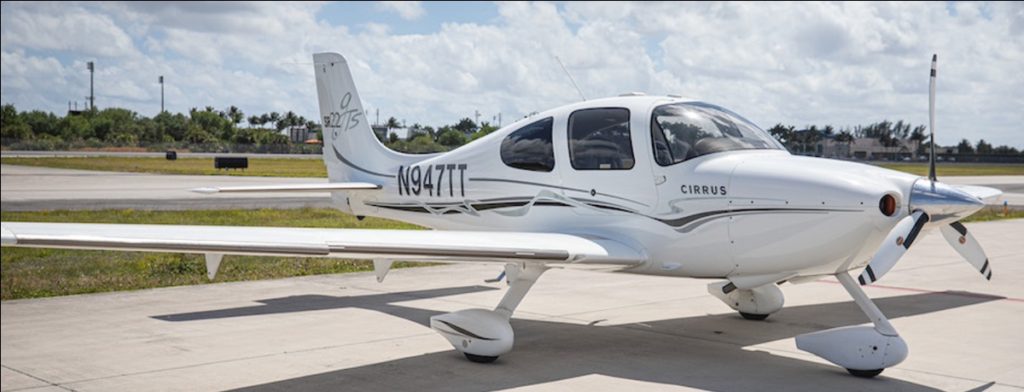
Harry based his 2006 Cirrus SR22 in Boca Raton, Florida. The summers there are hot and humid, so air conditioning is right up there with food, clothing and shelter. So when the air conditioning system in the plane quit working, Harry considered getting it fixed to be a high priority item.
Harry’s plane was enrolled in Savvy’s flagship maintenance management service known as SavvyMx. His Savvy account manager was Tom Cooper A&P/IA, one of Savvy’s most experienced technicians with years of Cirrus maintenance experience.
Tom arranged for Harry’s plane to go into the shop at East Coast Aviation Services (ECAS) in nearby Stuart, Florida (KSUA) for a scheduled oil change plus correction of a few squawks. ECAS is a Cirrus Authorized Service Center. The squawks included an inoperative pilot map light, a leaky rear window and stained headliner, a bad avionics cooling fan, and most importantly the problematic air conditioning system. Shortly thereafter, Harry departed on an airline trip to Australia, leaving things in Tom’s capable hands.
Diagnosis
Tom gave a list of those squawks to Rick Eppler, ECAS’s longtime Director of Maintenance, and indicated that at the top of the list was to inspect the air conditioning system and determine exactly why it had stopped working.
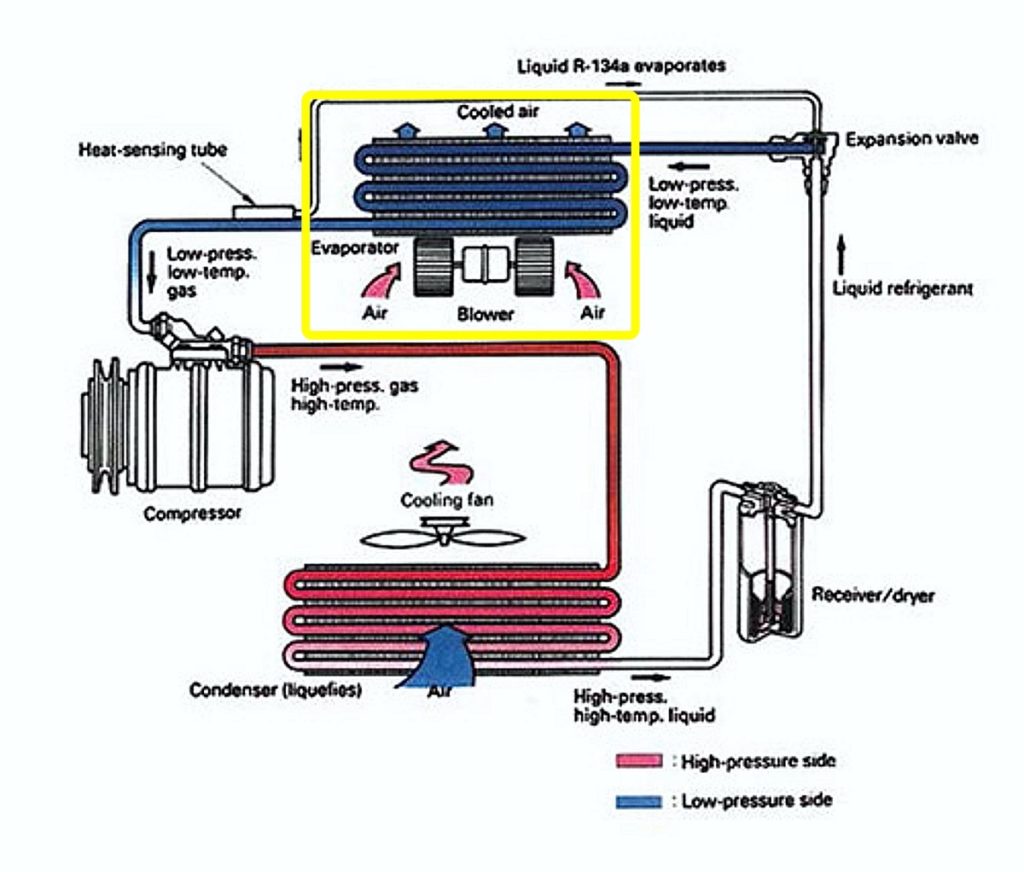
Tom had previously discussed the symptoms with Harry and concluded that the problem was most likely related to the recirculation louvers in the evaporator module. Those louvers are opened and closed by a small geared servo motor. Tom speculated that either the louvers were mechanically jammed or that the servo motor was inoperative. It didn’t take Rick long to diagnose the problem…
“There is power to the louver motor, but the motor appears to be frozen,” Rick reported to Tom. “You cannot get the motor out without breaking the system and removing the entire evaporator assembly. I called Cirrus, who instructed me to send the evaporator assembly back to the manufacturer—Enviro Systems Inc. in Seminole, Oklahoma—for repair. I am waiting to hear back from Enviro for instructions.”
“Considering that Harry is in Australia, let’s go ahead and forward the evaporator to Enviro for inspection only and get a repair cost estimate,” Tom told Rick. “From my conversation with them they should be able to fix the motor only and return it to us.”
Rick removed the evaporator assembly from the aircraft and shipped it to Oklahoma via UPS three-day (it was heavy!), then went to work on the oil change and other squawks. He inspected the rest of the air conditioning system and reported that it all looked to be in good shape.
Sticker Shock
Ten days after the evaporator assembly was shipped to Enviro for inspection, the company emailed Rick with the following evaluation and repair estimate:
VISUAL CONDITION AS RECEIVED: THE BRACKETS HAVE PLATING DAMAGE. TWO BRACKETS ARE MISSING FROM THE UNIT.
TEARDOWN ANALYSIS: S/N- 171 WW104025. THE RECIRCULATION LOUVERS DO NOT OPERATE. THE GEAR MOTOR GEARS ARE STRIPPED.
THE UNIT NEEDS TO BE OVERHAULED DUE TO AGE AND NORMAL WEAR. OVERHAUL IS NEEDED. WILL REPLACE ALL WORN/DAMAGED PARTS AND TEST PER ATP SPECS.
- 133141-3 BRACKET, TEMP SWITCH 1
- 1133142-3 BRACKET, EVAP AFT 1
- 1133143-3 BRACKET ASSY, EVAP FWD 1
- 1133146-5 ESCUTCHEON ASSEMBLY, EVAPORATOR 1
- 1133148-2 BRACKET, EVAP MOUNT CTR 1
- 1133148-3 BRACKET, EVAP CORNER AFT 1
- 1133148-4 BRKT, EVAP CORNER FWD 1
- 1133210-11 ASSY., CCW BLDC MOTOR 1
- 1250327-9 BLOWER WHEEL 1
- 1250383-15 SCROLL ASSY. 1
- 1133040-1 INLET PLENUM ASSEMBLY 1
- 1133185-1 EXPANSION VALVE, THERMOSTATIC 1
- 1133190-1 SWITCH, LOW TEMPERATURE 1
- 1133147-2 SHROUD ASSEMBLY, EVAPORATOR 1
COST: $4993.99
“WHAT???” Tom reacted when he saw this. “This assembly was working fine except that the recirculation lovers would not open and close properly. Seems absurd to replace nearly every component in the assembly when all that’s needed is to replace a couple of stripped gears. I think we need to push back on this.”
Tom asked Rick to contact Enviro and ask them to give a quote for just repairing “the gear motor gears [that] are stripped” in the recirculation louver servo and nothing else.
“I called Enviro yesterday but could not speak to the repair manager,” Rick reported back. “I left a voicemail, also sent a detailed email with our requests. No word from Enviro yet, I will call them again today.”
Persistence Pays
Anyone who knows Tom Cooper knows that he doesn’t give up easily.
“I managed to reach Enviro’s repair manager and we had a long conversation about this matter,” Tom told Rick. “If you will email her specific instructions that we want Enviro to fix ONLY the louver motor and to replace the two missing brackets, she has assured me that Enviro will fix only those items and send the complete unit back to you with an FAA Form 8130-3 marked ‘Repaired.’ They will also give a six-month warranty on the parts they replace or fix. This should save Harry thousands of dollars. Please advise when they expect to ship the unit back to you.”
“I managed to reach the Enviro repair manager by telephone,” Rick reported a short time later. “She says it should take 10 days to repair the evaporator assembly, and all parts are in stock.”
“That’s great news,” said Tom, “but we will need a repair estimate before we can approve the repair.”
Tom called Enviro once again and received the repair estimate: $2,478.00. While that still seemed an awful lot of money to replace a couple of stripped gears and a couple of missing brackets, it was still less than half the cost that Enviro had quoted for a full overhaul, and saved Harry more than $2,500.
A few weeks later…
“We finally got the repaired evaporator assembly back from Enviro,” Rick reported. “Installed it in the aircraft and it works as advertised!! Putting the aircraft back together today. Will keep you posted.”
When Harry got back from Australia, he posted his experience to the Cirrus Owners & Pilots Association (COPA) forums so that other Cirrus owners with air conditioning issues would know that overhauling these components was not the only option available. Hopefully this will save other Cirrus owners from unneeded expense when their air conditioning system goes on the fritz.
Harry’s story illustrates the kind of zealous owner-centric advocacy upon which Savvy has built its reputation since Mike Busch founded the company 13 years ago. The $2,500+ that Harry saved on this one repair alone is enough to pay for his $750/year SavvyMx subscription for the next three years with enough change left over for a few $100 hamburgers.
This isn’t unusual. Savvy almost always saves its clients far more in reduced maintenance costs than it charges them for its fixed annual subscription fees. And now you’ve seen how we do it.
If you’re not already a SavvyMx client, you might give serious thought to enrolling your aircraft in the program. You won’t be sorry. Just ask Harry.
You bought a plane to fly it, not stress over maintenance.
At Savvy Aviation, we believe you shouldn’t have to navigate the complexities of aircraft maintenance alone. And you definitely shouldn’t be surprised when your shop’s invoice arrives.
Savvy Aviation isn’t a maintenance shop – we empower you with the knowledge and expert consultation you need to be in control of your own maintenance events – so your shop takes directives (not gives them). Whatever your maintenance needs, Savvy has a perfect plan for you: