You’re on a trip when a mechanical arises. First you mutter the obligatory expletives, and then you must decide: Should you get the problem fixed now, or live with it until you get home?
Nothing is more frustrating than dealing with mechanical problems on the road. It’s always uncomfortable when you’re far away from your usual support system—your trusted mechanic, your hangar, your toolbox. To add insult to injury, mechanicals invariably seem occur at the most inconvenient possible time and place—like Sunday at Sheepdip County Airport when you’ve just gotta be back at work Monday morning. It’ll be a miracle if you can find a local A&P at Sheepdip on a Sunday…and if you do, he’ll probably be named “Bubba” and you might just get the uneasy feeling that Bubba knows he’s got you by the short ones.
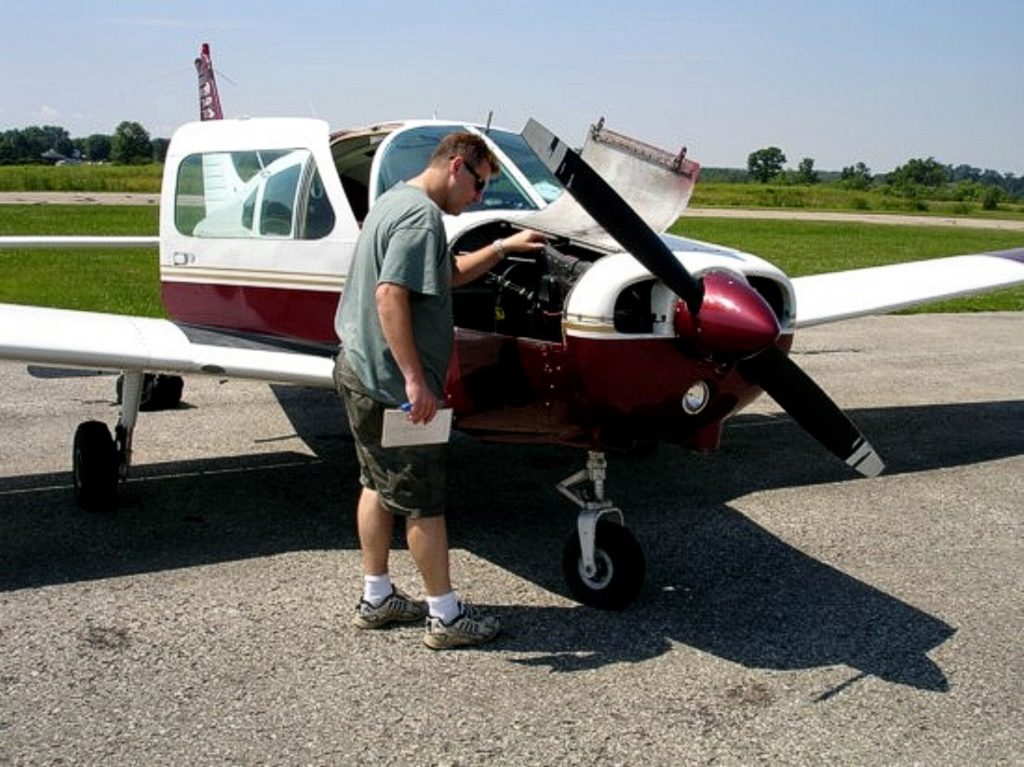
It’s natural to ask yourself whether it’s really necessary to fix the problem before further flight, or whether it’s okay to press on and get it resolved after you return home. There’s a strong temptation to defer the maintenance until a more convenient time, and often that’s a perfectly reasonable thing to do. But sometimes it isn’t—witness numerous NTSB accident reports in which the probable cause is “pilot’s decision to operate the airplane with a known deficiency.”
So, do you fix it now…or fix it later? Is fixing it now really necessary? Is fixing later really safe? It all depends.
What’s wrong, exactly?
Your first question should be this: Do I know exactly what’s wrong? Unless you are confident that you know the cause of a problem, you can’t make an informed decision about how serious the problem is and whether or not it’s safe to fly with it.
Often the cause is obvious—flat tire, inoperative radio, burned-out landing light bulb, noisy attitude gyro—and your decision is often straightforward. Sometimes, however, the cause is not so obvious. Are you absolutely certain about where that fine oil mist on the windshield is coming from? What that slight fuel odor in the cockpit really means? Why the engine seems to be running rougher that usual? Whether that dead #5 EGT indication signifies a non-firing cylinder or just a broken wire? In cases like these, you need to investigate further before making a go/no-go decision
Experience teaches that even seemingly minor anomalies are worth investigating before flight. I recall one time when I noticed a little “static” in my comm radios that I never heard before. It was so subtle that I’d have completely ignored it had I been flying any other aircraft but mine. But I knew my airplane well enough to know this wasn’t normal, so I investigated further. After some experimentation, I discovered that the noise would disappear when I turned off the right magneto on the left engine. I pulled the top cowling on the left engine and discovered that the four nuts that secure the ignition harness to the right magneto were loose and backing off the studs—one was completely gone and the other three were well on their way. Had I not followed up on the static in the radios, the harness could easily have fallen off the mag in a few more flight hours.
Another time, while flying home to California from Oregon, I spotted a tiny trickle of reddish liquid on the top of the left engine nacelle. Since the only red liquid I could think of was the red-dyed oil in the hub of my McCauley propellers, I decided to make a precautionary landing to investigate. It turned out that there was a major problem with the prop (due to an assembly error when the props were overhauled three years earlier) that could have resulted in loss of a blade in-flight…quite often a fatal scenario.
The moral: Don’t fly with an anomalous symptom—even a seemingly innocuous one—unless and until you’re satisfied you know exactly what’s causing it. Once you have ascertained the cause, you can make an informed decision whether to fly now and fix later or vice-versa.
Safe to fly?
Okay, you have a problem and you’ve determined its cause. Now, how do you decide whether or not it’s safe to fly home with the problem? That’s not an easy question to answer. Risk-assessment questions never are. It’s a lot like asking if it’s safe to fly in this weather. There are a lot of variables to consider, and every pilot’s risk tolerance is different.
Personally, I’m reluctant to fly with any significant problem that affects the engine(s), propeller(s), landing gear or primary flight controls. Some years ago, a Bonanza-owner friend discovered at runup that one of his two mags was misfiring badly during runup, and elected to fly home with the bad mag shut off. He made it, but I still think it was a dumb stunt. I’ve known piston twin pilots who will tolerate a questionable mag check in one engine if the other engine is running fine, but I’m definitely not one of them—an engine failure in a piston twin can sometimes be more dangerous than one in a single.
All twins have dual alternators and dual vacuum pumps. Many singles also have backup vacuum systems and/or backup alternators. Is it okay to fly with a bad alternator or vacuum pump if you’ve got another one that’s still working? For me, the answer is “yes” ONLY if the flight is day VFR, and a resounding “no” at night or in IMC. Your mileage may vary, of course, but it’s wise to establish your own “minimum equipment list” (MEL) criteria for problems like this ahead of time, otherwise you may succumb to the siren song of get-home-it is.
One of my personal MEL rules is that my autopilot is a no-go item for me if the flight is in IMC, at night, or if it exceeds two hours in duration. The only exception is if there’s another rated pilot in the right seat. I confess that my own mileage has varied on this one over the years: I used to fly my Skylane 40 years ago solo in nasty weather and believed that “real pilots don’t need autopilots or dual vacuum pumps.” My only defense is that I was young, stupid, and felt invulnerable at the time. Nowadays, I’m more old and less bold, and won’t make anything but a reasonably short VFR flight without dual vacuum pumps and George along. If that means fixing something on the road, that’s what I do.
Will it get worse?
Any time you consider flying with a minor mechanical problem, you need to ask yourself if you’re confident that your minor problem won’t turn into a major problem before you make it home. Will that noisy attitude gyro keep gyroing for another five hours? Will that small fuel seep stay small, or will it turn into a dangerous leak? If you stop-drill that windshield crack, will it stop growing long enough to fly back to home base?
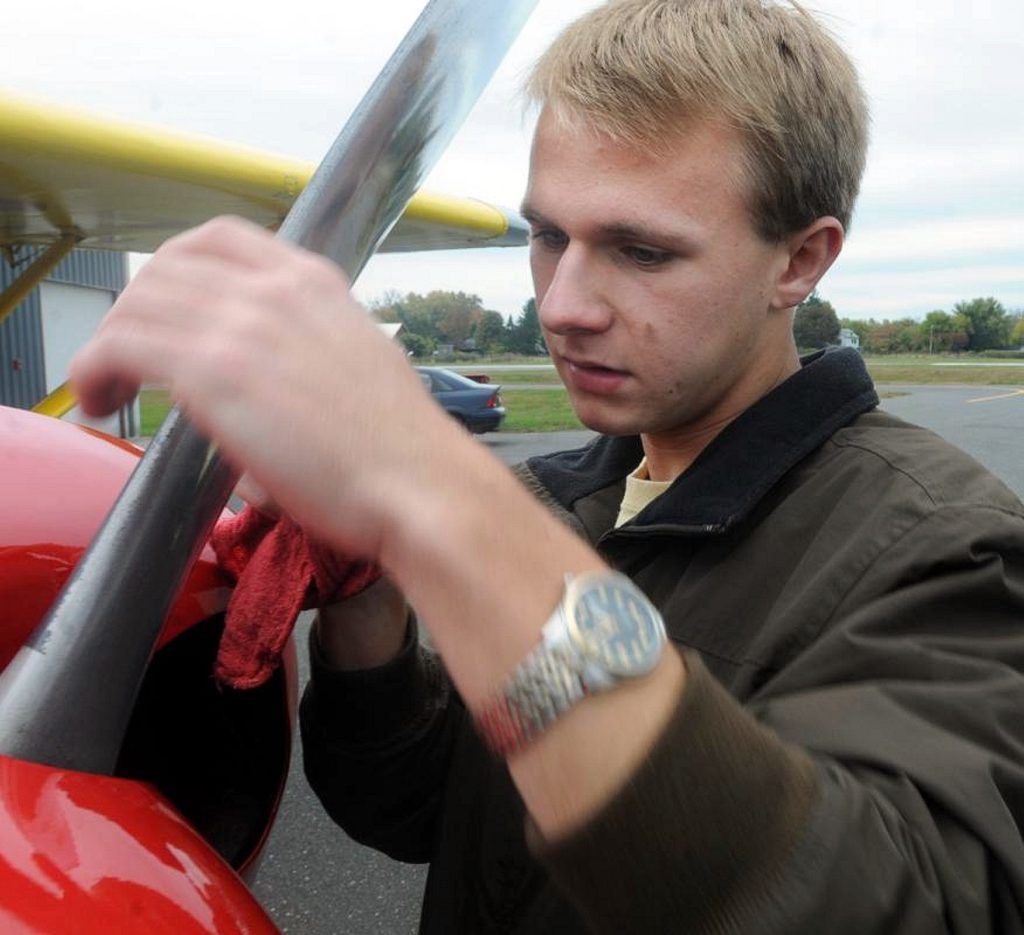
Sometimes a quick-and-dirty temporary fix is adequate to get you home so you can put the aircraft in the shop and do a proper repair. I once flew to Louisiana for an overnight stop en route to a speaking engagement in the Cayman Islands. The next morning, I was horrified to discover that the pilot-side window was cracked from the lower-front corner of the storm window opening to the edge of the frame. I didn’t feel safe flying in that condition all the way to the Caymans and back to California, but replacing the window would require downing the airplane for several days and no-showing my engagement. I wound up drilling two rows of 1/16-inch holes, one row on either side of the crack, and lacing the window back together with stainless steel safety wire. It was a truly ugly repair, but one that is FAA-approved (Advisory Circular 43.13-1B) and took me less than 30 minutes to accomplish. It held together just fine until I got back home and was able to order a new window and install it.
Another time, I discovered an electrothermal deicer coming loose from one of my propeller blades. I couldn’t fly with it flapping, but couldn’t easily down the airplane for a few days to get it replaced. After my best efforts to re-glue it failed miserably, I finally wound up securing it temporarily with duct tape—a decidedly unapproved repair, but one that worked long enough to get me home where I could install a new deicer. I still shudder to think what would have happened if I’d been ramp-checked with duct tape on my prop! (I think the statute of limitations has run on this one.)
!@#$%^&* intermittents
Intermittent problems are always the worst to deal with, particularly away from home. Invariably, such problems never happen when you’re trying to show them to the mechanic. Since a mechanic cannot properly troubleshoot a problem that he cannot reproduce, he has only two options: (1) confess he doesn’t know what’s wrong, or (2) guess as what might be wrong and replace one or more parts based on that guess. Mechanics hate to admit they don’t know to fix your problem, so more often than not they wind up guessing and hoping they get lucky. More often than not, such “shotgunning” winds up costing you time and money and very well might not cure the problem.
If your intermittent problem is potentially life-threatening—for example, intermittent oil pressure fluctuations—then naturally you have little choice but to deal with it right away, even if that requires guesswork, downtime and expense. But most intermittents aren’t life-threatening, and for those the best approach is often to be patient and wait until the problem worsens to the point that it can be reproduced and troubleshot. For such problems, deferring maintenance until you get home is often the wisest course of action.
Sometimes, of course, the problem won’t wait until you get home, and will worsen to the point you need to deal with it. Some years ago, I flew from California to New England shortly after completing a heavy annual that involved replacing the turbochargers on both engines. The engines ran perfectly all the way to New Haven, Connecticut. Then, while climbing out from New Haven headed towards Boston, the right engine stumbled—once—for about a second. It then ran perfectly for the remainder of the 30-minute flight to Boston. After landing at Boston, I performed and extensive runup and everything seemed perfectly normal. So although I was concerned about the earlier stumbling episode, I chose not to deal with it.
A few days later, while flying from Boston to Poughkeepsie, the right engine started running very rough (as in change-of-underwear rough), and this time the problem wasn’t intermittent. Shoving the mixture to full rich smoothed out the engine considerably. An in-flight mag check seemed normal. I elected to continue the flight to Poughkeepsie (although I probably wouldn’t have if I’d been flying a single). By the time I landed there, I knew I had a definite, reproducible problem with the right engine, and knew that it was most likely fuel-related rather than ignition-related. That was enough information to go on, so I put the airplane in the maintenance hangar at the Poughkeepsie FBO, and 30 minutes later we found that the #4 fuel injector nozzle was partially clogged with what looked like a small glob of grease. Cleaning the injectors completely cured the problem.
Fix or defer?
Here’s a brief checklist that may help you to decide whether to fix a problem now or let it wait until you get home:
- Investigate the problem and be sure you know exactly what’s wrong before making a fix-or-defer decision. Even seemingly minor anomalies can be clues to major problems, so investigate them promptly.
- Once you’re confident that you know exactly what’s wrong, decide whether it’s safe to fly home with the problem or whether it needs to be fixed now.
- Before deciding to defer maintenance, ask yourself if you’re confident that your deferrable problem won’t get too much worse before you get home.
- Consider making a temporary quick-fix that will get you home safely, then doing a proper repair at home base.
- For an intermittent problem that isn’t a safety-of-flight issue, the wisest course is often to be patient and let it get worse.
You bought a plane to fly it, not stress over maintenance.
At Savvy Aviation, we believe you shouldn’t have to navigate the complexities of aircraft maintenance alone. And you definitely shouldn’t be surprised when your shop’s invoice arrives.
Savvy Aviation isn’t a maintenance shop – we empower you with the knowledge and expert consultation you need to be in control of your own maintenance events – so your shop takes directives (not gives them). Whatever your maintenance needs, Savvy has a perfect plan for you: