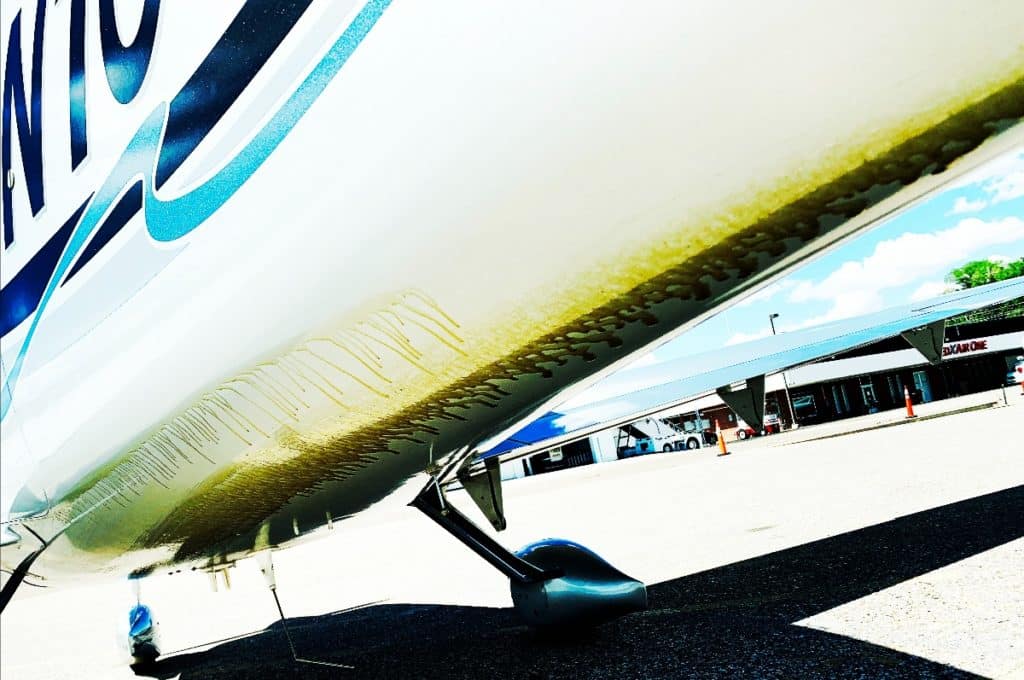
Elko Regional Airport (KEKO) is located in northeast Nevada at an elevation of 5,000 feet above sea level. The town has a population of 18,000 residents, and the airport has a small FBO (Mountain West Aviation) that offers attractive avgas prices. It’s pretty much in the middle of nowhere…but if you happen to be flying from the Pacific Northwest to Arizona, KEKO is a convenient midway fuel stop.
That’s exactly what Jack was doing one fine Thursday afternoon in his 2010 Cirrus SR22TN. The airplane had been performing flawlessly, so after landing at Elko Jack was floored to find engine oil dripping out of the left exhaust stack and streaked along the left underside of the fuselage. This is not the sort of thing that you want to see when you’re in the middle of nowhere.
Jack checked with the FBO but their A&P had gone home for the day. Fortunately, Jack had enrolled his aircraft in Savvy’s Aircraft Breakdown Assistance program (“AAA for GA”), so he called the 24/7 hotline number and quickly got a callback from Tony Barrell A&P/IA, one of Savvy’s most experienced account managers and former director of maintenance at a large Cirrus Service Center.
Remote Diagnosis
Jack sent Tony several smartphone photos of his oil-covered airplane. “No mechanic is available until tomorrow,” Jack told Tony. “Is there any value in me removing the top cowl to look for something simple?” Tony encouraged Jack to do that and take photos of what he found. As their conversation continued, Tony learned from Jack that the airplane had recently come out of an annual inspection during which all of its oil hoses had been replaced after 10 years in service. Tony suggested that Jack look closely at the oil lines to see if any of them appeared to be chafed or have loose connections.
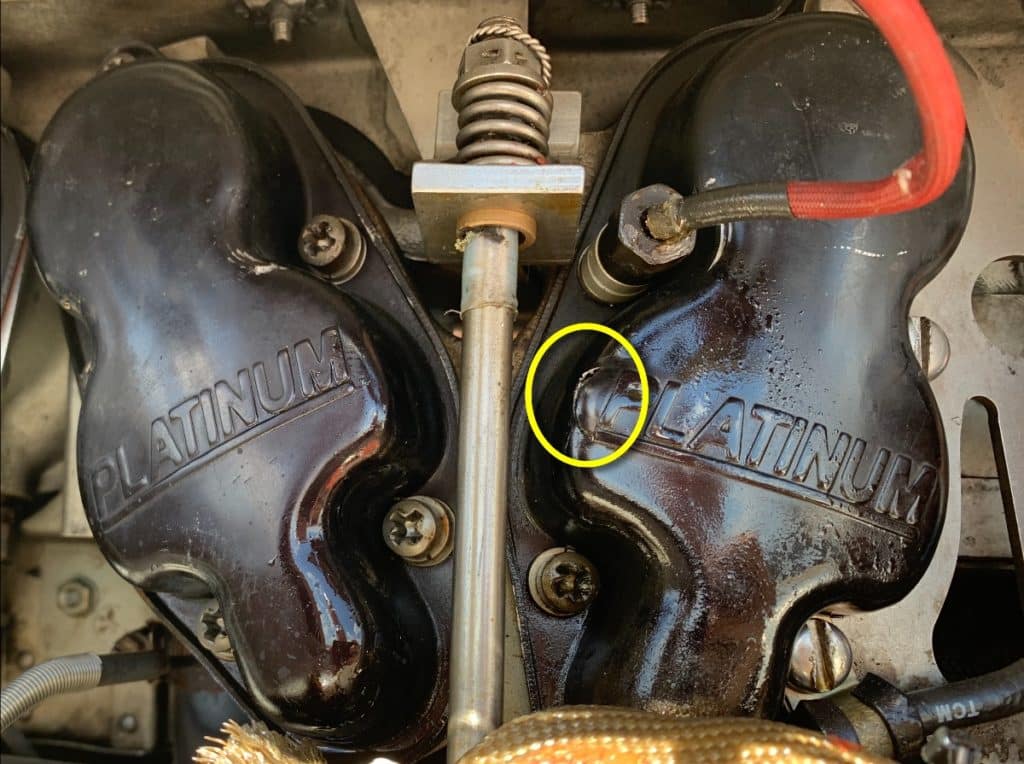
Jack removed the top cowling and sent Tony a half-dozen photos of what he found. There was oil all over the place on the left side of the engine, but all of the oil hoses appeared to be secure and intact. One photo caught Tony’s eye, however. Tony contacted another Savvy account manager, Al Hawthorne, who works closely with a big Cirrus Service Center near Sacramento, California.
“Check out the valve cover picture that Jack’s sent,” Tony told Al. “Looks to me like the cover is cracked and bulged out. Possibly the bolts securing the rocker shaft came loose. Hope not, but it looks possible. Shop on the field can’t look at this until tomorrow. Can you get a new valve cover overnighted to Elko?”
Al checked with the Sacramento service center and located a valve cover. It was too late to ship the part out that day, so Al arranged for it to be overnighted on Friday, together with a new gasket and locktabs.
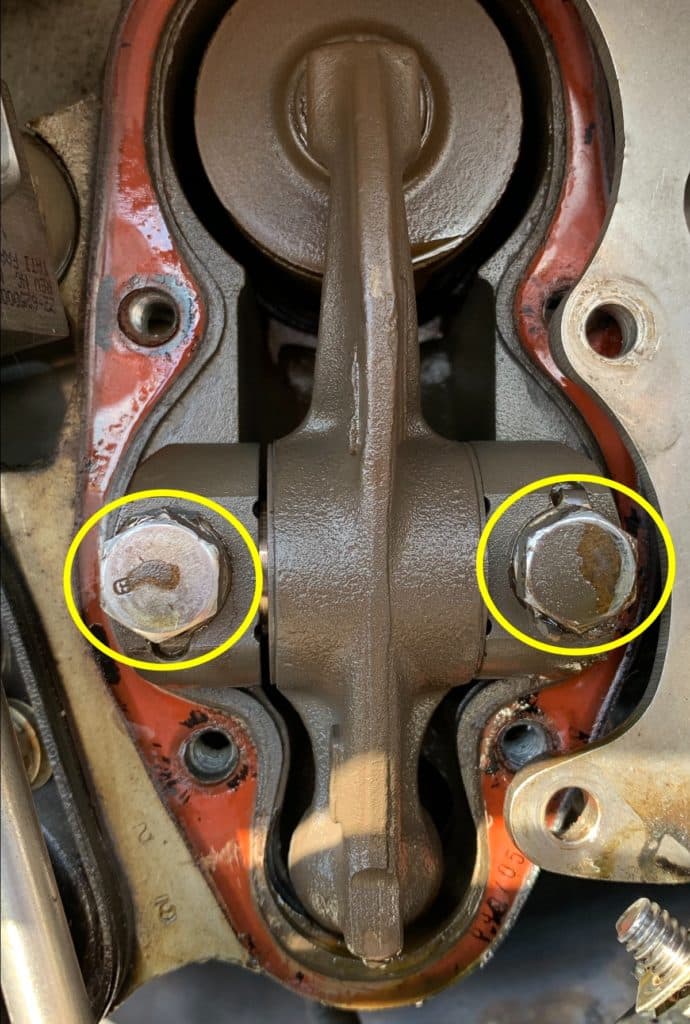
Surveying the Damage
Meantime, Jack had removed the damaged valve cover and verified that both bolts securing the rocker shaft had backed off despite the locktabs that were supposed to prevent this from happening. The rocker shaft was loose and the rocker assembly had been banging against the inside of the valve cover, gouging and cracking it to the point it was leaking oil.
Seeing how much metal had been gouged from the inside of the valve cover, Jack became concerned that his engine might be contaminated with metal. He voiced his concern to Tony, who assured him that there was nothing to worry about because any metal that managed to get out of the valve cover area and down the pushrod tube into the oil sump would have been caught by the suction screen or the oil filter and not contaminated the engine. Jack was relieved.
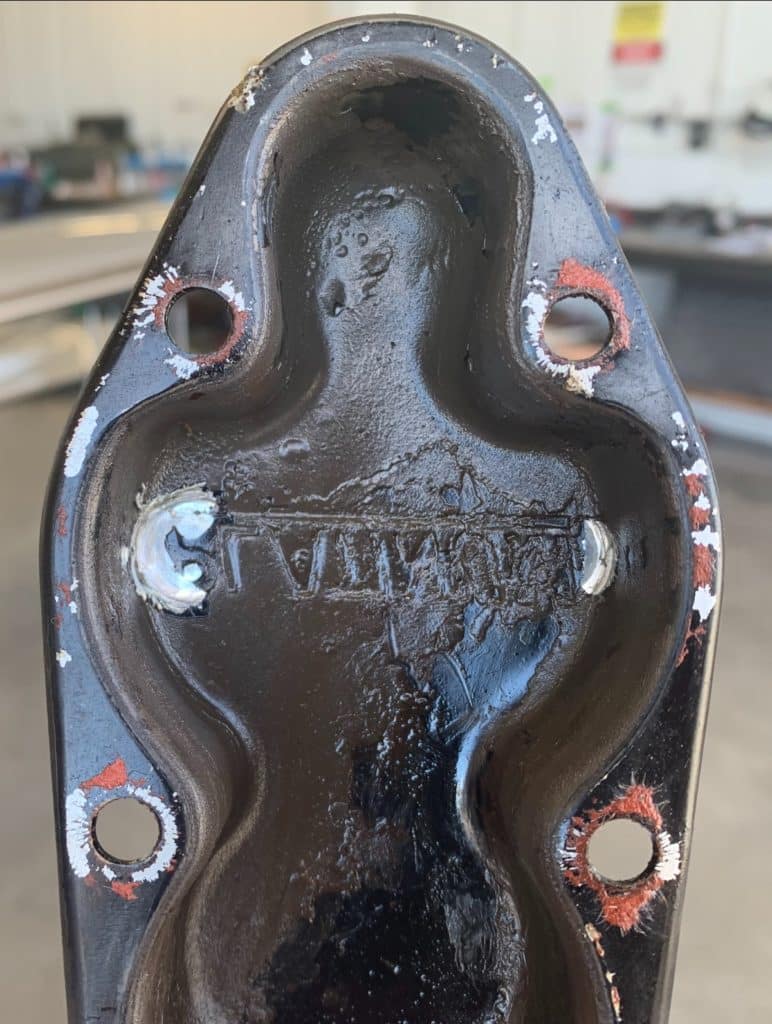
There’s no Saturday delivery to Elko, so the new valve cover, gasket and locktabs arrived on Monday morning. Meantime, the local A&P at Elko had removed the loose rocker bolts and found that they were badly stripped and stretched and unusable. So new bolts had to be overnighted in.
The new bolts arrived Tuesday morning, and the local A&P installed, torqued and safetied them, then installed the new valve cover and gasket. The engine compartment and oil-covered fuselage were washed with solvent, and the engine cowling was reinstalled. An extended runup and brief test flight revealed no further oil leaks. Jack was finally able to resume his trip after what turned into a six-day fuel stop in the middle of nowhere.“We’re back home and she flew great,” Jack reported to Tony and Al. “All temps were normal. We’re going to do an oil and filter change tomorrow. Thanks for the help.”
Jack’s call to our 24/7 Breakdown hotline and the assistance he received after-hours from Tony and Al wound up providing him with a pinpoint diagnosis by an expert set of eyes, saved him a couple of days of downtime, and relieved his concerns that his engine might have suffered serious internal damage.
It has been Savvy’s pleasure to take some worry out of flying during the past five months through our free Breakdown Assistance Service. We’ve helped many pilots during this difficult time with 24/7 troubleshooting by our experienced A&P/IA staff. Learn more about our Breakdown Assistance by clicking here.
You bought a plane to fly it, not stress over maintenance.
At Savvy Aviation, we believe you shouldn’t have to navigate the complexities of aircraft maintenance alone. And you definitely shouldn’t be surprised when your shop’s invoice arrives.
Savvy Aviation isn’t a maintenance shop – we empower you with the knowledge and expert consultation you need to be in control of your own maintenance events – so your shop takes directives (not gives them). Whatever your maintenance needs, Savvy has a perfect plan for you: