“Would you please take a look at my October 21 flight?” Matt posted on a SavvyAnalysis ticket. Matt owns a Glasair Sportsman 2+2 powered by a Lycoming YIO-390-EXP experimental engine.
“At about 50 minutes into the data, I was doing a preflight mag check,” Matt continued, “and it looked like EGT #2 was dropping instead of rising the way the other three EGTs were. I seem to recall from one of Mike Busch’s webinars that this indicates something’s wrong, but I don’t recall exactly what.”
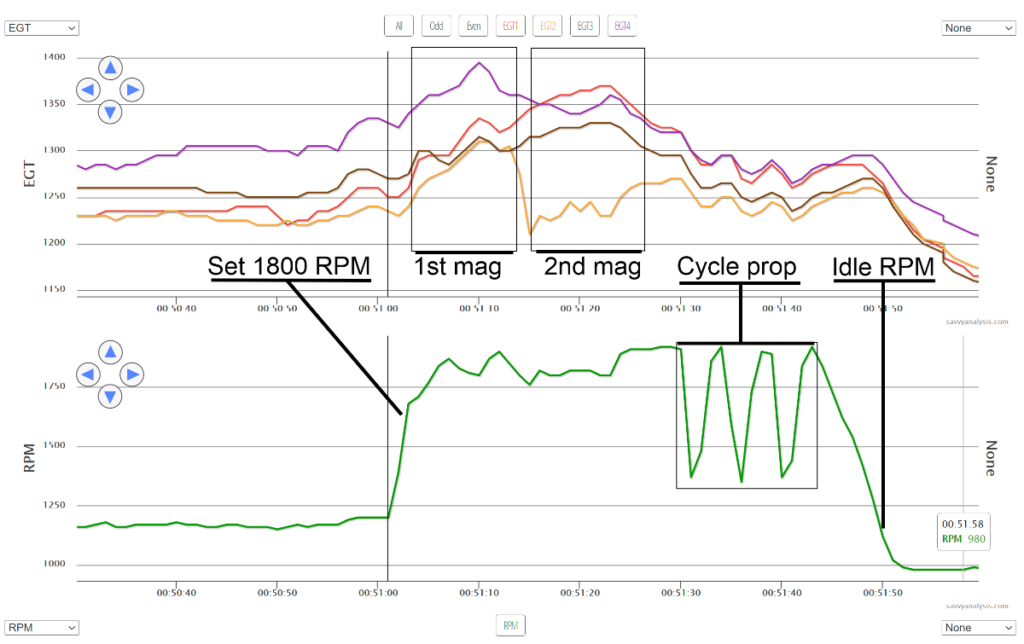
“When EGT drops during single-mag operation the way it did during your preflight,” replied Savvy’s chief analyst Joe Godfrey, “it usually indicates a weak or nonexistent spark on that plug. The good news is that EGT #2 looks okay in flight under higher power, so it might have just been a fouled plug that cleared itself when you applied takeoff power.”
“Your mag check was so quick that the sensors didn’t really get a chance to settle down,” Joe told Matt. “At your convenience, could you please perform an in-flight LOP mag check in accordance with Savvy’s Flight Test Profile? That will give us a lot more diagnostic information about the condition of your ignition system.”
Matt explained that it was low IFR that morning, and that he would be out of town for the next week or so, but promised to fly the test profile after he returned and upload it to the SavvyAnalysis platform for Joe to look at.
Flight Test Profile
About 10 days later, Matt posted, “I was able to do the in-flight mag check per the Savvy flight test procedure and have uploaded it for your review. The test is from 1:11 to 1:23 (log time).”
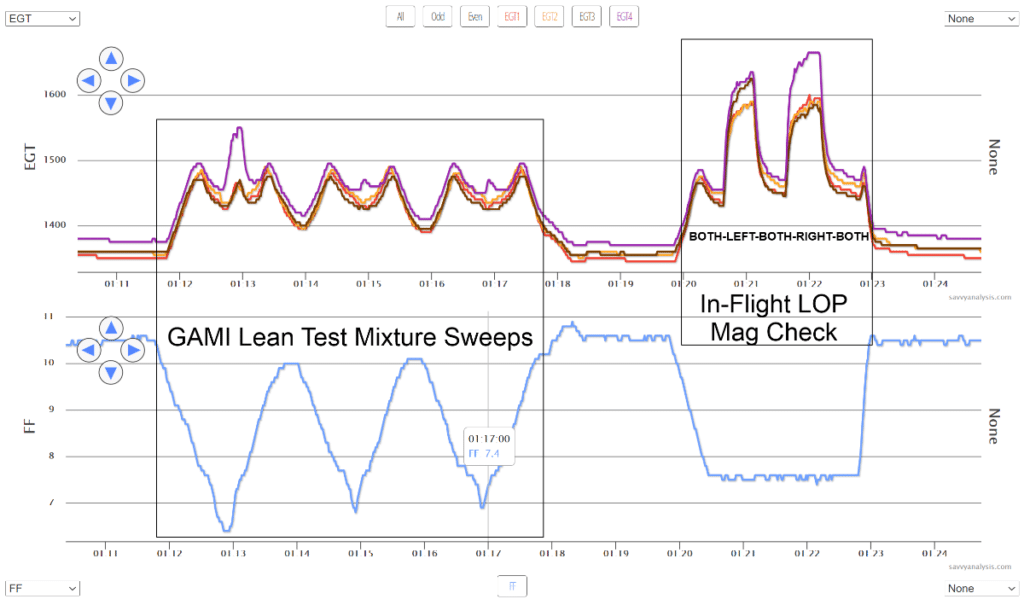
“During the first and third mixture sweep of the GAMI lean test, I noticed that when I got extremely lean (fuel flow 6.4 GPH) EGT #4 popped up. Why was that, and should I be concerned?”
“I also noticed that during the LOP in-flight mag check, EGT #4 popped away from the other three EGTs while I was running on the right mag during the BOTH-LEFT-BOTH-RIGHT-BOTH sequence. This is interesting since it was EGT #2 that looked abnormal during the original preflight mag check that I asked you to look at.”
The Plot Thickens
And then things got more interesting: “A while after completing the test (at about 1:51 into the flight) the engine suddenly “burbled” (for lack of a better word) which really got my attention.
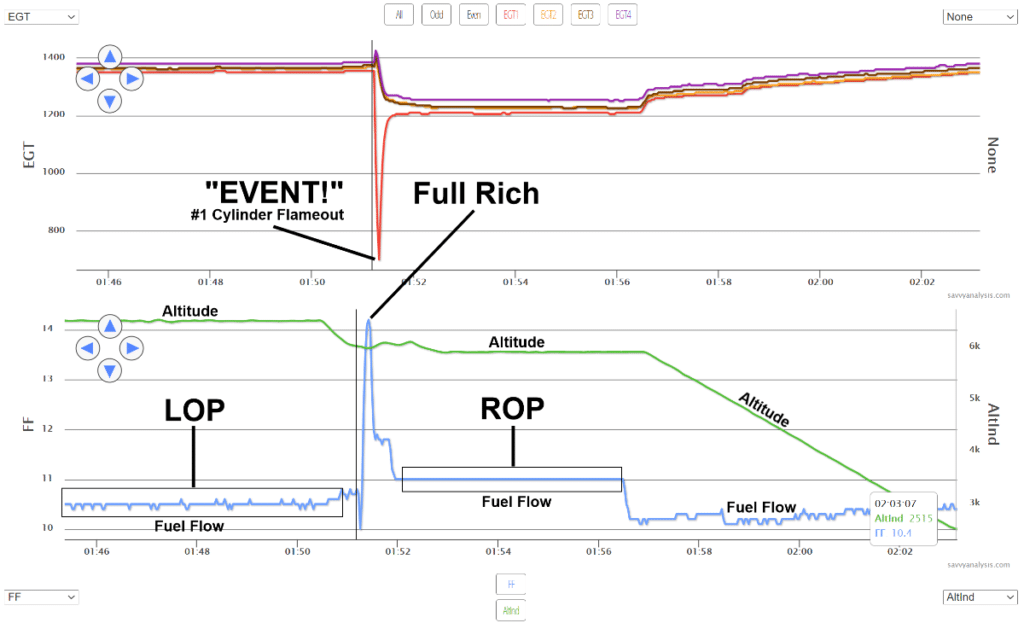
“My response (as you can see from the FF) was to go full-rich, then turn toward my home airport and start a descent. The engine seemed to run fine after that, but I’m obviously concerned about what caused the abnormality. Any thoughts?”
“So now let’s see … We had the original runup where EGT #2 seemed abnormal, then the flight test profile in which EGT #4 seemed different, and now EGT #1 going cold during the “burble” event. Is cylinder #3 the next one to act up? It’s the only one left!”
Interpreting Data
“Lots to process there,” replied Joe. “Let’s start with the GAMI lean test, where you noticed EGT #4 starting to rise during the mixture sweeps when the mixture got extremely lean. That’s normal behavior, the extremely lean mixture slows down the combustion event so much that it hasn’t quite completed when the exhaust valve starts to open. Nothing to worry about. Your GAMI spread looks good, it’s 0.5 GPH or less on all the sweeps.”
“The in-flight LOP mag check also looks pretty normal,” Joe went on. “Just a bit of asymmetry there. Does your YIO-390-EXP have standard magnetos, electronic ignition, or one of each?”
“Conventional Slick 4300-series magnetos,” Matt said.
“Well then, it’s possible that the two mags aren’t timed exactly the same,” Joe said, “but the asymmetry isn’t enough to worry about. Just check the timing again next time it’s convenient.”
“What about the burble event?” Matt asked. “That one has me concerned.”
“I’ve been thinking through the possibilities,” said Joe. “I don’t think it was an ignition problem, those usually result in EGT going up and not down. I don’t think it’s valve sticking, it would be unusual for a valve to stick in such a brief and isolated way. That leaves a fuel problem. Too much fuel (flooding) seems unlikely since the cylinder immediately re-lit when you went to full-rich mixture. Too little fuel seems more likely. I’m thinking it might have been a partial #1 fuel nozzle clog that caused the cylinder to flame out, and when you went full-rich the increased fuel pressure cleared out the clog. I can’t be certain that’s what happened, but that’s my theory and I’m sticking to it.”
Going Beyond the Data
Because Matt was a SavvyQA consulting client, Joe decided to bring in one of Savvy’s account managers, Brandon Thompson A&P/IA to follow up with Matt concerning the burble event.
“When you turn a 4-cylinder engine into a 3-cylinder engine at 2500 RPM, it tends to be pretty violent,” Brandon said to Matt. “You described it as a ‘burble’ but I’m assuming it was pretty shaky during that moment, right?”
“Yes, it was pretty violent,” replied Matt, “to the point I was thinking about catastrophic engine failure for a dozen seconds or two, and looking for an emergency landing location.”
Brandon asked Matt to give him some background on the engine, including:
- Any cylinder work since the engine was new 8 years ago?
- What type and brand of spark plugs are installed? Can you provide photos of what they look like (before you cleaned them)? Have you checked them for resistance?
- Can you check the magneto-to-engine timing and post the results?
- Can you perform a borescope inspection of the cylinders and upload photos of what the valves and cylinder walls look like?
- Can you remove the fuel nozzles and inspect them for debris? Also, with the nozzles removed, can you place clear plastic cups beneath each of the fuel nozzle feed lines, run the boost pump for 20 seconds, and then inspect the contents of the cups for debris?
- Have you noticed any signs of “morning sickness” (rough running right after engine cold start) that might indicate a valve sticking problem?
Matt indicated that there had been no cylinder work on the engine since it was new. The compressions at the last annual were 76/78/76/78 but the cylinders were not borescoped. The spark plugs are Tempest UREB37E projected-nose massive plugs that have 80 hours on them, and resistance was checked at the annual. The magnetos received 500-hour IRANs at Aircraft Magneto Service (one of Savvy’s favorite mag shops) about 200 hours ago.
“I’ve contacted my A&P to see if he can help me accomplish the borescope inspection, fuel nozzle checks, and spark plug photos. I’m looking forward to trying out my new borescope!”
About three weeks later…
“Brandon, I had a great time working with my A&P to get this stuff done,” Matt reported. “We cleaned, gapped, and measured resistance on all the spark plugs (the resistances ranged from 680 to 1230 ohms). We removed, inspected, cleaned, and flow-checked the fuel nozzles. Also changed the oil from Aeroshell W100 (summer oil) to Phillips X/C 20W-50 (winter oil).”
“We found some minor contamination on the lower spark plugs of cylinders #1, #2 and #3 but nothing really significant. However, in cylinder #4 we found:
- Considerable contamination on the lower spark plug.
- Blackening of the upper spark plug.
- Partial clogging of the fuel nozzle.
- Fuel staining noted on intake tube during post-maintenance runup. Removed and replaced the intake manifold gasket. No leakage noted on subsequent runup. A&P noted that this could have been an induction air leak.
“I dumped and uploaded the data after the post-maintenance test flight, and noticed that the EGTs are tracking one another much more closely now,” noted Matt.
“It sounds like you’ve made some good progress,” replied Brandon. “I’ve reviewed the borescope images you took, and besides some minor oil control issues and a lot of minor corrosion pitting on the cylinder walls, I don’t see any issues that concern me.”
“Your comment about cylinder wall corrosion certainly got my attention,” Matt said. “Is there something remedial that I need to do to deal with this? Going forward, after watching yet another Mike Busch webinar, I just purchased a Black Max engine dehydrator that I’m now using while the plane is hangared. I’m still not sure what to do when I put the airplane on floats and park it on the water during the summer (June to October). Thoughts?”
“Cylinder wall corrosion isn’t something you can remedy once it occurs,” said Brandon, “but the dehydrator is a great idea of which I wholeheartedly approve. As for the time the aircraft will be living on the water, I would suggest using a 5% concentration of ASL CamGuard in your oil (if you’re not already doing so). You can use as much as 10% concentration if the airplane is going to be inactive. You can also add some Phillips Anti-Rust oil. If the plane is going to be really inactive, you can install desiccant plugs in place of the top spark plugs and put desiccant bags in the engine intake and exhaust (although doing that is probably not easy when the plane is on the water.”
Matt indicated that he’d recently started using CamGuard after viewing yet another Mike Busch webinar, and he would be using it consistently going forward.
“Hi Brandon,” Matt posted a few weeks later, “I’ve been flying so much that I haven’t had time to follow up with you. Everything is running great. I’m really happy that you suggested that we pull the spark plugs and borescope the cylinders. When we inspected the plugs and found the fouling, I think that was the root cause of the troubles I was having. Also my sharp eyed mechanic noticed a blue streak on the #3 cylinder intake manifold from which he concluded that that gasket needed to be replaced so we may also have had a small induction leak there. I just love being able to view my engine data on the SavvyAnalysis platform, and I’ve been using it to find my ROP, Peak, and LOP fuel flows for various MP/RPM combinations so I can cleanly execute the ‘big mixture pull.’ Both my engine and I really appreciate your help!”
As a SavvyQA consulting client, Matt had immediate and unlimited access to maintenance wizards like Joe Godfrey (unquestionably the most experienced piston aircraft engine data analyst in General Aviation) and Brandon Thompson A&P/IA (one of Savvy’s most skillful diagnosticians) to help him get to the bottom of a serious problem (the ‘burble’ event), and to help put his mind at ease about several other things in his engine data that turned out to be perfectly normal.
Wouldn’t you feel more confident knowing that experts like Brandon and Joe were available to you any time you had a question?
You bought a plane to fly it, not stress over maintenance.
At Savvy Aviation, we believe you shouldn’t have to navigate the complexities of aircraft maintenance alone. And you definitely shouldn’t be surprised when your shop’s invoice arrives.
Savvy Aviation isn’t a maintenance shop – we empower you with the knowledge and expert consultation you need to be in control of your own maintenance events – so your shop takes directives (not gives them). Whatever your maintenance needs, Savvy has a perfect plan for you: