How we coax metal aircraft parts into doing what must be done
Metal is neat stuff. It’s strong, hard, and tough. It’s easy to form, work, shape and machine. It’s fireproof and can stand up to high temperatures. But these properties aren’t unique to metal.
Ordinary cotton fiber actually has higher tensile strength than the aluminum alloys we use to build airplanes, and Kevlar is stronger than even high-tensile strength steel. Diamond and carbides (artificial diamonds) are harder than the hardest metals. Ceramics can withstand heat that would cause metal to melt. Wood is easy to shape and machine, and aviation-grade Sitka spruce is nearly as strong as aluminum alloy, at least if the stress is applied with the grain
What makes metal so useful is that it exhibits all of these properties. You might say that metal is the Cessna Skylane or Piper Dakota of aircraft construction materials—it may not be the best at any particular thing, but it sure does a lot of things well.
Stress/strain, elastic/plastic
What primarily sets metal apart from other materials is how it deforms when a force is applied to it. Metallurgists call the applied force “stress” and the deformation it causes “strain.” Here’s a typical stress-strain diagram for metal:
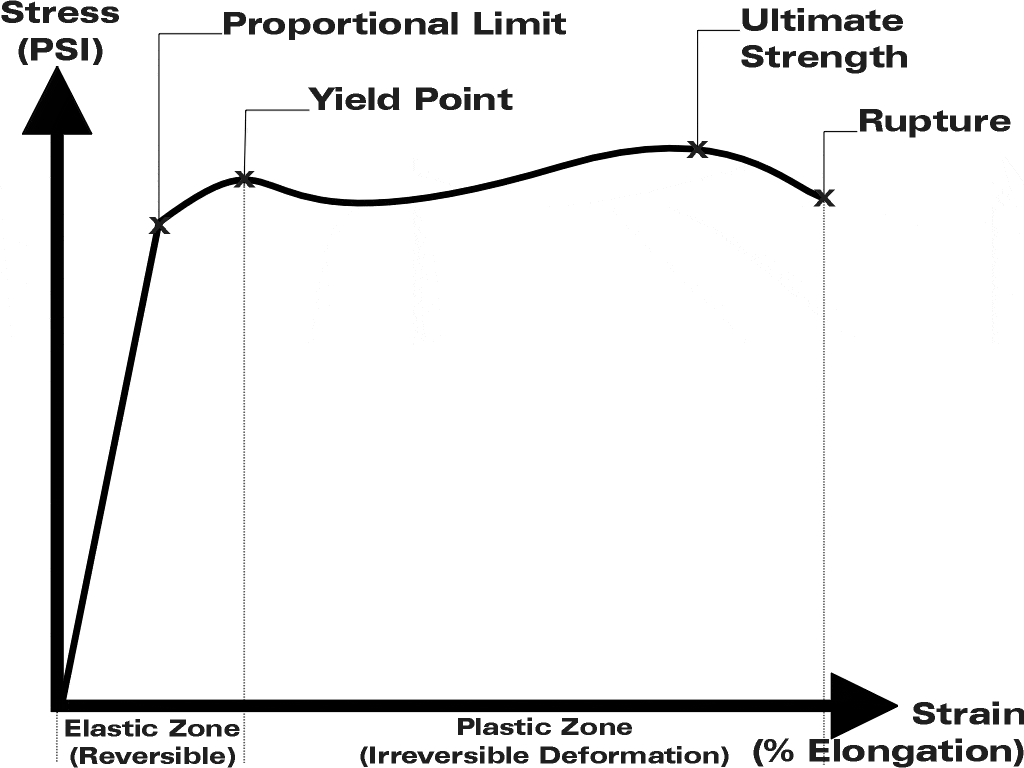
If a modest amount of stress is applied to a metal object, it deforms “elastically”—the object returns to its original shape and size when the stress is removed. This is obvious in the spring steel landing gear leg of a Cessna or the aluminum wing spar of a Boeing, but it’s also true of metal parts like bolts and crankshafts where the deformation is not so obvious.
During elastic deformation, strain is proportional to stress (Hooke’s Law), so the stress-strain curve is a straight line. But if the stress is great enough, the crystalline structure of the metal starts to rip apart, and non-linear things start to happen. This level of stress is called the “elastic limit” or “proportional limit” of the metal.
Stress beyond the metal’s elastic limit causes “plastic” deformation—the deformation is permanent even after the stress is removed. This might sound bad, but it’s one of metal’s most endearing features. Metal’s plastic properties are what allow us to bend, stamp, forge, extrude, roll, and otherwise coerce metal into complex shapes. In service, those same plastic properties are what permit an overloaded metal part to bend rather than break, a characteristic known as “toughness.”
Metal’s ability to be elastic under moderate stress and plastic under high stress is what makes it so useful. Nonmetallic materials tend to have very different stress-strain curves. Hard, brittle materials like brick, concrete and glass react to stress by shattering rather than deforming. Tough materials like rubber, leather and softwood remain elastic all the way to rupture, and can’t be cold-worked into a desired shape the way metal can.
Soft, hard, and tough
The simplest elemental metals like iron and aluminum and copper are relatively soft and ductile. Their elastic limit is relatively low so it doesn’t take much force to deform them permanently. Where higher strength is required, the elemental metal is usually alloyed by adding a relatively small amount of one or more additional elements that strengthen the metal.
It doesn’t take much. Adding just a few percent (by weight) of carbon turns soft iron into high-carbon steel with ten times the tensile strength. Adding about 4% copper to commercially pure aluminum creates 2024 aluminum alloy (the most common one used in aircraft) that’s more than four times as strong. These alloying elements work their magic by invading the crystalline structure of the metal in a way that makes the resulting lattice of atoms much denser and harder to dislodge. Here’s what happens to the stress-strain curve of iron when a bit of carbon is added to form steel:
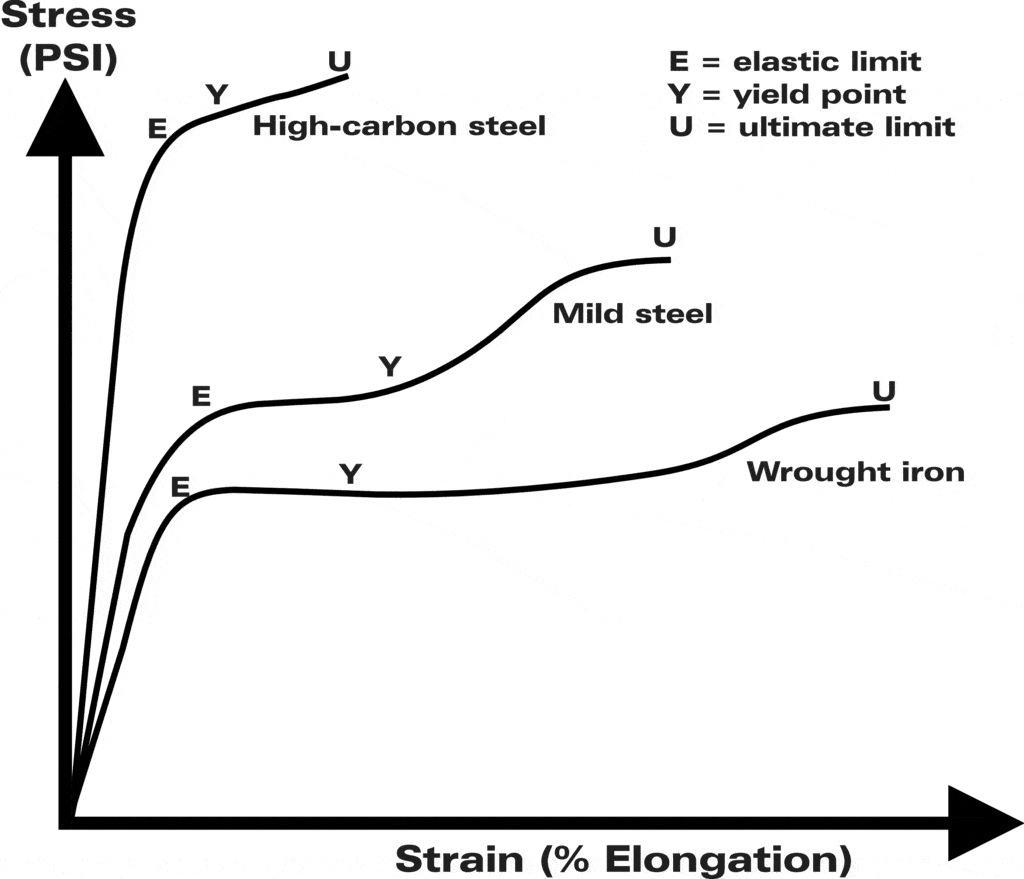
Notice how the linear portion of the curve gets much steeper, indicating that steel is much harder than iron—it can handle much greater stress without permanent deformation, and a given amount of stress causes far less strain.
But also notice that as more carbon is added to create high-carbon steel, the well-defined “knee” at the yield point that is seen in iron and mild steel tends to disappear. What this means is that high-carbon steel is more prone to sudden failure without warning—it’s more brittle and can’t bend much before it breaks.
In some applications—such as cylinder barrels, crankshaft journals, cam lobes and tappets—hardness is all-important for maximum service life. In other cases—wing spars and landing gear legs, for example—toughness (the ability to bend without breaking) is crucial. Metallurgists spend a lot of their time coming up with the optimum tradeoff between hardness and toughness for each metal airplane part.
Iron can also be alloyed with chromium and/or nickel to form various flavors of stainless steel. These are generally not nearly as strong as carbon steel, but they’re much more resistant to heat and corrosion. These chromium and nickel varieties are often used in exhaust systems, heat shields and firewalls.
Aluminum can also be alloyed with various elements to improve its structural properties. Copper is added to create the 2000-series alloys most commonly found in aircraft structures, providing excellent strength-to-weight ratio and good fatigue resistance. The biggest downside of this alloy is that it is far more vulnerable to corrosion than pure aluminum. Consequently, it is generally protected by an anodized finish or with a thin layer of pure aluminum (“Alclad”).
Other aluminum alloys used in aircraft include the 6000-series (containing magnesium and silicon) and the 7000-series (containing zinc)—the former is highly corrosion-resistant, while the latter is the strongest of all aluminum alloys.
Heat-treating
The strength, hardness and toughness of alloys like carbon steels and aluminum-copper alloys—can also be profoundly affected by heat-treating. Anyone who has built model airplanes is probably already familiar with this.
Suppose you want to make a spring-steel landing gear for your model out of a length of high-carbon steel “piano wire” available at any hobby shop. As it comes from the store, piano wire is very springy and tough—perfect for a landing gear—but it’s also extremely difficult to bend and form without breaking. The solution most modelers use is to heat the wire with a torch until it becomes a bright cherry red (about 1400ºF), and then let it cool slowly. This is called “annealing” and transforms the steel wire into a soft, non-springy form that can easily be bent and formed to the desired shape.
Of course, the annealed wire is way too soft to be suitable landing gear material, but that can be easily rectified. Once the gear is bent to shape, the next step is to heat-treat the wire by heating it back up to bright cherry red and then plunging it into a bucket of water. This “quenching” transforms the wire into a very hard condition. In fact, the heat-treated wire is now so hard that it is quite brittle and would probably snap off in a hard landing.
The final step is to “temper” the wire back to somewhat reduced hardness to provide the required toughness and springiness. This is done by heating the wire back up to a medium blue color (about 750ºF) and allowing it to cool slowly. The final hardness is a function of temperature—the hotter the metal is heated during the tempering process, the softer, tougher and less brittle it will be.
This very same process—annealing, bending, heat-treating, and tempering—is precisely the way spring-steel landing gear legs on production aircraft are made.
How heat-treating works
The physics and chemistry behind heat-treating of carbon steel is complex, but the basic principle is this: At room temperature, the atoms of metallic iron are organized as a crystalline structure known as “body-centered cubic” (BCC). When iron is heated above its critical temperature of about 1400ºF, the structure transforms into “face-centered cubic” (FCC).
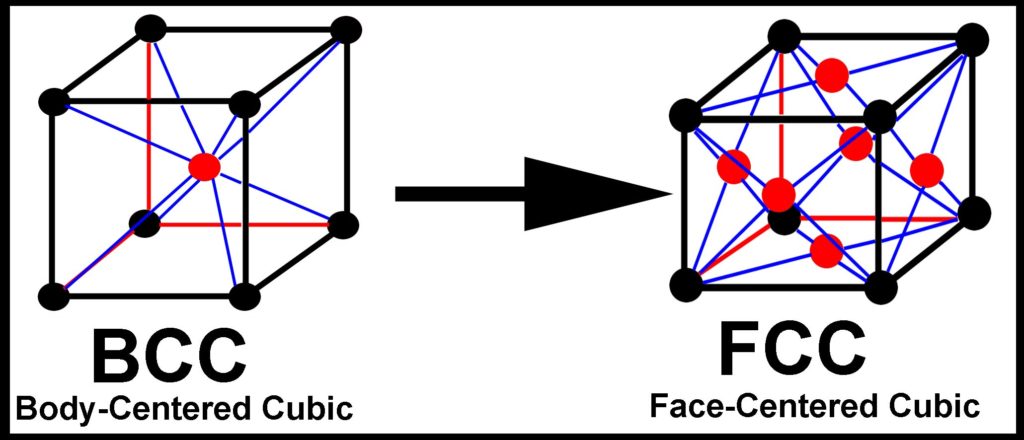
Steel is iron with a few percent of carbon mixed in. When steel is heated to the critical temperature and the iron transforms from BCC to FCC, the carbon atoms migrate into the central position of the cubes formerly occupied by iron atoms, creating non-magnetic “austentite.”
If this austentite is allowed to cool slowly (“anneal”), iron atoms migrate back into the center of the cubes and force the carbon atoms back out, resulting in a mixture of pure iron (Fe) and iron carbide (Fe3C), which is a soft steel known as pearlite.
On the other hand, if austentite is cooled quickly by quenching it in water or oil, the carbon atoms get trapped inside the crystalline structure to form a very hard, very brittle steel called “martensite.” This process is called heat-treating, and the result is too brittle for most uses.
The martensite may then be tempered by heating it back up to a temperature well below critical—typically 200ºF to 800ºF depending on the final hardness desired. This allows some of the trapped carbon atoms out of their crystalline jail cells, and relieves some of the hardness and brittleness. In this way, varying degrees of hardness and toughness may be achieved. A steel cutting tool needs to be very hard, while a steel landing gear leg needs to be tough and springy.
Aluminum alloys can also be hardened through heat-treating and softened by annealing. The critical temperature is a lot lower (about 800ºF), but the principle is the same.
Strain-hardening
Another way to harden metal involves pressure. When soft metal is compressed beyond its elastic limit, it becomes harder because the atoms in its crystalline structure are packed together more tightly. This is known as “strain-hardening” or “work-hardening.
Sheet metal may be strain-hardened by passing it between pressure rollers, either when cold (“cold-rolling”) or hot. The most common sheet metal used in aircraft construction is called “2024-T3 Alclad.” The “2024” refers to the aluminum alloy (approximately 4% copper plus small amounts of tin and zinc). The “T3” means that the metal is heat-treated and then cold-rolled. The “Alclad” means it’s then plated on both sides with a very thin layer of commercially pure aluminum to provide corrosion-resistance.
Another example of strain-hardening is the humble rivet. The “AD” rivets most commonly used in aircraft construction are made of relatively soft 2017 aluminum alloy. When the rivet is driven with a rivet gun and bucking bar, the alloy is strain-hardened to form a strong joint.
For large parts like pistons, connecting rods, crankshafts and camshafts, strain-hardening is often accomplished by “forging” in which a hot metal ingot is pressed into shape in a hydraulic press. Forged parts are stronger than cast parts because the forging process strain-hardens the metal as it is being shaped.
Case-hardening
Alloying, heat-treating and strain-hardening are all methods of hardening a metal part in its entirety—so-called “through-hardening.” Sometimes, it’s desirable to harden only the surface (perhaps just one surface) of a metal part, while leaving the interior tougher and less brittle. Examples include cylinder walls, crankshaft journals, cam lobes and tappets. The process of hardening only the surface of a part is known as “case-hardening” and it can be accomplished in two ways: mechanical and chemical.
Mechanical case-hardening is commonly accomplished by cold-rolling or shot-peening, both of which harden the metal surface by strain-hardening. The two most common methods of chemical case-hardening are “carburizing” and “nitriding.” Carburizing involves baking the part in a carbon monoxide (CO) atmosphere, causing additional carbon to be absorbed into the surface and converting a thin outer layer from mild steel to harder and stronger high-carbon steel. Nitriding is similar, but the part is baked in an atmosphere of ammonia gas (NH3), causing the surface to absorb nitrogen atoms that make their way into the interstitial regions of the iron lattice much as carbon does. Both methods result in extremely hard and durable wear surfaces without embrittling the interior of the part.
It’s amazing what metal can be coaxed into doing. It’s fascinating stuff.
You bought a plane to fly it, not stress over maintenance.
At Savvy Aviation, we believe you shouldn’t have to navigate the complexities of aircraft maintenance alone. And you definitely shouldn’t be surprised when your shop’s invoice arrives.
Savvy Aviation isn’t a maintenance shop – we empower you with the knowledge and expert consultation you need to be in control of your own maintenance events – so your shop takes directives (not gives them). Whatever your maintenance needs, Savvy has a perfect plan for you: