lopsided), the valve is in distress and needs to be replaced. Simple as that.
The only problem with borescope inspections is that they need to be done regularly, and often enough to ensure that a distressed valve is detected before it fails in flight. How often is that? My research indicates that a well-trained inspector can generally detect a hot spot on an exhaust valve 100 to 200 hours before the valve fails in flight. If you have your cylinders borescoped at intervals of 100 hours or less, you can be fairly confident that a burned exhaust valve will be detected before it fails in flight.
By happy coincidence, 100 hours is just about the right interval for cleaning, gapping and rotating spark plugs. If the top cowling and the top spark plugs are removed, then doing a borescope inspection is a no-brainer, and shouldn’t take more than an extra 30 minutes. In fact, any time a spark plug is removed from a cylinder for any reason, it would be crazy not to stick a borescope in the hole and look around.
Engine Monitor Analysis
These days, an increasing proportion of the piston aircraft fleet—including the majority of high-performance aircraft—are equipped with digital engine monitors that display and record per-cylinder EGT and CHT data and often numerous other parameters as well. The digital engine monitor should be our second line of defense against exhaust valve failures. Although it can’t give nearly as much advanced warning of valve distress as the borescope, the engine monitor’s compelling advantage is that is that it monitors the engine continuously, and doesn’t need to be scheduled.
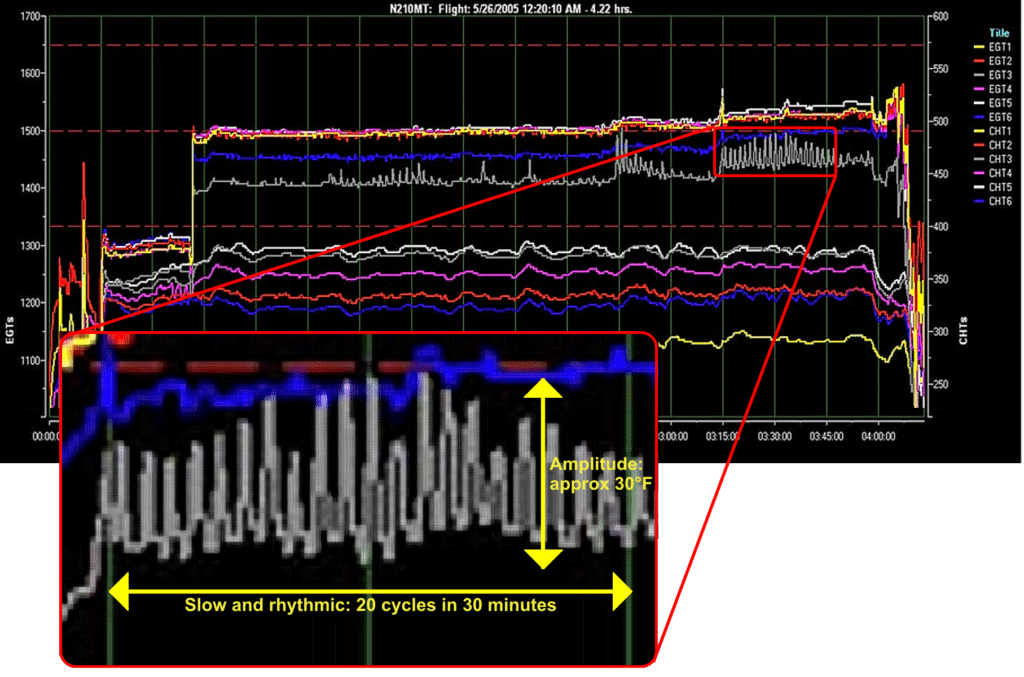
Look at the engine monitor data dump in Figure 7, and focus on the anomalous appearance of the EGT trace for cylinder #3 (light gray trace). At first glance, this might seem like it’s coming from a failing probe or a loose connection. But closer examination reveals that the EGT oscillations are not rapid and random (as one would expect from a bad probe or connection), but rather very slow and almost perfectly rhythmic. As the inset shows, the EGT oscillated exactly 10 times in each 15-minute period, and for a total of exactly 20 cycles in 30 minutes—a bit less than one cycle per minute. A failing probe or connection can’t do that. In fact, there’s only one thing that can do that: a failing exhaust valve.
Most Lycoming and TCM engines employ a “rotator cap” mounted at the tip of the exhaust valve stem that causes the valve to rotate a fraction of a degree every time the valve cycles open and closed. The purpose of this valve rotation is to prolong valve life by equalizing the heat load around the circumference of the valve face, and helping to keep the valve and seat clean and free of deposits. The rate of valve rotation varies with engine RPM and rotator cap construction. For most TCM engines it’s about one revolution per minute at typical cruise RPMs, a bit faster for most Lycoming engines.
Consequently, if you notice a slow, rhythmic variation of EGT with a frequency on the general order of once cycle per minute, there’s only one phenomenon that can possibly account for that EGT variation: exhaust valve leakage. Your response to such an observation should be to schedule a borescope inspection of the offending cylinder as soon as possible. In all likelihood, the borescope will reveal that the exhaust valve has an obvious hot spot, and the cylinder will need to come off for replacement of the exhaust valve and guide and dressing of the valve seat.
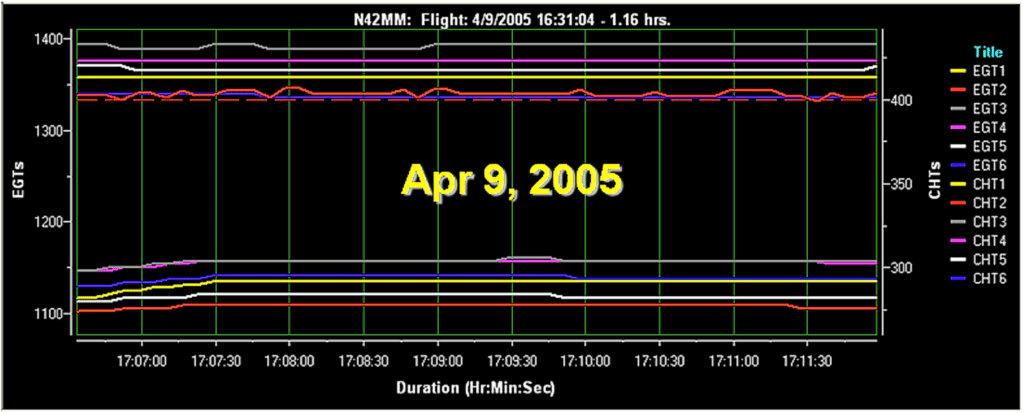
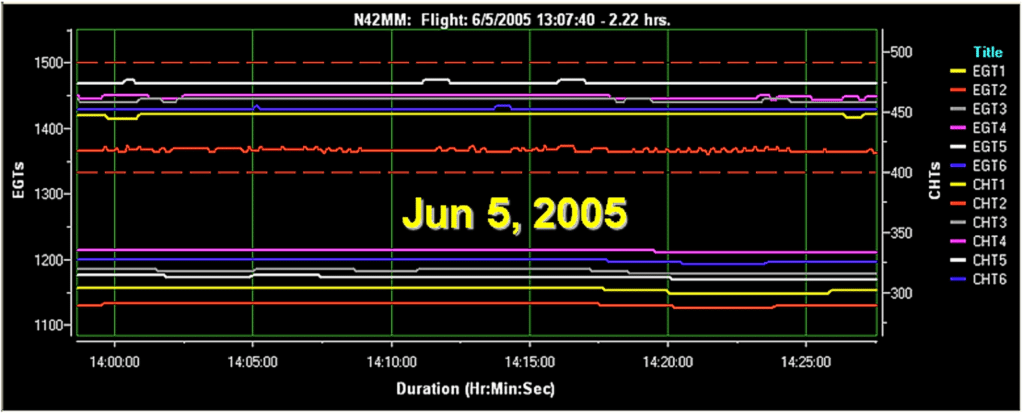
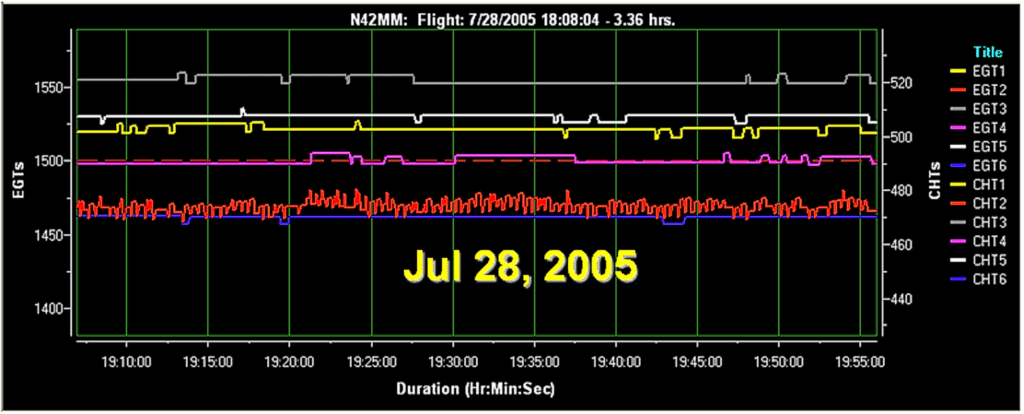
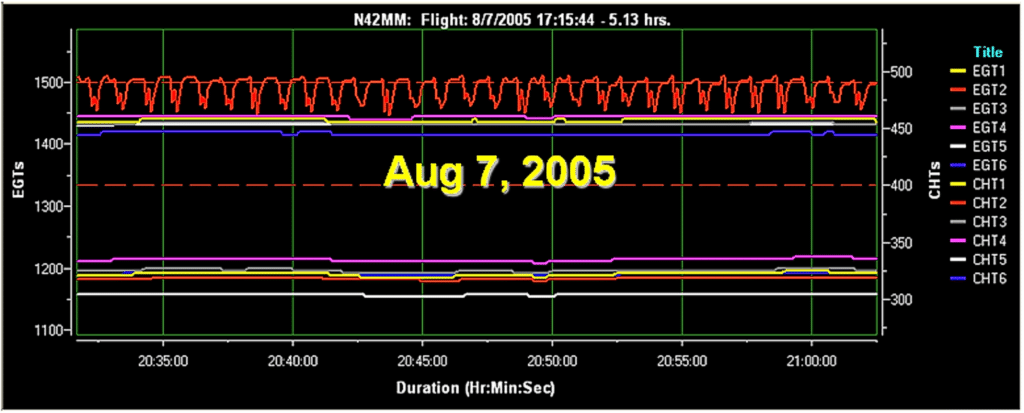
Figure 8 shows the progressive deterioration of the #2 exhaust valve (top red trace) in a Bonanza’s TCM IO-520 engine over a period of five months. Note how the EGT variation becomes increasingly obvious, regular and rhythmic as the exhaust valve deteriorates. Also note the frequency: almost precisely one cycle per minute. The valve was literally crying out for attention. Ultimately the owner noticed the problem and pulled the cylinder before the valve failed in-flight.
The engine monitor will not give nearly as much advance warning of a failing exhaust valve as the borescope, but my research suggests that it will give something on the order of 25 hours lead time before failure—provided the pilot is paying attention and knows what to look for (and now you do).
Note that this EGT signature depends on the fact that the exhaust valve is rotating during engine operation. A few engines don’t use rotator caps (notably Lycomings with solid-stem exhaust valves), and certain failure modes (e.g., stuck valves) may prevent the valve from rotating. Therefore, the slow rhythmic EGT variation may not be present in every failing exhaust valve scenario, but it will be present in most of them.
Oil Analysis
A third line of defense against exhaust valve failure is spectrographic oil analysis. We’ve seen that exhaust valve failure is usually caused by accelerated valve guide wear. Exhaust valve guides are made of a high-nickel alloy, so accelerated guide wear usually shows up in oil analysis as increased nickel.
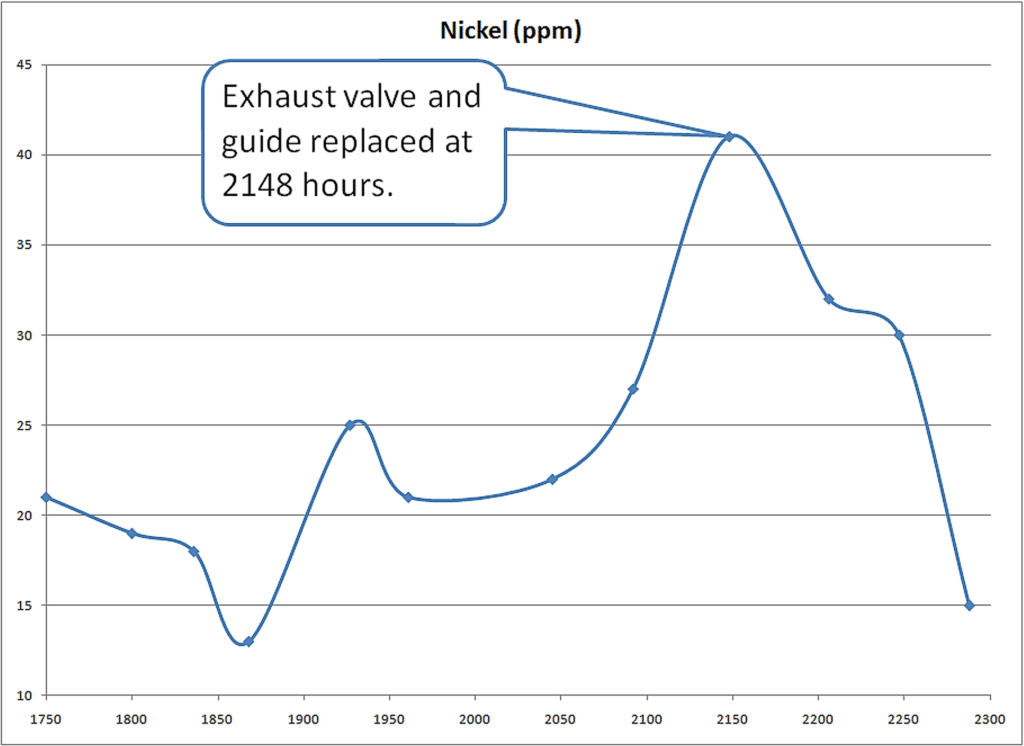
Figure 9 shows 550 hours worth of history of nickel readings in the left engine of my Cessna T310R. This engine had traditionally “made” about 14 parts per million (ppm) of nickel during the first 1500 hours since major overhaul, which is about normal for a six-cylinder TCM engine. Then the nickel readings started acting strange, rising into the low 20s, then the high 20s, giving warning of accelerated exhaust valve guide wear.
Unfortunately, oil analysis cannot identify which cylinder is the culprit. But the increasing nickel readings put me on notice that there was likely to be a failing exhaust valve in my future. Consequently, I started watching the engine monitor carefully, and started doing more frequent borescope inspections. Eventually, the #3 exhaust valve was found to be developing a hot spot. At 2,148 hours SMOH, the #3 cylinder came off and the exhaust valve and guide were replaced. Nickel then started to decline as the new valve and guide broke in, and after a few oil changes it dropped back to a healthy 15 ppm.
By using oil analysis, engine monitor data, and regular borescope inspections, exhaust valve distress can be detected reliably long before the valve reaches the point where it will fail. Nowadays there’s really no excuse for suffering the kind of swallowed valve episode that I experienced two decades ago. We have the technology to eliminate these failures.
You bought a plane to fly it, not stress over maintenance.
At Savvy Aviation, we believe you shouldn’t have to navigate the complexities of aircraft maintenance alone. And you definitely shouldn’t be surprised when your shop’s invoice arrives.
Savvy Aviation isn’t a maintenance shop – we empower you with the knowledge and expert consultation you need to be in control of your own maintenance events – so your shop takes directives (not gives them). Whatever your maintenance needs, Savvy has a perfect plan for you: