George was flying his trusty old 1960 Cessna 182 from its Southern California home base to Lake Tahoe when—about halfway through the planned three-hour flight while cruising at VFR at 10,500 feet over the Mojave Desert just northwest of Edwards Air Force Base—he observed the Skylane’s oil pressure gauge was reading ZERO! He quickly concluded that he needed to put the aircraft on the ground ASAP.
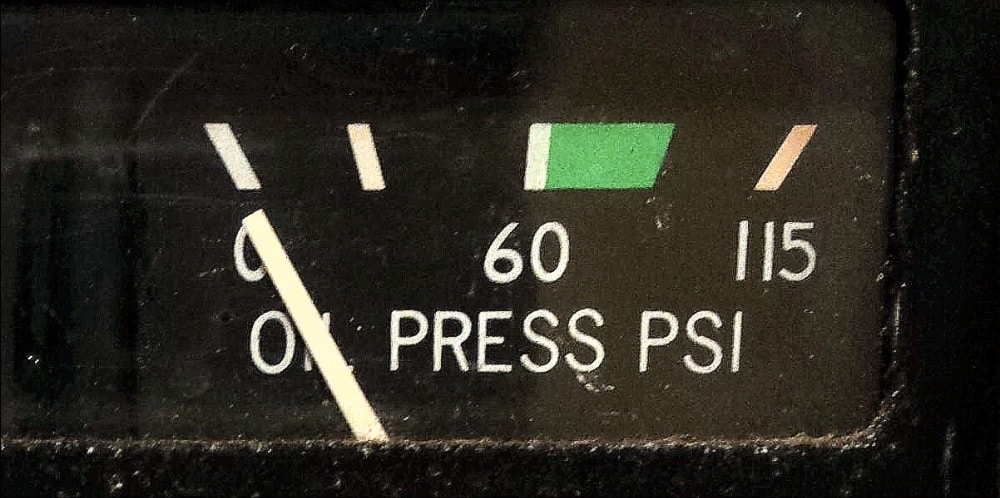
He had just passed Mojave Airport (KMHV), and quickly turned back toward it while reducing power to minimize engine damage and descend to the airport’s pattern altitude of 3,800 feet. The landing was uneventful. The engine seemed to be running fine despite the aberrant oil pressure reading. As George taxied to transient parking, he figured this was most likely just an indication problem and that the oil pressure gauge must be lying.
All that changed after George shut down the engine and egressed the aircraft to find the belly completely covered and dripping with oil. He checked the dipstick and found no oil adhering to it. Now he was seriously worried.
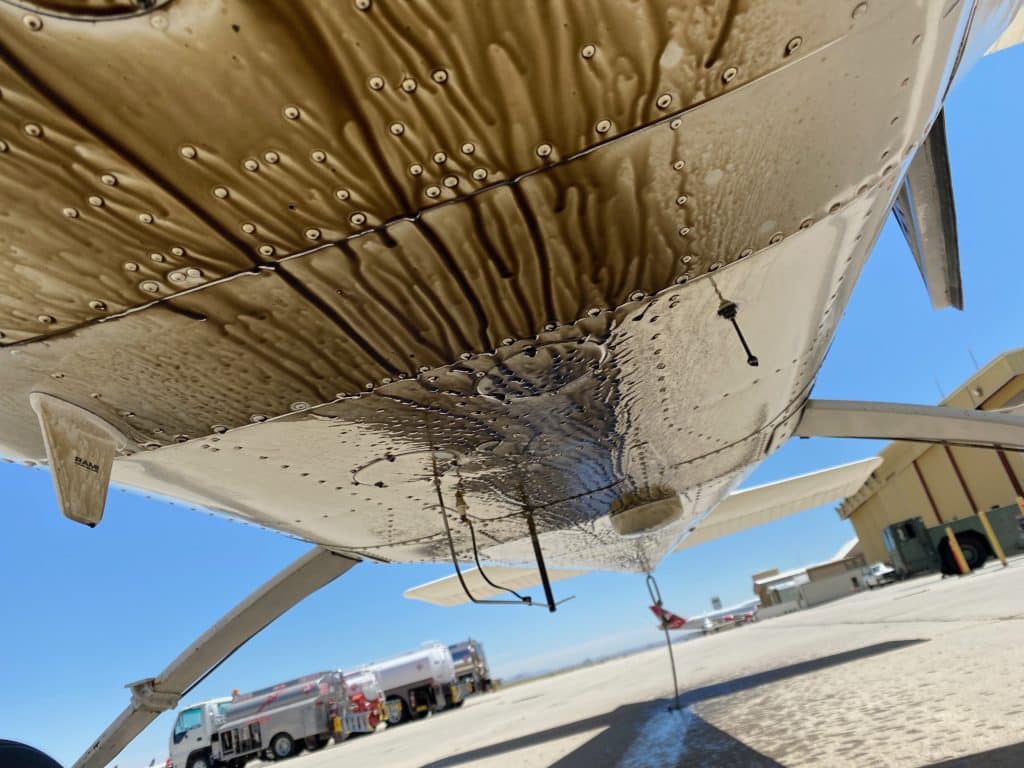
George started searching for a maintenance shop or mechanic on the field, but he came up dry. Despite MHV being the home of Burt Rutan’s company Scaled Composites as well as hundreds of mothballed airliners, it seemed that there were no maintenance resources anywhere on the airport.
Now George started to feel seriously stranded and a little freaked out. He wasn’t sure what to do next. Then he remembered that he’d enrolled his Skylane in Savvy’s 24/7 breakdown assistance program, so he called the toll-free hotline and explained his predicament. Within minutes, George received a callback from Jeff Iskierka, Savvy’s Technical Director and a veteran A&P/IA.
Jeff asked George to go over the symptoms—in-flight loss of oil pressure, power reduction and landing within 10 minutes, no loss of power or abnormal engine noise, oil-covered belly, no oil visible on the dipstick—and to text some smartphone photos of the oil loss. Jeff warned George not to restart the engine until the cause of the oil loss was investigated.
Jeff searched Savvy’s database of maintenance resources and located a few A&Ps who might be called upon to help if necessary. George turned out to be a pretty maintenance-savvy hands-on owner who routinely performed his own oil changes and other preventive maintenance. Ultimately it was decided that Jeff would guide George through an initial investigation, and then call in an A&P only if necessary.
George had already determined that both the oil filler cap and oil sump quick-drain were secure. Jeff huddled with other members of Savvy’s technical team, and the consensus verdict was that there were very few other ways a Continental O-470 could lose so much oil in flight.
One possibility was if the engine had been modified by replacing the oil pressure screen with an adapter for a full-flow spin-on oil filter. These oil filter adapters have a history of vibrating loose, and some have a repetitive Airworthiness Directive against them requiring a regular torque check. Jeff asked George about this, and George confirmed that his engine did indeed have an STC’d Tempest oil filter adapter installed, and that he’d replaced the spin-on filter at the last oil change. Jeff told George that the security of the oil filter adapter should be the first thing to check once the engine cowling was removed.
Meantime, George called the owner of an excellent engine shop in Southern California for a second opinion. The engine shop owner strongly urged that the engine be removed from the aircraft and torn down to inspect for damage. This would clearly be a very expensive thing to do, and George asked Jeff whether he thought it might be covered by the Skylane’s hull insurance. Jeff discussed this with the Savvy team and reported back to George that it was quite unlikely that such an engine teardown would be covered by insurance.
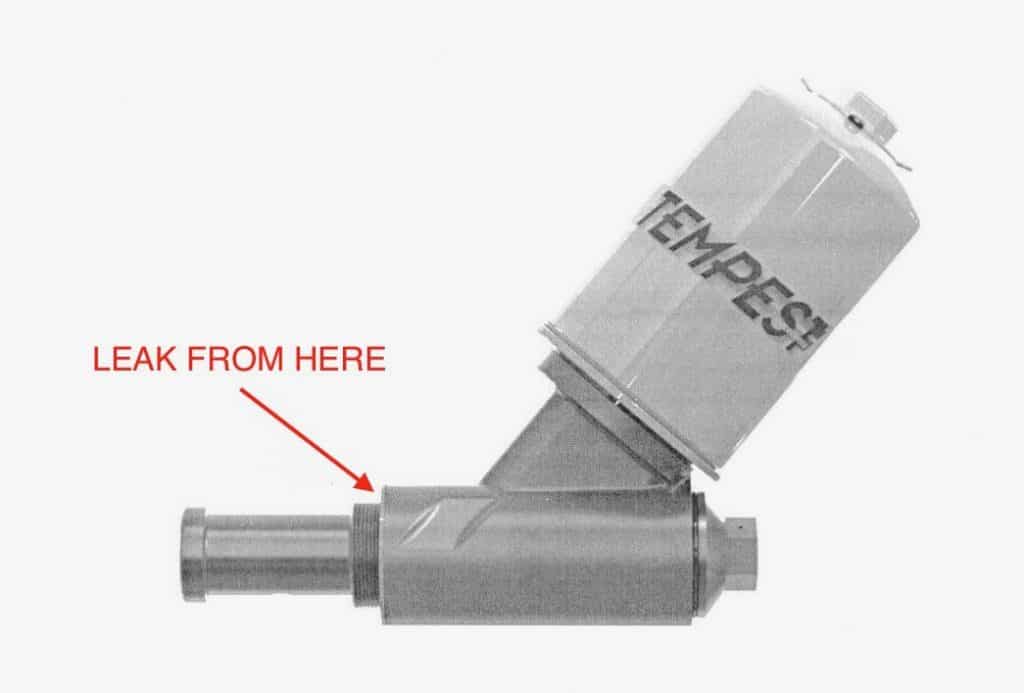
George returned to MHV with an A&P friend and some tools. They decowled the engine, and it became immediately obvious that the oil filter adapter had loosened and was leaking badly at the mounting gasket. The oil sump was drained through a paint strainer. Only one and a half quarts of oil remained in the 10-quart-capacity sump. No metal was found in the paint strainer. The oil filter was removed and cut open and no metal was found there, either. George texted photos of all this to Jeff so he could confirm George’s findings.
At Jeff’s advice, George and his friend replaced the oil filter adapter gasket, tightened the adapter mounting bolt to the specified torque, installed a new oil filter, and serviced the sump with nine quarts of fresh oil. The engine was then started and ground-run for nearly an hour, including several high-power high-speed taxi runs down MHV’s 12,500-foot runway. George reported to Jeff that the engine ran flawlessly, oil pressure was normal and stable, and there were no leaks. The oil filter was then removed and cut open. There was no sign of metal in the filter media. George took an oil sample and sent it out to a lab for spectrographic analysis, and the report came back normal.
Returning to MHV a third time, George flew the aircraft around the pattern a few times, then removed the oil filter and cut it open. Once again, no metal was found. He installed yet another new filter and flew the aircraft home to Southern California. Upon arriving home, he removed and cut open the filter once more and it was clean.
Jeff continued to follow up with George, who reported that he’d flown another five hours, cut the filter again, drained the oil through a paint strainer again, and there was still no sign of metal. George’s plan is to do this again in another 10 hours, then in another 25 hours. He is very happy with this outcome, is becoming increasingly convinced that he dodged the bullet and glad that he decided not to follow the engine shop’s advice to remove and tear down what appears to be a healthy engine.
Learn more about our breakdown assistance by clicking here.
You bought a plane to fly it, not stress over maintenance.
At Savvy Aviation, we believe you shouldn’t have to navigate the complexities of aircraft maintenance alone. And you definitely shouldn’t be surprised when your shop’s invoice arrives.
Savvy Aviation isn’t a maintenance shop – we empower you with the knowledge and expert consultation you need to be in control of your own maintenance events – so your shop takes directives (not gives them). Whatever your maintenance needs, Savvy has a perfect plan for you: