Dan just purchased his first airplane, a 1974 Piper Warrior PA-28-151. A 60-hour student pilot, he bought the plane in Texas and—accompanied by his CFI—flew it home to California. Part of Dan’s deal with the seller was that the seller would have an annual inspection performed and any airworthiness discrepancies corrected before Dan took delivery of the aircraft.
On the ferry flight to California, the plane seemed to fly fine except for a rather anemic rate of climb. This wasn’t a big issue during the flight home because all stops were at airports with long runways. But Dan’s home field has a 3,300-foot runway, and on takeoff the plane just barely cleared the trees off the departure end.
Dan subsequently became aware that the PA-28-151 had a minimum static RPM specification of 2275 RPM, and this is something that should have been checked by the shop during the post-annual runup. Dan’s airplane barely made 2200 RPM on a good day. Now he was getting concerned..
Dan took his newly-purchased fresh-out-of-annual Warrior to a local mechanic on his home field and asked him to look the plane over to find out the reason for its anemic climb rate and failure to make specified static RPM. The local mechanic reported the following findings:
- Compressions 50/58/62/64 (though the Texas shop recorded 71/73/68/74 at annual)
- Borescope revealed all cylinders severely scored with obvious hot spots on the exhaust valves
- Grossly excessive dry tappet clearance (suggestive of a severely worn camshaft)
- Nearly ½ teaspoon of ferrous metal found in the oil filter and suction screen
- Additional airworthiness discrepancies involving a leaking carburetor, damaged ignition harness, worn and frayed trim cables, and severely chafed brake hoses
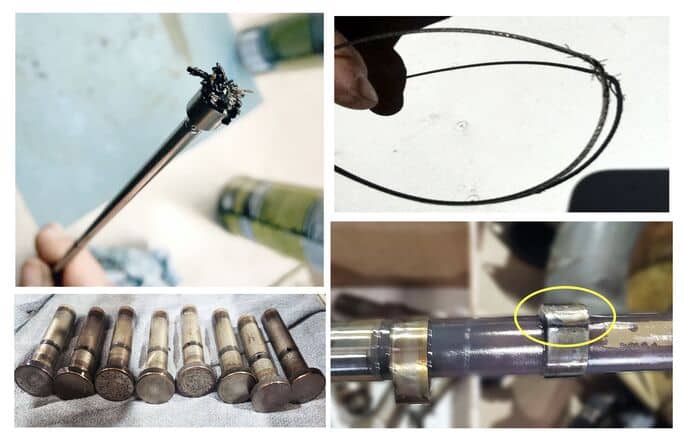
Dan found himself with a grounded airplane and an engine in need of teardown. The teardown confirmed that the engine was pretty much a train wreck internally with a bad cam, bad oil pump, and contaminated bearings. He felt that he’d been cheated and defrauded, but what was his recourse?
Dan’s purchase/sale agreement with the seller included the typical “as-is” language in which the seller provides no warranty and the buyer is solely responsible for determining the airworthiness of the aircraft. Dan spoke with the seller and came away convinced that the seller was honestly unaware of the mechanical issues with the aircraft.
The shop that did the annual had been maintaining the aircraft for the past four years and the shop’s owner and the seller were quite friendly. Although it appears the shop was negligent in its performance (pencil-whipping?) of the annual inspection, Dan did not hire the shop and so the shop owed no duty to him.
Dan contacted Savvy, but at this point there wasn’t a lot we could do for him. We recommended he contact an AOPA Legal Services Plan attorney, who drafted an official-sounding demand letter that was sent to the shop. The shop turned it over to their insurance company, whose adjuster offered Dan a $5,000 settlement in order to “make this go away.” Dan declined the settlement because it represented only a very small down-payment on what it would cost to make the Warrior airworthy.
Dan learned the hard way something that we’ve been telling our SavvyPrebuy clients for more than a decade:
An annual inspection furnished by the seller is never an adequate substitute for an independent prebuy examination conducted by the buyer.
Savvy Aviation manages hundreds of prebuys each year, and we’ve seen just about everything that can go wrong. Consequently, we have developed a series of strict rules that we follow without exception. The prebuy examination must be performed by a shop or mechanic who has never seen the aircraft before, and who has no prior relationship with the seller (or with the seller’s broker if a broker is involved in the sale).
To ensure such independence, we require the seller to authorize the prospective buyer to perform a prebuy by any shop or mechanic of the buyer’s choice within one-hour flying time of the aircraft’s home base. In almost every case, we insist on having the aircraft flown somewhere other than its home airport for the prebuy (but not an unreasonable distance away) to guarantee that the examination is performed outside the seller’s or broker’s sphere of influence. Often this ferry flight doubles as a test flight to ensure that the plane flies straight, performs to spec, and all systems and avionics are working properly.
If the seller or his broker will not agree to these terms, we invariably advise our client to pass on the aircraft and move on to another purchase candidate. Had Dan utilized our SavvyPrebuy service, he would have been spared what will probably wind up being a $50,000 shock, not to mention an enormous amount of aggravation.
If you’re in the market to purchase a pre-owned aircraft, wouldn’t you benefit from a Savvy-managed prebuy to help ensure you don’t wind up buying a lemon the way poor Dan did?
You bought a plane to fly it, not stress over maintenance.
At Savvy Aviation, we believe you shouldn’t have to navigate the complexities of aircraft maintenance alone. And you definitely shouldn’t be surprised when your shop’s invoice arrives.
Savvy Aviation isn’t a maintenance shop – we empower you with the knowledge and expert consultation you need to be in control of your own maintenance events – so your shop takes directives (not gives them). Whatever your maintenance needs, Savvy has a perfect plan for you: