Would you know the symptoms of a broken valve spring in your engine data? We’re pretty good at spotting clogged injectors and fouled plugs from their distinctive patterns. We even developed our FEVA scan for detecting burned valves. Broken valve springs can be, like the song says — as restless as a willow in a windstorm, as jumpy as a puppet on a string. Sometimes the decision tree is more like a forest as you work through the possibilities and rule things out.
A broken valve spring is rare enough that it’s usually not the first thing we suspect. Or even the fifth thing. But they’re out there and the more of them we see the better we’ll get in spotting the data patterns for them. It’s not much of a puzzle if you get the answer ahead of time, so without telling you which one, we’ll tell you that one of this month’s cases was a broken valve spring.
We’ll start with data from a Cirrus SR20 with a Continental IO-360 and data from a Garmin Perspective with a 1 sec sample rate. The concern was “severe surges in the takeoff roll” so since CHTs are normal and aren’t really useful here, the display is EGTs, RPMs and FF. Here’s the whole 28 min sequence from startup to rejected takeoff and shutdown. Cursor is off to the left to get it out of the way.
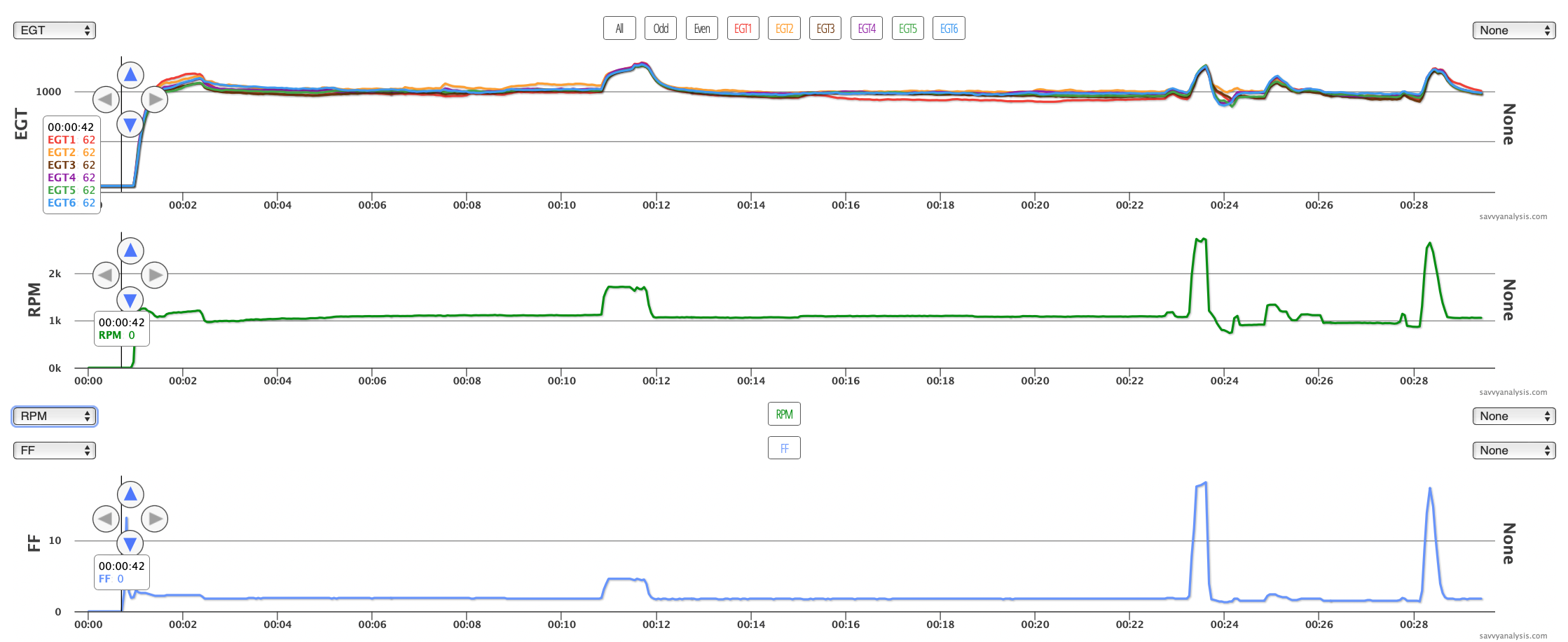
The event happens around the 23 min mark so let’s zoom in on that. I’ll bet that many of you upon seeing the word “surge” went right to oil temp in the prop hub. If you’ve ever forgotten to cycle the prop, or cycled it meagerly so that warm oil didn’t get into the hub, you may have surged in the takeoff roll and gone “oh, I forgot to cycle the prop” – or words to that effect. I may or may not have done this once or twice in almost 40 years of flying, and was reminded of the importance of checklists. I’ll bet I’m not alone. Anyway, here’s the same data zoomed into the 23 min mark and with a 4th rank added to display oil temp. Cursor is off to the right.
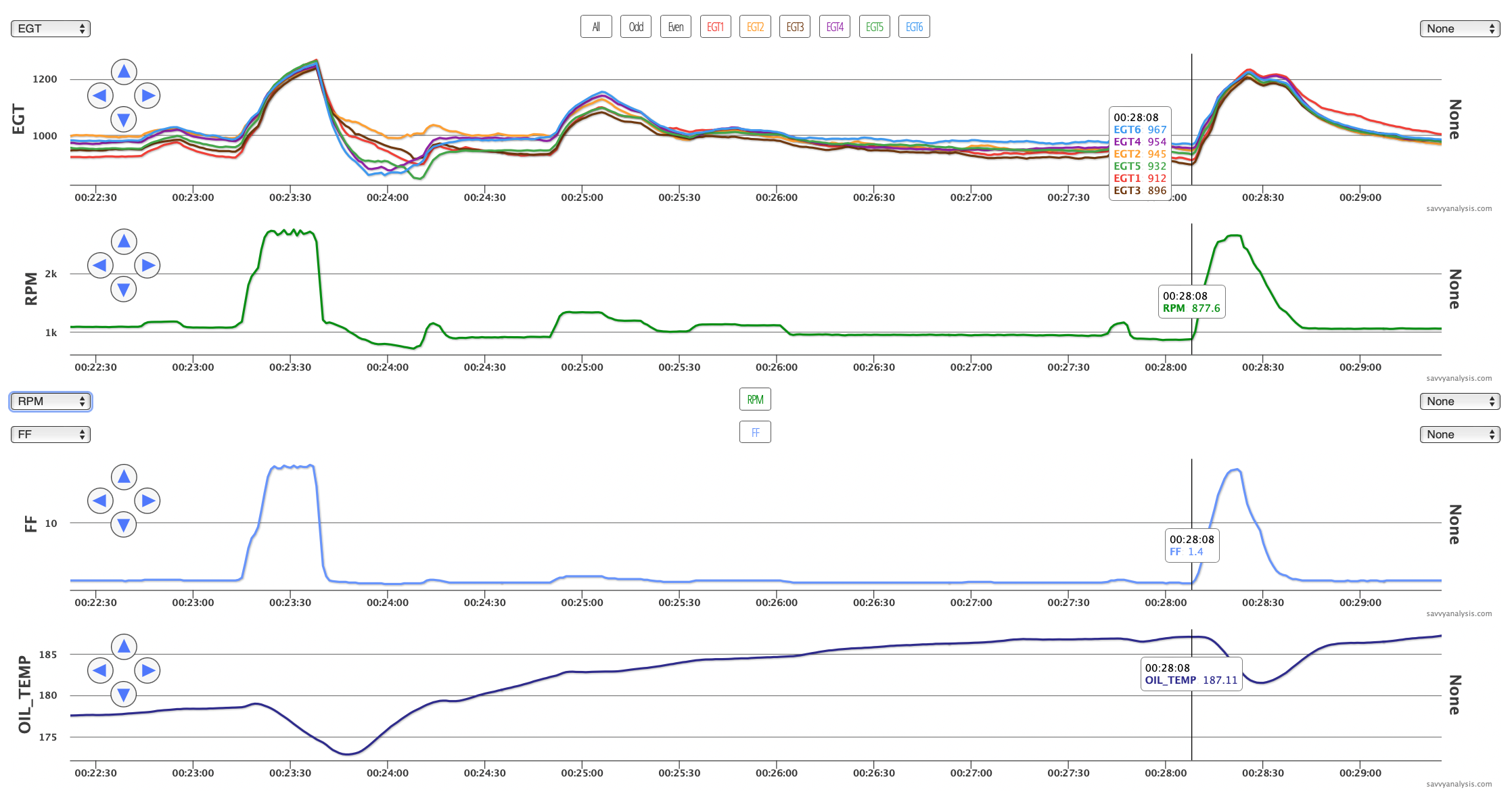
For those thinking that the oil temp must have been really low, it’s almost 180º at takeoff. The engine has been idling for 23 mins. The SR20 POH says “in most cases, oil is considered warmed up at 100º F.” But – the warm oil circulating through the case hasn’t necessarily made it to the prop hub. The SR20 doesn’t have a separate prop control and the runup checklist to 1700 RPMs covers the electrical system and mags, but nothing about the prop before bringing power back to idle.
Fortunately the takeoff data gives us a pretty good record of events. Power is applied, the warmer oil from the case mixed with the cool oil in the prop hub, the prop surges – those short cycles are about 80 RPMs from peak to trough – FF is also effected through the engine-driven pump, and the takeoff is aborted. Notice the big drop in oil temp as the cold oil from the hub blends with the case oil.
EGTs get messy after the power chop, but we don’t think a spark problem caused the surging. EGTs get messy because there’s not a lot of unburned fuel sloshing around. It evens out in less than half a minute. If you’re wondering what oil pressure did during this event, good question. Here’s the same zoomed-in data with oil pressure and RPMs.
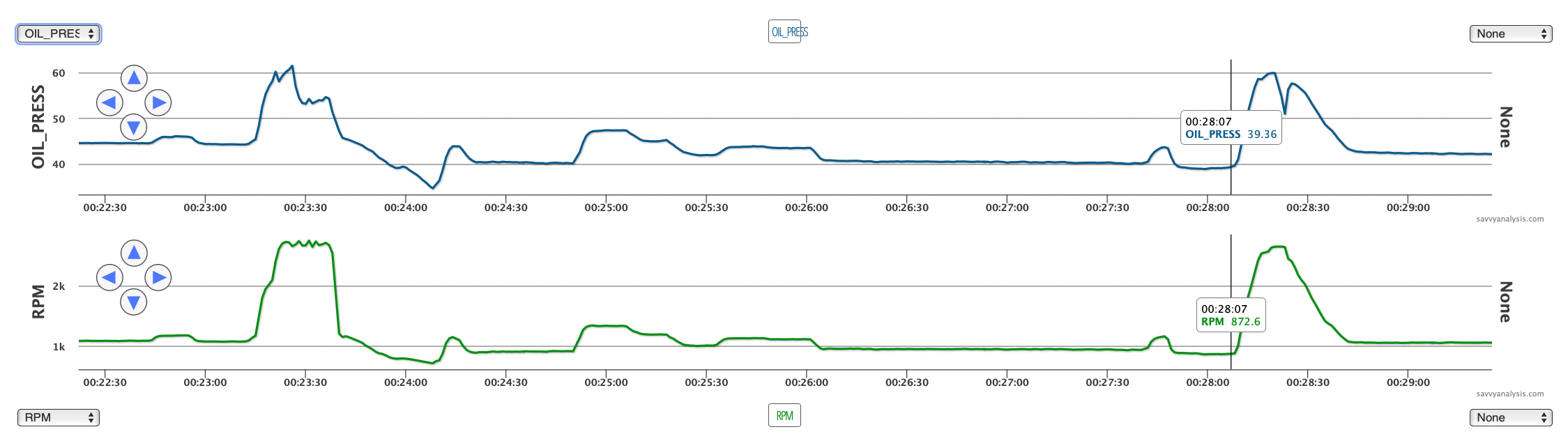
The POH says “discontinue takeoff at any sign of rough operation or sluggish acceleration. Make a thorough full-throttle static runup before attempting another takeoff.” So it looks like the pilot got off the runway, found a safe spot, read the book and performed the static runup around the 28 min mark.
The epilog to this one is that this was the first flight after a three-month COVID lockdown. The shop had been performing runups three times a week through that time but apparently that wasn’t quite enough to get the cold-soaked oil out of the hub. No issues since this event.
That last one wasn’t the valve spring, so maybe it’s this one. Here’s data from a Socata TB-20 with a Lycoming IO-540 engine and data from a JPI 700 with a 6 sec sample rate. EGTs, CHTs and FF.
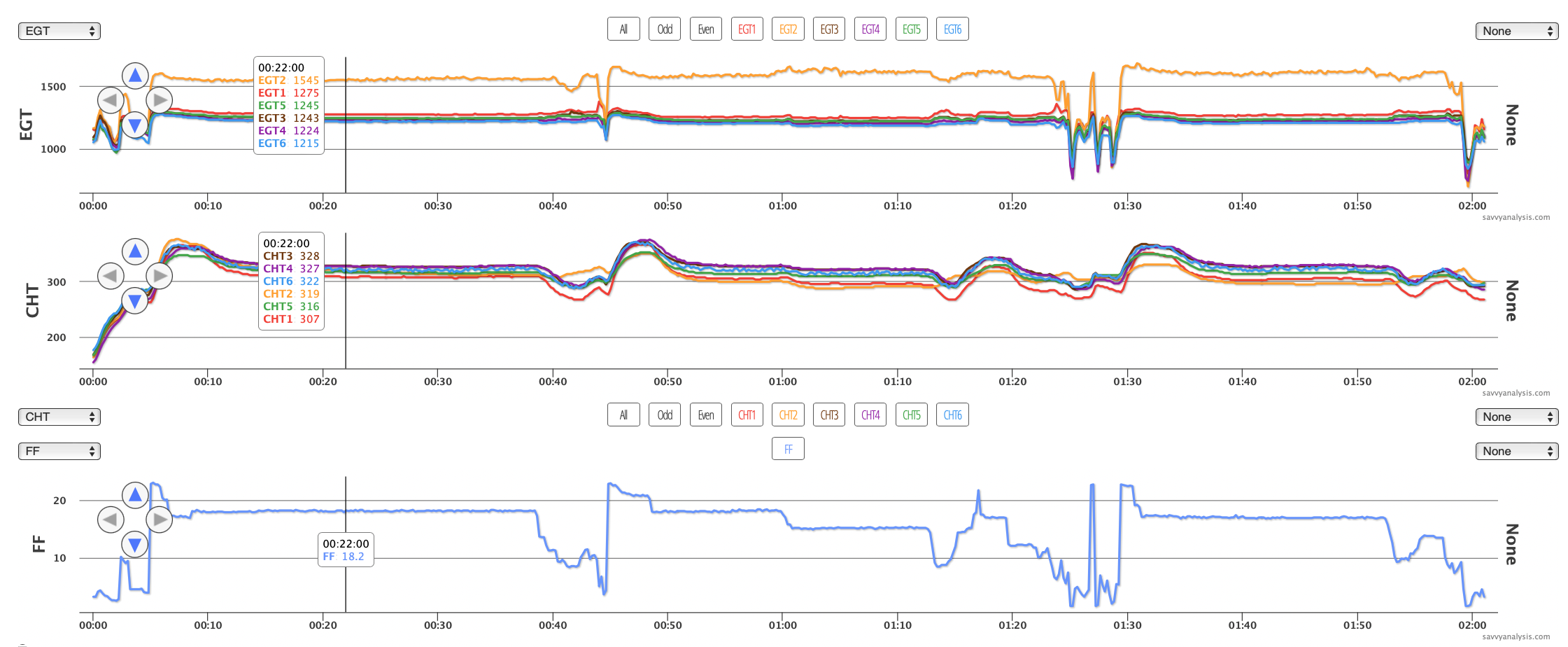
EGT 2 is high, but CHT 2 isn’t. At the cursor, it’s 4th in rank. Later in the flight it’s either lowest or next-to. With an injector clog, we expect to see EGT & CHT moving together. Both should be high at max FF and then both should move lower as FF is reduced – that’s not happening here. In fact, EGT drops and CHT rises when FF gets under about 10 GPH. It’s most normal at idle. Just as we’re formulating our theory, we got this data from the subsequent flight.
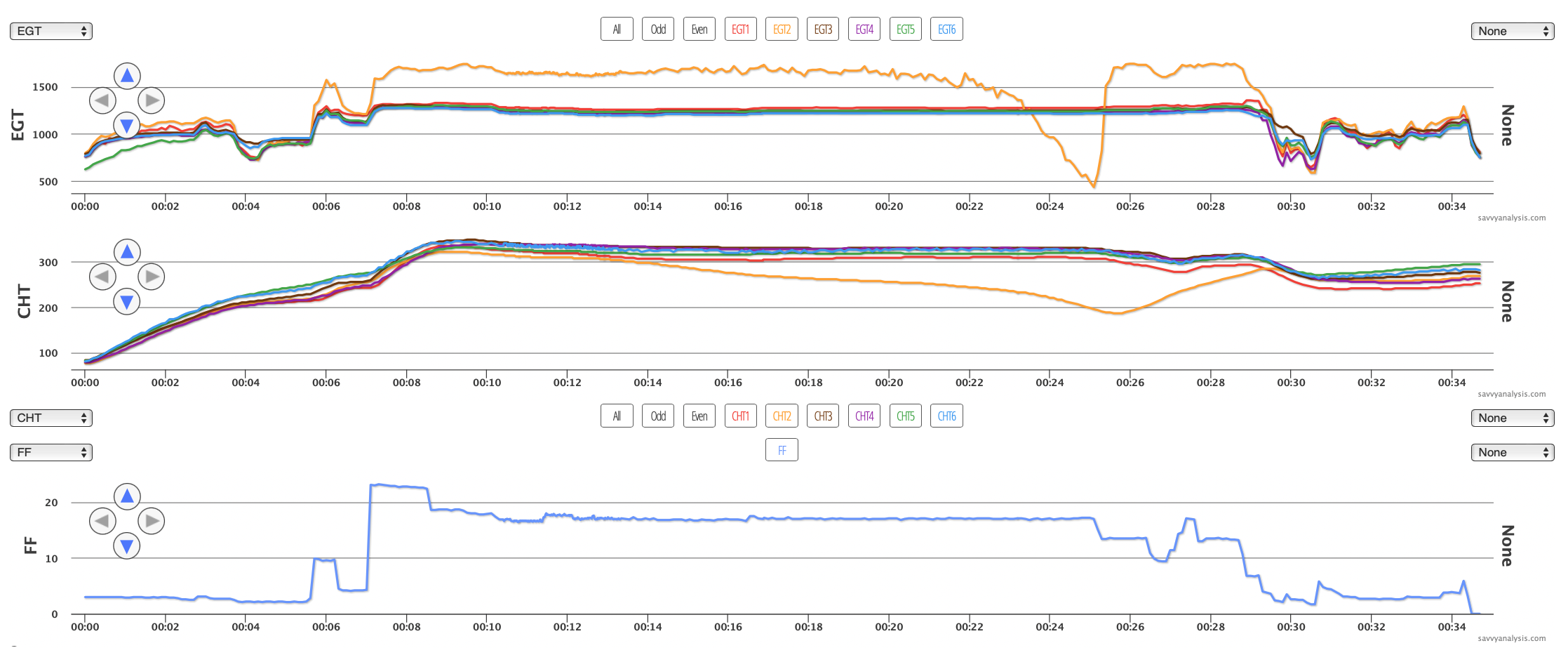
Now CHT is dropping on its own, while EGT stays high. But they’re moving together more than last flight. What hasn’t changed is the cylinder output seems most normal when FF is 10 GPH or less. That’s also when the pilot deployed the fuel pump, which complicates the issue. We hate to recommend unnecessary maintenance, and we want to feel confident that what we recommend will correct the problem, and with this one we weren’t quite there yet. On his own, the client decided to have the shop clean all the injectors and purge the fuel lines. We don’t know which of those fixed it, but one of them did. Cyl 2 was normal after that maintenance. So that wasn’t the valve spring either.
Next up is data from an RV 7 with a Lycoming IO-360 engine and data from a Dynon Skyview with a 1 sec sample rate. The concern was EGTs 1 and 2 dropping intermittently during some flights. No reported roughness, no corroborating change in CHTs, FF, RPMs or any other parameter, including the electrical system. No malfunctions – the client just happened to notice them while reviewing data and asked us to take a look. Here are three instances – EGTs only for each one.



Each time 1 and 2 drop, 3 and 4 are steady. So it didn’t look like a mag problem. No roughness so didn’t seem like a fuel problem. It’s almost like something was going on and off. We barely had time to digest the facts and start probing the possibilities when the client remembered these were the flights where he was testing his new smoke system. And guess which two cylinders the smoke system diverts exhaust gas from. Yep. He was very apologetic but no need for that – we wish they were all that easy. No valve spring here, either.
That must mean that this one is the valve spring. This is data from a Lancair Legacy with a Continental TSIO-550 and data from a Garmin G3X with a 1 sec sample rate. EGTs, CHTs and FF.
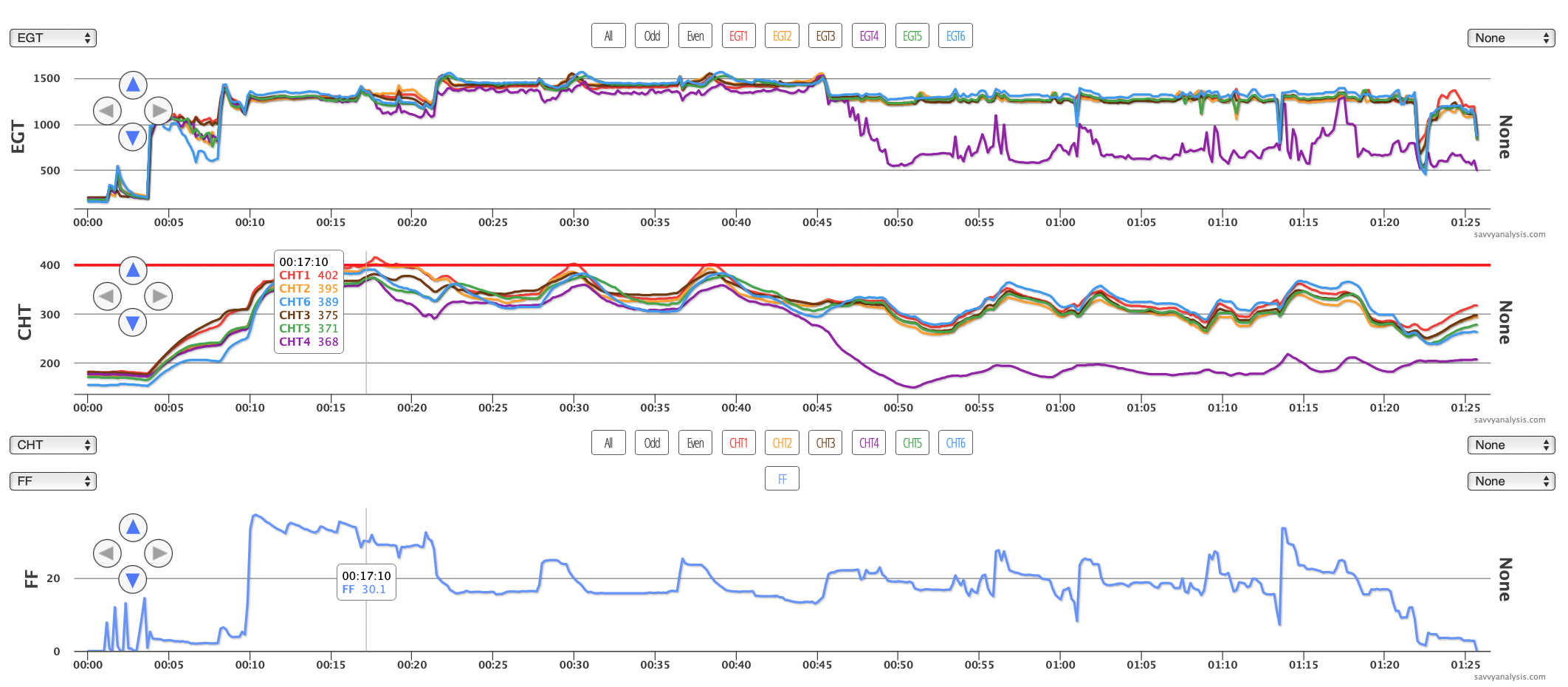
Now that you know what happens and when, let’s look at the same flight and change EGT, CHT and FF to EGT, MAP and Altitude.
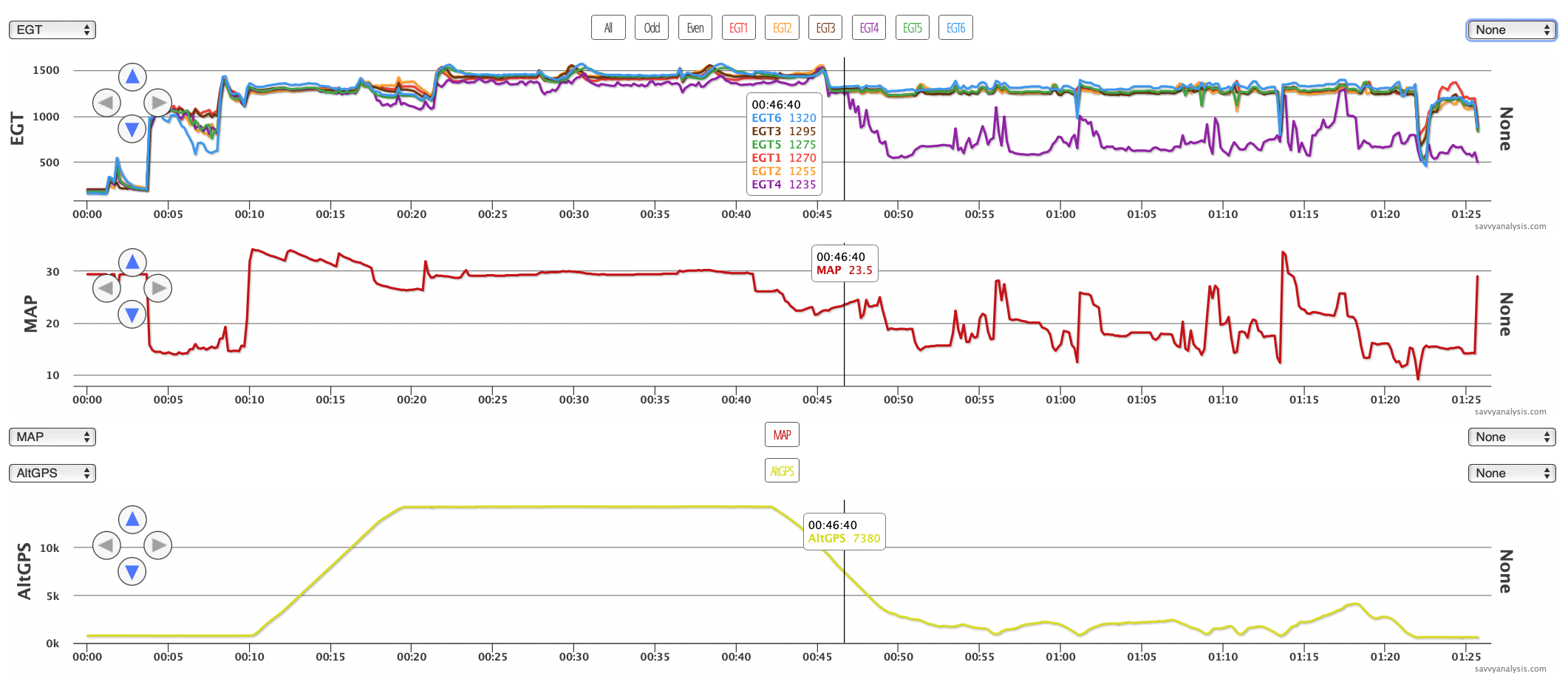
And here’s the guilty party…
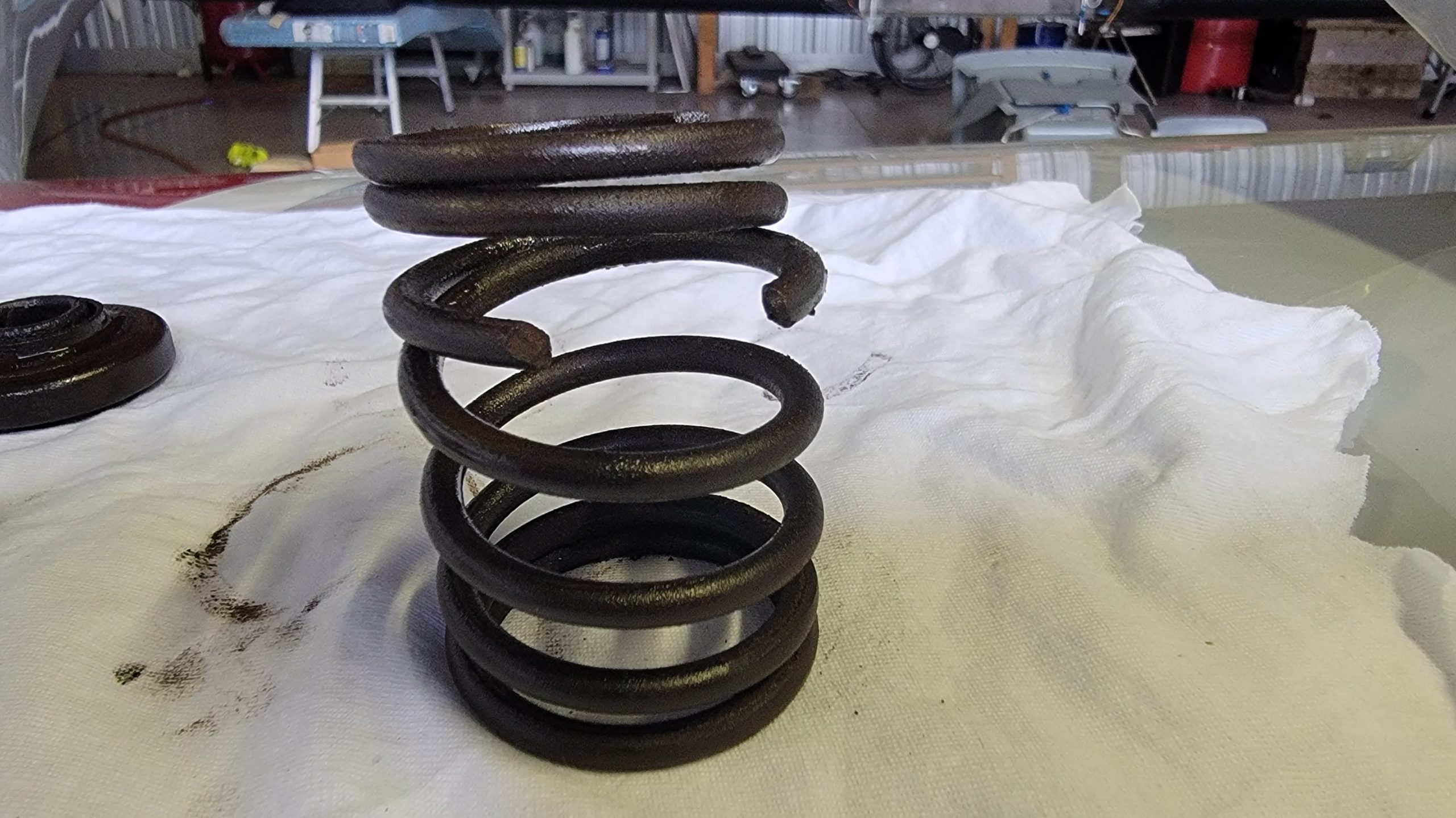
So if you were thinking the spring had sprung as a result of a big power increase – no. It’s a modest power increase during a decent from 14,000 to the 1,000 msl range. The pilot does some go-arounds and EGT 4 sort of gets back into the picture on each go-around power application. Then it drops again when power is reduced. Rounding up the usual suspects — fuel flow, spark, induction — doesn’t seem to provide an answer.
Zeroing on on 45-50 mins, you almost think maybe the valve has munched, except it sort of comes back under power – which a munched valve wouldn’t do.
In previous cases where a broken valve spring turned out to be the culprit, we saw EGT data more like the 20-45 min range. Jumpy, and not quite right. And before that, during takeoff and climb, EGT 4 is right in there with the others.
So can we count on that as a symptom for a valve spring problem – ok at higher power and more likely to show up at lower power settings? We’ll have to see more instances to be able to count on it, but for now it’s a good start.