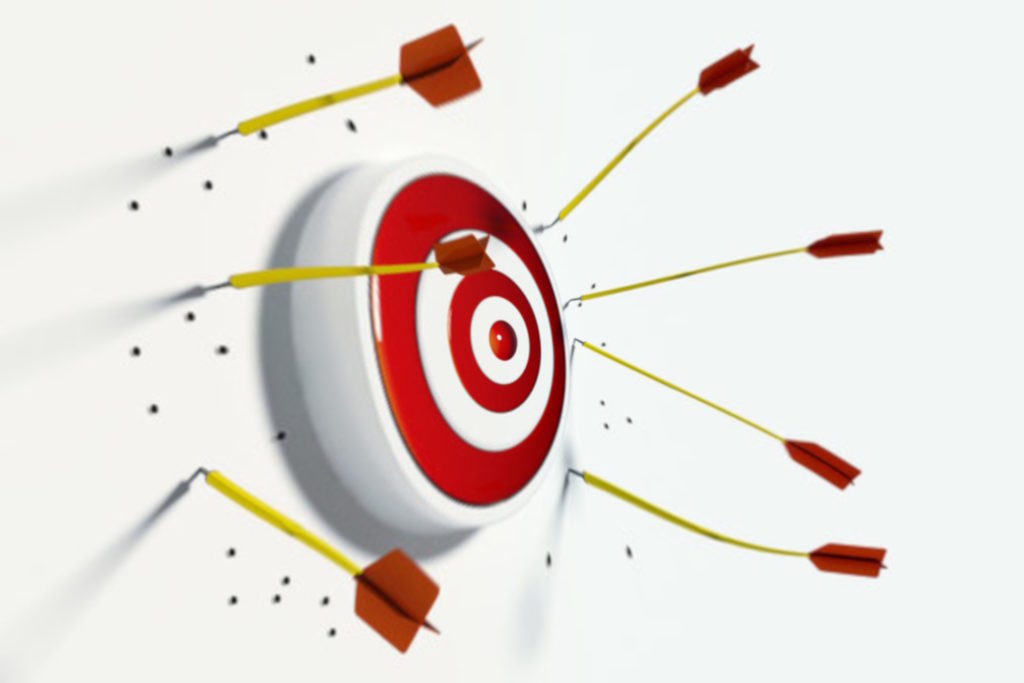
Picture this: For several months, you’ve been suffering from debilitating pain that seems to run from your lower back and radiate into your right upper leg. You report this to your primary care physician, who refers you to an orthopedic surgeon. The orthopod asks you numerous questions about your symptoms, observes you as you painfully limp up and down the hallway outside his examining room, and schedules you for a L4/L5 lumbar fusion. After surgery in which titanium plates, screws and rods are installed to fuse those vertebrae, you endure a difficult four-month recovery period, after which it becomes apparent that your back and leg pain is no better than before the surgery. You schedule a follow-up appointment with the orthopedic surgeon and express your dismay with the disappointing outcome in no uncertain terms. The surgeon scratches his head, strokes his chin, and finally says “hmm, maybe we should do a lumbar MRI to see what’s going on.”
Can you imagine any orthopedic surgeon doing spine surgery first and an MRI afterwards? No, neither can I. Yet I see this happen in GA maintenance shops all the time!
Recently (in the February 2025 issue of AOPA Pilot), I related the story of a Beech F33A whose owner reported the engine ran rough at high power, and the engine monitor “flashed on #6.” His A&P proceeded to change the spark plugs, cleaned the fuel screen and nozzles, and performed a compression check. The problem remained unresolved. The mechanic then disassembled the cylinder #6 valve train and checked the valves, guides and lifters, but still couldn’t find anything wrong. Out of ideas, the A&P reached out to me for advice. I suggested that he dump the engine monitor data so we could analyze it and “see what’s going on.”
Do you suppose a better outcome would have been achieved if the mechanic dumped and analyzed the engine monitor data BEFORE he started attacking the engine with tools? Of course it would! It is always best to gather as much diagnostic data as possible (using non-invasive or minimally invasive methods) and using it to arrive at a well-reasoned diagnosis before taking things apart or replacing things. Putting this off until all attempts to resolve the issue through guesswork and shotgunning have failed amounts to malpractice.
It’s not enough to do the right things. You have to do them in the right order.
Case In Point: The Annual Ordeal
For most of us, the most significant maintenance event happens once a year. It involves an annual inspection by an IA (or for experimentals, an annual condition inspection by an A&P or the builder who holds a Repairman certificate). The purpose of the inspection is to identify any discrepancies that make the aircraft unairworthy (or unsafe), although it often identifies other discrepancies that don’t rise to that level of concern. Generally, the owner is required to have all such unairworthy (or unsafe) discrepancies corrected before the airplane may be flown (other than on a ferry permit). This whole shebang—inspecting for, identifying, and correcting discrepancies—is what I refer to as “the annual ordeal.”
There is a right way to conduct this annual ordeal. It involves a specific series of steps that must be undertaken in the correct order. If these steps are done in the wrong order or if any of them are skipped, the outcome will almost certainly be less than satisfactory. But before we discuss these steps and their proper sequence, let’s take a step back for a moment and look at the big picture.
Under the FAA regulations, aircraft maintenance is a joint responsibility between the aircraft owner and the maintenance provider. The owner’s maintenance responsibilities are described in Part 91 (specifically the rules numbered 91.4xx), and the maintainer’s responsibilities are set forth in Part 43. In particular, Part 91 says (among other things) that the owner is primarily responsible for maintaining his aircraft in an airworthy condition, that he has to have an annual inspection performed every 12 months, and that the aircraft may not be flown again until it has been signed off as airworthy. Part 43 defines (among other things) who may perform maintenance, who may sign it off, what logbook entries must be made, what methods may be used, what quality must be achieved, and the minimum scope of an annual inspection.
There’s a lot to unpack here, so let me reduce it to its bare essentials: Owners are responsible for deciding what maintenance is done, when it is done, and by whom it is done. Maintainers are responsible for performing the maintenance that the owner requests in a satisfactory fashion, and also for performing inspections when requested by the owner and either determining that the aircraft is airworthy or itemizing any specific discrepancies that make it unairworthy.
Sequencing the Annual Ordeal
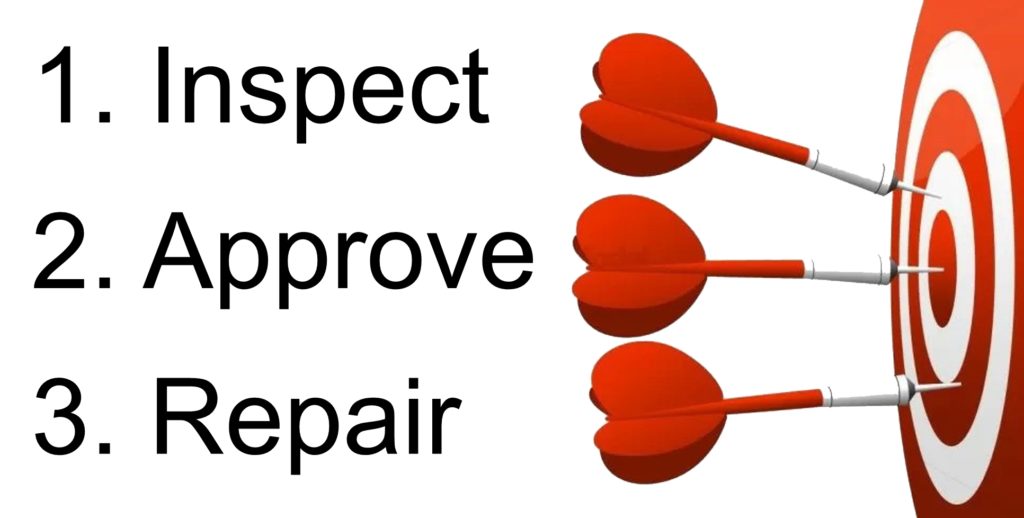
Given these regulatory maintenance responsibilities of owners and maintainers, there’s really only one right way to conduct the annual ordeal. It involves three discrete steps that must be conducted in the correct order.
STEP ONE is the inspection itself. This step is requested and scheduled by the owner and performed by an IA, usually for an agreed-to flat rate. It’s important to understand that this is purely an inspection, nothing more. Its purpose is NOT to make the aircraft airworthy, only to identify any discrepancies that make it unairworthy.
An annual inspection is largely a minimally-invasive visual inspection that involves no disassembly of the aircraft beyond the usual “opening up” (removing cowlings, fairings, inspection plates, seats, carpets, floorboards, etc.) necessary to gain access to the various components to be inspected. The inspection does NOT include repairing or replacing anything. It is just a detailed “looksee” performed in accordance with an inspection checklist, with the inspector keeping careful notes of anything found to be amiss. It also includes a review of the aircraft’s maintenance records to determine whether or not all applicable Airworthiness Directives (ADs) have been complied with.
Once the inspector finishes going through the inspection checklist and AD research, he writes up his findings in the form of a discrepancy list. For each identified discrepancy, the inspector normally recommends some corrective maintenance action to resolve the discrepancy and an estimate of what that action will cost. The discrepancy list should also clearly identify which discrepancies the inspector considers to be unairworthy items. Nowadays, all this is usually documented in the form of a computerized work order that should be presented to the aircraft owner.
STEP TWO is the review and approval phase, during which the aircraft owner reviews the list of discrepancies, recommended corrective actions and cost estimates. During this phase, the owner may pose questions to the mechanic, perform research, and seek outside advice and second opinions. Ultimately, the owner goes back to the inspector with specific direction as to which of the recommended maintenance actions are approved and which are declined.
In the 16 years that my company has been managing annual inspections on behalf of thousands of GA aircraft owners, it is quite routine for us to decline half of the recommended maintenance actions and approve the other half. There have been some cases where we’ve declined two-thirds of the recommendations and approved only one third. I’ve never seen a case where we “rubber stamped” the shop’s work order and approved everything.
There are lots of reasons for an owner to decline maintenance tasks recommended by the shop. It might be a non-airworthiness discrepancy that the owner feels isn’t worth worrying about. It might be one that the owner wants to defer to a later date. It might be one that the owner wants to have addressed by a different facility—perhaps an avionics shop, engine shop, or sheet metal shop.
It might be one that the owner wants corrected but in a different fashion than what the shop has proposed—perhaps the shop recommended replacing a defective component with a new one from the OEM, but the owner wants to use a less expensive PMA part or possibly a serviceable part from a salvage yard. It might even be one that the inspector has identified as an airworthiness discrepancy but the owner disagrees—perhaps the shop wants to overhaul the prop or engine because it’s past TBO
At the conclusion of this step, the owner provides the shop with explicit authorization to perform certain corrective maintenance tasks and clear instructions as to what work he does NOT want done. This should always be done in writing—never verbally—to ensure there can be no miscommunication or misremembering.
STEP THREE is the corrective phase, during which the shop performs the requested repairs in accordance with the marching orders received from the owner. The owner’s expectation is that this work will be done within the cost estimates provided by the shop in Step One. Should the shop run into unanticipated difficulties that would cause the cost to significantly exceed the shop’s estimate, it should stop work on the task, provide the owner with a revised estimate and explanation, and wait for the owner to approve the new estimate before resuming work on the task in question.
Ready, Fire, Aim
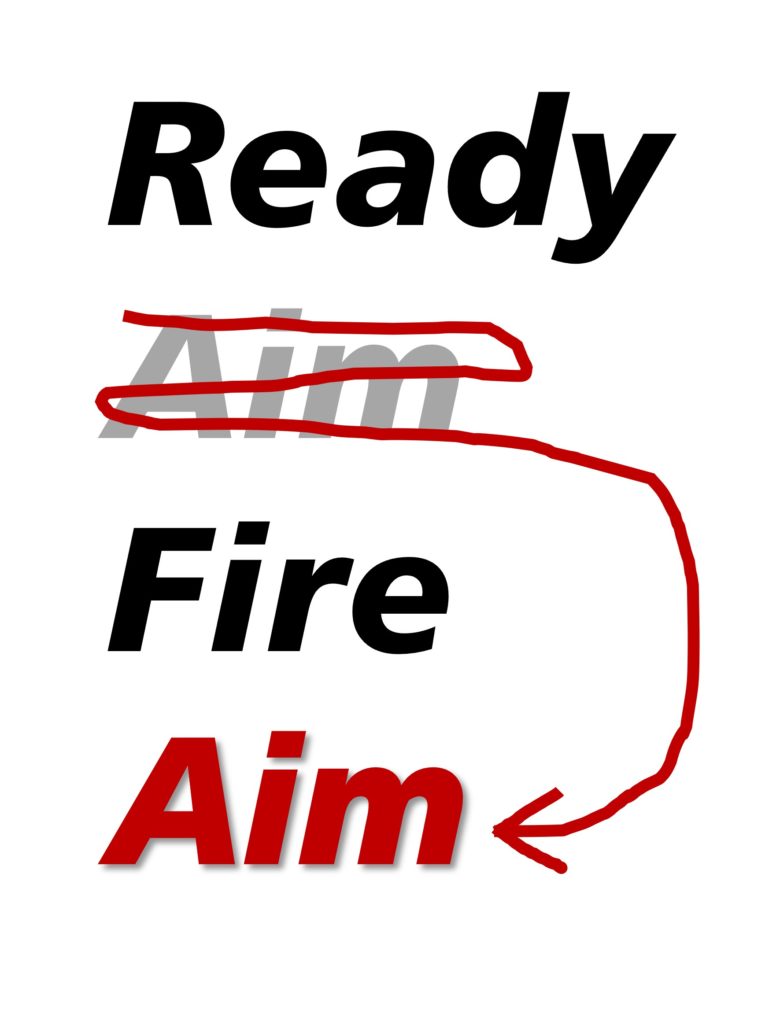
Unfortunately, a lot of annuals don’t follow this three-step process. I’d guess that the majority don’t. There are a number of ways that this process can go off the rails.
It’s common to see Steps Two and Three reversed. The shop performs the inspection, creates a discrepancy list, and then ASSUMES that it’s authorized to correct all the discrepancies that the inspection uncovers. The shop then presents the work order to the owner as a fait accompli and labels it as an invoice. By the time the owner sees the discrepancy list, the corrective actions have already been accomplished. Not good.
In this common scenario, the owner is often shocked and upset by the invoice total. The owner may even dispute the invoice amount, but that’s often an exercise in futility because the work has already been done and the shop is entitled to be paid for it. If the owner balks at paying the invoice, the shop may hold the aircraft hostage and—if the invoice remains unpaid—go to court to obtain a mechanic’s lien. Most of the time, the owner doesn’t have a leg to stand on legally speaking.
Another common (and even worse) scenario is where the shop merges Steps One and Three like shuffling a deck of cards. The aircraft is inspected and any discrepancies found are fixed right on the spot. The result is something I call “inspect a little, fix a little, lather, rinse, repeat” in which there really isn’t a discrepancy list created, just a list of work accomplished. This methodology is very convenient for the shop, but it cuts the owner completely out of the decision loop by making Step Two impossible. Owners should never allow this to happen. It is anathema.
Ensuring Proper Sequencing
The very best maintenance shops conduct annual ordeals using the three-step protocol, but in my experience the majority of shops and mechanics don’t unless the owner takes steps to make sure it’s done that way. Things often go awry when an owner schedules an annual ordeal at a new shop, assuming they will use the same procedures as the prior shop and getting blindsided when they don’t. I’ve even seen cases where an owner has used the same shop for many years with no surprises until the year he receives an over-the-top invoice that includes costly work he would never have approved if asked.
To protect yourself against such unpleasantries, when you put your plane in the shop for its annual ordeal you should always make it explicitly clear (preferably in writing) that you are authorizing the shop to perform an annual inspection at the agreed-to flat rate and to prepare a discrepancy list with recommended repairs and cost estimates, but you are NOT authorizing the shop to perform any repairs or to purchase any repair parts. Your authorization to perform repairs and order parts will come only AFTER you have had the opportunity to review the inspection findings, repair recommendations and cost estimates.
Many owners tell their shop to “do whatever it needs,” effectively giving the shop a blank check. Never do this! It’s an engraved invitation for the shop to over-maintain your aircraft to the detriment of both your plane and your bank account. In my experience, an owner who lets his mechanics make fix-or-defer decisions rather than making those decisions himself can double his annual maintenance cost.
Always remember that as an aircraft owner, it’s your responsibility to decide what maintenance is done, when it is to be done, and by whom. It’s your mechanic’s responsibility to ensure that the work you ask him to do is done in a satisfactory fashion, and once a year to inspect it to determine whether or not it is airworthy. Don’t abdicate your maintenance decision making responsibilities to your mechanic. If you do, you might not like the outcome.