Condition-based maintenance meets big data and artificial intelligence
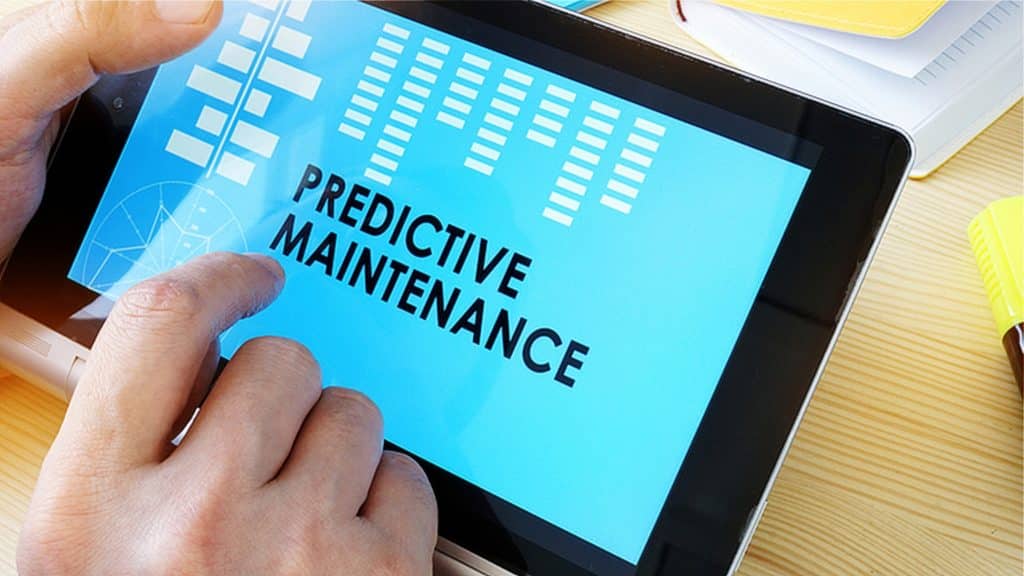
For the past 20 years, I’ve been preaching the gospel of Reliability-Centered Maintenance (RCM), the then-revolutionary philosophy of maintenance developed in the 1960s at United Airlines by aeronautical engineer Stanley Nowlan and mathermatician Howard Heap. RCM was almost universally adopted by the airlines in the 1970s, by military aviation in the 1980s, and by high-end business aviation in the 1990s. The only segment of aviation that hasn’t yet enthusiastically adopted RCM is owner-flown GA. I’ve made it my personal crusade to change this, and to help drag lightplane maintenance kicking and screaming into the 21st century.
RCM arose from a rigorous analysis of historical data by Nowlan & Heap showing that the airlines’ maintenance programs called for more preventive maintenance than necessary, and that such excessive maintenance was actually making aircraft safety and dispatch reliability worse rather than better by increasing the incidence of maintenance-induced failures (MIFs). At the time, these findings were considered heresy by most folks in the airline maintenance organizations, who had been taught to believe that maintenance is a good thing and more maintenance is always better. In spite of these objections, the airlines adopted RCM anyway. Not only did they save a fortune on reduced maintenance costs, but aircraft safety and dispatch reliability improved significantly.
The core principle of RCM is that most preventive maintenance should be performed only when genuinely necessary. It accomplishes this by doing away with most scheduled preventive maintenance (including most TBOs) and replacing it with a program of condition-based maintenance. This means doing away with time-based maintenance in favor of a program of inspections designed to assess the condition of critical aircraft components and to determine when their condition has deteriorated to the point that failure might be imminent. Component repair, overhaul or replacement is not performed until a condition inspection indicates it is required. The result is that work is performed only when demonstrably necessary, as opposed to at an arbitrary time interval when some aeronautical engineer calculated that it might possibly be necessary.
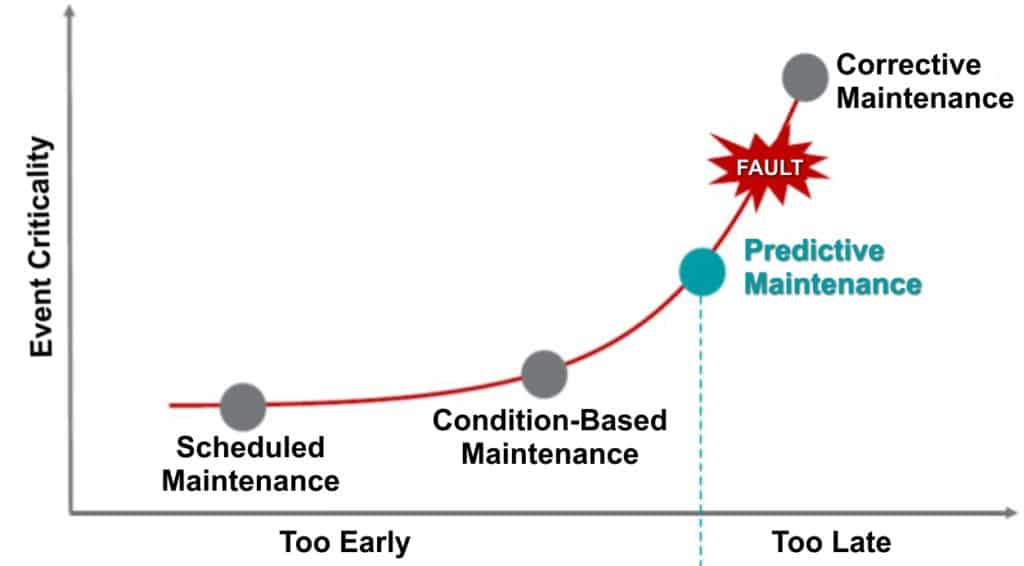
Condition-based maintenance has been a huge step forward compared with traditional scheduled maintenance. Predictive maintenance is the next big step forward.
RCM has been a huge step in the right direction, but it’s still less than a perfect solution. It requires regular condition inspections that are not inexpensive and may be somewhat invasive—they involve taking things apart and putting them back together—so are not completely free of MIF risk. Perhaps we can do even better.
During the two decades I’ve been working to bring the benefits of RCM to owner-flown GA, there has been another quiet revolution going on that started with the airlines and has been quietly trickling down the aviation food chain. It’s called Predictive Maintenance (PdM) and is based on a technology known as predictive analytics.
Predictive Analytics
Modern air transport aircraft and engines are built with thousands of sensors that measure air data, critical engine operating parameters, vibration levels, electrical and hydraulic system parameters, flight control and landing gear positions, fluid levels of all kinds, cabin pressurization and environmental parameters, and just about every other measurable aspect of the aircraft. Measurements from these many sensors are digitized by the aircraft’s data acquisition unit (DAU) and then either transmitted to ground stations in real time or captured continuously by a quick access recorder (QAR) and extracted once the aircraft is on the ground via the cellular network or on flash memory cards.
Predictive analytics—also known as predictive failure analysis (PFA)—employs various kinds of computer algorithms to process this mass of digital data and detect patterns indicating that some sort of preventive maintenance is necessary, or that evidence some incipient component failure has been detected.
Detection of parameter degradation, exceedance, or adverse trending—low tire pressure, high electrical bus voltage, decreasing oil pressure—is generally pretty easy. Prediction of “rare events”—contaminated fuel nozzle, damaged compressor blade, failing engine bearing—may require complex algorithms.
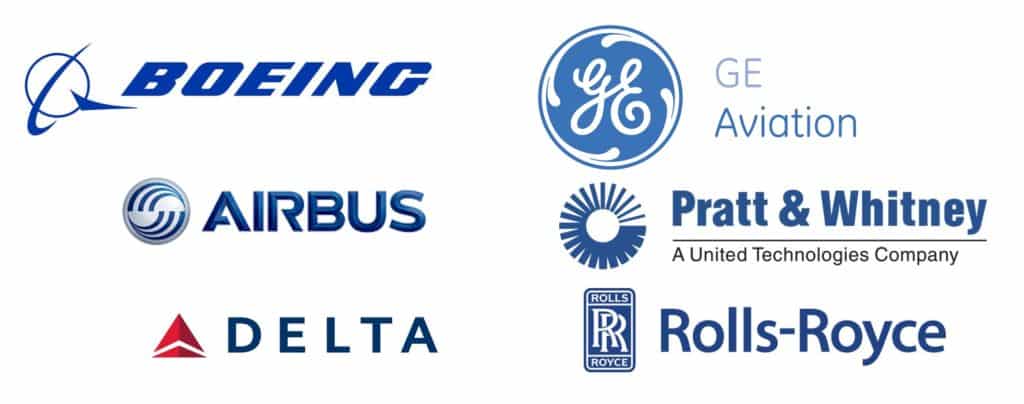
Transport aircraft and engine manufacturers have climbed aboard the predictive maintenance bandwagon in a big way.
Boeing pioneered predictive analytics 16 years ago when it introduced a service it calls Airplane Health Management (AHM). Boeing’s AHM monitors the health of an airplane in flight and relays that information in real time to airline personnel on the ground. When the airplane lands and arrives at the gate, maintenance crews are ready to make any needed repairs quickly. AHM algorithms also attempt to predict when aircraft components are in jeopardy of failing so that the operator can replace or repair them at the next scheduled maintenance check.
Nowadays, virtually every airline that flies Boeing’s 777s or 787s uses AHM, and Boeing is working to expand the service to earlier Boeing models as well as to non-Boeing aircraft (e.g., intercontinental bizjets). Last year, I had the opportunity to see AHM in action when I visited the Boeing Global Services office in Inglewood, Colorado, and to say I was impressed would be an understatement. This is very cool technology.
Not to be outdone, Boeing’s archrival Airbus has launched a predictive analytics service called Skywise in partnership with Palantir Technologies, a Palo Alto software company that specializes in big data analytics. Recently Airbus announced a partnership with Delta Air Lines as the pilot customer for Skywise Predictive Maintenance on Delta’s A320 and A330 aircraft to assess the failure probabilities of aircraft parts to anticipate the need for preventive maintenance tasks. Delta is claiming a success rate of over 95 percent for pending failure predictions. According to Delta, the carrier had only 55 maintenance-related flight cancellations in 2018, compared with more than 5,600 cancellations in 2010, and it credits predictive analytics for most of this improvement in dispatch reliability.
Jet engine manufacturers have also adopted this technology. General Electric presently appears to have the lead in predictive analytics with its Prognostic Health Management Plus (PHM+) program of real time analysis of continuously downlinked engine operating data for both air carriers and high-end bizjets. Pratt & Whitney’s eFAST has similar objectives, and in 2018 its parent company (United Technologies) acquired Predikto, an Atlanta-based provider of predictive analytics software. Rolls Royce appears to be still developing its predictive analytics program called IntelligentEngine.
What About Piston GA?
Few of our piston GA aircraft are riddled with sensors the way modern airliners like the 787 or A330 are. But more than half our fleet is equipped with some sort of digital engine monitor capable of capturing EGTs, CHTs, and other engine parameters. Some of these engine monitors also capture fuel flow, air data (altitude, airspeed, OAT), electrical bus data (volts and amps), and/or GPS position. There’s quite a bit of interesting analysis that can be done with this data.
In 2012 my company launched a free web-based digital engine data analysis platform at https://SavvyAnalysis.com. Since then, owners have uploaded data from more than 10,000 piston GA aircraft to the platform, and our database now contains data from some 2.5 million flights. From inception, this platform has automatically flagged exceedences such as high CHT. In recent years, we’ve been developing and incorporating more sophisticated predictive analytics algorithms.
Failing (burned) exhaust valves are “rare events” but they’re the leading cause of cylinder replacement, and exhaust valve failure is a significant cause of piston engine power-loss incidents. I’ve long observed that failing exhaust valves often cause small, slow, rhythmic EGT oscillations that are fairly easy to spot in a graphical plot of the data. In 2015, we developed a heuristic algorithm called FEVA™ (Failing Exhaust Valve Analytics) that scans all uploaded engine monitor data for this signature. We’ve been using this to alert owners to the possibility that they may have a failing exhaust valve and that a borescope inspection of the cylinder is suggested. But to be honest, we’ve been less than thrilled about the accuracy of the FEVA algorithm.
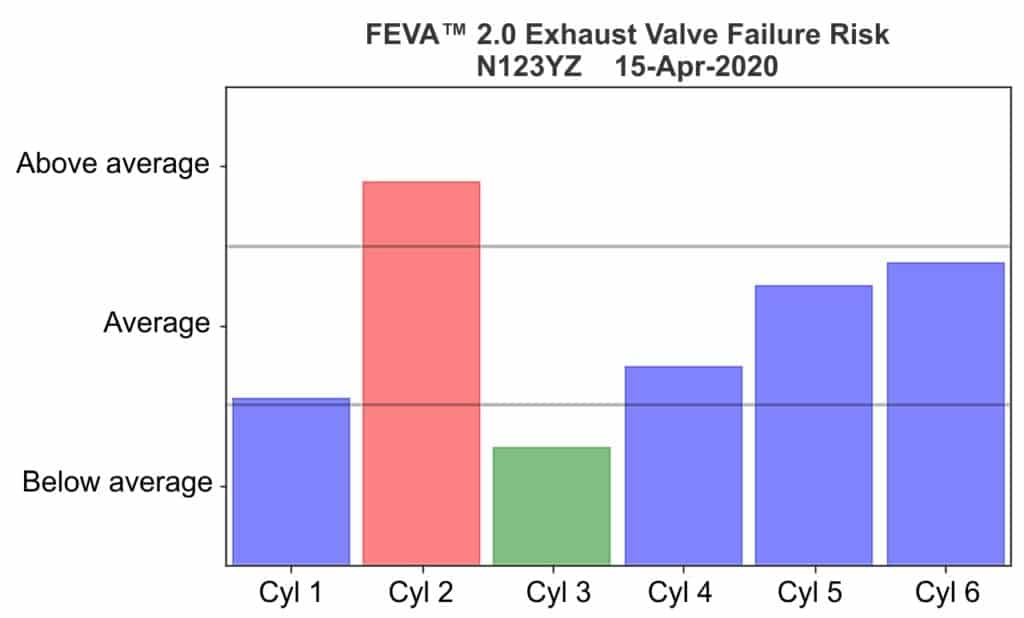
Over the past year, we’ve been developing a new algorithm (FEVA 2.0) that uses machine learning techniques, and we’ve trained the algorithm on thousands of flights involving known-good and known-failing exhaust valves. The result is a significantly higher accuracy rate and fewer false positives than the heuristic FEVA 1.0. By the time you read this, FEVA 2.0 should be fully deployed on the SavvyAnalysis.com platform.
Meantime, we’ve been working hard to develop another algorithm (SEVA) to detect the sticking exhaust valve syndrome that especially afflicts Lycoming engines and is often referred to as “morning sickness.” A sticking exhaust valve typically starts off causing fairly innocuous roughness when the engine is first started cold that goes away as the engine warms up. But if not detected and addressed early, a sticking exhaust valve can progress to the point that it results in a bent pushrod and power loss, and occasionally a valve strike and catastrophic engine failure. It’s obviously important to catch this condition early when it’s still in the incipient stage. This seems like a perfect candidate for predictive analytics, and the preliminary results of our R&D have been very encouraging. By the time you read this, I hope that a beta test version of SEVA will be deployed on SavvyAnalysis.com.
Predictive maintenance is clearly the wave of the future. The more sensors we have in our airplanes, the more comprehensive and powerful it will become. Over time, it will increasingly be our aircraft—not our mechanics—that tell us what maintenance needs to be done.
You bought a plane to fly it, not stress over maintenance.
At Savvy Aviation, we believe you shouldn’t have to navigate the complexities of aircraft maintenance alone. And you definitely shouldn’t be surprised when your shop’s invoice arrives.
Savvy Aviation isn’t a maintenance shop – we empower you with the knowledge and expert consultation you need to be in control of your own maintenance events – so your shop takes directives (not gives them). Whatever your maintenance needs, Savvy has a perfect plan for you: