Continental has a CHT redline of 460º. Lycoming’s beefier head-to-barrel construction and sodium-filled valves push their CHT redline to 500º. If you had a detonation event that sent one cylinder’s CHT past the redline – you know exactly how long and how much higher thanks to the engine data – would you have qualms about keeping that jug in service? Would it depend on the subsequent performance? Maybe on the borescope results?
We’ve seen cases where a detonated jug later fails at the head-to-barrel junction. “Later” is anywhere from the next flight to months after the initial event. Lots of things in life have some wiggle room. Data suggests that CHT redlines are not negotiable.
First up is a Cessna 182 powered by a Lycoming IO-540 and data from a Garmin G1000 with a one second sample rate. Here are EGTs, CHTs and FF for a typical 90 minute flight with the cursor about halfway through cruise.
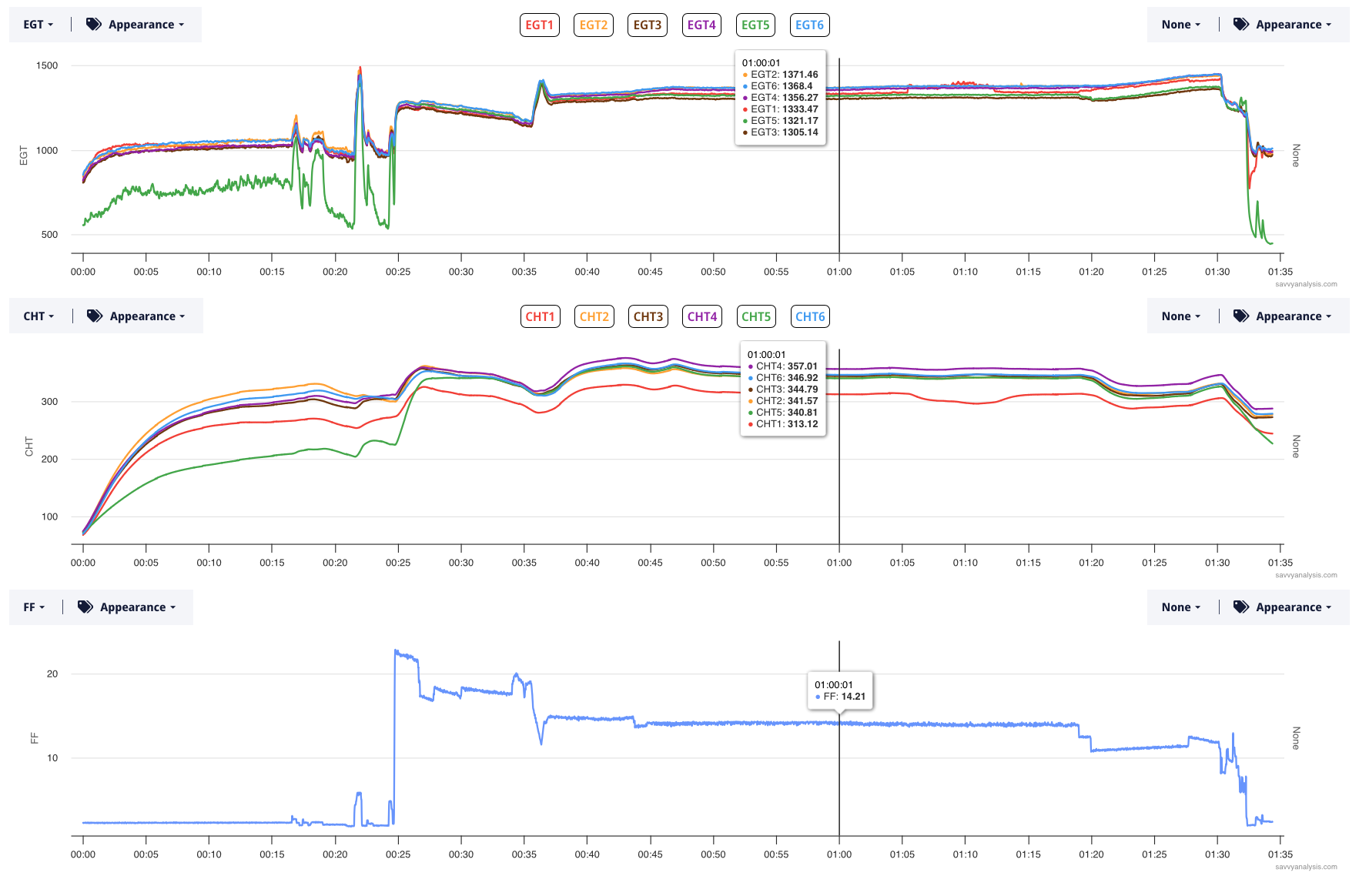
CHT 1 is low throughout – probably because cylinder one is using the bayonet probe to feed the legacy CHT gauge and the G1000 is using a spark plug gasket probe. Just to the right of the cursor there’s an excursion in EGT 1 that looks like a plug misfiring. We think it’s real and not bogus data because CHT 1 drops there. But the bigger problem, of course, is cylinder 5 at idle power. It’s the classic signature of a sticky valve. Here’s the previous flight.
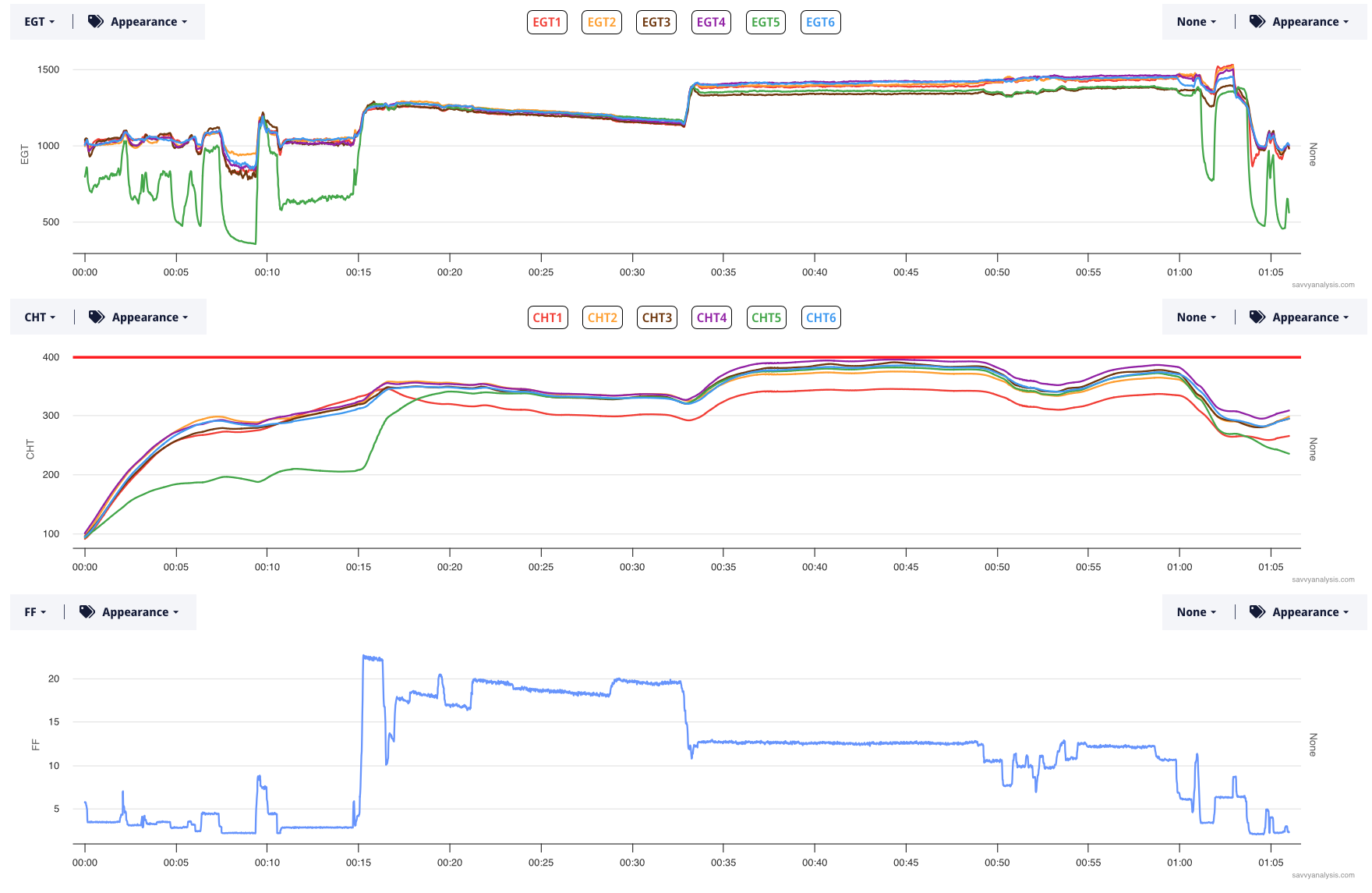
Keep in mind that FEVA 2.1 looks at cruise segments of your flight data. We see more sticky valves at engine start- a.k.a. morning sickness – than in-flight. So your FEVA report is not going to flag this sticky valve because it’s looking at cruise data. We’re working on an algorithm that will flag sticky valves. Meanwhile, the best ounce of prevention is to take a look at data for each of your flights, especially if you encountered roughness during idle.
Next is a Morrisey 2150 powered by a Lycoming O-320 and data from an Insight G2 with a 2 second sample rate. We used to have two Varga Kachinas on my field doing “Top Gun” fun flights, and I think this is the same design. Here are EGTs. CHTs and FF for a recent flight.
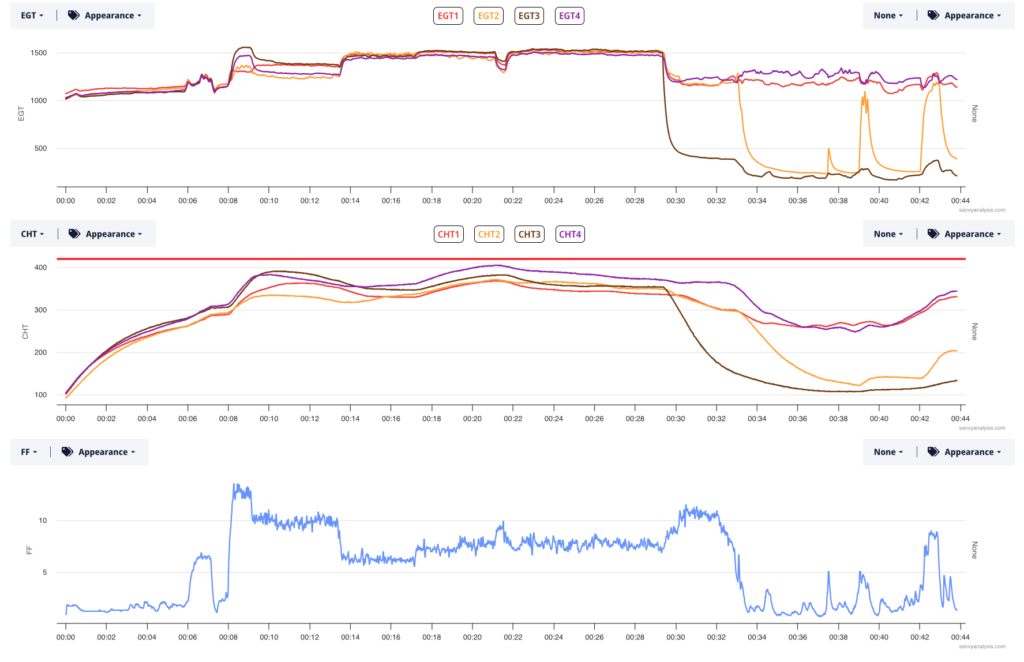
This scenario is pretty much the mirror image of the earlier Cessna. There the problem was during idle and the valve worked OK in flight.
Here, the valve didn’t stick during idle or climb and ran for about 15 minutes in cruise before failing. We had borescope images from the previous annual last September which showed no signs of asymmetrical heating or green spots.
When the valve failed it banged around in the cylinder for a while and carved up the piston dome.
The pilot was able to nurse the plane to the nearest airport and all walked away.
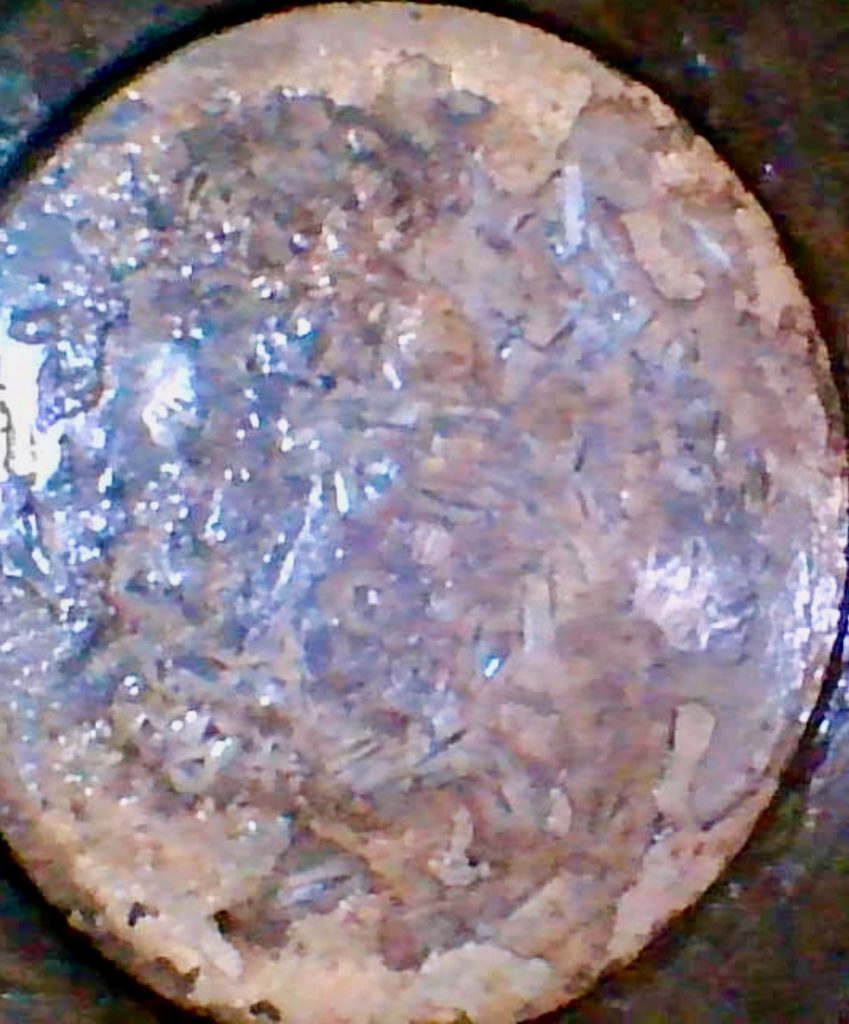
Next is a Cirrus SR22 powered by a Continental IO-550 with data from an Avidyne Entegra with a 6 sec sample rate. Here are EGTs, CHTs, and FF from a flight about 6 months ago. Cursor is on the detonation event.
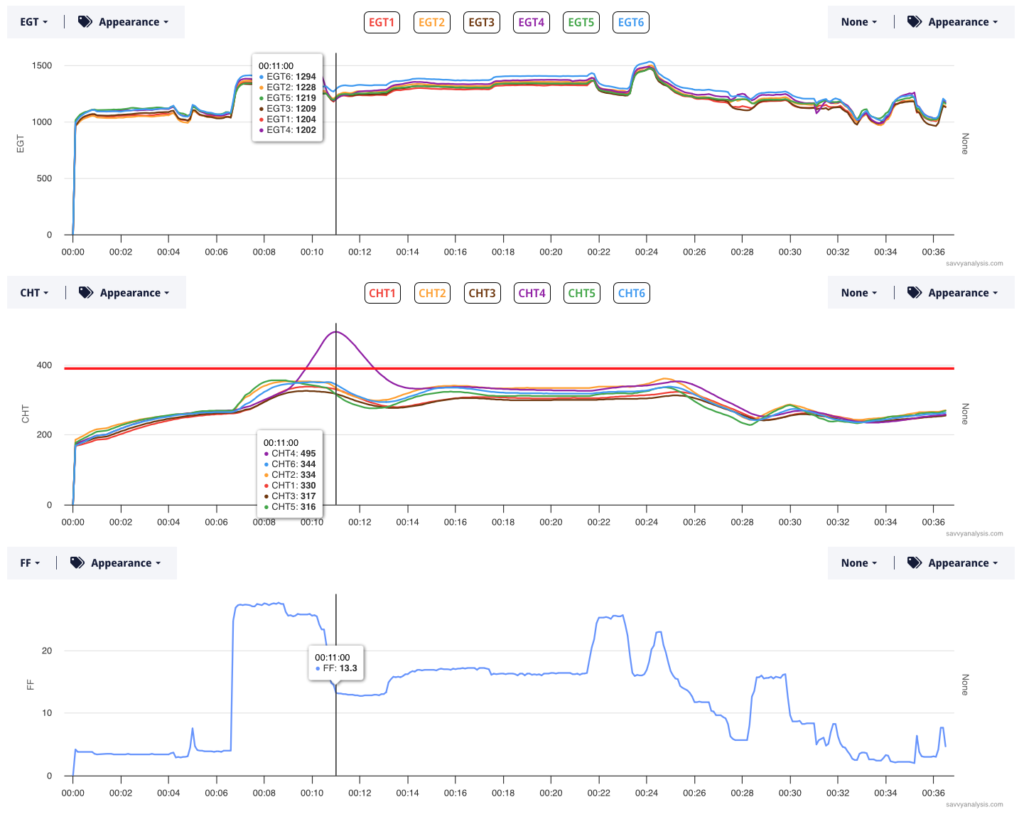
If we believe the CHT gauge – and there’s no reason not to – CHT peaked at 495°. Total time above 400º was about 3 minutes and total time above Continental’s redline of 460º was about 90 seconds. The pilot continued on and landed uneventfully. Seems like the very least you should do after an event like this is to borescope the cylinder. That was done and we observed some “chatter” around the piston circumference. It wasn’t so bad that the only option was to remove the cylinder from service. It was in that grey area where you balance the hassle and the risk and the cost of removing the cylinder versus keeping it in service with a watchful eye.
The engine data from the flights after the detonation event until recently didn’t show a problem with cylinder 4. Here’s a sample.

One clue is that CHT 4 moved down from the middle of the pack to second lowest. Not really a “smoking gun” of evidence but a clue that 4 wasn’t making as much power post-event. In mid-February we got a borescope analysis request with these three pictures of cylinder 4’s dome and barrel.
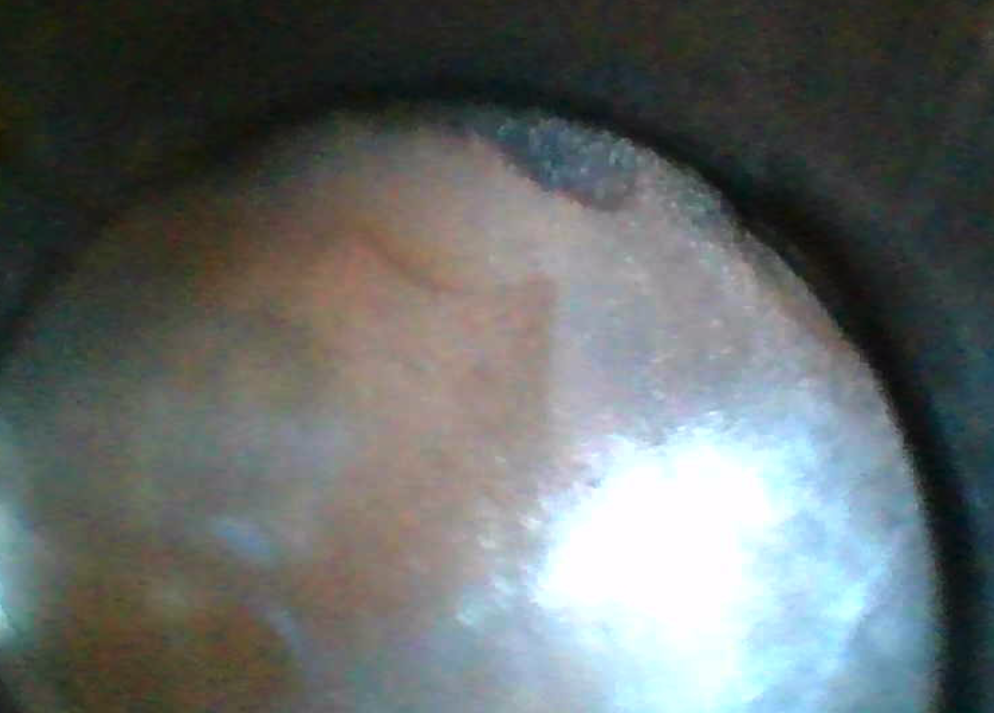
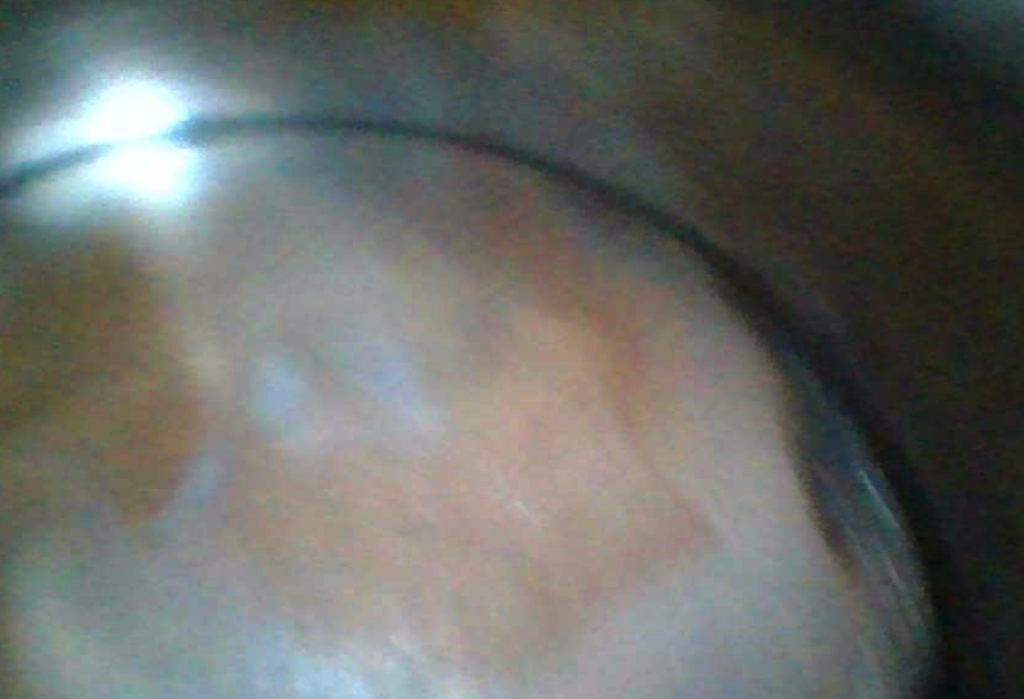
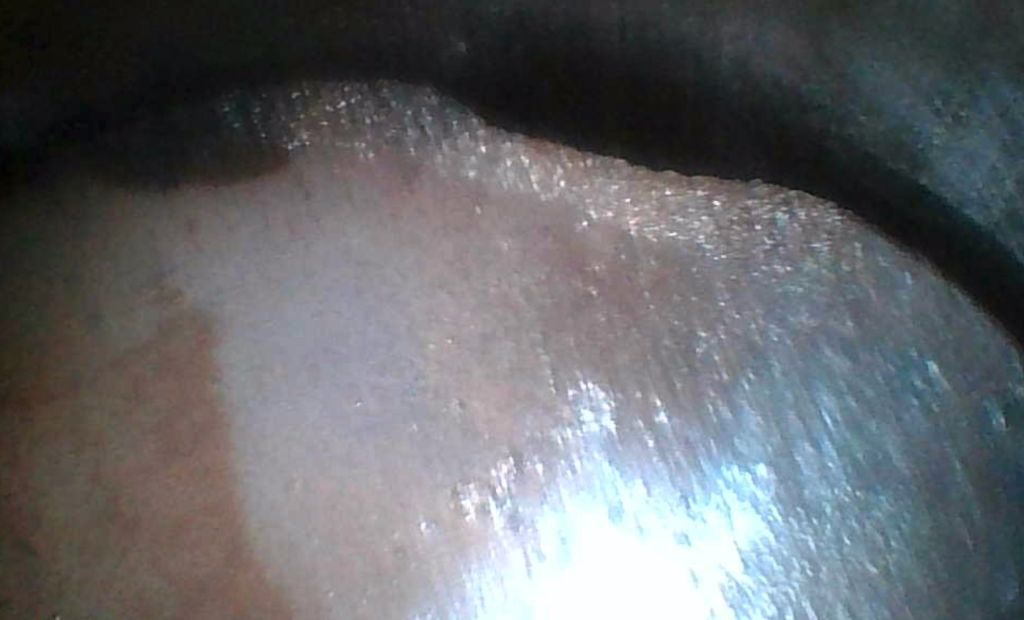
It looks like more time in service has not been kind to this dome and it’s hard to make a case for continuing in service, even if it’s making its numbers.
We’ll finish this month with a Piper Cherokee powered by a Lycoming O-360 and data from an Insight G2 with a 2 second sample rate. Here are EGTs, CHTs and FF from a recent flight.
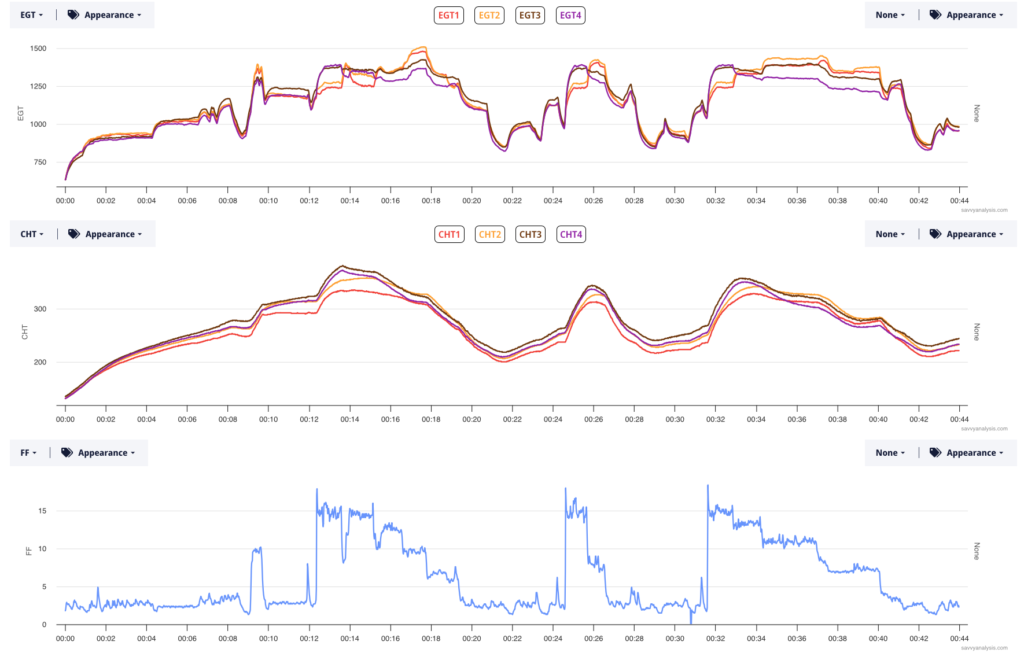
The report was misfires, stumbling. and hard starting. OAT is not depicted but it’s in the range where carb ice is possible. Another possibility is mixture distribution. At 12, 24 and 32 mins when FF goes to max, EGTs diverge into 3-4 going high and 1-2 going low. CHTs 3 and 4 follow EGTs 3-4 higher at max FF. Then EGT rank changes when FF is reduced.
For the hard starting, that’s often a sign of mag trouble. Poor idle mixture is another possibility, but that had been ok until recently and hadn’t been adjusted. Mags had been OH’d 9 months previous, so neither in that “just OH’d” category or in that “probably time for OH” category. Here’s what the owner reported —
My A&P had the same trouble starting it that I did, and same as with me, it would start on the back kick when releasing START to BOTH. As you probably know, in START, the right mag is locked out and only the left mag, with impulse coupler, engages. Releasing START engages both mags and the right alone can then fire the engine if there is enough remaining momentum.
Funny thing is that the run up on the day of my flight seemed normal. Funnier still is that a couple of flights before I did the Savvy GAMI lean test of the mags at altitude, sent the engine data into Savvy, and they pronounced good functioning. And… even yet still funnier, both mags were rebuilt 9 months ago at last annual.
One of the internal gears on the right mag failed (broke some teeth). So, when it failed in flight it showed up as misfiring which gave the stumbling effect, rather than simply a one-mag drop. Also, during the course of the subsequent installation of the repaired right mag, my A&P discovered that the P-leads had been cross-wired, so that instead of cutting out the right mag during START, the left mag with the impulse coupler was cut out, thus accounting for the additional observation of hard starting.