Don’t do anything rash until you’re sure where the oil is going.
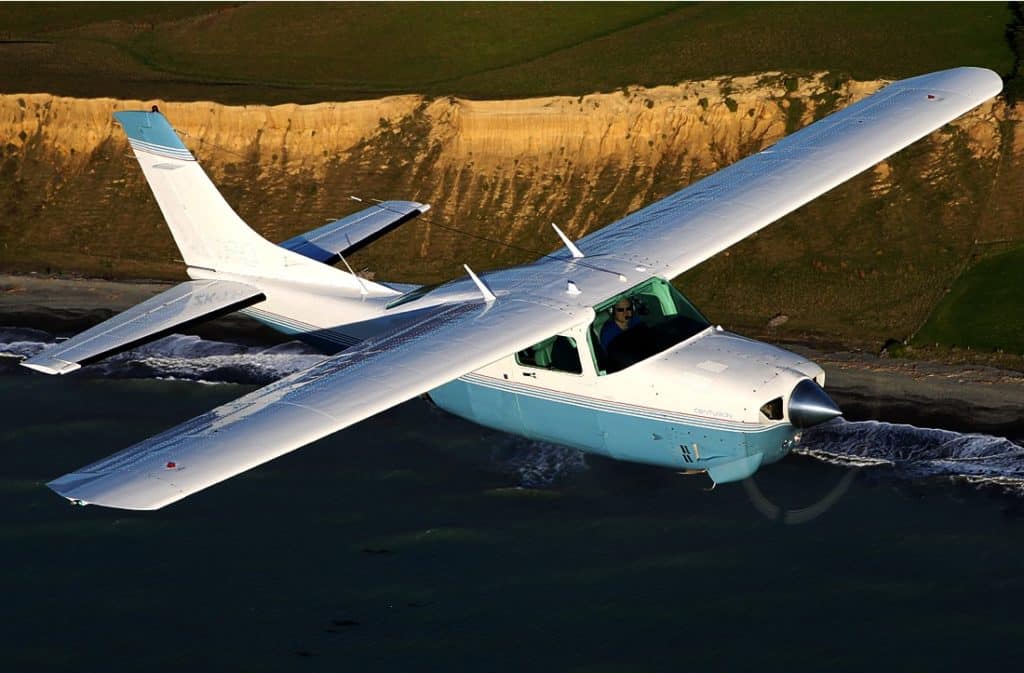
A fellow named Ted phoned me to say that his 1984 Cessna T210 was in the shop for its annual inspection, and his mechanic was suggesting a $14,000 top overhaul. “Mike, I’ve read a lot of your articles and I know you’re not a big fan of top overhauls,” Ted told me, “so I thought I’d ask your opinion before I tell my mechanic to proceed.”
“What’s the problem with your engine?” I asked.
Ted told me his oil consumption had suddenly increased dramatically to a quart every 3 or 4 hours, and that the compressions on his 1200-hour engine were mediocre (mostly 60s, a couple of high 50s). The mechanic said his cylinders were “tired,” that this was typical for a mid-time Continental TSIO-520-R, and that turbocharged Continentals seldom make TBO without cylinder replacement.
I counseled Ted to slow down and take a thoughtful approach. While his increased oil consumption was certainly a matter of concern, it wasn’t yet an airworthiness or safety-of-flight issue. Continental says maximum permissible oil consumption for this 310 hp engine is about one quart per hour (and Ted’s oil consumption wasn’t anywhere close). No airplane has ever fallen out of the sky because of high oil consumption…unless the oil consumption was so high that the engine ran out of oil before it ran out of fuel (which is always embarrassing). With a sump capacity of 12 quarts (8 useable) and a maximum IFR range of 5 hours, it would be hard to do that in a T210. So before throwing a five-digit sum of money at the problem, I suggested to Ted that some systematic troubleshooting was in order.
Where’s the oil going?
When troubleshooting an oil consumption problem, the first question to ask is always “where’s the oil going?” There are only three possibilities:
- The oil is exiting the engine through its breather line.
- The oil is leaking out of the engine somewhere else.
- The oil is getting into the combustion chamber of one or more cylinders and being “consumed” in combustion.
It’s usually not hard to figure out the answer. If the oil is departing through the breather, then there will be excessive oil on the belly of the aircraft. If it’s leaking from the engine, then there will be excessive oil inside the engine compartment. If it’s being consumed in combustion, then the inside of the tailpipe(s) will be dark and oily instead of being coated with the normal light powdery residue.
I questioned Ted about these possible symptoms. He responded that he hadn’t noticed any more oil on the belly than usual, and that the engine compartment seemed relatively dry and oil-free…but now that I mentioned it, the residue on the inside of the tailpipe did strike him as being dark and oily.
This suggested that the oil was being consumed in combustion. If so, the next obvious questions in the troubleshooting tree are “how is the oil getting into the combustion chamber(s)?” and “which cylinder(s) is/are involved?”
One way that oil can wind up in a cylinder’s combustion chamber is a bad intake valve oil seal that permits oil from the cylinder’s rocker box area to be sucked into the cylinder during the intake stroke through the annulus between the intake valve stem and intake valve guide. This problem is usually easy to localize and diagnose by using a borescope inserted into the combustion chamber through the top spark plug hole to inspect the intake valve stem when the exhaust valve is open. If the intake valve stem appears oily, then you’ve found the problem…and the fix is quick and easy (replace the intake valve oil seal) and doesn’t require cylinder removal.
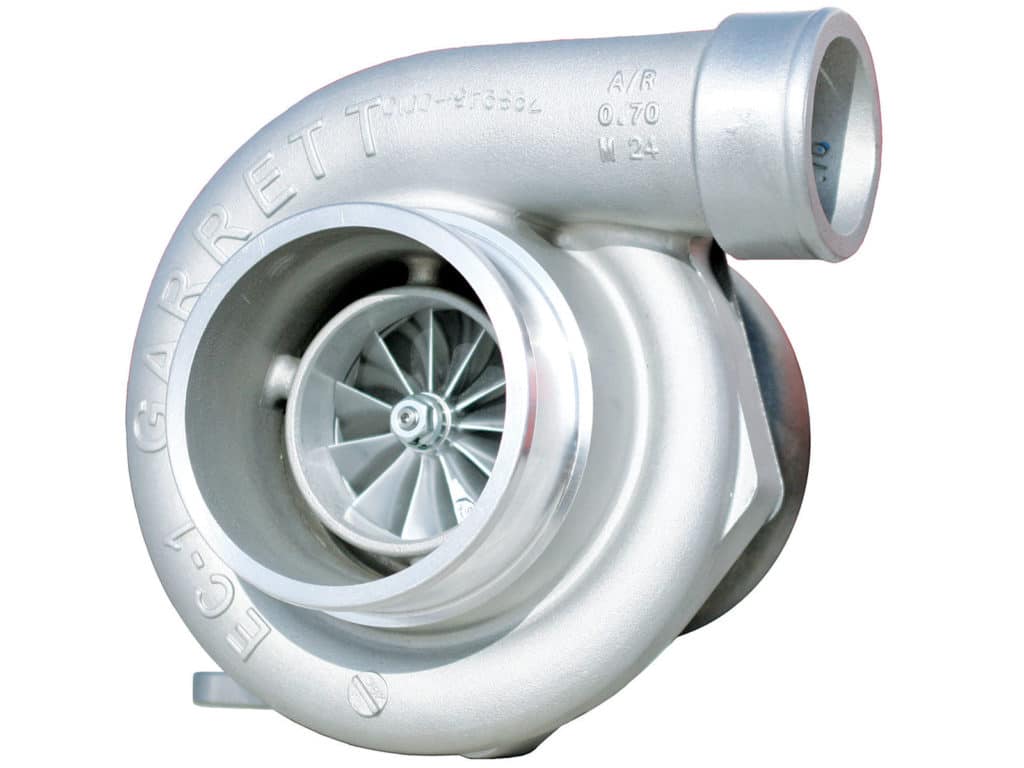
In a turbocharged engine like Ted’s, there’s another possibility. If the turbocharger has a bad oil seal that allows oil to escape from the center section into the compressor section, that oil will be “inhaled” by all cylinders, consumed in combustion, and leave a dark oily residue inside the tailpipe. In discussing this possibility with Ted, he admitted that he’d noticed a small quantity of oil dripping from the clamp where the induction air duct connects to the turbocharger compressor discharge. This struck me as being a possible smoking gun.
I advised Ted to have his mechanic disconnect the air duct from the turbocharger and inspect the compressor, which should be bone dry. If oil is found in the compressor, then my presumptive diagnosis would be confirmed, and the cure for Ted’s oil consumption problem would be a $1,400 turbocharger overhaul/exchange rather than a $14,000 top overhaul.
Oil-on-the-belly syndrome
Had Ted told me that he’d noticed a big increase in oil discharge from the breather onto the belly of the aircraft, our dialog would have focused on an entirely different branch of the troubleshooting tree. Excessive breather discharge is the most common reason for elevated oil consumption. It manifests itself as excessive oil on the belly, and it’s usually—but not always—caused by excessive blow-by past the compression rings in one or more cylinders.
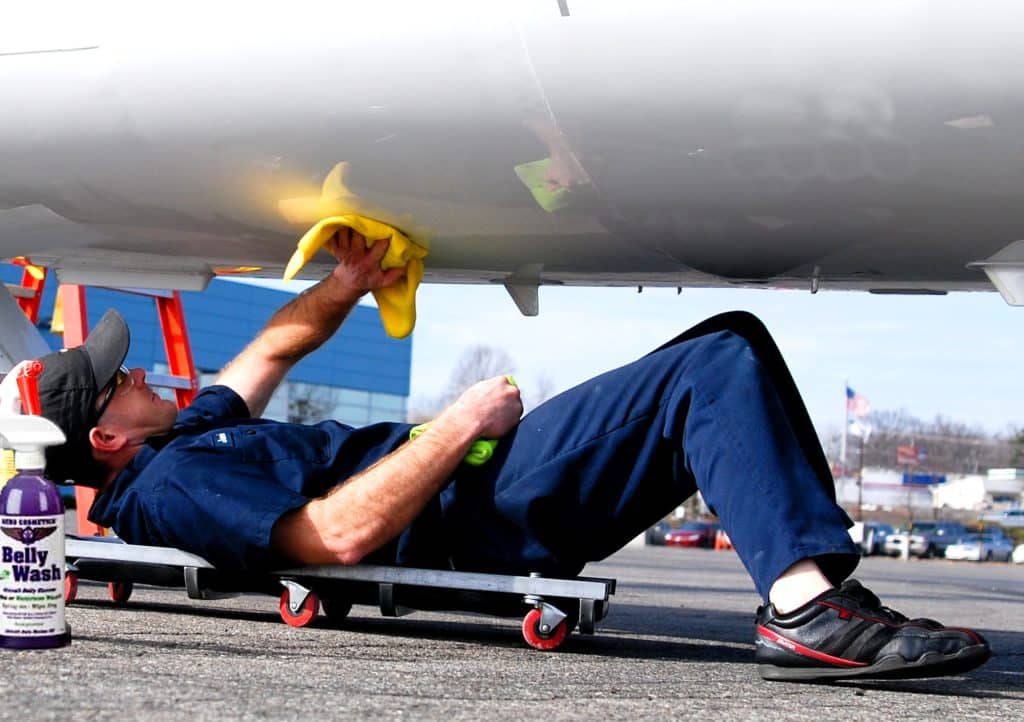
But just because you have elevated oil consumption and oil on the belly doesn’t necessarily mean that it’s appropriate to do a top overhaul. Usually it isn’t. For one thing, the problem might involve only one or perhaps two cylinders, not all of them. For another, excessive blow-by is not the only cause of oil-on-the-belly syndrome; there are several other possibilities. Once again, a thoughtful approach and systematic troubleshooting is called for before doing anything invasive or expensive.
A first step that is often useful is to measure crankcase pressure and find out whether it’s actually excessive. Continental has an old service bulletin (M89-9, “Excessive Crankcase Pressures”) that explains how to do this. The procedure involves hooking up a length of tubing to the crankcase—via the dipstick tube, a modified oil cap, or a modified timing plug, depending on engine model—and hooking up the other end of the tubing to an old airspeed indicator. (The airspeed indicator is used as a sensitive pressure gauge.) The engine is then run up at full power, and the crankcase pressure is read from the airspeed indicator. Continental’s service bulletin specifies the maximum acceptable pressure reading on the airspeed indicator; for small-bore engines (A- and C-series, O-200, O-300), the maximum is 44 mph (38 knots), and for big-bore engines (360-, 470-, 520-, 550-series), the maximum is 90 mph (78 knots). A reading above these thresholds indicates excessive blow-by. (The same approach would work for Lycomings, although Lycoming doesn’t have a Service Bulletin about it.)
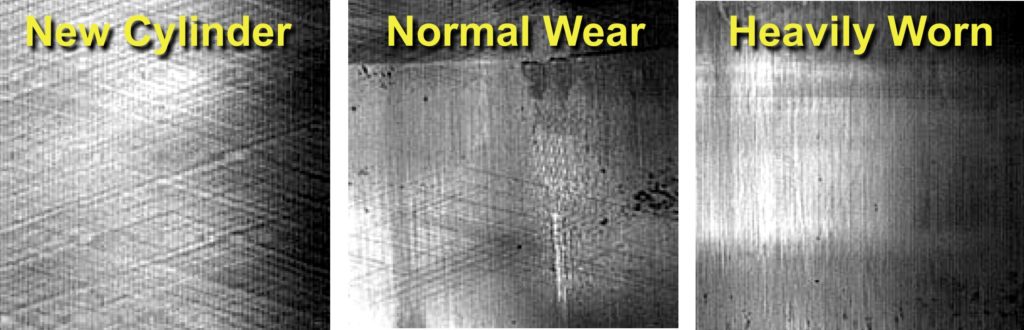
If crankcase pressure is high, then the problem is likely excessive blow-by in one or more cylinders. A confirming symptom of excessive blow-by would be oil that turns dark and opaque very quickly after each oil change.
The best way to determine which cylinder(s) is/are at fault is to perform a borescope inspection with emphasis on the condition of the cylinder barrels. Any cylinders exhibiting excessive barrel wear (shiny spots with no crosshatch), substantial barrel damage (vertical scoring), or excessive corrosion pitting are candidates for coming off for rework or replacement. Low compression with air leakage past the rings audible through the oil filler would tend to confirm the high blow-by diagnosis for a particular cylinder, although a compression test alone is not reliable enough to use as a primary diagnostic tool.
Yanking all cylinders (“top overhaul”) rather than taking the time to determine which one(s) is/are at fault is the worst kind of “shotgunning” in my opinion. What’s the probability of all six cylinders going bad simultaneously? Probably about the same as drawing a royal straight flush in poker. Think about it…
If crankcase pressure is NOT excessive, then the problem isn’t high blow-by and the problem isn’t cylinder-related. So what could be causing oil-on-the-belly syndrome? One of two things: Either something is pressurizing the crankcase in the air but not on the ground, or else something is sucking oil out the breather in flight. Pressurization of the crankcase in flight could be caused by something as simple as a leaky gasket or O-ring in the oil filler cap or dipstick, or something else that permits ram air to enter the crankcase in flight. Suction could be caused by an improperly positioned breather outlet that’s located in a low-pressure area in flight.
Oil Leaks
While an engine oil leak is a third possible escape route that could account for increased oil consumption, it’s the least likely in my experience. While engine oil leaks are quite commonplace, it would take a massive leak to cause a noticeable increase in oil consumption. Most engine oil leaks are tiny, although even a tiny leak can make a major mess in the engine compartment. A little bit of leaking oil can cover a lot of real estate rather quickly when exposed to a 100-knot breeze.
Most common sources of oil leaks—rocker cover gaskets, pushrod housing seals, magneto gaskets, garlock seals, oil filler cap gaskets, dispstick O-rings, etc.—are quick and easy fixes, and are almost always worth fixing to make sure they don’t cover up something more serious like a crankcase crack, chafed oil pan, or leaky oil quick-drain.
Chasing down the source of an oil leak is often quite frustrating because the oil spreads so rapidly throughout the engine compartment. The key is to spray down the engine with solvent until it’s scrupulously clean of oil, then run the engine on the ground (absent the 100-knot breeze) and inspect it. The application of some white aerosol powder like dye-penetrant developer (or jock-itch spray) can sometimes be helpful in localizing the source of the leak.
None of my recommendations to Ted or the other things I’ve discussed here involve rocket science, only simple logic. My advice is simply that when faced with elevated oil consumption, resist the temptation to throw money at the problem. Better to throw neurons at it instead.
You bought a plane to fly it, not stress over maintenance.
At Savvy Aviation, we believe you shouldn’t have to navigate the complexities of aircraft maintenance alone. And you definitely shouldn’t be surprised when your shop’s invoice arrives.
Savvy Aviation isn’t a maintenance shop – we empower you with the knowledge and expert consultation you need to be in control of your own maintenance events – so your shop takes directives (not gives them). Whatever your maintenance needs, Savvy has a perfect plan for you: