Rigid baffles and flexible baffle seals are critical in keeping your engine cool.
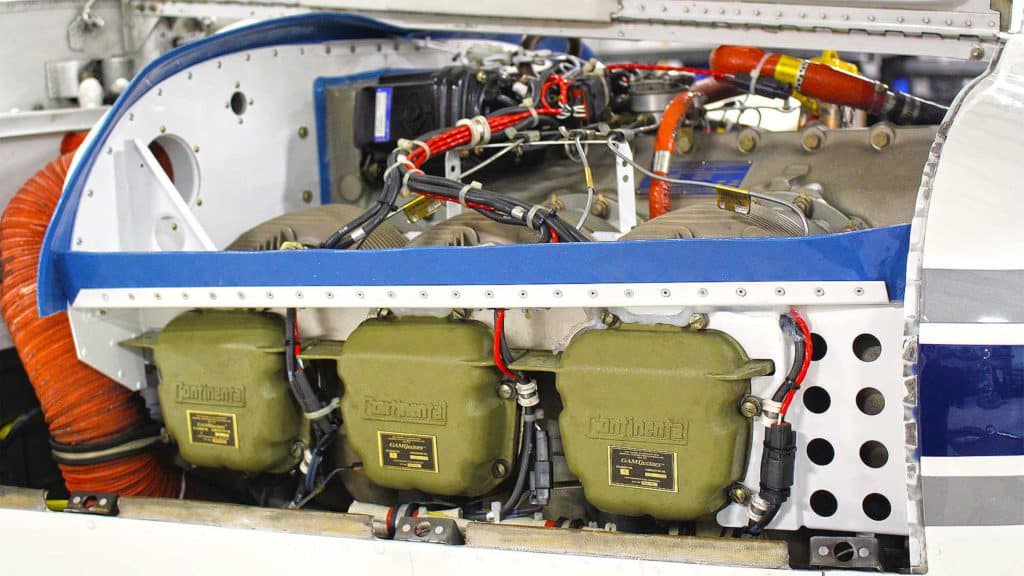
The Cessna T210 owner was clearly frustrated with his new engine installation:
“I recently had my engine rebuilt and had a new baffle kit installed. The CHTs for cylinders #5 and #6 are always 20ºF to 30ºF hotter than the rest. During climb the difference gets even bigger. Cylinder #5 and #6 CHTs are very difficult to keep below 400ºF during a climb, even with the cowl flaps open and full-rich mixture. Should I consider giving them some air? On cylinder #6, why not cut one or more holes in the white aluminum baffle in front of the cylinder? On cylinder #5, why not drill one or more holes in the horizontal aluminum plate located behind the oil cooler?”
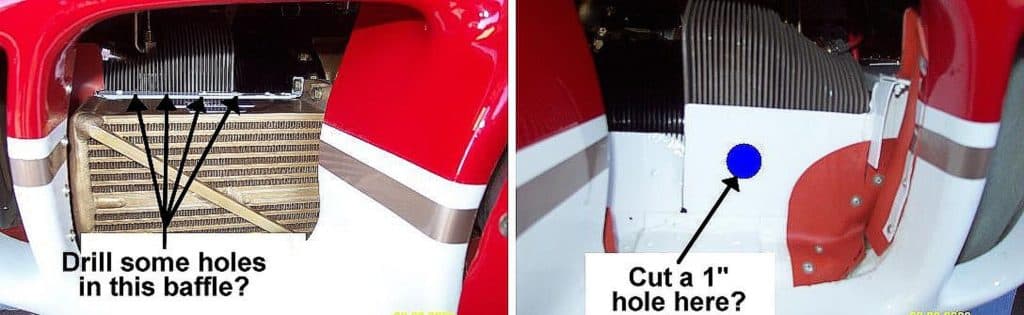
After looking at the marked-up photo from the T210 owner, I replied that cutting holes in the baffles was definitely NOT a good idea, and that doing so would undoubtedly make the cooling problems worse, not better. It was apparent that this owner didn’t understand how the powerplant cooling system in his aircraft works, or what the function of the baffles is. He’s not alone—some A&P mechanics don’t fully understand it, either!
Cooling: Then and Now
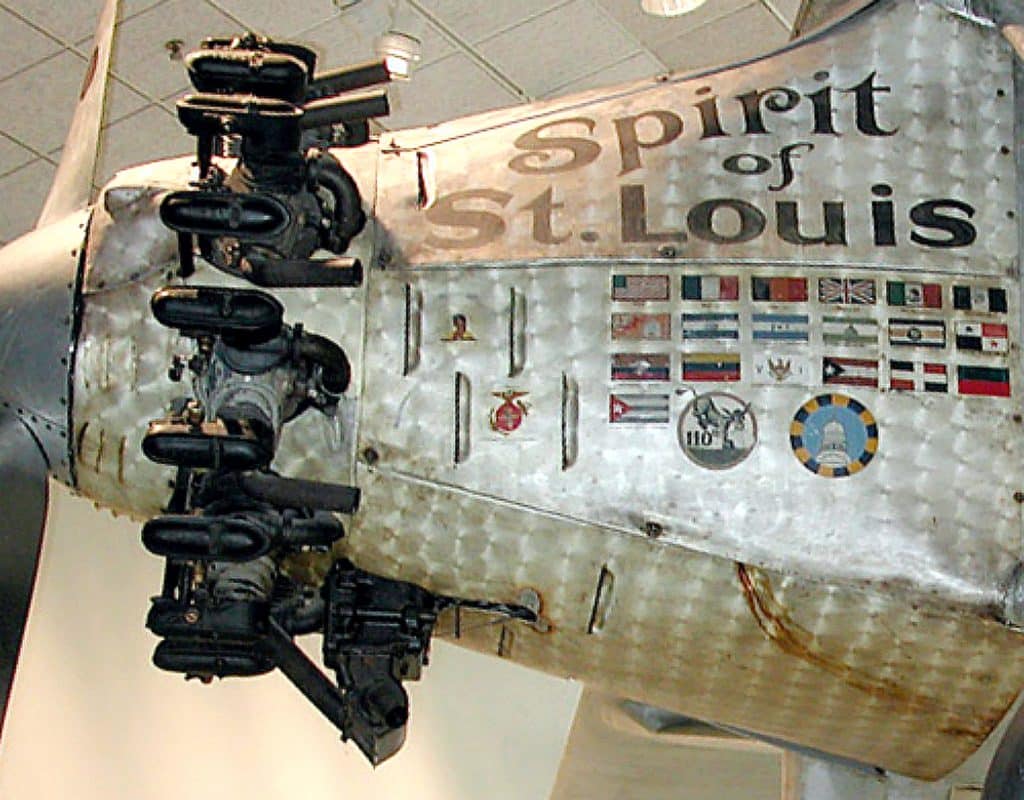
In the early days of aviation, aircraft designers took a simple approach to the problem of cooling aircraft engines. The engines were mounted with their finned cylinders out in the slipstream and cooled by the horizontal flow of ram air. This design is known as “velocity cooling” and was adequate for cooling the low-compression single-row radial engines of the time.
As engines grew more powerful and multi-row radials and horizontally opposed engines came into fashion, it became obvious that simple velocity cooling wasn’t up to the job. For one thing, cooling was uneven—front cylinders got a lot more cooling airflow than rear ones. For another, sticking all those cylinders out in the breeze created horrendous cooling drag. A better scheme was obviously needed.
That better system was known as “pressure cooling” and is the method used in all modern piston aircraft. Pressure cooling is accomplished by placing a cowling around the engine and using a system of rigid baffles and flexible baffle seals to produce the volume and pattern of cooling airflow necessary to achieve even cooling with minimum drag.
What do baffles do?
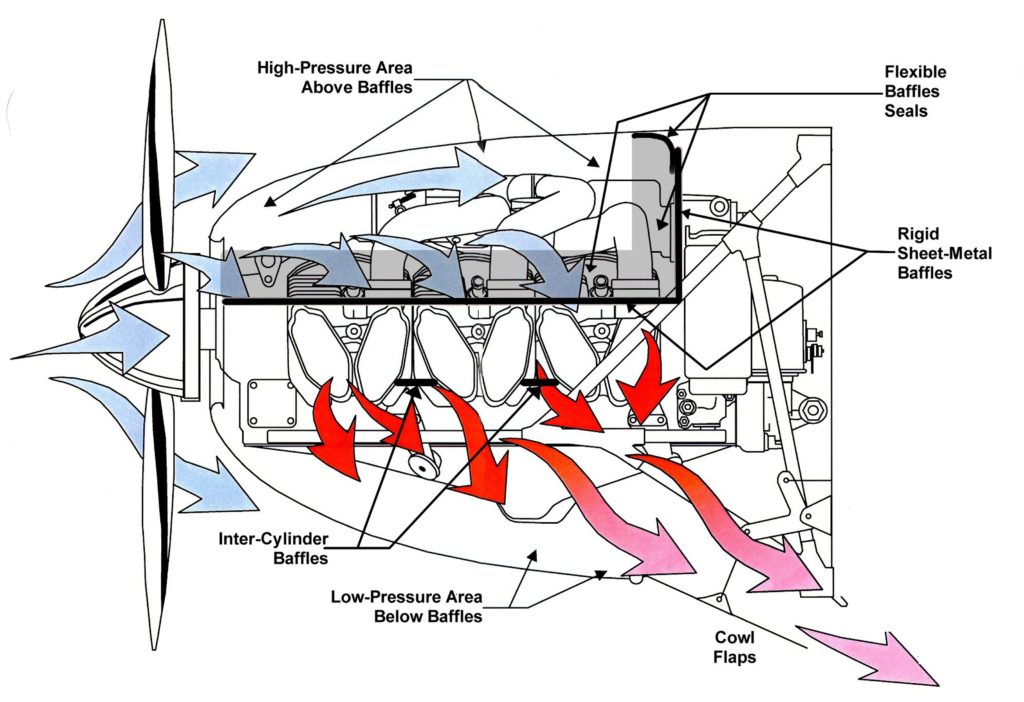
The volume of cooling airflow that passes across the cylinders is a function of the pressure differential between the upper (high-pressure) chamber and the lower (low-pressure) chamber of the engine compartment. This pressure differential is known as “delta-P.” Cowl flaps are often used to modulate the cooling airflow. Opening the cowl flaps reduces the air pressure in the lower chamber, thereby increasing delta-P and consequently the volume of cooling air that passes vertically across the cylinder fins.
It’s important to understand that the pressure differential between the upper and lower chambers is remarkably small: A typical high-performance piston aircraft generally relies on a delta-P of just 6 or 7 inches of water—about 1/4 PSI! Aircraft designers try to keep this delta-P to an absolute minimum, because higher delta-P means higher cooling drag.
…and so what if they don’t?
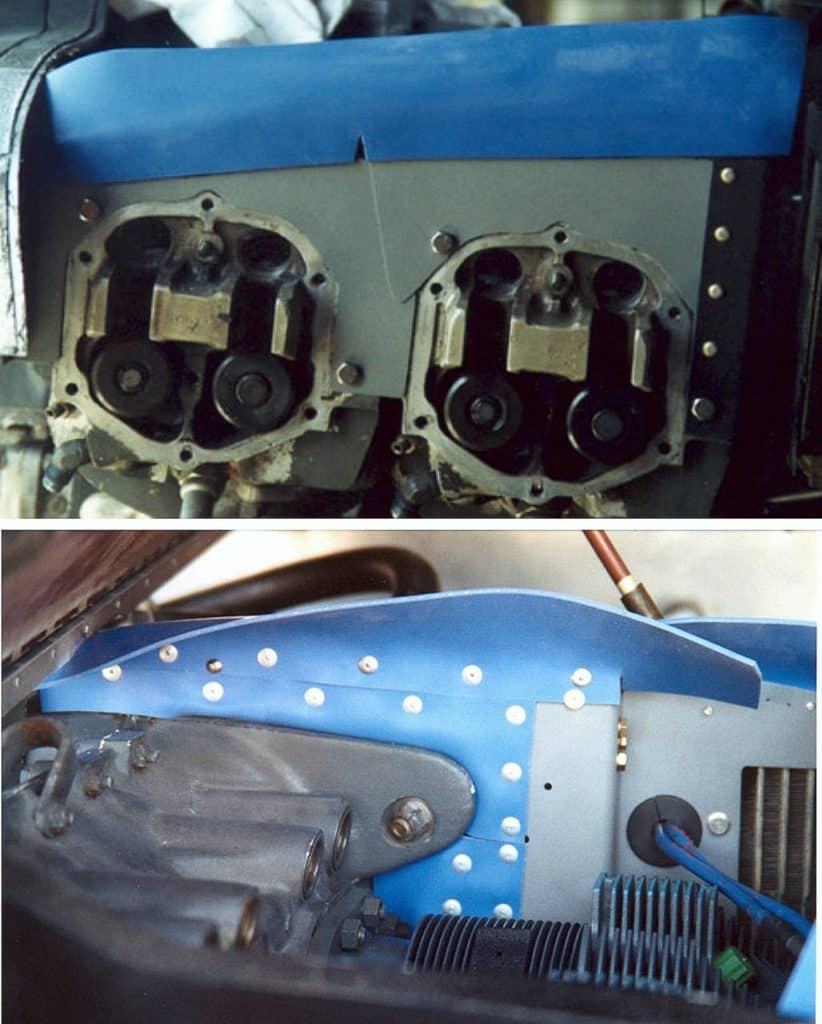
Because delta-P is so tiny, even small leaks in the system of baffles and seals can have a serious adverse impact on cylinder cooling. Any missing, broken, or improperly positioned baffles or seals will degrade engine cooling by providing an alternative path for air to pass from the upper chamber to the lower chamber without flowing across the cylinder cooling fins. (That’s what would have happened if the T210 owner had cut holes in his baffles.)
One of the most problematic parts of the cooling system is the system of flexible baffle seals. These strips—usually made of high-temp silicone rubber—are used to seal up the gaps between the sheet metal baffles and the cowling. These gaps are necessary because the baffles move around inside the cowling as the engine rocks on its shock mounts.
To do their job, the seals must curve up and forward into the high-pressure chamber, so that the delta-P presses the seals tightly against the cowling. If the seals are permitted to curve away from the high-pressure area—not hard to do when reinstalling the cowling if you’re not careful—they will blow away from the cowling in-flight and permit large amounts of precious cooling air to escape.
I recall some years ago inspecting a Cessna TR182 whose pilots had complained of high CHTs. Upon removing the top engine cowling, I immediately spotted the problem: One of the ignition leads was misrouted and became trapped between the baffle seal and the cowling, preventing the baffle seal from sealing against the cowling. The ignition lead had become severely chafed where it rubbed against the cowling, and an A&P had wrapped the chafed area with electrical tape, but failed to reroute the tape-wrapped lead to keep it away from the baffle seal. Clearly that A&P didn’t understand the importance of an air-tight seal between the baffle seals and the cowling. Repositioning the ignition lead solved both the cooling problem and the chafing problem.
Another common problem is that seals may develop wrinkles or creases when the cowling is installed, preventing them from sealing airtight against the cowling and allowing air to escape. It’s important to look carefully for such problems each time the cowling is removed and replaced, and especially important when new seals have been installed (as was the case with the T210).
Intercylinder Baffles
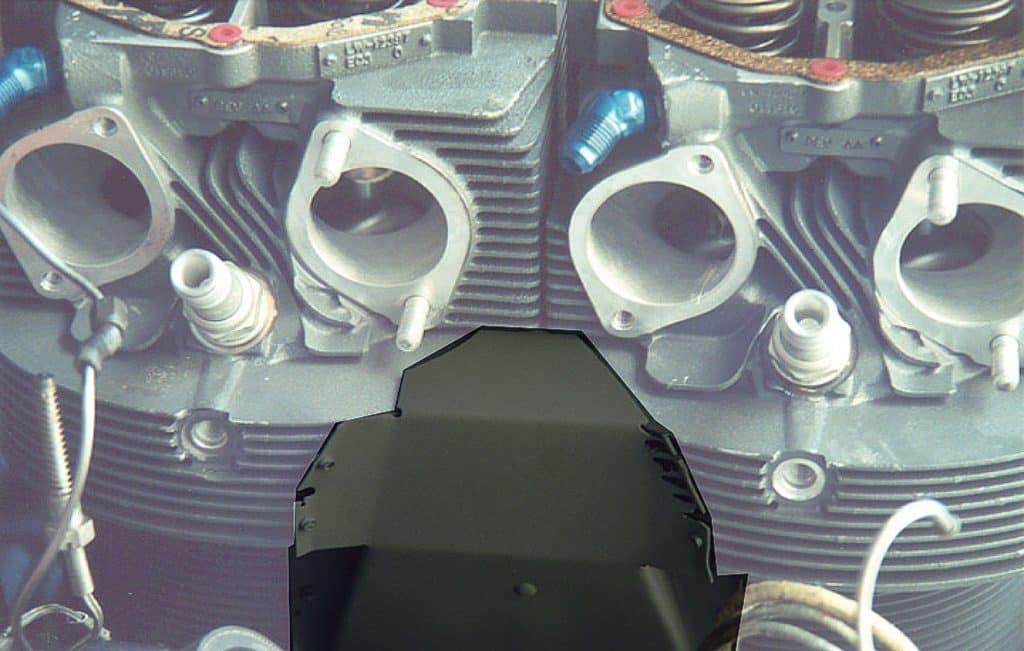
Yet another common cooling system problem involves the intercylinder baffles. These small, oddly-shaped pieces of sheet metal are mounted below and between the cylinders. Their purpose is to prevent cooling air from passing through the spaces between adjacent cylinders, and to force the down-flowing cooling air to wrap around and cool the bottom of the cylinders, rather than just cooling the top and sides. These baffles are absolutely critical for proper cooling, but they’re difficult to see unless you know exactly where to look for them. During engine installation or cylinder replacement, it’s not at all uncommon for them to be left out or mispositioned, and it’s not unheard of for them to vibrate loose and fall out during engine operation. Hot-running cylinders are the inevitable result.
Awhile back, I noticed that the #3 cylinder of the right engine on my Cessna 310 was running noticeably hotter than its neighbors. I removed the top cowling from the right engine nacelle and carefully inspected all the aluminum baffles and rubber baffle seals, but couldn’t find anything awry. Frustrated, I removed the lower cowlings so that I could inspect the underside of the engine. Sure enough, I discovered that the intercylinder baffle between cylinders #1 and #3 had vibrated loose and shifted about 1/4 inch away from the crankcase, creating a significant air leak near the #3 cylinder. Repositioning the baffle properly and tightening its attach bolt to hold it securely in place against the cylinders and crankcase solved the problem.
Subsequently, I discovered a neat trick to make it easier to locate such problems. Just this week, I worked with three different Skylane owners who were complaining that one of their rearmost cylinders (#1 or #2) was running hot. In each case, the owners had spent months and hundreds of dollars in shop labor trying to correct the problem to no avail. I advised each of these owners to place a bright shop light in the lower cowling beneath the engine, remove the top cowling, then stand on a ladder and look straight down on the cylinders from above. If they could see light coming up from the bottom of the engine, then they had a missing or improperly placed intercylinder baffle and downward-flowing cooling air could take the same path that the upward-flowing light was taking. In in each case, this quickly located the problem, which was then quickly and easily corrected and which cured the high CHTs.
Why The T210 Engine Ran Hot
Returning to our frustrated T210 owner, I discouraged him from cutting holes in his baffles, and suggested instead that he examine his baffles and seals for gaps that could be plugged to improve cooling. At my request, the owner emailed me a series of high-resolution photos of his newly installed baffle kit.
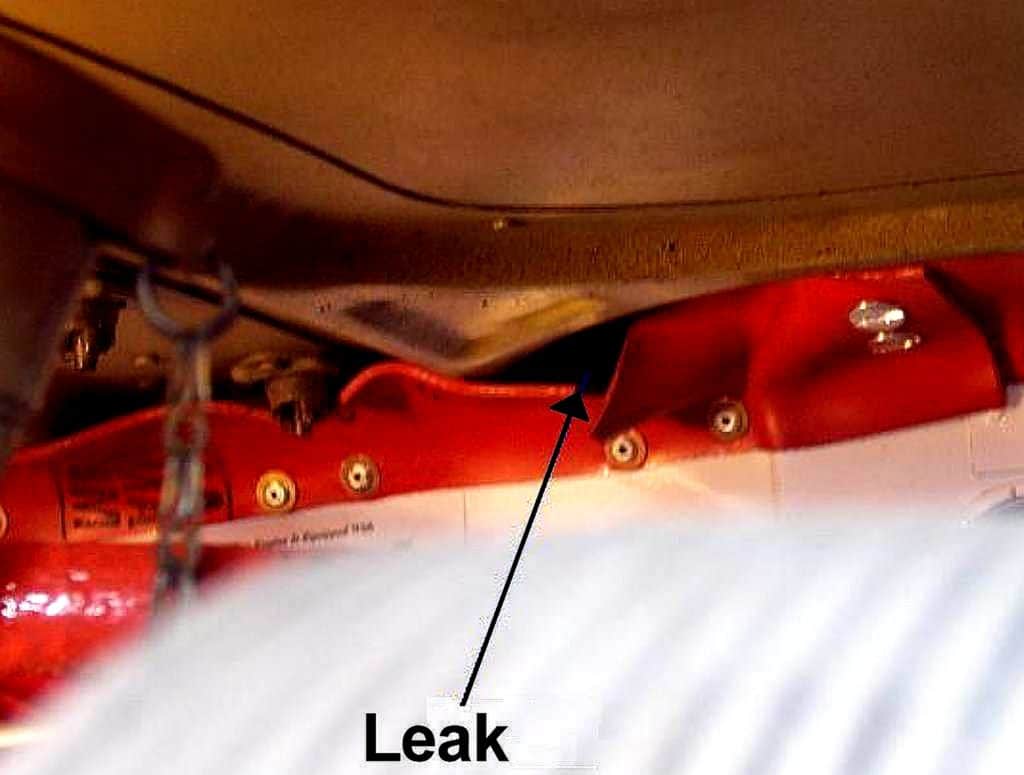
One of those photos revealed a rather significant cooling air leak due to a wrinkle in a flexible baffle seal. This problem was apparent only with the top cowl installed, and could be seen by inspecting through the front intake openings using a flashlight. Savvy pilots who understand the importance of baffles and seals look for this sort of thing during pre-flight inspection. Since mechanics do most of their inspecting with the cowlings removed, problems like this sometimes escape their detection.
I studied the photos and continued my email dialog with the T210 owner. Between the two of us, we managed to identify a dozen leaks in the T210’s baffle system. Some were small, others more serious. Combined, they accounted for a significant loss of cooling efficiency. With a little trimming of the flexible seal strips plus a few well-placed dabs of high-temp RTV sealant, the owner succeeded in plugging the leaks in short order, and reported that his engine was running noticeably cooler.
You bought a plane to fly it, not stress over maintenance.
At Savvy Aviation, we believe you shouldn’t have to navigate the complexities of aircraft maintenance alone. And you definitely shouldn’t be surprised when your shop’s invoice arrives.
Savvy Aviation isn’t a maintenance shop – we empower you with the knowledge and expert consultation you need to be in control of your own maintenance events – so your shop takes directives (not gives them). Whatever your maintenance needs, Savvy has a perfect plan for you: