Compared to Lycocontisauruses, the Rotax 912 is delightfully different.
The past 20 years may well have yielded more outside-the-box ideas than any other comparable period in history. The iPod redefined the music industry in 2001. Facebook, YouTube and Twitter (2004–2006) redefined how we interact. The iPhone (2007) not only redefined “cell phone” but changed our lives in too many ways to count. Airbnb (2008) redefined “lodging,” Uber (2009) redefined “ground transportation,” and the iPad (2010) and Foreflight (2011) redefined our GA cockpits. (Remember when we schlepped around 15 pounds of Jepp binders, and spent mind-numbing hours keeping them updated?) Wow!
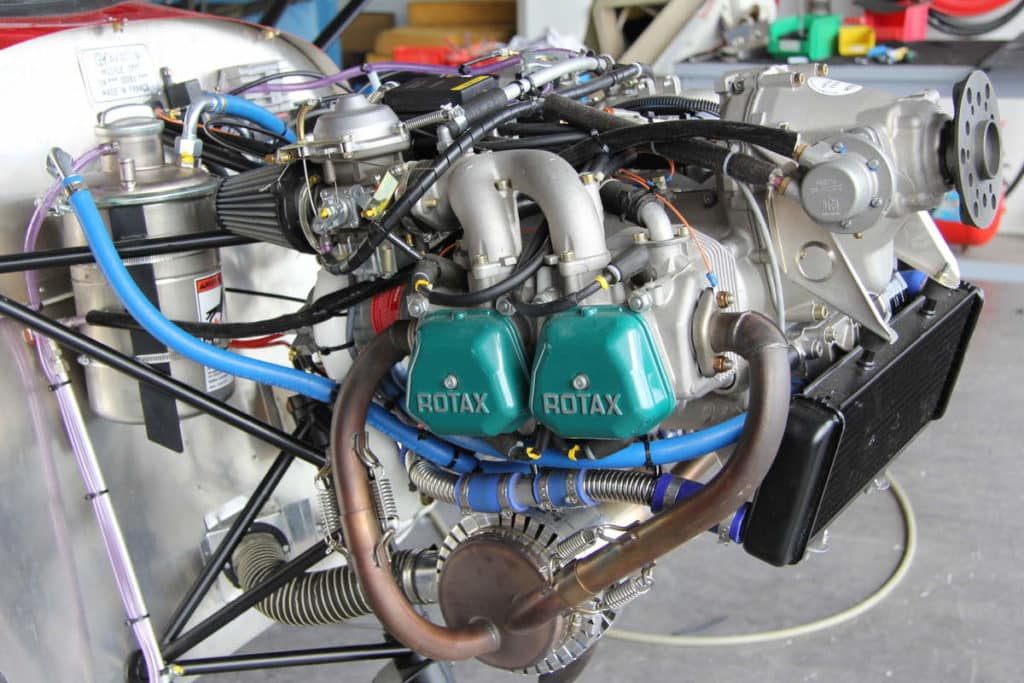
While all this amazing innovation was happening, few U.S. aviators noticed that an obscure Austrian subsidiary of a Canadian company mostly known for its two-stroke snowmobile, motorbike and ATV engines was quietly redefining the small (under 150hp) four-stroke piston aircraft engine. Few noticed, that is, until 2004 when the FAA approved the LSA rule, and sexy factory-built Special Light Sport Aircraft started entering the U.S. aircraft registry and showing up at Oshkosh, Lakeland and Sebring.
Nearly all those S-LSAs turned out to have same engine: the Rotax 912. (Huh? Ro-who? Isn’t that the engine used on ultralights? The one that sounds like what you get when you cross a mosquito with a chainsaw?)
Today, as the LSA rule celebrates its 13th birthday, nearly every pilot has heard of Rotax. Yet the outside-the-box nature of its innovative engines remains widely underappreciated outside the S-LSA community. This 100hp engine is definitely not your daddy’s Lycoming O-235 or Continental O-200!
Evolution
The Rotax 912 story actually began in 1989, when the first 80 hp engines were shipped to customers in Europe for use on ultralights and motorgliders. Rotax already dominated those markets with its two-stroke engines derived from their snowmobile engines. But almost nobody outside the ultralight community took notice.
For one thing, Rotax had developed a reputation for building cheap, light, cantankerous, not-very-reliable “throw away” engines with ridiculously short 300-hour TBOs. For another, the new 912 four-stroke engine had a TBO of only 600 hours—perhaps an improvement by ultralight standards, but hardly acceptable in the world of “real airplanes.”
Rotax pressed forward. By 1994, Rotax obtained FAA certification of the 80 hp 912, and in 1996, it introduced a turbocharged version (the 914) rated 115 hp. In 1999, a 100 hp normally-aspirated version for ultralights (912 ULS) was introduced, and an FAA-certified version (912 S) quickly followed. By now, the TBO had been increased to 1,200 hours for the 912 and 1,000 hours for the 914. The engines were selling like hotcakes abroad, but never gained much traction in the U.S.
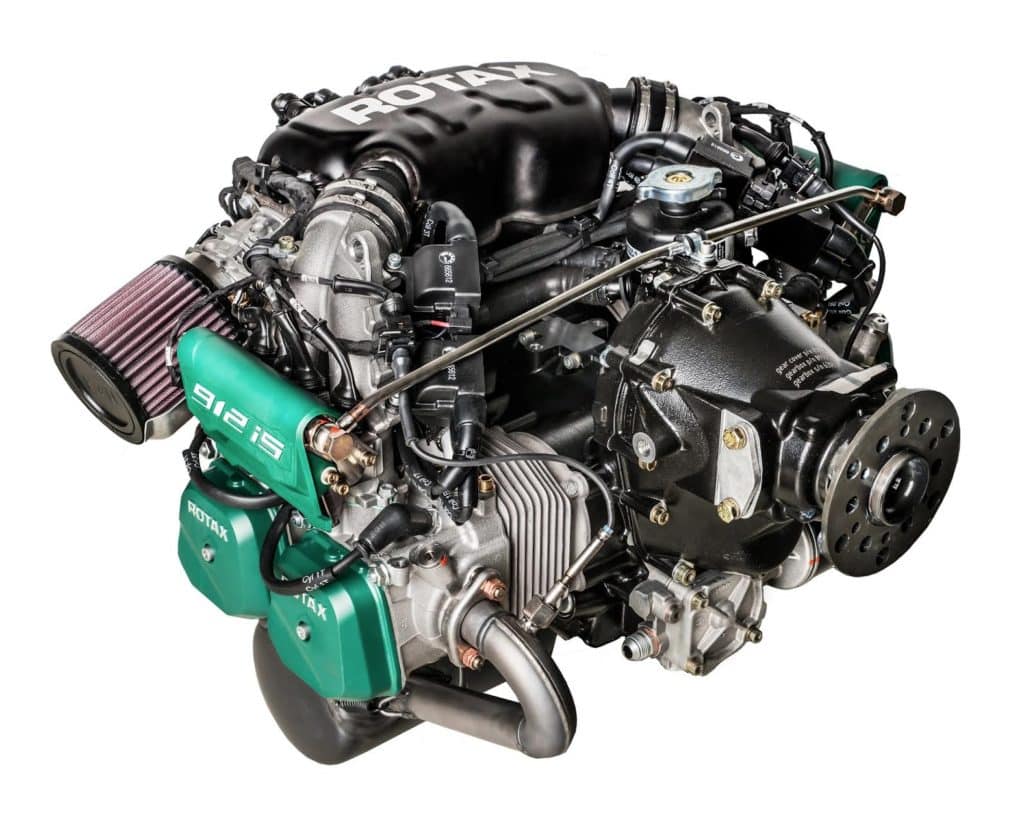
Everything changed in 2004–2005 when the LSA rule was adopted by the FAA. Suddenly factory-built S-LSAs became all the rage, and the overwhelming majority of them were powered by the Rotax 912 ULS. LSA designers considered it the obvious choice: It was substantially lighter and more compact and efficient than traditional 100 hp engines (e.g., Lycoming O-235, Continental O-200), was designed to run on unleaded mogas, and by then had a credible 1,500-hour TBO. What wasn’t to like?
Finally, in 2009, Rotax upped the TBO of the 912-series to 2,000 hours, and the following year did the same for the turbocharged 914. In 2012, the company started shipping a fuel-injected FADEC version (912 iS).
By 2014, Rotax had delivered 50,000 of these engines. A 135 hp version (915 iS) announced in 2015 should start shipping by the end of this year. It wouldn’t surprise me if a turbocharged version of the 915 iS is in the company’s skunkworks.
Delightfully Different
If you grew up in a world of Continentals and Lycomings like I did, these four-stroke Rotaxes take some getting used to. They’re definitely different…and I mean that in a good way. Heck, if Rotax made a 300 hp version I could hang on my Cessna T310 in place of its Jurassic Continental TSIO-520s that were designed more than a half-century ago, I’d do so in a heartbeat!
To begin with, the engine is astonishingly small and light. The ubiquitous 912 ULS has a dry weight of just 132 pounds, compared to 199 pounds for a Continental O-200-D or 240 pounds for a Lycoming O-235-C. (All three of these engines are rated at 100 hp.) How does Rotax accomplish this? Mainly, by turning the engine twice as fast: Redline is 5,800 RPM for takeoff and typically 5,000 RPM in cruise. Hence the cylinders can have a lot less displacement because they process twice as many combustion events.
Of course, you can’t turn a prop that fast without the prop tips going supersonic (and generating a lot more noise than thrust), so the engine has a reduction gearbox with a 2.43-to-1 gear ratio. At redline (5,800 RPM), the prop turns at less than 2,400 RPM; in cruise (5,000 RPM), the prop turns just over 2,000 RPM. The notion of a geared engine might sound scary, but the Rotax gearboxes have been trouble-free and require no special maintenance other than a 1,000-hour recommended inspection.
Obtaining 100 hp from such tiny cylinders at such high RPM creates a bit of a cooling challenge. Rotax deals with this elegantly by combining conventional air-cooling of the finned cylinder barrels with liquid cooling of the cylinder heads. The engine incorporates a small integral coolant pump and a small external radiator. Coolant volume is only about a half-gallon, so it doesn’t add much weight. Liquid cooling of the heads results in far lower CHTs that most of us are used to seeing—typically less than 200°F in cruise, with a 275°F redline.
The ignition system is electronic, powered by dual alternators that are built right into the engine. There’s a powerful permanent magnet on the flywheel that induces AC current into a pair of stator coils inside the crankcase. The AC is fed to an electronic rectifier/regulator unit that puts out 13.8 volts DC. These dual alternators power the dual solid-state ignition system. They also drive the electronic tachometer (which displays crankshaft speed, not propeller speed).
Oil and Gas
The oil system is a bit different, too. Instead of using a “wet sump” system with a large oil pan on the bottom of the crankcase (like all Lycomings and most Continentals), the Rotax uses a “dry sump” system employing an external cylindrical oil tank. Instead of relying on a scavenge pump to return oil to the tank—or on gravity like the O-200 does, requiring the oil tank to be below the crankcase—Rotax uses internal crankcase pressure (caused by blow-by of combustion gases) to propel the oil from the bottom of the crankcase to the oil tank.
This demands a novel preflight procedure: Before checking the dipstick to determine the oil level, it is necessary to “burp the engine” by removing the oil filler cap and then pulling the prop through by a few blades until you hear a gurgling sound that indicates that all the oil from the bottom of the crankcase has been pushed into the oil tank and only air is left in the crankcase. Once the engine has been “burped,” you can obtain an accurate dipstick reading and you’re assured of a full oil tank at engine start.
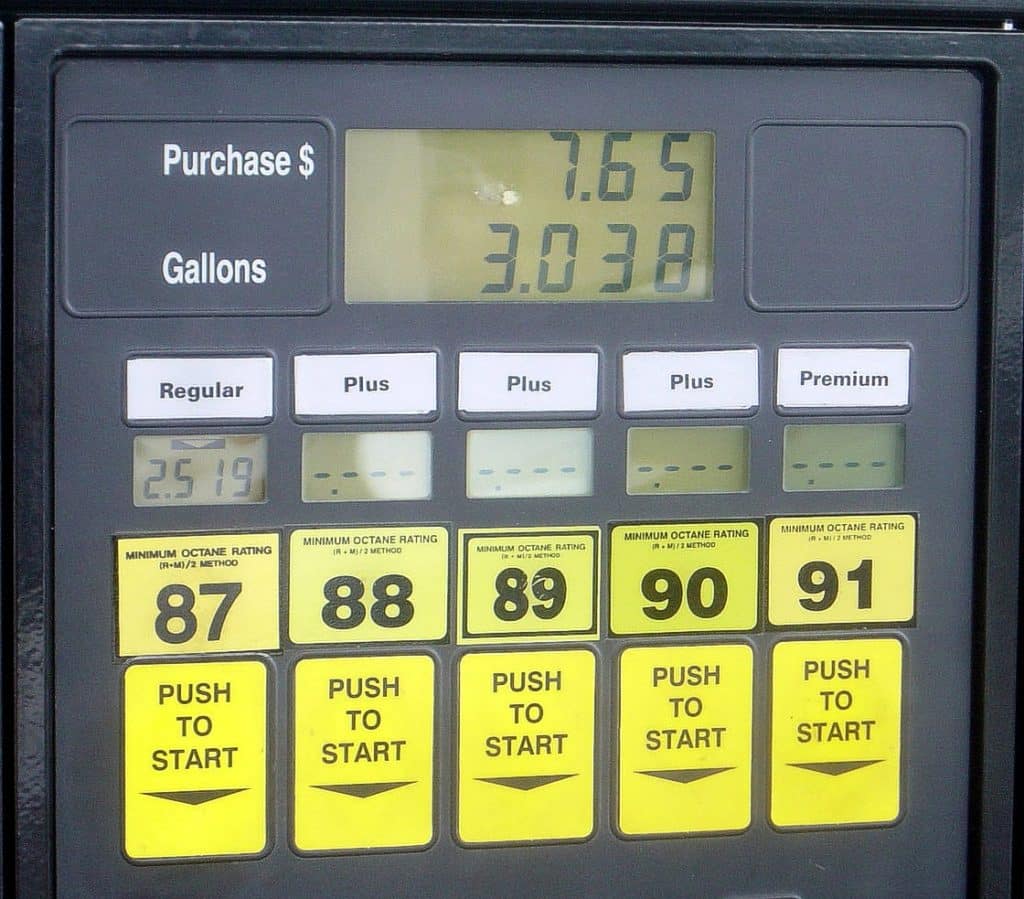
Rotax engines have no mixture control knob. Most carbureted ones like the 912 ULS incorporate dual Bing carburetors with a high-altitude compensator (H.A.C.) that automatically adjusts the fuel-air mixture by sensing pressure altitude. The injected ones like the 912 iS incorporate a FADEC that accomplishes the same thing.
Perhaps the most delightful difference is that the Rotax is designed to use unleaded autogas, which is significantly cheaper and cleaner than avgas. Using 100LL is permissible but not recommended. In fact, if the engine is run on 100LL more than 30% of the time, Rotax calls for a reduced oil and filter change interval, and increased preventive maintenance. The use of leaded avgas can cause buildup of lead sludge in the oil tank and reduction gearbox, among other bad things. Also, oil recommendations are different—you’re not allowed to use all-synthetic oil like Mobil 1 if you use leaded avgas, because synthetic oil can’t hold lead in suspension. Bottom line: Try to use unleaded mogas instead of leaded avgas if you possibly can.
Operation
Preflight is straightforward, but with a few Rotax-specific twists. We’ve already discussed the need to “burp the engine” before checking the dipstick and possibly adding oil. It’s also important to check the coolant level; the main coolant tank should be full, and there should always be some extra coolant in the overflow tank. The preflight visual inspection should include looking for coolant leaks.
Starting is a bit different. The carbureted 912s have a choke but no primer. Cold-starting is accomplished by pulling the throttle all the way back to idle, activating the choke fully, turning on the electric aux fuel pump, and cranking the engine (10 seconds maximum). Once the engine starts, retard the choke slowly and simultaneously advance the throttle to maintain an idle speed of about 2,000 RPM—remember, that’s crankshaft speed, not prop speed.
After the engine warms up for a minute or two, advance the throttle to 2,500 RPM and make sure that the oil temperature is coming up. When oil temperature reaches about 120°F (50°C), it’s okay to taxi to the runup area. The mag…oops…ignition check is done at 4,000 RPM with a maximum drop of 300 RPM and no more than 120 RPM difference between the two ignition circuits. After the runup, throttle back to idle (around 2,000 RPM).
On takeoff, redline is 5,800 RPM for up to five minutes, then 5,500 RPM continuous. Typical cruise is 4,900 to 5,100 RPM. There’s no leaning to worry about. Make sure that CHT stays around 175°F–195°F (80°C–90°C) and never exceeds 275°F (135°C). Oil temperature should be between 165°F–230°F (75°C–110°C), and oil pressure should be about 60 PSI (4 bar).
After landing, allow the engine to cool down at idle RPM for a bit before shutting the engine down (with the ignition switch, there’s no mixture control). This keeps the coolant circulating and helps prevent any boiling that might occur if the engine stopped with hot cylinder heads. Using waterless coolant eliminates the issue.
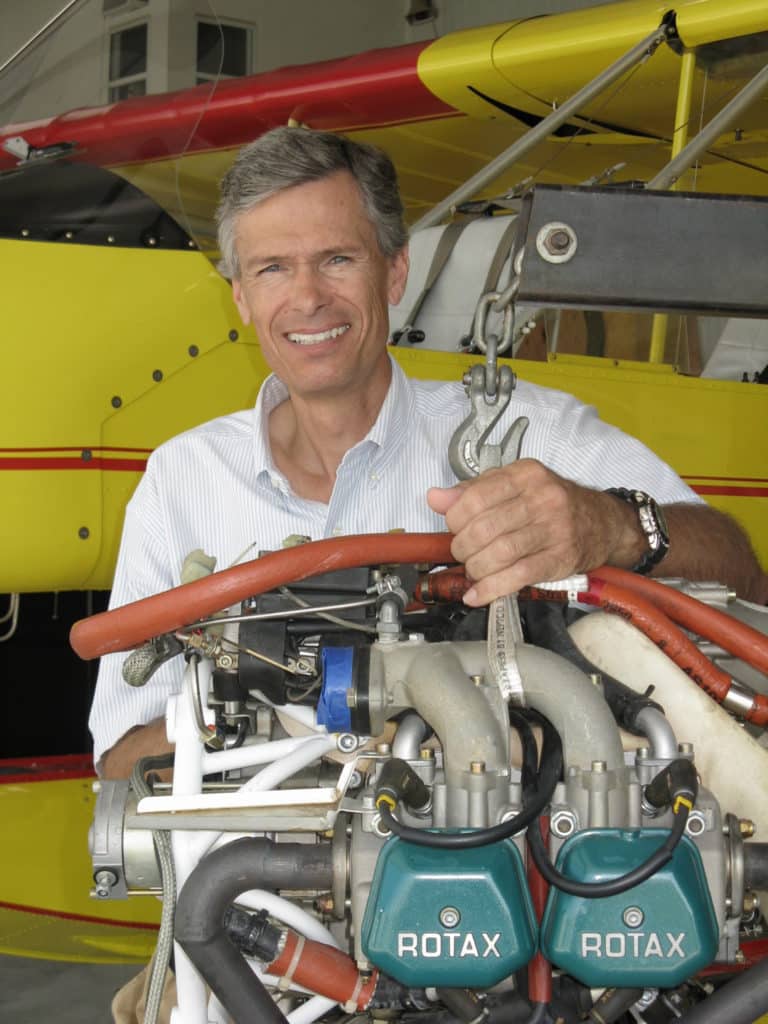
Bulletproof
Lockwood Aviation in Sebring, Florida is the preeminent provider of Rotax parts, overhaul, and maintenance training in the U.S. I had a long chat with Rotax guru Phil Lockwood about the reliability and durability of these engines. Phil told me that when Rotax 912s come into his shop for overhaul after 2,000 hours and he tears them apart, it’s absolutely astonishing how pristine they are inside. After 28 years of incremental evolution, product improvement and TBO extension, these engines seem to be about as bulletproof as anything in aviation.
Now if they’d only build a 300 hp version…
You bought a plane to fly it, not stress over maintenance.
At Savvy Aviation, we believe you shouldn’t have to navigate the complexities of aircraft maintenance alone. And you definitely shouldn’t be surprised when your shop’s invoice arrives.
Savvy Aviation isn’t a maintenance shop – we empower you with the knowledge and expert consultation you need to be in control of your own maintenance events – so your shop takes directives (not gives them). Whatever your maintenance needs, Savvy has a perfect plan for you: