Much of the award-winning advertising from the last several decades was produced by Weiden + Kennedy. As they grew and pushed the creative envelope, their motto became “Fail Harder” – if your failures are small you’re not trying hard enough. As pilots and airplane owners it would be nice if nothing ever failed. Since that’s not realistic, maybe we could save time and money if things failed harder. On second thought no thanks – too many rough runners, dead-stick landings and dark glass panels where purple and green should be. Sometimes the engine monitor data gives us great clues on where to start looking. Sometimes the best you can do is rule things out.
Let’s begin this month with data from a Cirrus SR22T with a Continental TSIO-550-K and data from a Garmin G1000 with a 1 sec sample rate. EGTs on top, then CHTs and FF.
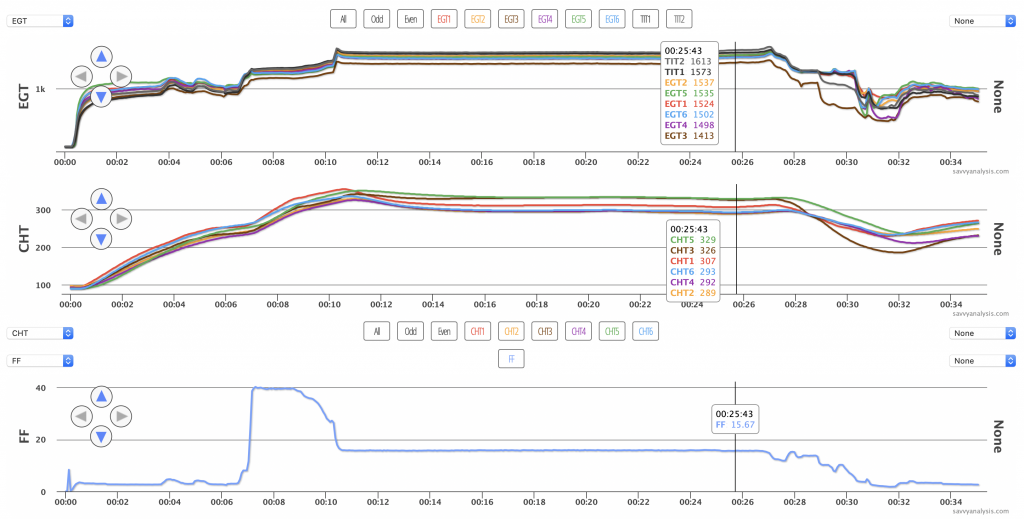
Up to about the 27 min mark things look ok. EGT 3 has pulled away from the pack to the low side, but it’s steady. Cruise CHTs are great at 300º ± 25º. CHTs 1-3-5 are a little hotter than 2-4-6 as a group, but that’s not corroborated in EGTs 1 and 5, which are mixed in with the others, while 3 is low. Then at 27 mins cyl 3 starts dropping. I won’t show the flight map because it would be easier to identify the aircraft – which we don’t do without permission – but if you saw it you’d see a big fishhook as the pilot diverts to an airport he just passed, and lands without incident.
The pilot reported the engine started to run rough with some shaking, mag check was the same on either mag, the engine still ran rough on the ground. He got it to a shop who observed zero compression on cyl 3 when hot, borescope showed no evidence of a burned spot on the valve face, no indication of the FEVA pattern in the data, but the valve wasn’t closing all the way. Based on that what can we rule out? It’s not acting like a fuel problem or an induction problem, and weak spark usually sends EGTs higher and this one’s lower.
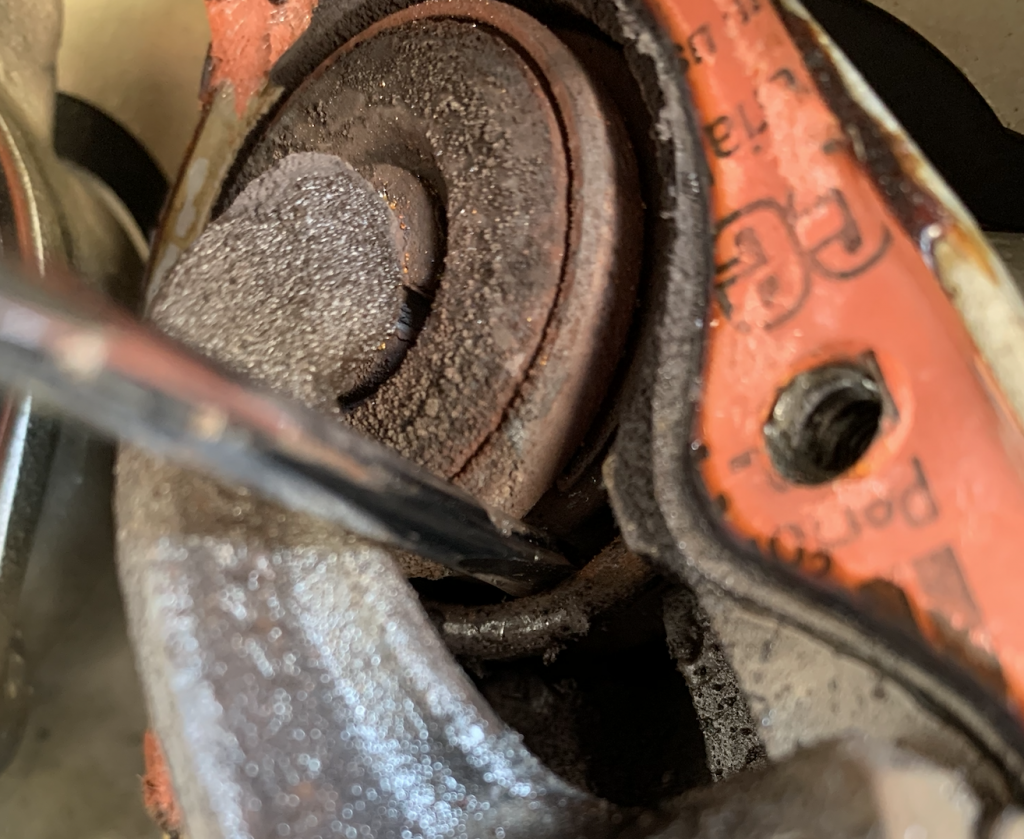
What keeps a valve from closing completely? A worn cam lobe, a bent valve stem, or a broken valve spring. Here’s the picture the shop sent us of the broken spring.
Looking back through the data, we didn’t see any trend that would have flagged this as an impending failure. EGT 3 had been low for a while and was sometimes lower than the others at engine start, but no roughness was reported. We also didn’t see anything in the data that pointed to poor powerplant management or poor maintenance.
Would you want your valve spring to fail harder? Since this is a dreamworld anyway, I’ll go with the ideal being some indication in the data – and this slightly lower EGT is too subtle for my ideal – that triggers a borescope inspection which reveals the broken valve spring on the ground during inspection. And while we’re at it, let’s have it happen when I was going to change the oil anyway.
Next is data from a Cessna 182RG with a Lycoming O-540 engine and data from a JPI 700 with a 6 sec sample rate. Here are two flights about about two weeks apart. There’s nothing special about cursor placement – just keeping it out of the way.
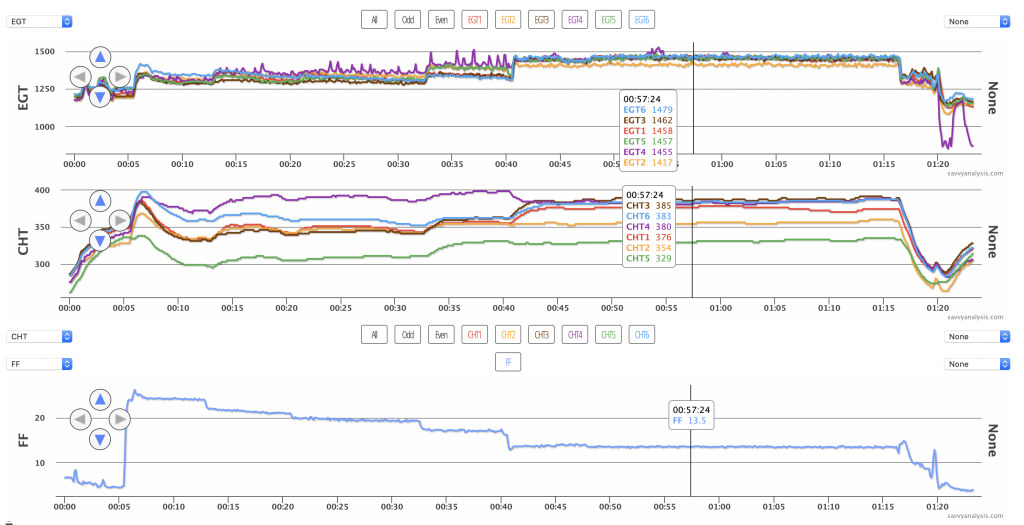
On the first flight something bad is happening on cyl 4 until about the 40 min mark, when it settles down. Did it fix itself once and for all, or is the anomaly conditional on higher FF, or angle of attack, or altitude – maybe temperature – or something else?
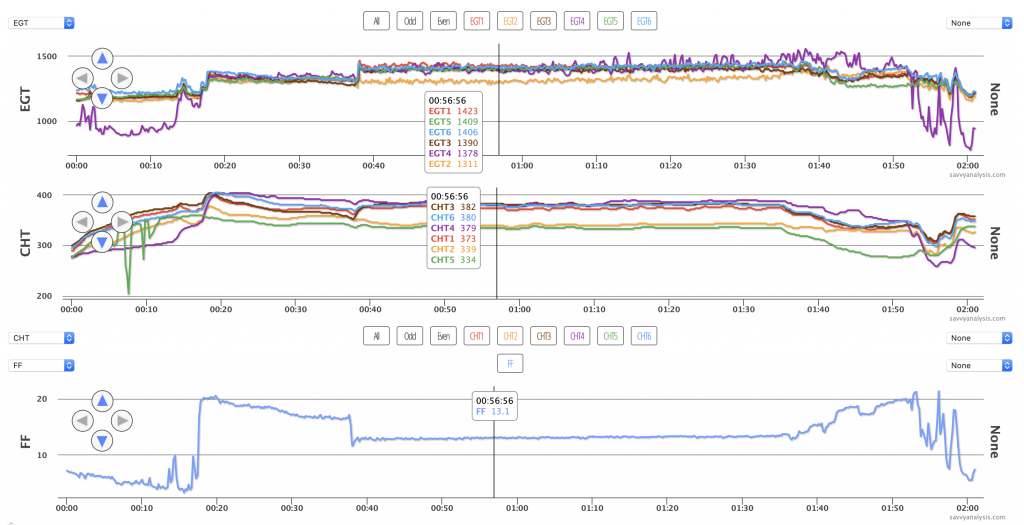
On this flight cyl 4’s low EGT and CHT during taxi-out look like a stuck valve. But it looks ok in the runup and when power is applied. EGT 4 is not steady, but it’s not showing the oscillating pattern of a burned valve that our FEVA scan looks for. It’s a carbureted engine so we can rule out injectors. It’s definitely worse as the flight progresses, which is just the opposite of the previous flight.
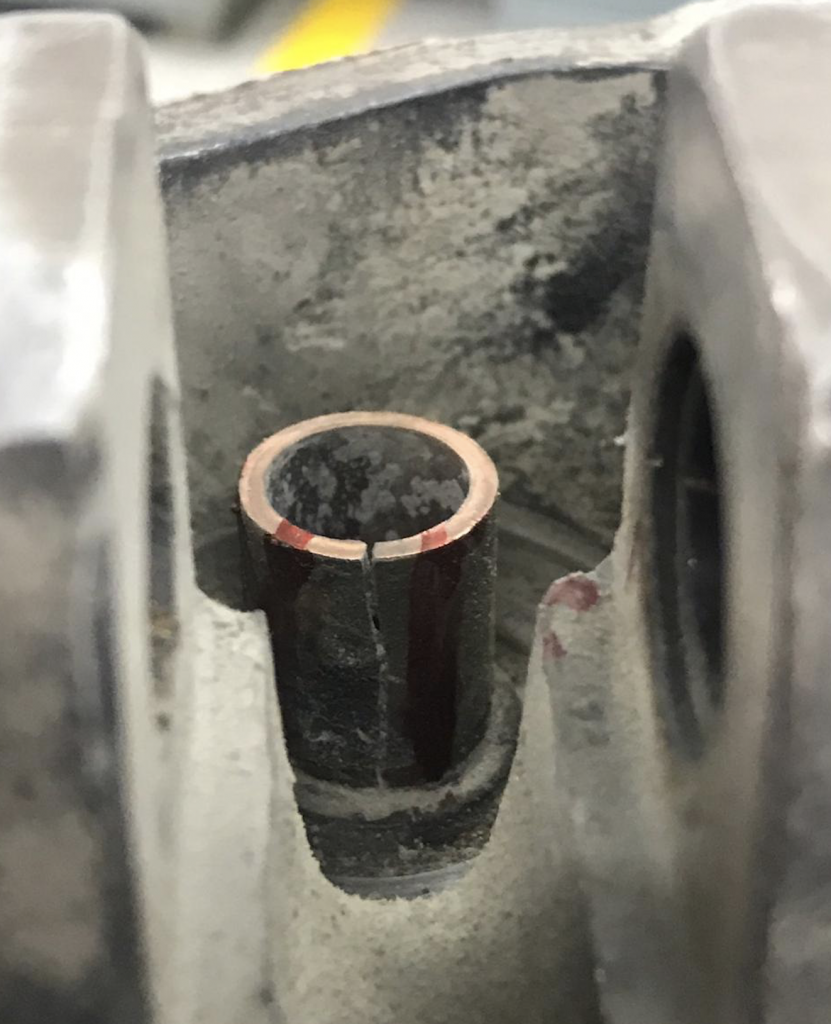
MAP isn’t logged so we don’t have that as a clue for an induction leak, but an induction leak caused by a leaky gasket or a tear in a sleeve is typically steady – not jumpy like this. Is there a scenario where the induction leak could be jumpy? It’s probably not the first thing that leaps to mind, but a wobbly intake valve caused by a crack in the intake valve guide could do it. Here’s the picture our client sent us.
If a part’s going to fail, this seems like the right amount of notice. It put something in the data that it was impossible to ignore or overlook, it failed enough to matter and to require attention, but it didn’t fail catastrophically and require landing on a freeway and it didn’t work its way through the engine requiring a complete tear-down. To me this is a Goldilocks failure.
Here’s another Cessna 182, this one has a Lycoming O-470 engine and data is from a JPI 700 with a 6 sec sample rate. FF is not logged, which explains the GAMI button being greyed out, so I included Carb Temp in the 3rd rank.
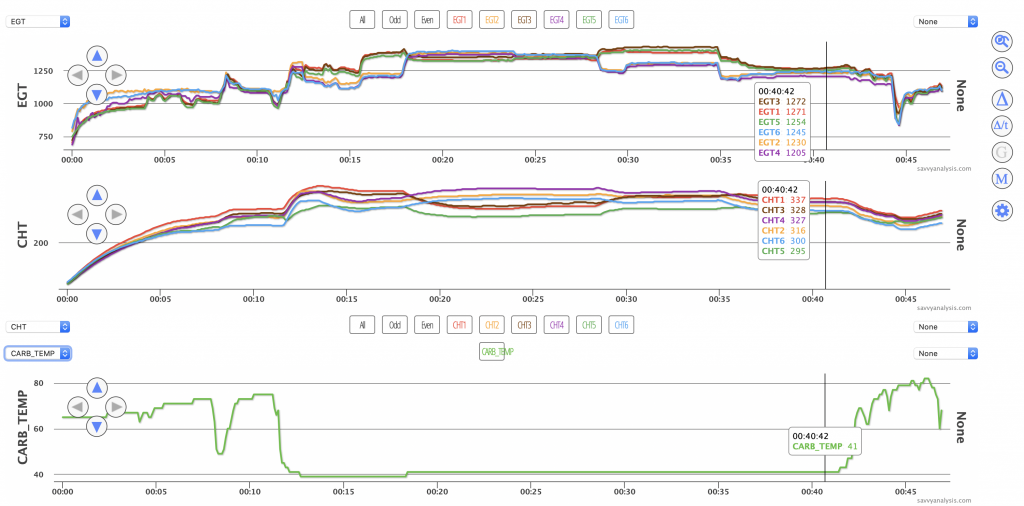
Normally I wouldn’t put two 182s back to back, but given that we just covered what a leaky induction tube would look like, this should be a gimme. 1-3-5 and 2-4-6 have very different patterns some of the time, and then are remarkably uniform around the 25 min mark, before splitting up again. MAP isn’t logged, but let’s assume it was full throttle and ambient pressure at takeoff and climb. Carb heat can shuffle the deck when it comes to induction, and I expected to see it change along with the EGTs, but as you can see it doesn’t.
Of the range of possibilities – spark, fuel or air – this looks like an air problem. We recommended checking the induction system and were happy to hear that when they pressurized the system with a vacuum cleaner they found a leak between cyls 3 and 5. To me this is another Goldilocks failure – no harm, no foul and no diversion but a clear indication that something needs fixing.
Last up this month is another Cirrus SR22T with a Continental TSIO-550-K and data from a Garmin Perspective with a 1 sec sample rate. EGTs on top, then CHTs, then FF and MAP. The cursor is on the left to show you MAP at idle.
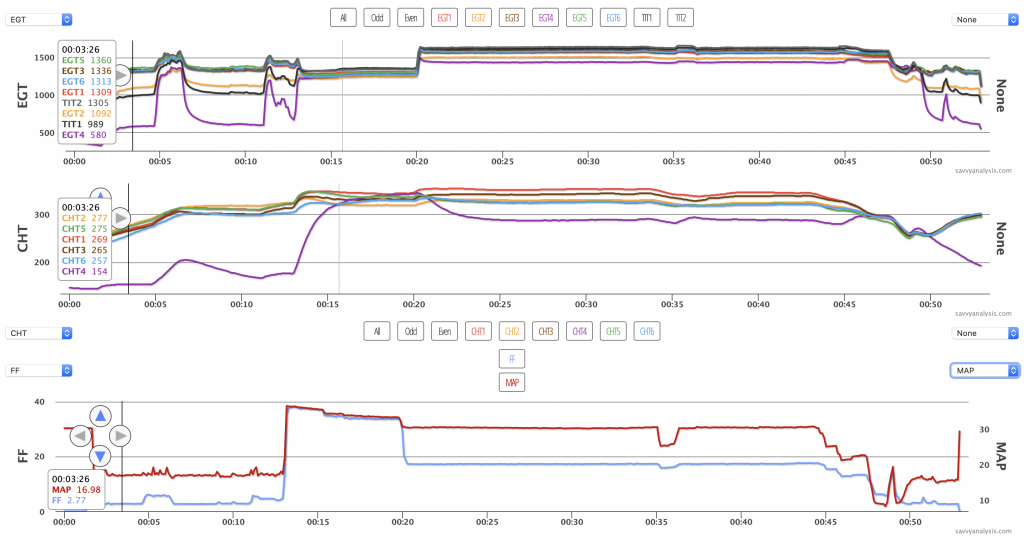
If you’ve read these Puzzlers before you’ve heard my speech about taking off with known malfunctions. We’ve all got our personal minimums and for me a very low EGT along with a very low CHT is one too many. That tells me something’s wrong and it isn’t just bad data. Enough about that.
The high MAP at idle is often a symptom of an induction leak. When the throttle is mostly closed, the air sneaks around the closed throttle and the cylinder is too lean. When the throttle is wide open the leak doesn’t matter. In a turbo, when the throttle is partially closed – like at the 20 min mark – the turbo is contributing incoming air, so the leak is less of a factor.
I’d say this is also a Goldilocks failure. The data gets your attention. For me it would have scrubbed the flight, but nothing bad happened. We received this note from our client —
The big surprise today was to discover that all 4 bolts on cylinder 4 induction tubes were loose. The gasket was partially gone. The engine was running on 5 cylinders at low RPM.
The aircraft was fresh out of annual inspection. All 6 intake manifold gaskets were replaced but cylinder 4 bolts were simply hand tightened instead of the required 85 in/pound.
I thought about calling this Puzzler Respiratory Failure and didn’t for three reasons. First, it’s a little too close to the daily news and the pandemic we’re all trying to live through. Second, the first two cases were mechanical failures but not induction failures. And third, if I give you the answer in the title then it’s not a Puzzler anymore.
Stay healthy.